Introduction: Elven Keyboard
I don't know where to start to explain this project. It seemed to grow a mind of it's own. I have spent over 6 months and I lost track of time put in after 200 man hours (that is well in the rear view mirror). The project is not completely finished but I have decided to leave it in the state it is in at this point. (more on this as later). The project involves, moding a plastic keyboard (grinding, cutting and gluing), woodwork (veneer, cutting, carving and burning), metalwork (cutting, bending, forming and embossing), glass work (grinding, painting). electronics (solar panels, joule thief and led's this part is incomplete at the time of writing and may never be finished at this point).
The project started simple enough. My girlfriend suggested that our daughter having turned 4 was at a point where she probably needed a computer of her own. I was on ebay and found a mini itx motherboard for next to nothing and decided to place a bid not thinking I would win it but I did. Now having a mini itx I decided to make my daughter a computer. I wanted it to be an heirloom piece so it wasn't just some computer she would outgrow and we would end up scrapping out after a while. Something she could hang on to as a work of art and say "My daddy made that for me".
The gears start turning on the big brain....
Well my daughters name is Lillian and we call her Lily. So the computer should have a theme of lily's. To get inspiration I started looking around for images of lily's and found one of a water lily that I really liked and started thinking out the design. At this point you may say "But hey he is doing an instructable about a keyboard not a mini itx machine" Well that's where the big ol' brain got in the way. While thinking out the box design I thought you know a good keyboard to go with that would be a great idea something that will match it and isn't just some beige or black piece of junk. I noticed the girlfriend had some glass beads that are used for decorative purposes you know the kind a bit like a marble but flat on one side. The colors reminded me of water (clear, blues and greens). I noticed that each was about the size of a key for a keyboard.
And so it begins....
I used an old ps2 keyboard since the mini itx board had a connection for that and I didn't want to take up a usb port if I didn't need to. I tried to keep the cost down because, well we are broke. I have been out of work now for 3 years so a project like this keeps me from going insane but can be frustrating not having needed tools or materials. It just presents opportunities to find creative solutions to otherwise simple problems I guess.
As anyone who has done a project like this probably knows you may find more than one way to do things. You may find better ways too which you may not implement because you have gone to far to turn back, don't have the funds for additional material or just decide you like one way over another. As I go along I will try to highlight mistakes as well as successes and point out alternative options which I may not have used but are useful.
I am going to write this instructable a bit different than I usually do. Typically I start with a list of tools and materials for the whole project. For this one since there are so many different disciplines I am going to break it down by "parts" of the project. So I will provide the tools and materials in each "section" so for instance "Metal work", "Wood Veneer", "Keys" etc.
Step 1: The Keyboard
For this you want
- Screwdriver (almost certainly going to be phillips)
- Tweezers
- A chisel or something to pry with.
- Cotton swabs
- Rubbing alcohol (or something else for cleaning)
I chose the keyboard I did because it was a ps2 connection which saved using a usb port on the computer. It was pretty sturdy and it was bound for recycling if I didn't do something with it anyway so if I botched the job it wasn't something that would be missed or be costly. I like the idea of taking something which would otherwise be pretty useless and give it a new life. Better for the environment and for my budget (or complete lack thereof).
I didn't take a picture of the keyboard before disassembling it but we all know what a keyboard looks like. The parts of this keyboard include.
- Upper plastic housing (ABS Plastic)
- Lower plastic housing (ABS Plastic)
- The keys
- A rubber "mat" that has little "nipples".
- A mylar sheet with silver traces
- A controller
The parts that we will modify are the upper and lower plastic housing (the upper is the bulk of the work). The keys of course and the rubber mat (in this build since I removed the numeric keyboard to make room for the solar cells we will trim the mat so contact is not made to the corresponding keys ever).
A quick note on how a keyboard works. The mat sits on top of the mylar sheet, actually 3 sheets. 2 contact sheets and a seperator sheet. The mylar sheets have silver traces on them and when those traces come in contact with one another they complete a circuit (a key press). So the key pushes down the shaft, which depresses the "nipple" on the mat over the mylar, which creates a contact on the specific trace for that key. My suggestion is to remove the upper plastic housing with the keys and just leave the lower, the mat, the mylar, and the controller alone to the side for the bulk of your project only messing with it to maybe put the upper on when you have your keys made to make sure they work.
The mat is important in that it holds the keys "up".
Ok now that we know what to expect in there and what it does time to pop it open.
Each keyboard is going to be somewhat different but I'm sure you can figure out how to open it and if you can't then then this project really is not for you.
- Remove all the screws from the back of the keyboard
- Take your chisel or whatever you decide to use as a pry bar and pry the upper and lower apart on my keyboard there is a gap in the back with little "clips" that you need to pry apart. Do this gently you don't want to break anything (again different keyboard may require different steps or locations to pry). Also don't use your ratchet style screwdriver as a pry bar. Really don't do it... (says the guy that has done it knowing better and ruined more than one)
- Place your screws in a ziploc bag somewhere safe that you won't lose.
- Place your lower with everything to the side out of the way safe.
- Remove your keys
- Clean your upper and keys with rubbing alcohol (DO NOT USE RUBBING ALCOHOL ON YOUR MYLAR SHEETS). My old G30 says from it's grave "I don't like beer nearly as much as my owner did".
Once you have the keyboard taken apart and have your upper remove the keys. The best way to do this is to use a pair of tweezers as shown above. In the end I took my keys on and off many times and I used pliers from the upper side generally but I would suggest avoiding that method until necessary as you don't want to make a kink in the little runners on the shafts. They keep the keys aligned so they don't twist and so that they slide vertically. If you crush or dent them they can cause your keys to stick and a repair is unlikely to work well so in the words of General Public "A little tenderness".
Step 2: The Keys
Ok I am going to break this out into multiple steps because on this project I made keys that are glass and some that had wood veneer. I also am going to add another step where I present other approaches both well working and some that didn't work and why so you can avoid mistakes I made or do them in a different way.
Step 3: The Glass Keys
Tools
- Dremel (this depends on a choice see below)
- Diamond burr bits (this depends on a choice see below)
- Small rotary sander or grinder (you could use a dremel for this but really my mini rotary sander was perfect)
- Fine paint brush
- Exacto knife (optional)
- Printer (optional)
- Plate of glass (mirror, picture frame etc this is really optional)
- Safety glasses (seriously you can't replace an eye)
- Hair ties if you have long hair and decide to use the dremel route (Seriously I figured out how to make instant dreadlocks... It's not fun)
Materials
- Glass paint (2 colors I used a dark color almost black and silver of course you could use something else)
- Glass glue
- Rubbing alcohol
- Cotton swabs
- Scotch tape (optional)
- Printer paper (optional)
Cleaning
Ok the first thing you want to do is clean up all your keys. Perhaps your a neat freak and your keyboard was in great shape and clean as can be. Mine wasn't years of grit and grime etc. So take the rubbing alcohol and cotton swabs and clean it all up.
