Introduction: Dust Boot for CNC Router
After watching the videos and following the instructions on the page you'll be able to create your own custom dust boot for your CNC router. This is a great first project to design something practical. We're going to be using Fusion 360 and you'll learn a lot of great features which I think set Fusion 360 above other CAD programs. I was using Sketchup before this and once I made the switch I realized that Sketchup is basically Microsoft Paint and Fusion 360 is Photoshop. There are so many amazing features you'll learn in this tutorial that'll get you started and comfortable enough to start making your own unique ideas.
Things you'll need:
Fusion 360
Access to a CNC
Brush bristles (I used this on amazon)
Wood
2 bolts with nuts
Step 1: Step 1: Creating the Model
Check out the videos for detailed instructions.
Start by setting 3 parameters called "router", "hose" and "thick".
router will refer to the diameter of your CNC router
hose will refer to the outside diameter of the vacuum hose you plan on attaching
thick will refer to the thickness of the material you're cutting from which will be the overall thickness of the finished product.
In the video my router is 2.717", my hose is 2.25" and my thick is 1".
Start by drawing 2 circles that are diameters of "router" and "hose" and then space them out a distance, I set mine apart 3/4 inch. Create circles around the hose and router that will be bigger than the hose and router by the space you just set on both sides. I just set mine to 3/4" so I want my circle diameters to be the router or hose +2*.75. The reasoning we double our gap is because we're typing in the diameter, not the radius. So in my example my other circles are hose+1.5 and router+1.5. We can draw those circles anywhere and position them with the "concentric" constraint as I do in the video.
The next thing we do is connect those outer circles with lines to smooth it out. We want to use out tangent constraint to make everything look as smooth as possible.
We'll trim up some excess lines as in the video and then offset the outer wall twice, 1 that is 1/3 of the gap (.75) and 1 that is 2/3 of the gap, this will give us a .25" wall, then a .25" gap for our bristles and then another .25" wall before the router/hose.
We'll add tabs on the ends of both so that we can cut a line through it into the router and into the hose holes so we then use a bolt to tighten down and clamp our router in tight. Watch the video to learn a few different ways to do this with different constraints. Remember though, we don't want to clamp on both the vacuum and the router because then we will be placing crazy stress on the center piece between the router and hose. Just clamp down on the router and the hose slot will open up slightly.
Now that we have it totally drawn in 2D we need to extrude the outside and inside walls the full thickness (thick) and the routed section 20% of thick so that we can place the bristles 80% into our design.
At this point I decided I didn't like how square the edges were so I used a fillet to round the edges and make it look smoother.
In the next step we'll give it some tool paths so we can cut it out.
Step 2: Step 2: Tool Paths and Generating the G-code
We just need to start a set up, identify what models we want to cut and what we're cutting it from. In my video I take off any offsets to the block and make it exactly as thick as the material I'm cutting from.
After we've created a set up we can start a tool path, we'll need 2 for this project. We'll start with a 2d slot to route out the section for the bristles. I set it to multiple depths at .1" passes, I'll be using a 1/4" flat end mill. Then we'll do a 2d countour and cut out our circles and outside shape using the same tool, we'll also use multiple depths and .1" passes but we're also going to add tabs so things don't become dislodged and ruin the project or worse, the CNC. We can simulate our cuts in Fusion 360 as I do in the video, but after that runs and looks good we can create the g code. Press post process to bring up the menu and adjust the settings as you may need to, save your file and then we can take it over to the CNC.
Step 3: Step 3: Cut It Out
The fun part! Open your g-code with universal g code sender (or whatever you use), square up your stock and cut it out. In mine I guess my wood was thicker in spots than I thought so it didn't cut all the way through but you can use a knife, jigsaw, hand saw, chisel or even a sander to fix it. Drill holes in the tabs for a bolt. Cut lines down the tabs into the hose and router holes, but do not cut from router to hose or you'll cut the whole thing in half. Put bristles in the slot, put the boot on the router, put the nuts and bolts on and tighten on the router end. Congrats, you're done! You've made a dust boot that'll work great!
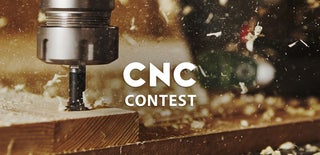
Participated in the
CNC Contest 2020