Introduction: Eccentric Articulated Lamp ::)
Hello fellow Instructables fam.
For my first post, I'm sharing the process of a lamp that I made for my aunt and uncle as a housewarming gift. They lived in Thailand for 4 years but have now returned to Dublin. I think they missed the sun and brightness of Thailand so I made them a lamp to help ease the transition to less sunny Dublin.
DISCLAIMER!! Before you attempt the instructable be aware that it involves using a lot of tools and techniques that might cause serious injury if not done correctly. Also, the whole instructable is in metric (sorry not sorry to the makers over the pond). If you choose to recreate any part of this be careful and use appropriate judgement.
The steps I took to make this lamp are outlined below, I hope you enjoy reading and hopefully recreating your own eccentric articulated lamp.
Thank you.
Step 1: Materials and Tools
This is a relatively complex project to undertake as it incorporates a lot of different techniques and uses some specialized tools/ processes. There are also multiple materials and components that will need to be procured but these can be easily substituted with something more easily available at your discretion. You've been warned it's a long list ::)
Base:
- Transparent acrylic block 200mmX200mmX50mm
- Butcher's block offcut 200mmX200mmX50mm
- Aluminium sheet 170mmX170mmX5mm
- Junction box with a terminal block
- Ikea Lampan cable (plug, switch and wire)
- 4 Circle felt pads
Middle:
- 2 pieces of beech 50mmX50mmX300mm
- 2 pieces of cherry 50mmX50mmX300mm
Top:
- Walnut block 110mmX110mmX35mm
- 8 Black acrylic 20mmX20mmX1mm
- 8 Walnut pieces 20mmX20mmX35mm
- 4 12mmX110mm chrome plated copper tube
- 4 12mmX25mm chrome plated copper tube
- 4 Brass bayonet lamp fittings
- 4 35mmX35mmX40mm transparent acrylic block
- 4 LED corn bulbs
Miscellaneous:
- Scrap wood
- 4 10mm Screws and accompanying washers
- 4 80mm Screws
- 4 Bolts and wing nuts for a 3mm hole
- One pack of epoxy adhesive
- 4 lengths of black 3 core mains flex wire at 800mm each
The tools and other things used:
- Pencil
- Ruler
- Tri-square
- Craft knife
- Bandsaw and or table saw
- Piller drill
- Cordless Drill
- Drillbits
- Laser cutter
- Clamps and vices
- Forstner bits
- Sandpaper of varying grits
- Apron
- Wire wool
- Brasso
- Gloves
- Danish oil
- Cloth
- Phillips head screwdriver
- Pliers
- Multimeter
- Wire cutters
- Lathe and turning tools ( roughing gouge, spindle gouge etc)
- Mallot and chisels
- Hot glue gun
- Masking tape
- Wire strippers
- Pipe cutter
- Router
- Planer
- Safety equipment where possible
Step 2: Design Development and Prototype
I went through many iterations of my design to get it just how I wanted. Sketches and sketchup were used throughout from the initial sketch to the final design. After I finished final the sketchup design(attached) I made a prototype using the measurements in sketchup to give me a sense of scale and a physical model that I could interact with. The tools and materials I used were:
•Duplex board
•Pencil
•Rule
•Try-square
•Masking tape
•Craft knife
Firstly, the base of the lamp was the reference point for the proportions for the other components so I made it to the exact dimensions of the model 200mmX200mmX50mm. I started by marking out a net for the base (pictured) by using a pencil, ruler and a try-square. Then I used a craft knife to score then cut across the outer perimeter of the net. After this, I bent the edges of the base and taped the corners and edges together to secure everything in place. For the middle and other lamp components, the sizes were determined mainly by the sketchup model but were also altered to what I thought was more in proportion to the base. For making the conical and tubular shapes shown I used the same technique as on the base but instead of the bending the pieces I rolled them as you would a crepe then I secured with masking tape. Once all the pieces were complete I worked from the base up attaching each component with pieces of tape.
Articulated lamp
Step 3: Making the Base
To make the base I went through a series of steps that are detailed below with pictures.
- I started by getting the stock materials for the base and marking them out to be cut into the sizes and quantities listed before.
- I cut the acrylic and butcher's block material first with a band saw by tilting the bed and going slowly as the blade was melting the acrylic. (I recommend not doing this step with a new blade as it could be significantly dulled)
- I took the one half of each material and began to remove the saw lines by sanding it vigorously with various sandpaper grits.
- I made a jig out of scrap wood and screws to hold the base in the position where the 45-degree faces were touching.
- A pillar drill was then used to drill the 4 pilot holes connecting the base to the middle and also the bigger hole going through the middle of the base. This allowed the wires to come through and connect to the junction box and switch cable.
- Using a pillar drill with a 20mm Forstner bit we drilled multiple holes into the base following the path of wires and junction box design on the bottom of the base. To make sure the depth of each hole was correct I used tape stuck to the height where the bit should stop.
- A chisel and a router were also used to clean up the hole and wire paths.
After the middle and top were complete the below steps were done on the base:
- The wiring was connected in the terminal box and all of it was then hot glued into place.
- The screws going through the base and into the middle were then screwed in using a Phillips head screwdriver.