Making the keys
Now for the glass keys I did them 2 different ways. At first I decided that I needed to grind out a small hole in the bottom of each bead to the size of the "post" from the key and then fit that in there. This took on average a bit over 1.5hrs per piece and longer as it goes when the bits start to wear down. Add to that the fact that grinding glass that way has a real tendency even if your careful to heat up and cause thermal shock to the glass and the small imperfections in the glass in the form of bubbles and that... leads to all that work being worthless when your bead just splits in half out of the blue sometimes well after the work has been done and it's cooled. Oh and that speaks nothing to the pain your hands will be in after that much time grinding a small piece holding it in your hand and the dremel vibrating too so... I will explain this approach but right up front I will tell you there is a much easier and better way that unfortunately I didn't decide to do until after I had all the lower standard keys done and over 15 that cracked on me.
I got some super cheap diamond burrs for glass cutting/etching on ebay from China. When I got them they didn't fit my dremel. I was obviously upset contacted the seller they refunded me even though I didn't ask just did it out of the gate and didn't want them returned. Well I found a way to make them work by using electrical tape and tightly wrapping it on the shaft. This worked well though I would strongly suggest going out and buying a collet kit that dremel offers which comes collets of smaller sizes and of course would have worked with those bits I got mine well after all the grinding was done of course...
Take the bead in your non dominant hand. Take the dremel at fairly high (though not full blown) rpm and lay it at about a 45 degree angle on the bead to start to get a divet in there. Slowly and firmly rotate the dremel on that angle to widen the hole. Eventually when you get enough "bite" start to work the dremel vertically and grind around the edges ever widening the hole to the size of the key post. Now you could use a vise or a pair of vise grips here but I find that being able to feel what your doing and being able to reposition the bead in your hand while working helps.
This worked great but I found in the end was completely overworked and unneeded. The only advantage this has over the (to be described) approach is that it allows more light to come up from below the key.
Now if you do the dremel route you will need to take the grinder and grind down the key to the post. Don't go to deep try to get as close to the top of the post while removing the actual square key portion. See above.
The second way is to just grind the key edges off leaving a fair bit of the flat portion of the key on the top and then gluing that on to the bottom of the glass. Yes really it's WAY easier, holds just as well, has the advantage of keeping the bottom of your key to the original height. It also opens up 2 other advantages which I will discuss later in the other options for keys section. I ended up doing all the function keys this way and holy cow I did all of them in about the time it would have taken for 2 of the other keys.
Painting the keys
This part ended up being more difficult than I would ever have thought. The whole time I was working on the keys I just assumed I could find some stencils at a craft store and life would be good. Well.... life is never that easy. I couldn't find any stencils anywhere that were small enough for the keys. I was able to find decals and stickers but that's a real no go for the dremel ones I did. (you could use those on other approaches mentioned later in another section). I worked out a way to make my own stencils sort of and started out doing that so I will describe that method though in the end after a few stencils I decided I was comfortable enough to free hand paint them. So what you see for the most part is me free handing them. Who knew that drafting class in like 6th grade would come back to be useful.
As you can see I did 2 tones on my keys. Originally I was just doing them in the dark color (tried the silver too) neither worked very well alone as they just were not very visible with the way the light plays with the glass and it's colors. Adding the silver outline REALLY made it pop, made it very visible and I think added a lot of character to the keys (pun intended).
If you want to make your stencils. Pick you font in notepad or word or whatever. Figure out the size that will work on your keys. Now
- Print your fonts
- Cut the paper out as close to the font leaving a small border.
- Cover that with scotch tape
- Use a small part of the cut paper to use as a pull tab to easily remove the tape from the glass
- Adhere the scotch tape to a plate of glass or a mirror
- Take an exacto knife and cut the font portion out
- Remove the scotch tape (with the paper still attached) from the glass
- Place it on your key to be painted (for stencils I liked to hold the key in my hand for hand painting I liked to have them actually on the keyboard)
- Paint your stencil.
- Remove stencil.
Step 4: The Wood Veneer Keys
I decided to make the larger keys with wood veneer over the actual keys. I decided to do this for a couple of reasons. First the other options I tried either didn't look great or they did look great but were too heavy. If a key is too heavy the "nipple" on the rubber mat can't hold the key in the up position. The edges I painted. I experimented with banding them with metal which I will go over later but decided against it personally.
Tools
- Paint brush
- Exacto knife or other cutting tool (I actually used a wood engraving tool)
- Binder clips
- Wood branding tool (I actually used my soldering iron.. oh my.. /cringe)
- Printer (optional)
Materials
- Wood veneer (I used a 2 ply cherry wood veneer from Rockler this was enough for the whole keyboard, the keys, my Ornament for one of my other daughters, and will be enough for the mini itx pc.)
- Epoxy (I used Locktites 5 minute epoxy)
- Testor model paint (I used the aluminum color)
- Natural color stain
- Polyurethane spray
- Sand paper (I got a pack of flexible model sandpaper)
- Printer paper (optional)
- Alcohol or other cleaning solvent per the instructions on your epoxy
First paint your keys. A quick tip is to write the name of the key on the underside of the key so that later when it is covered up you know what it is. As you can see in the photos I don't coat the top just the edges and the lip of the top.
Next take a strip of your veneer (make sure that you match the grain and direction if you want it to all look similar). I actually had a band of veneer from over cut on the actual keyboard when I did this. That made use of otherwise scrap material and made sure the grain was matched. Cut the veneer to have a small amount of overhang on the key on all sides (when binding it can slide a bit so getting it right on it's just easier to have some excess material you can trim after its bound).
Now apply your epoxy to the veneer and key. Hand press it good in to get into the grain etc. Prior to this you may want to drastically scuff the surface of the key and may want to even drill some very small holes in the top. ABS is notoriously difficult to glue to (more on that later) and giving the epoxy cavities to adhere to is helpful on making a good and lasting join.
Work quick and stick on binder clips as shown in the picture above. Make sure to look at the veneer and see that it's seating into the concave shape of the key. You can get the binders "off" center and applying pressure only to the lip of the key so make sure you are getting good even pressure where you are applying it. Make sure to do a dry run without epoxy as once you mix the epoxy and place it you have very limited time.
Now use some alcohol or other solvent (read the epoxy label to see what works) to clean up any overage that squeezes out. If you damage the paint job don't worry so much you will be coming back and touching it up at the end anyway.
Let that set up overnight.
Remove the clips.
Use an exacto knife or other sharp cutting tool to remove the overhang you left on there. Do this by placing the key face down and firmly but not aggressively running the cutting tool along the edge of the key.
