Introduction: Easy Transfer Lithografy/Planography for School
We like to teach a variety of printing techniques at school. The most popular are relief / block-printing techniques like linocut, woodcut or cardboard block or foam rubber printing. Since the school also got a printing press we can also do various kinds of intaglio / gravure work, mostly drypoint in copper, acrylic, CDs, Tetrapak (those are also great for hybrid techniques where you cut away the foil to the paper and can print full areas too along the engraved lines.) but occasionally also etchings in steel with FeCl3 . Then screen-printing and stencil work.
The one technique that has always been a little elusive was flat-printing or Lithography. It would be great to get our hands on some tons of Solnhofer limestone but storing and handling that kind of material would be a little too much for a common high school :).
Enter Transfer-Lithography - a planoprint technique pupils can easily learn and even practice at home with cheap, commonly available supplies.
while I just selected grade 9 I guess this technique, although a bit messy, would also be suitable for younger children like 10yr+.
Supplies
1) a surface that can handle some water. I just used some cut open trash bag and a cutting mat under it.
2) a laserprint or lasercopy of your artwork. Remember it will print mirrored.
3) water sprayer with water
4) 0il paint
5) a roller to spread your oil paint.
6) Gummi Arabic, either powder or granules, dissolved (over night in cold water but works in warm water shortly before using it too) in a jar of water 1:2 gummi to water.
7) Aquarelle paper or some other heavy paper.
If you are from Europe you can buy most of the supplies at Action really cheap (80 sheets of heavy paper for 3€...)
I ordered the gummi arabic from Amazon for 9€/500g. This will last for quite some printing. Cheap oilpaint is also readily available from Action, Tedi or even Lidl sometimes. Very convenient for price sensitive teachers ;)
Step 1: Preparing the Printing Surface
Lithography is based on the principle of surfaces either attracting oil or repelling it. Lipophilic surfaces will hold the oil color, like seen in the first picture, while lipophobic surfaces will repel it.
We start by watering the photocopy/laserprint and rolling it out on a flat surface. Ideally a glass or acrylic glass surface is used but the plastic over the cutting mat will do just fine. We also like to use plastic sheets from old folders.
Then you roll on the gummi arabic solution. Just pour some on the paper and roll it on carefully. Let it soak in for some minutes and water the plate again with the sprayer.
The water dissolved gummi arabic will soak into the inkfree surface off your paper and create a lipophobic surface while the inc will hold oil based paint.
Step 2: Printing and Results
Spread the oil paint on another plastic plate and roll it on your paper without pressure. You got plenty of time, the oil color will not dry. Use the sprayer in between and try to get rid of the water by rolling over the paper again. you should see color sticking to the black surfaces. The white surface should be free of paint. This actually look really cool.
We tried thinning the oil paint with more oil as recommended by some but it worked best when the paint was more pastos or directly from the tube.
When you are satisfied just press on a sheet of paper (we also tried fabric with great results), press or roll it on carefully. Try not to press all water out or you printing paper will stick to the paper plate and ruin your print and the plate.
The the first result you see in the picture is a copy of a painting we did in a comic/Manga workshop the day before. It was vectorized from a photo of the A3 original in PhotoPea (a free online Photoshop clone which has proven a great tool for us at school. Here is a great tutorial ) and printed on a laser copier on A4 (most copiers can print PDF directly from USB or network).
This was the 5th print from that papercopy. I honestly can't say how many prints you can do from one plate but it didn't show any signs of wear after that last one. The 4th print was on fabric so even that didn't destroy the plate.
The second plate we prepared was from a copy of a bookpage and an old floppy disc. Grayscale worked pretty fine too. We have to explore that path more in the future with bigger copies, this one was only A4.
I also like the fact that you can print anything you can copy. Just mix together some objects and get creative.
This opens up a whole new realm of printing at our school. I will hopefully explore some other interesting techniques like kitchen lithography (etching tinfoil with coke) during the next semester.
till then,
Happy printing!
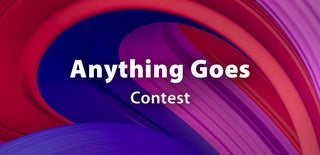
Participated in the
Anything Goes Contest