Introduction: Edison Bulb Projector Shelves
About three years ago I started building these shelves.
About Three weeks, two apartments, and two couches ago, I finally finished them.
This project, like many, stemmed from that ever niggling thought all makers get: “huh, I could probably build a better solution for this”. That thought came to me shortly after I moved into my first Portland area apartment while watching the Wizard of Oz on a projector that was precariously perched on a steamer trunk and further propped up with books. It was the first night that I didn’t feel like I was just camping in my new space but I knew I could do better.
Step 1: Design Considerations
Any time you’re building custom furniture the best place to start is figuring out your constraints:
- How much space do you have?
- Does it need to accommodate anything specific?
- Other furniture?
- Objects?
- Features?
- How much are you willing to spend on it?
The first part for my space was relatively easy. However be sure to check for potential unexpected surprises like counter edges, trim boards, or couches that are wider in the front than in the back (we’ll come back to that one in particular).
The second part needs a bit more consideration. For my case I knew I wanted the whole unit to be free standing since I was renting. The couch, a futon at the time, needed to fit beneath with enough room to easily pull it out. I also wanted to be able to fit my desktop PC, a rather tall 3D printer, and a smaller 3D printer somewhere on the shelves to get them up off the carpet. On top of that making the unit so that it could break down easily when I had to move while still being sturdy enough to have little risk of falling over were both requirements.
The last part is tricky and difficult to judge even for professionals. In general I fall back on the old tripod maxim:
Cost, Effort, Quality pick two.
For this project I decided I was willing to put in the extra time and effort for something both inexpensive but good quality. If I had started with the final design I probably could have finished in a couple of weekends after finding the materials. As it was it took a bit longer than that but I was able to use it for most of that time as well so I never minded.
Step 2: Materials and Design
Given that low cost was my aim I didn’t rush getting materials. Patience may be a virtue broadly, but it also pays dividends at this stage of a project. I lucked out about a month into my search and found four cherry veneer solid core accordion doors at a local building surplus store for $5 each. I didn’t even mind having to fix the dent in my car’s roof after schlepping them home at that price.
This was a super lucky find, however when I rebuilt the central shelves I found an alternate solution, see Step 7.
Given how nice they looked I decided to make them the center piece of the design. The rest of the build is just edged dimensional lumber sanded and painted satin black. Be sure when you are picking out your lumber to check that each piece is dry (not noticeably cool to the touch) and as close to square as possible. Especially when using inexpensive materials it pays to take your time and be picky now, it’ll save boatloads of time and frustration down the road.
The main struts are 2x4s cut at a miter on a chop saw and the shelf braces are 2x2s cut to the same length as the shelves. To achieve greater stability I decided to go with a ladder design making the base deeper than the top. You’re welcome to use my design attached, however if you want to make your own be sure to double check that all of your angles sum to 360 degrees. It may not hurt to build or 3D print a small model as well as at times it can be hard to fully grasp the proportions of a design without a physical reference. Better to burn some time and effort at the small scale than discover a problem later at scale.
Step 3: Construction
This should go without saying but for all steps involving tools proper Personal Protective Equipment (PPE) and safety precautions should be used! If you are not 100% sure how to do a step safely then don’t do so without the assistance of someone familiar with the tool or process!
*steps down from soapbox*
Alright now you can cut your dimensional lumber to size, preferably using a chop/miter saw. Measuring twice is well and good but periodically doing a dry fit up of your pieces to make sure they align as you expect can help identify unforeseen problems earlier when they are more mole hills than mountains.
For the shelves a circular saw and saw guide work wonders. When using any kind of laminated material it helps to tape along both sides of your intended cut. This, and cutting slowly with a sharp blade, will help prevent the material from chipping while you cut.
Before routing or assembly examine the edges of your 2x4s. If there are any flaws now’s the time to address them. A few of my pieces had knots with cracks near the edges. To ensure they didn’t break further during routing, or show through on the final product I filled them using two part epoxy along with painter’s tape to keep it contained. Epoxy works great for this sort of thing since you can cut and route through it as easily as wood in small quantities and it’ll be completely hidden under the final paint job.
If you have access to a router table you can run your 2x4s through it before gluing which will speed things up. If not most edging bits have a small ball bearing that will keep the bit at the proper depth even when using them free hand so it can be done easily enough once the sides are assembled, this is what I ended up doing. In either case you’ll want to take your time and be sure your work space is easy to sweep up, routing generates an astonishing amount of saw dust!
To fasten the pieces together I recommend drilling pilot holes to prevent splitting and using a larger bit to drill a recess for the screw head. I used a 1/8” bit for my pilots and a 3/8” bit for my recess. I made the recesses about ½” deep and once each side was assembled and dried I coated a length of 3/8” dowel with glue and hammered it in to place before trimming off the excess. After sanding and painting this will completely hide all of your screw heads leaving you with a near uniform surface.
Step 4: Prep and Paint
After giving the glue about 24 hours to fully dry the lumber will need to be sanded. I recommend two thorough sandings for something like this, one with 80 grit and one with 150. With inexpensive wood like this you’ll quickly start to get diminishing returns as you go to higher grits. You’re welcome to sand higher but personally I’ve found that having some roughness helped break up the reflections in the satin paint making the supports less noticeable.