Sand your face and soften the edges etc. (you will almost certainly need to do some touch up painting after this so it's to be expected).
Now print out (or you could do this by hand). The text for your keys. I free handed the windows key and the context menu key. I used the tracing method described below for the rest.
Tape the paper with the text on the key in the proper position.
Trace over the fonts on the paper with your wood burning tool (or in my case soldering iron which surprisingly didn't really screw up my iron at all though I wouldn't do this a lot with it tbh). Be careful that you don't "bridge" the paper on the concave surface. I found that if the paper is not in direct contact with the surface of the wood it will be more likely to burn or even flash. You are ok with it burning a little but not flaring.
Once you have a good trace on there remove the paper and touch up the burn.
Sand.
Stain.
Seal.
Touch up the paint job.
Done with the veneer keys yea only hundreds more hours left to go ;)
Some gotchas. Remember to pay attention to which side if the key goes to the top. Those who are really observant may have noticed that the backspace key on my keyboard is upside down.... long story. Also make sure you know what the keys are (like I said label them when painting) as some keys are the same size and geometry.
Step 5: Keys - Other Options, Mistakes Etc.
The photos above show some other approaches I took and opt'd against for one reason or another.
The first and third photo show a key ground down and then fitted with a glass bead that has been cut with a dremel diamond wheel to fit in. I didn't think it looked very good, was rather dangerous for my fingers which I have some fondness for. You could probably go that route and use an epoxy or something just was not something I liked for this project.
The second picture and last one show the glass tiles that I tried. I did very much like the way they looked. They had 2 big problems though. First they were to heavy and the nipple could not hold them up well enough. Second the type of glass seemed to break much easier and when it did tended to "shard" creating nasty sharp edges. Since my daughter would be using this I decided not to proceed. I ended up using the remaining tiles in the Nightlight project.
In the fourth picture you can see that I ground down the top of the bead removing the rounded top. This is something I almost certainly would have done if the keyboard was for me or another adult. The reason I say that is it has a more "natural" feel to it that way whereas the rounded tops not being completely even on the end product would be cumbersome to use for me. My 4 year old doesn't know how to type yet so keys like that are a non issue. The down side to the grinding is getting the glass polished up to completely smooth is not so easy.
The 5th picture is a glass bead of the same style as the others just much bigger. I cut it down with the diamond wheel and really couldn't get it straight enough and even if I had I just didn't like the way it looked. It seemed kludgy and out of place even though it was the same glass.
In the 6th image you can see that on one of the wood veneer keys I added aluminum banding. If you look at the 8th image you can see the pattern so that it is a single piece. To produce that place your key on a piece of paper on one side outline it and start rolling it to the next side and repeating until all four sides have been done. Now when I did the example you see I did not have all the tools I have now so that was done using only my hands and a small gunsmith hammer. I think it looked great however.... The down sides were. First I couldn't come up with a really good way to join the pieces. I tried to solder it in place. Very bad plan it burnt the plastic and warped the post even so that it no longer slid up and down smoothly. (Fortunately I had a spare key of the same configuration from the numeric pad which was not being used). The other issue was I was concerned about the edges maybe becoming sharp or peeling off. Also it added some size to the edges which would have become problematic for the copper banding that (has yet to go on) the gap would not likely have been enough to allow the key to move freely.
The 7th image is an experiment to see about bending copper wire into the shape of letters then either inlaying them in the veneer or epoxying them to the top. I didn't like the look and scrapped the idea.
Finally you can see the next image has text underneath of the glass bead. That was an accident that I didn't get it sanded off enough. However..... I really like the possibility here especially with the keys that were not ground and posted. Rather than the paint being on the top just paint the keys in mirror image on the bottom before gluing them. This has 3 great advantages. First its a LOT easier to paint on a flat surface then on a curved piece of glass. Second it is naturally protected from wear. Third you could bake it (the paint I used allows that and probably sets better that way)
Finally I didn't bother to post an image of it but I tried some of that glass etching compound. It just does not work in this application. It etched the glass but with the curve and color it was virtually invisible. I really had to look and hold it just right to see that the stuff actually worked. I could feel it and as I said it did work just not something to bother with for this application.
Step 6: Metalwork
The metalwork consists of 3 parts. One part is cutting and bending metal for trim and banding. The second part is the artwork on the end caps. The third is engraving the name plate. I will break it into two sections here trim/banding and artwork.
Step 7: Metalwork - Trim and Banding
Tools
- Tin snips
- Jewelers saw (I didn't have one for any of this got one for christmas after it was all complete makes life way easier)
- Gunsmith hammer (just a small ball peen type hammer)
- Jewelers file
- Toothless flat pliers (didn't have these to start boooyyyy were these great when I got em)
- A good straight edge (I have a matte cutter I used a good metal ruler is fine)
- Bench block (I didn't even know what this was and had a piece which is pretty much exactly that which was just a weight in the bottom of an old charging station that I scrapped out)
- A bench pin (I don't have one didn't use one but it would help for sure)
- Ruler
- Calipers (didn't have these they are handy though)
- Small glasses flat head screw driver (I used this to mark the metal)
- Felt tip pen or wax pencil for marking the metal something that's not permanent
- Hot glue gun
Materials
- Thin gauge copper (Sorry I don't have the gauge or thickness as it wasn't on the packaging)
- Thin gauge aluminum (I used 2 different thicknesses for this project one was some sheet that I got from home depot used for banding the other was hobby stuff from Michaels again gauge not specified that was used for the embossing)
- Poster board or construction paper
When I did my first piece of trim for the key cavities I didn't have anything other than the tin snips, hammer, block, a chisel and the edge of my desk. I managed to make one and it looked fine though it took a very long time. So you don't need a lot of expensive tools to get this done. The right tools do however make it a lot easier. Michaels has a nice and cheap jewelers pliers kit and jewelers files for cheap get them the flat nosed pliers alone are worth it. The kit was pink but hey for $10 for all them instead of $15 for a single tool I couldn't resist. Good thing I'm secure in my masculinity eh.
The first thing I do is measure and mark out the holes. Then I add the amount of trim I want (I eyeballed this if you have calipers all the better make it the same). Then mark the interior cuts and draw a line from the interior to the edge of the hole (not the edge of the metal). This should be 45 degrees and will be where the metal folds down into the cavity. If you look at the pics you will see an example piece of copper marked out. If you look in the tools picture you can see my tin snips are HUGE so it was not at all easy making the small cuts. Drilling a hole and using a jewelers saw would be best. What I had to do was actually fold my metal, make a snip on either side (not all the way on the lines) so that I could get the snips in and finish the rest of the cuts. I then round my corners (by eye) with my snips though you can buy a tool that will cut them for you.
