Introduction: Electric Motorbike
This project began with a free Razor Pocket Mod Scooter found on the side of the road. Although it didn't run, the frame was in good shape. I decided to use whatever parts I could salvage and combine them with a mountain bike and custom body to build a more powerful (and adult size) electric motorbike. I decided to use a boys 20" bike, so that the wheel size and low profile matched the size of a small-engined motorbike.
Step 1: What I Needed
- 1 Razor Pocket Mod Scooter (for frame, brake lever, seat, and charging plug)
- 1 Boy's 20" Mountain Bike (for wheels and tires, brake, freewheel set, shifter, derailleur, front fork, chain, handlebars, kickstand, and grips)
- 1 1000w 48v electric motor
- 1 11 tooth motor sprocket
- 1 48v 30amp controller
- 4 12v 9ah SLA batteries
- 1 48v 2.5amp battery charger
- 1 twist-grip throttle
- 1 key start switch
- 1 additional 7-speed freewheel set
- 1 additional bicycle chain
- 1 cyclometer
- 1 handlebar mirror
- 1 set 12v headlight and taillight
- 2' angled steel support bar (for extending rear axle and supporting seat)
- 1 section of 6" PVC pipe
- 4' of 3/8" threaded steel rod (for rear axle supports and foot-pegs)
- 10' of 14" width aluminum flashing
- 20"x14" vinyl fabric
- 1 can spray glue
- MANY pan head wood screws and machine screws
- Various lock nuts and bolts (mostly 3/8")
- Lots of wood (1x2 and 1x6 boards, and 1/8" veneered plywood for dash and headlight mount)
- 1 roll of window insulation foam
- Electrical connectors for batteries and controller plugs
- 20' roll of 12 gauge electrical wire
- 3 cans of Spray paint/primer
- 1 can wood stain
- 1 can clear coat
- 1 can polyurethane
Step 2: Tools Used
- Electric Drill
- Drill Press
- Band Saw
- Dremel Tool
- Soldering Iron
- Metal Shears
- Staple Gun
- Bicycle chain adjustment tool
- Various wrenches, hammers, and screwdrivers
Step 3: Disassembly and Fitting the Fork
The frame on the Razor was in great shape with no rust or damage. I purchased the donor bicycle new ($70 from Walmart). All parts were separated and labeled. Because the Razor used a larger pipe diameter for the front fork, I had to cut the downtube from the Razor and attach it over the bicycle downtube. Luckily, the fit was very snug, so a bit of J-B Weld and several pins worked very well to secure the new tube.
Step 4: Extending the Rear Axle
I used the angled steel pieces and threaded rod to create a longer rear end which could accommodate the rear wheel. Because I wanted to complete the project at home without additional tools, I needed a design with no welding. The angled steel worked out very well. It was easy to mount to the frame and offered mounting points for other parts.
Step 5: Construction of the Body and "Tank"
I know, I know, it's made out of wood. Initially, I wanted to design an all-steel and aluminum frame, but once I decided to use the Razor frame and avoid welding one myself, that plan changed. I used steel for all structural elements, and created the cosmetic structure out of wood. This saved a lot of time and a ton of weight. Essentially, the wooden structure is mounted to the chassis, so the bike feels solid. The Razor frame had quite a few mounting points where the plastic scooter panels had been, so I just needed to create a design which used those points.
I created the "tank" and headlight mount using a piece of 6" PVC pipe, cut in half. Cutting such severe angles in the pipe was a bit tricky without a larger band saw, but I was very pleased with the resulting shape. The tank is also the access point for the batteries and and electrics, so I mounted it using hinges. I cut sections of veneered plywood to create the dash.
Step 6: Cutting and Shaping the Body Panels
I initially had trouble deciding how I would cover the body. I didn't want to use wood, and while searching through the hardware store, I stumbled upon rolls of aluminum flashing (ordinarily used for roofing). The aluminum was quite thin and cheap, perfect for my project.
I started creating the panels using sheets of poster paper. Once I had formed all of the shapes and bends, I traced the designs onto the flashing, and cut them using a pair of shears. I then bent and fit the aluminum panels by hand to the frame. This was where lots of finger-cutting and swearing ensued. I finally got all the panels cut and fit, and drilled all the mounting holes for the screws. I wanted the body to look like vintage riveted airplane panels, so I drilled parallel rows of holes along the edges of each piece.
Step 7: Painting and Rebuilding
Once the panels were fitted and drilled, I removed them along with the front fork and rear supports. I painted the entire frame, panels, and tank in glossy black. I figured this was the best color to hide less than perfectly even seams between the panels. I used three coats of paint, followed by two coats of clear coat. For the wooden dash, I stained the panels with Cherry stain, and coated them in glossy polyurethane.
When everything was dry, I reassembled the bike, adding the window insulation around the tank hinge. I also recovered the seat (originally white) in a caramel vinyl, and installed the lights, kickstand, motor, and foot pegs. I also added the cyclometer from my commuter bike once I remembered it could be calibrated for a 20" wheel.
Step 8: Wiring, Building the Transmission, More Wiring
Then began the wiring...
I first had to solder electrical connectors to all the lengths of wire. I then connected the four batteries in series with a 30amp fuse wired in. This was connected to the controller, and everything else pretty much plugged into labeled inputs(with some minor adjustments). Because I was using a 48v system with 12v lights, and because I didn't want to buy a DC-DC converter, I wired the lights in series to two of the batteries. They draw so little current that it does not affect power while riding. In the future, if I swap the SLAs for a Lithium battery, this will have to change.
My starter switch still hadn't arrived, so I began working on the transmission. The motor I bought has an advertised max RPM of 3000, so I knew I really needed to scale up the gear ratios. If I didn't allow the motor to spin at least 6(ish) times faster than the wheel in first gear, I risked burning it out. At the same time, I still wanted to use the existing freewheel and derailleur set to change gears. What I decided to do was mount a second freewheel set to the frame. This way the motor goes from an 11 tooth to 34 tooth gear, which then goes from a 14 tooth gear to the rear wheel. The mechanical losses due to this system are higher, but it does allow for high torque and low strain at low speed, as well as the option to change gears.
Once the starter switch arrived, I drilled out holes in the dash for it and the light switch and wired them up. With that, the bike was ready.
Step 9: Completed Project (video to Come)
I am very pleased with the final results of the project. Already, I can see parts I want to change and upgrade, but as it stands, the bike works very well. Riding position is low (seat height of 26"), but can be adjusted by changing the length of the rear support threaded rods.
The bike can reach speeds of 25 mph in first gear on level ground, and onto a top speed of about 40 mph. Right now the range seems to be about 10 miles. It weighs about 100lbs, so it's not the lightest. A 48v Lithium battery could definitely help the weight and range. That being said, I have it at full throttle most of the time, so it could probably go a bit farther with a lighter touch. Total cost of the project was about $650 (free Razor scooter definitely helped). I ordered all the electrical components from Amazon and TNC Scooters (tncscooters.com). Hardware was from Lowe's and Home Depot. The batteries were from a local dealer (but also easily available online).
I hope you enjoyed my build. Any comments or questions are appreciated!
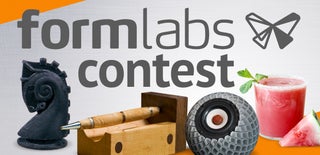
Finalist in the
Formlabs Contest