- The base was then finished by drilling the holes for the cover plate and securing it with screws onto the base. Then felt pads were then added as a final touch.
Step 4: Making the Middle
I think middle was one of the more fun parts to make as turning on the lathe always brings awe with the shavings and sight of your work in the process of being formed.
- I started by cutting the lengths of cherry and beech I marked out then planing them for lamination.
- I then used wood glue and a few clamps to laminate the pieces.
- Once the glue was dry the square blank was cut into an octagon using the bandsaw as it’s faster for roughing it out on the lathe.
- I then took the blank to the woodturning centre I attend and began to turn it, you can see in the videos and pictures below. I spent about 1-hour turning and sanding the whole middle section.
- Unfortunately, I couldn’t use the long hole boring technique I knew to put a hole in the middle of the piece. So I had to use a specialised jig (pictured), a power drill and an extended large drill bit to make the hole.
- I drilled 4 pilot holes into the bottom for the base screws and then I put Danish oil on it to bring out its beautiful natural colour.
- The walnut piece on the top was made by using the bandsaw to cut a circle that was marked onto the walnut block previously.
- 4 holes were drilled into the piece using a Forstner bit just bigger than the diameter of the tube.
- This bandsawed piece was then sanded by hand in order to be symmetrical and smooth.
Once the top was done:
- I ran the wires from the top through the hole in the middle section down into the base.
Step 5: Making the Top
The top is separated into two sections that come together, the joints/stems and the light fittings/shades. The joints/stems were made through incorporating trial and error into the design, whereas the fittings/ shades were relatively straightforward and came together as planned. The steps for this are detailed below:
- The joints were made by marking out a finger joint type outline and cutting that out on a bandsaw.
- A drill was used to make holes for all 8 joints for the point where the bolts and wingnuts were to be attached.
- A Forstner bit was used to drill into the joints where the pipe connects.
- Another hole was drilled into the joints perpendicular to the Forstner bit hole to allow a hole for the wire to pass through (pictured).
- The black acrylic squares at the top and bottom of each joint where the joint meets the tubes were cut out on a laser cutter. The file was done in AutoCAD and was just a simple square 20mmX20mm with a 12mm diameter circle cut in the middle.
- The squares were then glued to the top and bottom of each joint using a thin layer of epoxy.
- The joints were then sanded and oiled with danish oil then connected using the bolts and wing nuts.
- The metal pipe was cut to length first using a pipe cutter then it was cut again using a bandsaw make the groves to allow the wire to pass through.
- The acrylic was then cut and then drilled, first with a small pilot hole then a large Forstner bit. Cutting out the hole was hard as the bit kept on getting jammed because the acrylic melted behind it.
- I connected the brass fittings with the 3 core wire stripped at the ends then I closed the tightened the fitting and also pulled out slack for the wire in the stems and joints to be able to bend easily.
- The brass fittings were attached to the pipe using epoxy, then placed into the hole made by the Forstner bit in the acrylic and fastened using the supplied ring and epoxy.
- After the tubes, acrylic shades and fittings were dry they were then glued into the fittings as well as another pipe going from the joint to the middle section.
- Once everything was dry I ran the wires through the middle and connected them to the junction box in the base.
- I glued the tubes to the middle using epoxy.
- Then I finished the top by cleaning up the components, polishing the tubes to a sheen and attaching the bulbs.
Step 6: Wiring the Lamp and Testing
For the electric component of my lamp, I used a junction box to connect all four wires from the bulbs together in order for all of the power to be transferred using only one plug and one wire going out of the base. The steps of wiring the lamp are below:
- After routing out the channels as detailed in step 2 I laid out all the wires and electrical components that needed to be placed.
- Once the 4 wires from the top were pulled through to the base I cut them to the length needed using wire cutters.
- I stripped the outer casing of the wire which revealed the 3 core wires (Earth, Live and Neutral) that I also stripped. I then twisted the exposed ends to make it harder for them to fray when connecting it into the terminal block.
- The wires were then inserted and connected to the terminal block in the junction box using a small flathead screwdriver.
- After doing this I used a multimeter to test that each connection was wired safely and correctly to avoid any shorts and shocks as a metal lamp could induce such things if not wired correctly.
- Once these steps have been done completely the last points of step 2 then finally you can plug it into a socket and switch it on.
Step 7: Installation, Dublin and the Family ::)
The reason I had for making this lamp was for a housewarming present to my aunt and uncle in Dublin so when I completed it I knew what I had to do...GO TO DUBLIN. I left Bristol on an hour flight to Dublin with my backpack and the lamp wrapped in an old hoodie as my check-in luggage. I arrived safely, met them at their house, installed the lamp and had an amazing few days exploring Irelands capital with my family.
The pictures of the lamp in my aunt's house are shown above as well as some obligatory pictures from my trip. Also if you get the chance to go to Dublin I recommend seeing the Guinness Storehouse as well as the Gaiety Theatre.
I hope you can take something away from this project and make something to give or just for yourself. Leave questions below if you're unsure of a step and I'll try to get back to you ::)
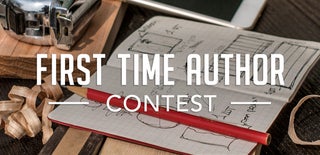
Participated in the
First Time Author