Now we should have a rectangular piece of metal with rounded corners, interior cut out and 45 degree angles snipped in the corners. Now we take our flat nosed pliers and gently place it on the bend line from the interior side. Make a bend (not harsh just smooth and not 90 degree yet) lift move a bit and repeat. Once you have the line roughed out you can put it on the block and hammer a bit or go back over it again with the pliers and finish the bend to 90 degrees.
If you look at the photos you will see the bottom banding made of the thicker gauge aluminum. This was an after thought and a solution to help with the problem of pull up I was having with veneer. It worked well and looked really good in my opinion. I cut a piece the width of the keyboard. I did a rough estimate on the width of the piece by using a piece of paper and folding it in the folds I wanted and to the height on the exterior of the keyboard and where I wanted to pinch it on the interior of the keyboard. We will be making a bend on the top (so sharp edge of metal isn't pointed up right where our hands go) then a bend at the point where it will meet the bottom of the keyboard then another bend to give us some distance to allow for the veneer and the thickness of the keyboards plastic. Finally a bend up into the back of the keyboard (back of the front edge that is). After we have that all bent as we want it stick the piece to the front and mark the cut outs where the lower part of the keyboard attaches to the upper part. I think the photos probably illustrate this better than my explanation.
Finally I made a small collar to go around the edges and back of the riser I built. For this I used a piece of poster board. Placed it at the right side, marked the angle and length, turned the card marked the back, turned the card again at that point and marked the angle and height. The result was a single template which looks like a ramp leading to platform to a ramp leading down. Sorry I didn't take photos of the template when I did it as originally I was going to use veneer on the edges of the nameplate riser that I added.
Make sure to use your jewelers file to soften the edges on any metal that will be exposed.
Step 8: Metalwork - Decorative
Originally I was just going to do plain old end caps. If you look through the images you can see a copper plate end cap I had made. I trimmed it closer to the edge of the board instead of up and over the lip. I could have done that because I could have glued it on. I could not do that with the decorative end cap that I ended up using because the glue would only be attached to some poster board and not to the metal so I used the lip as part of the way the piece is bound to the board.
The design I would appreciate if no one used since it is an original design just for my daughter. As mentioned originally I was just going to do plain copper. Somehow while visiting my sister for Thanksgiving I got it in my head that I wanted to do some engraving or something decorative. Unfortunately I had no experience in this and just started to wing it with some scrap pieces from other parts of the project. Once I started to feel like I could do something interesting with metal work (again completely lacking the tools at the time the first pieces I made using a pen and the gun smiths hammer really...) I realized getting real stylus's was gonna be necessary to do a good design and picked up a set. Also useful is a sandbag and a foam mat of some sort that firm but has give (daughters lalaloopsi house that was strewn about the house fit the bill). Once I knew I could do something and not make a complete mess of it I started sketching some designs. Since the project is based on water lily's and thus water and personally liking Norse and Celtic design as well as being a Tolkien fan (my nickname nearly 30 years ago was Frodo so...) anyway I decided to make this thing Elven and like Tolkien to borrow a bit from Norse mythology. The design is based on Jörmungandr, the "World Serpent" who is usually depicted biting his own tail. I didn't want to be so graphic on my daughters keyboard so I did a single "knot" to symbolize the continuity and made it a bit more deco or elf like (at least in my opinion). I like the way it came out personally.
Once I decided to go Elven and did the serpent I decided to name the keyboard like any good Elven made item it should have a name. I don't speak elvish and have never been that deep in the lore so I took some time to read up in dictionaries etc to give it the name "Touch of the lily" as best as I could make out that should be in elvish written in common speak "Appa Uin Indil" so that is the hand engraving I did. If I flubbed that up I guess let me know in the comments. I have not yet glued the plate on so I could rectify the situation I guess. I did a lot of versions of the plate embossing and even trying layered embossing with both aluminum and copper some with better results that others. In the end I felt that the simple hand etched version looked the best for the amount of space I had and the clean look I wanted for it.
Ok enough rambling about the how and why and on to how I did it.
Tools
- Same as the previous list
- Stylus
- Soft but firm item for smoothing. I used a couple of things though you probably should get a teflon tip stylus or a paper smudge pen. I used a wood fingernail pick and the plastic side of the eyeglass screwdriver with good success.
- Sand bag
- Foam mat (swiped mine from the kiddo on a toy she made a mess with and didn't play with)
- Stove or hotpad
- Old soup can or the like that can be put on the stove.
- Needle nose bent pliers
- Butter knife
- Clay sculpting tool shown above (not absolutely required but certainly helpful)
Materials
- Thin gauge copper sheet
- Thin gauge aluminum sheet
- Poster board
- Wax (I used paraffin and it worked but beeswax is the preferred I believe though it costs like 3x's more so...)
For the end caps the first thing I did was to trace the keyboard end in a notebook a few times so I had the dimensions to create my design.
Next I took a piece of poster board place the end of the keyboard on it upright so you can trace the outline. Now add some borders to that as you will want this piece to start out larger than you need and you will need some extra material all the way around for two reasons. First on the front, top and back you will be making bends with which to attach the copper and for the bottom you will fold it over the bottom of the uppers section of the keyboard to fasten it. Now cut that piece of aluminum out. The pics aren't in any great order but I hope you can understand the aluminum pics which show this. Next put that piece on the keyboard and using your fingers only rub the outline of the keyboard into the aluminum. You don't want to be folding it so much now just making sure to get the impression of the end of the keyboards outline on there. The reason for this is so when you are embossing your design you know the borders, have the bends that are going to be there anyway already in place so you don't end up with some odd crease or the like. The keyboard I have in many places including the ends curves both horizontally and vertically. It's not super noticeable but when you do the veneer you will really notice it. Metal is a bit more forgiving of this but it's good to get the shape on the metal before you start.
Now you should have a fairly flat piece in a piece a bit larger than the actual end with a raised outline of the keyboards end. Now draw your pattern in there with a felt tip marker or wax pen on the side that would be touching the keyboard. It can be permanent as this side will never be seen. Now take your piece and place it on the foam mat, take a stylus that matches the size you want to use and begin tracing your pattern. Don't force it and try to get it all to the depth you want at once. Go over it firmly but gently to start with at least to get your pattern down. Turn your piece over occasionally and use your smoothing tool on a hard flat surface like your jewelers block or even just a flat hard desktop. Take the tool and gently at first push down the metal that should be flat up to the raised areas to make the lines more crisp. Keep this up until you get the image embossed to the depth you want. Using the sand bag will let you emboss deeper but will distort the piece more and you will need to smooth it more and more often. I suggest practicing this some on smaller scrap pieces until you get the hang of it if you have never done this before.