After sanding the wood you’ll want to wipe it down to remove any excess saw dust. Using a barely damp rag will work but ideally you’d want something like tack cloth.
For the painting step I went with two coats of primer, lightly sanding between each one to knock down any raised grain, and three coats of paint. Much like the sanding grit don’t worry about leaving brush strokes, I would recommend trying to make your brush strokes relatively parallel however as it will give the impression of wood grain on casual inspection.
Step 5: Assembly
Once the last coat of paint has had a full 24 hours to dry hard you can begin final assembly! To assemble the shelves simply run 2.5” screws through from the under side of the 2x2 braces into the shelves to hold them in place. I would recommend not gluing these joints as it makes it easier to break the shelves down for transport in the event you need to move them. Once each end tower is assembled the central shelves can be mounted in the same way, be sure to start with the top shelf as the bottom shelf doesn’t leave a whole lot of room for a drill gun if you put it in first. If you would like to further hide any screw heads a small dab of black acrylic paint does wonders.
Put everything away and revel in your completed shelves!
Step 6: Folly Necessitates an Upgrade
About a month after I finished these shelves I moved to different apartment in the same building. Shortly there after my favorite local coffee shop closed and sold off all their furniture including a beautiful leather couch and love seat combo. By the end of the day they had marked them down from $500 to free. One of my best friends was in town and offered to help haul them up the stairs so I decided to go for it, if and only if the couch would fit under my shelves. I measured the back and it would be tight but I thought it would fit.
Do you see the folly in my story yet? It’s in the last sentence, “I measured the back…” After hauling both the couch and the love seat up a flight of stairs and through a narrow hallway I found to my dismay that the couch was about 8” wider up front around the armrests. I put up with my new couch sticking an extra foot and a half out for about a year. I liked the couch but the constant reminder of my snap decision irked me.
Last summer I lucked across some beautiful mahogany veneer and a plan formed. The pieces were oddly shaped but at a dollar a sheet the price was more than right, I bought as much as I could carry, twice.
Step 7: New Shelves With an Eidson Twist
The new wider shelves are essentially DIY hollow core doors.Their frames are made from 2x2s again since they will be well and truly hidden. The cores are made of 1.5” thick insulation foam, and the whole thing is sheathed with 0.1” thick MDF sheets. The MDF sheets are regularly recycled at my work since they’re designed to protect PCB panels during shipping and have limited uses around the shop after that, so I offered to recycle a few of them myself.
If you’re making your own any thin MDF or plywood would server for this. Additionally you could skip the veneer step as well and simply paint your shelves or cover them with a vinyl wrap of some kind, sky's the limit!
After cutting the 2x2’s to size and assembling them with my poorman’s pocket screws much like the 2x4 braces I glued and stapled the MDF sheets to one side then glued in the foam. For the lower shelf I cut wire runs and openings for light sockets into the foam with a box knife, then used a hole saw to drill evenly spaced holes for the Edison bulbs. I opted for 12v LED faux Edison bulbs for the lower energy usage and ease of control. These were then wired in parallel and connected to power through a small custom ATTiny85 dimmer circuit and an XT30 connector glued to the back edge of the shelf. The contacts on the backs of the sockets were all sealed with thin layers of hot glue then the back set of MDF sheets were glued and stapled in place. These lights are perfect for watching movies and can be dimmed to give off just enough illumination to see without washing out the projector.
After this I thoroughly pounded down all the staples. I also took care to fill in the thin gaps between MDF sheets and at the corners between the MDF and 2x2s with wood filler before sanding smoot with 150 grit.
I tried two methods of applying veneer. The first I assembled like a puzzle gluing each piece down and fitting their edges together. While this could have turned out much worse I don’t recommend it. The method I recommend is using blue painters tape to secure your individual pieces together in advance then laminate them on as a single sheet using weights to hold them down. Make sure the sheet is large enough to fold down later to glue and clamp to the edges as well.
Using PVA glue (elmer’s, titebond, etc.) is a must here! PVA is actually a thermoplastic so after it’s dry you can go over the whole surface with a hot iron to firmly seal it to the MDF beneath and work out any errant air bubbles between the two. Using the iron to heat the bends when wrapping the edges will also help prevent cracking.
Finally I lightly sanded and sealed the veneer with urethane and painted the bottoms of the shelves black in a similar manner to the 2x4s.
I added metal angle braces to the bottom shelf to help stabilize the now longer shelves and also added a projector mount to the underside of the upper shelf rounding out the upgrade.
Currently the dimmer control is just dangling, however a small 3D printed case is all that’s needed to solve that problem.
Step 8: Try It!
I hope you’ve enjoyed reading this, I can’t recommend making your own furniture enough. It’s cheaper, better looking, more solid, and if you’re careful it can become exactly what you need in a way that something store bought never could.
If you want to make this project as is go for it! But I would encourage you to consider adapting the ideas and techniques I used to your needs and materials. There’s nothing quite like a bespoke piece of furniture specifically designed for your needs!
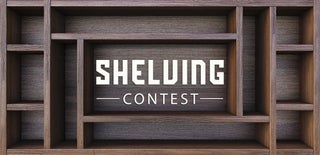
Participated in the
Shelving Contest