Next you want to make your bends. This may involve trimming your piece. You also need to make some cuts for your corners and the front curve. The corner on the rear of the piece will need a 90 degree cut (45 degrees on either side of the center of the corner). The front will need multiple cuts to all the bend to go around the curve. I didn't do this perfect but only had 2 chances to get it right. Both came out ok but I found that more cuts at small degrees work better than a few cuts at wider angles. This one I can only say do what works. Look at the photos to get the idea if my explanation isn't clicking. Once you have your cuts in place you now need to make a bend of 180 degrees along the back, around to the top, and along the front curve. At this point though just make it about 90 degrees. Also make the bottom part about 90 degrees as well.
Now we are going to heat up the wax and pour it into the pattern we made. Why???? you may ask. Well the embossed image is very weak and just bumping it you could ruin your art. By putting the wax in (or some other firm but flexible material) you are making the piece solid and avoiding damage to your work. So. If you have something that's soft and can manually be pushed into the design by hand go for that. If you use paraffin like I did take an aluminum can, using pliers make a small lip (learned something making lead sinkers with my dad as a kid). Place wax in the can and place the can on the stove. Use low heat you want to heat it without flaming it up and it's not just gonna melt all at once. We don't want it boiling. Follow safety precautions on the label and use common sense when working with hot liquids and a stove.
With the wax melted take a pair of bent face pliers as a grip and pour the wax slowly into the design (the back side) and let it settle. Don't pour to much you just want to fill in the grooves you made. Once it cools you want to remove excess wax especially along the bends. A butter knife works good for the edges. I found using a sculpting tool like the one in the pics above works well to carve the wax to a uniform and even surface along the rest of the piece. Once all of this is done I cut a piece of poster board out and place it over the wax. I make it a nice tight fit to keep the wax from any other surfaces.
Next you will want to make a template for your copper using some poster board. Be as precise doing this as you can. First turn the edges of your aluminum further in but still not completely down to 180 degrees. I cut a strip one inch wide for my copper you need to decide how wide your piece will be and accommodate the 2 180 degree bends you will be adding to bind the copper to the aluminum. I start at the back, and fold my paper as I go using a pair of scissors to cut where the corners are. Take a look at the pictures to get an idea what the template looks like and what the end product looks like. You will unfold the paper template and use that to cut out your copper piece so take your time and be patient and precise here.
Now use your flat nosed pliers to bend your copper into shape. I do this and keep dry fitting it to my aluminum as I go to make sure I am matched up and on track.
Now it's time to join up the pieces. Bend you aluminum back, top and front to as close to 180 degrees as you can and still fit your copper in there. Now put your copper in (also with those bends as tight as you can get while still fitting in with the aluminum). Now pinch as much closed as you can with your fingers. Be careful here if you haven't filed burrs off you can cut or prick your fingers so file those burrs or wear gloves or suffer the consequences. Once you have the two pieces joined up firmly you will still have a pretty loose and weak joint. To fix this I use a stylus as a once over firm but not to hard. Next I take a chisel and place the piece on the foam or even the sand bag. I line the chisel up all the way to the edge of the seam from the back and give it a whack with the gunsmith hammer. We are trying to pinch the two metals together as tightly as we can without damaging the embossed piece. To much wax will make this hard so hopefully you took heed when I said scrape it and get your corners clear. After the chisel has been used all the way along at the top of the join go back and do it at an angle next to seal it the rest of the way down. You can get a bit more done with a hammer once the piece is on the board.
Ok now that's pretty much done until until you get your veneer on and are finishing it. At that point you may want to trim some of the copper, you may want to bend the outside edge of the copper 180 degrees (the part that will face you) so that it's a nice smooth edge. I didn't do this and wish I had. At the point I placed the end caps I was in burn out mode and made some rash decisions that I came to regret. Much to do with problems with the bottom curve of the veneer not holding well with the epoxy. I eventually got it sorted out and all was well but it kinda sent me in a tail spin mentally with the project and I started doing things like making cuts on the fly without thinking it out, hammering parts on etc... If you get frustrated take a break walk away and come back to it.
The name plate was pretty easy. I had actually engraved it on a scrap piece as practice and had no intention of using that specific piece. After some other attempts at different designs and approaches I noticed that poor little piece and liked it. I just used the sharp ended stylus generally used to punch holes to etch the text in there. I did it by hand with no guide though I might suggest you set yourself some wax guide lines at least or maybe even draw it out first. Anyway after that I cut a piece of veneer to match the size I wanted the plate to be. I traced around that on a piece of aluminum and gave it a border only as thick as the veneer. I cut 90 angles on each corner (45 in each direction). Took my flat pliers bent a small little lip up to 90 degrees. Placed the veneer in there and then used the hammer to lightly tap it in place pretty much permanently. This piece will be glued to the riser I carved in a hole I cut the veneer piece from. That will make the plate be almost on level with the veneer (slightly lifted).
Wow so this is what writing a novel is like.... On to the next stuff....
Step 9: Modifications to the Keyboard
Here I will explain modifications I made to the keyboard and why. For these modifications I just used my rotary sander and my dremel with a diamond wheel.
Slots for the LED back lighting
I went over this many times trying to decide where to cut the holes, how many LED's to use and so on. I suggest you draw out your keyboard cavities like I did and decide where to place your holes. In the end I made cuts that let an LED share 2 cavities at once wherever possible. For instance the F1-F4 keys and the main keys, The Print Screen keys to the insert keys etc. I cut a little slit close to the floor of the cavity so it's not noticeable when the keys are in. Be careful not to go cut crazy you don't want to make your keyboard structurally weak by doing this. Also consider that you have to fit LED's into the area that the slots you are cutting are at.
Removing the numeric keypad
You may notice that I have solar panels in my keyboard. At this point I haven't wired them up to the keyboard and may never do it. This is because I am at that burn out point on the project and I was getting far to frustrated. I didn't want to flub up the whole job right at the end after so much work. I may well come back and connect them up but for now they are just sitting in there. The way that I managed this though was using the rotary sander and grinding down the key holes to the level of the bottom of the cavity. Don't grind it all the way out. You will still have the mylar below and you don't want to get in a situation where something is pressing down on something there effectively making a key stuck on permanently. The other part of this is that I cut the rubber "mat" with the nipples at the point where it goes under the board there. Since there are no keys to press there they were just taking up space.
Cutting holes for the switches
I was planning on having 20 led's 10 each of blue and white with the ability to turn either or both off or on. Pay good attention where you cut there as my first cut even though I had held them in there with the lower and looked and thought all was good I messed up a bit and had to cut a second hole. There is a little piece that sticks out between the lower to the upper where the cord comes out and cutting that was not an option. Remember measure twice cut once. LOL sage advice from the guy that did and still flubbed it. Anyway not hard just be careful and patient.
Cutting a space for the joule thief circuit and coil
Even as small as I made my circuit (smaller than my thumbnail) I needed to make some cuts to get it to fit. I did this on the side of where the numeric keypad had been. I also had to cut some grooves in the vertical trusses of the keyboard upper so I could fit wires into other sections. Again as few cuts as possible to get the job done.
Painting the cavities silver
I painted my cavities silver so they would be more reflective (other than the numeric as that was fully covered and reflection is not what you want there). Some testors works great for that task though I used the glass paint. Gluing in some silver mylar would work fine too I would think.
Making a diffusion back light plate
I bought cheap poster frame and took the clear plastic out and cut that into a panel that fit under the keys. I roughed it with a sander to make it diffuse light and act as a back light panel. See pics above. I used a diamond burr to make the holes. This took a good deal of time to get cut out and fit up right. I cut a template out made of poster board first taping it to the front and using a marker to go through the key holes on the back to mark each keyhole. After I had that cut out and marked on the plastic I set it on the keyboard using the marked dots as center lines and then used a marker to draw the outer diameter of the keys visually looked down from above the keyboard.
Riser for the name plate
I added a riser that I carved out and epoxied to the keyboard which I will discuss more in the wood section.
Fitting aluminum in led socket gaps
I pinched some aluminum that's highly reflective into the gaps where the led's would go to help reflect as much light as possible.
Step 10: The Wood Veneer
When I was a kid there was a was a large church yard behind our house. On the other side of that was a house that myself and the other kids claimed a mean old man lived. There was a large fence and a large garage with piles and piles of old wood and occasionally loud sounds coming from it. We would sneak under or over the 8ft tall wooden privacy fence into the yard to check things out ever mindful not to be caught by the ogre living there. Well one day I got caught. As it turns out the ogre was a retired old man named John one of the nicest people you would ever want to meet in your life. John it turns out loved woodworking. He had a very well equipped shop in his converted garage and built clocks and other woodcraft items that he and his wife sold at art shows and such. His clocks were made of barn board. This was in Iowa over 30 years ago so he was pretty well ahead of his time on the whole reclaimed wood movement and had been going and helping farmers tear down their old barns and salvaging the lumber. John apparently enjoyed having me and my friend around to "help" him in the shop. By help I mean he taught us how to use his tools and let us use them whenever we wanted. At one point he even helped us build a go-cart out of a destroyed old big wheel by salvaging the rear wheels of that for the front wheels and giving us a pair of bike wheels for the rears. The rest of the go-cart was built entirely of wood including the steering wheel. The experience left an impression on me to this day. I learned people aren't always what you expect, that beautiful things can be found even in what others consider garbage, that ingenuity and creativity can solve most problems and that I absolutely loved working with wood.
Unfortunately I moved away to Florida and never saw John again and really didn't work with wood in any meaningful way again... Until lately. My best friend from high school came to visit from New Hampshire where he now lives while I was working on this project. During our discussion of what we had been doing with our lives he mentioned that he had been doing work refinishing high end antique wood veneer pieces. At that point in this project the only thing that was on the table for the keyboard was the glass beads. Well after that visit I really got it in my head that doing some wood veneer was the way to go. I don't know if I should cuss my buddy for reawakening my passion for wood and ultimately leading to my new found love of metalworking to boot or to thank him. Not having money and having a head full of ideas can suck but the enjoyment in the sense of accomplishment and artistic expression can't be beat.
I have seen a number of other wood keyboard projects (generally steampunk) most of which make use of nice plunge routers and other tools I don't have and are out of my price range. So when I decided wood my buddies wood veneer work inspired me in that veneer is much cheaper than larger full blocks of exotic woods. It also is more sustainable and cheaper to work with (with regard to tools). I had never worked with veneer at this point but had always appreciated the look of it especially on antique furniture. I had planned the whole time to make the mini itx box with some sort of wood this opened up new possibilities. Time to figure out how to work with the veneer.
Step 11: Wood Veneer - Cutting and Shaping
Tools
- Sharp scissors, tin snips or a blade (for big cuts)
- Exacto knife or sharp wood carving corner chisel or the like (for fine cuts)
- Large box preferably wood (I used a plastic storage box)
- Steam source (I used a steam wrinkle remover thing the gf had and was going to use a salvaged steam shark floor cleaner but the pump on it is on the fritz) (a tea kettle can even work)
- Some cloth to plug gaps in the box (I used an old t-shirt)
- Clamps (I used a bunch of binder clips at this point because sadly I had no clamps I did buy some clamps later for the gluing but for this part the binder clips worked just fine)
Materials
- Poster board
- Wood veneer (I used the rockler 2 ply cherry wood)
A quick note about veneers. They come in different thicknesses and types. The type I am working with is an all wood 2 ply veneer. Other types have paper backing and you will need to treat that differently. I can't offer much advice on that front other than read up on it if that's what you chose.
The first thing I did was to make a template with my poster board. You can see this in the second picture. I didn't make it completely accurate and left room for overhang into the negative space areas. I did this so that I had some room to work with positioning the veneer when it was cut. Later when it is glued the excess material is cut out with and exacto knife.
Next I cut out a piece of the veneer as you can see in the first picture. Now the amount of material I have is limited and I have need for it for other purposes. Given that I took a piece straight off the edge to minimize the amount of scrap. If you are really wanting to do this the best you may want to look at the whole piece and find where the grain is best suited to your likes.
Now that I have a piece the size of the keyboard I tape the template to the piece and cut out following the template.
At this point we have a rough piece. Now we want to form it. The keyboard is not a flat surface. It has a very tight radius bend on the front, it has some other bends here and there and we want to form the wood to that instead of trying to force it while dry and more brittle we will make a steam box so we will alter the wood to be in the shape of the keyboard.
Making the steambox
A steam box sounds like some big expensive contraption you have to order for a ridiculous price from a specialty shop right? Well not really. It is a box. A box with steam. Yes that's it. Surely we can make such a thing right? The preferred method I believe is to make a box out of wood. I used a plastic storage box. Really what you want is something large enough to house your work piece without touching the sides, top or bottom and is not going to burn, melt etc.
I had a steam shark floor cleaner steam thingy that I had scrapped a long while back and was wondering what I could use it for. I was going to use it for this but sadly while I had got it working when I scrapped it apparently I had just as quickly messed it up storing it in a box between then and now so it wasn't working.... what else could I make steam with... Well luckily the gf had bought one of those clothes wrinkle remover things recently and it was up to the task. It had a hose and everything SCORE. You could use a teapot even and a hose. Just need something to generate steam and get it into the box without burning yourself, burning down your home, or having the steam escape before it gets in the box.
So armed with a box, a t-shirt and a wrinkle remover I placed the hose to the box, sealed around it with the t-shirt and placed my piece (elevated we don't want it sitting in a pool of water when some of the steam condenses. I also made sure to have the lid tilt away from the piece so any condensation doesn't drip down on to the wood directly.
Steaming and forming
Now that we have our steam box place the work piece in there. Again elevated on something so it doesn't sit on the bottom. Make sure the "something" is not something that is going to bleed into the wood when wet and that it's something that can take the heat. Steam the piece for 1 - 1.5 hours.
Remove the piece from the steam box and first using your hands mold it around the keyboard the way you need it. Be careful with your piece it will bend just don't be too aggressive with it. You have limited time to work with it so quick but not rushed.
Once you have it pretty well formed up take your clamps or clips and clip it up. You want full coverage so you don't have waves or humps that form. You can use other thin pieces of wood to help with this but again make sure you don't have gaps and such of any size or you may end up with warped "humps and bumps". Look closely at some of the images and you will see what I mean. You can look at the later images and see when all the clips are on that it's removed. On the top of the board I used some heavy objects to keep the flat areas pressed down onto the keyboard. (yes that is a gutted ceiling fan with neodymium magnets from hard drives stuck to the outside maybe one day it will grow up and be a wind generator)
Now if you have it all formed up and good let it dry. I left mine for 48hrs. When I pulled it apart and looked the tight radius on the bottom was nice and dry but the center was still pretty damp. I took the piece and placed it in between 2 old computer panels. They worked well as they had vents cut in them, they were painted so rust bleeding onto the work was not an issue and they were nice and flat for the flat surface that needed bound. I placed the heavy objects on top and waited for another 48hrs. I also placed something at the base of the protruding tight radius to keep it from sagging back down. I live in South Florida so humidity sucks here.
One other note. Make sure if you have clamps or are using binders that have bare metal or even the potential of any bare metal that you put something in between it and the work piece. You don't want rust or other oxidation bleeding into the wood and staining it.
Step 12: Wood Veneer - Gluing
Tools
- Clamps, lots and lots of clamps (binder clips can be helpful too)
- Epoxy (I used locktite 5 min epoxy)
- A roller (I didn't have one sadly but it's a nice to have for sure)
- File
- Drill (not absolutely required but I need it for some fix see below)
- Wood shims
- Exacto or other cutting tool
Materials
- Alcohol (for cleaning up squeeze out read your epoxy to determine what will work for this)
- Cotton swabs
- A popsicle stick (or some other disposable mixing tool and applicator device)
- Aluminum foil or other disposable mixing surface for the epoxy (Of course if you can grab something that's going in the trash anyway use that instead)
Cutting the veneer
The first thing to do now that you have your veneer shaped and ready is to cut it to fit. On the edges I had a lip so I needed to cut slits to let the different levels seat on the board properly. Now originally I was going to do the whole top of the board as one piece. I was leery of cutting it and having joints. After talking to my friend he suggested that I cut it. I came to the decision to cut it. I came to this decision for a number of reasons. First the board is not flat so getting all the pieces pressed down on the curves etc was gonna be difficult to say the least and VERY prone to causing waves and weak glue points. Second using epoxy you have a VERY VERY small window to get the epoxy mixed, apply it, and get your clamps all bound. More work material means less time to get it right as a whole. Finally I don't have a good work space. As you can see in many of my pics my work space is a crowded computer desk and a tiny back porch. I really couldn't figure a way to get the entire board clamped down all at once in a clean and effective way.
So.... My advice is to take your time and consider where best to make cuts and cut your piece into to smaller more manageable pieces at locations that will minimize the chance of a bad seam joint.
Preparing the keyboard
Before you glue you want to rough the surface of the keyboard. I mean really rough it up. Use a file. I might also suggest using a very fine drill bit and making a number of small holes to act as "pins" for the epoxy. This wasn't such a big deal on flat portions of my keyboard but I had a real melt down with the tight radius on the front. The epoxy pulled up in multiple places on the top and the bottom. The pressure squeezed the epoxy to those areas and when I went to cut out the overhang it broke the seal basically and the veneer lifted. Ultimately (after a lot of hair pulling cussing and general frustration) I managed to drill some holes from the bottom side without damaging the veneer above. I then managed to squeeze some more epoxy into the lift points and clamp it again. It worked but save yourself the stress and trouble and make sure that your surface has plenty of area for the epoxy to bind to.
Preparing your veneer
I don't have a lot to say on this. When you get your veneer it should have instructions regarding application. Like humidity levels, sanding etc. Follow those directions for best results.
Gluing it up
First off a piece of advice. Before you actually decide to mix your epoxy and get going start off by doing a dry run. Place all your clamps where you think you want them. Get them placed and make sure they are firm and are going to hold and apply pressure where you need it. This may sound like extra work but trust me especially when you get to the tight radius you want to do this. Really trust me. This comes into play especially on the tight radius of the front where I use shims to help clamp the piece evenly. I included a number of pictures of clamping different sections so have a look.
Get a timer and set it to the time you have for your epoxy. Now mix your epoxy. Quickly apply it to the back of your piece and to the keyboard. Place the piece. If you have a roller use it to roll over the whole working piece. If you don't work it by hand. Get your clamps on. Now wait. The epoxy I used says it is workable for 5 minutes, sets in 20 minutes and is cured in 24 hrs. I leave my clamps on the full 24 hrs.
Step 13: Wood Veneer - Finishing
Tools
- Paintbrush
- Exacto knife
- Dremel with sanding bit
- Sandpaper
Materials
- Stain
- Paper towels (or better cotton rag)
- Polyurethane sealant (I used spray)
- Wood filler (hopefully you don't need it I didn't)
- Tissue paper
Finishing the fitting
Now that the pieces are glued in you are likely to have some overhang into the cavities and over the edges. For this where you can use an exacto knife or other good sharp cutting tool and remove that excess. Other places I had to use a dremel with a sanding bit and GENTLY and SLOWLY remove some of the excess. Be careful here you don't want to overheat using a dremel or tear up the wood or release the epoxy. Just take your time and be patient.
Sanding
Now you may have had problems with your seams or have some flaws. If you do use a non shrink sandable wood filler or putty. I didn't have to do this luckily I got all my seams on good (anywhere visible at least) and had no real knicks or flaws to fix. If you do follow the instructions for your product of choice (pay attention about color matching). Now time to sand. Do this by hand. You don't want to use power tools for this really you don't. Wood veneer is thin and you don't want to end up sanding into the glue layer between the ply. I used 320-600 grit flexible hobby sandpaper and it worked for me.
Staining
This is clearly a personal choice with a ton of options. I used a natural stain from Varathane. I wanted to keep the color light but again this is all personal choice. I like the way the natural brought out the color. I applied the stain with a brush let sit for about 10 minutes and then wiped it off with a paper towel. Not ideal but I like the look and it worked well. You may want to sand and restain I didn't feel I needed to. I got the color and application I felt was good and stuck with it.
Sealing
This is another matter of personal taste. I went with a clear satin poly spray. They make tons of finishes pick what works for you. To get the spray on there I filled all the cavities with tissue paper took the piece outside and lightly sprayed it. Follow the instructions of the product you choose.
Word of advice
I suggest before you dive in and start staining and sealing your piece that you take a scrap piece of your veneer and stain and seal it with what you plan on using to make sure it comes out the way you wanted. I had some other stains on hand and tried them (the whole time suspecting I wanted natural but wanting to make sure) and used the poly to make sure it came out the way I wanted. Nothing would be worse then spending all that time and effort and then applying something and finding out the way your wood reacts to it is not what you expected.
Also other than stains there are plenty of chemical treatments out there. I would urge you to take the time to make sure if you choose a route like that you know what it's reaction will be with the veneer. Remember it's a thin layer of plywood you are dealing with so the glue that binds the 2 plies together is something you will want to consider if you are using bases, solvents or acids. Some of these treatments also decay or alter the wood in some way which works nice on larger pieces but may cause problems with such a thin layer of wood. Be wary I hear people say without really understanding what some of these do with the wood that it's always "The wood reacting with the tannin" that is not all that some of these treatments do. Take the time to understand them if you use them.
Step 14: Electronics
Ok as mentioned in previous sections. I did not complete wiring up my solar panels and LED's. Partly due to wanting to finish the project and put it behind me and partly because of my concern that frustration would get the better of me and I might damage the project rendering the whole thing useless. I may come back later and finish wiring it up. I just had to walk away for now. I will however explain what I did.
I wired up a jewel thief circuit. I won't go into detail about that as there are a ton of instructables, youtube videos, and websites where you can get plenty of information about them, what they do, how they work and how to wire them. I will tell you that I pulled my transistors out of an old TV that I scrapped out and the coil I got from a laptop or PSU or who knows something else that I scrapped. I got a C1815 and an A105.
The solar panels and rechargeable batteries came from the dollar store. They were part of a Halloween yard light thing as pictured. I cut the panels out (leaving the plastic in a very thin layer as a housing) and then painted them with black testors paint.
I bought the LED's (ultra bright 3mm) blue and white, switches, and battery holder from Tayda Electronics and RadioShack. I just couldn't find 2 switches of the same type from scrap and while I cut out the battery holders from the solar yard item I just didn't like how flimsy they were so I bought one.
I decided to use a joule thief because I was running 20 LED's in total and I managed to get this circuit to drive them with just 2 AAA batteries (though I eventually went up to 3). I actually managed to drive all 20 off of a single AAA but that was so dim it was worthless. The reason this is important is that I have limited output from the solar cells to charge the batteries. I took readings in the area that the keyboard would be and depending on what lights were on I got between .4V and 1.2V so with 6 panels I would have (in series) a range of 2.4V to 7.2V. Now the more normal condition would be between 1V - 1.2V (based on readings with the mulitmeter) so thats 6V - 7.2V but very low amp output. So I figured I would wire them in series and parallel and could manage to get 4V - 4.8V which should be enough to charge the 3.6V for 3 AAA batteries. If the battery voltage dipped below its 3.6V it would still drive the LED's and I could always swap the rechargeable batteries out as I had them mounted to the exterior.
Initially I planned on making 2 joule thief circuits and using 2 sets of 2 AAA batteries. I scrapped that idea when I realized I could drive all 20 off of one circuit (didn't expect that tbh) and that space was becoming a real concern. That threw a wrench in my works with just 2 switches however and I would have needed to add a third switch as an ON/OFF or completely remove the switches (not easy to do now they were glued in) and change them to a multifunction switch with multiple positions, ON BLUE, ON WHITE, ON BOTH, OFF. Not in the cards.
If you decide to go this route and do the LED's (would have been nice my breadboarding and putting some in place looked really good) here's a gotcha. I hot glued the switches in place. This was a problem the glue got into the slide mechanism and bound it up. They still worked but didn't go all the way each way and required more force to switch than it should which I was worried would damage the veneer if used with any frequency. And ooooohhhh boy does my daughter LOVE lights. Her "glow shows" are loud, long and active lol.
The design was going to have the battery holder attached to the bottom of the keyboard. There was plenty of room from testing for this to fit. I soldered on some female connectors. I then wired 2 male connectors to some wires which would be the lead and attached to the upper of the keyboard. That way if you need to take the keyboard apart some time later it's very easy to just unplug the battery and the 2 sections are not bound together.
Step 15: In Closing
Boy I have been working on this instructable for 2 days now. Wow so much. I still feel like I left things out or didn't clarify enough. If you have questions I will be happy to answer any I can. If you have suggestions I am all ears. Thanks for taking the time to read this novel. If I have entered any contests please give me a vote.
Step 16: Bits and Bobs
I will use this section to add anything I forgot etc.
One thing you may have noticed and I mentioned a couple of times was the "riser" section of the keyboard. For this I took a hobby piece of pine and carved it to shape. First I measured where I wanted it to sit. I made it go over the top of the led's for num lock, scroll lock etc. So I also drilled holes for that. I then heavily sanded the piece with a mini vibrating sander to make it nice and flat. I then epoxied the piece to the keyboard. A tip I used small dowels (toothpicks would work) to help keep the holes from the keyboard to join with the holes in the riser. That also helped keep the riser in its proper place while clamped.
I placed my veneer on the board and cut slits to let part of the veneer follow the plate up and the parts that stay level with the keyboard remain down. I then determined where I wanted the plate. I traced the plate I had made then cut that out of the veneer. When I glued down that section I actually used normal yellow wood glue to join the riser and the veneer. After it was in place I poked holes through my veneer and used a jewelers file to widen the holes for the led light to come through. I then used little plastic "gems" that are faceted like a diamond to go over the holes. These have a mirrored surface on the bottom so I had to scrape that off in the middle where it would line up in the hole. Then a dab of hot glue.
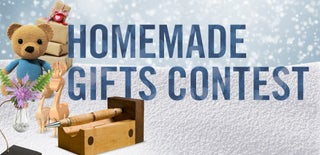
Participated in the
Homemade Gifts Contest
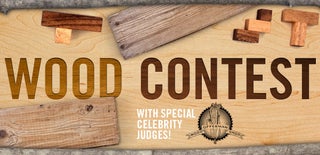
Participated in the
Wood Contest
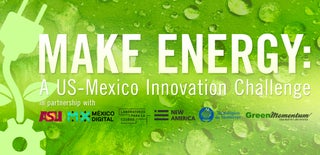
Participated in the
MAKE ENERGY: A US-Mexico Innovation Challenge