Introduction: Emergency Fire Starter
I originally made this to replace an old fire starter I had lost on a trip. It includes a carbide window breaker, a carbon steel pick, a striker-wheel and flint, and a few inches of jute tinder twine that also functions as a key lanyard. Id like to note right from the beginning that this is a fairly involved build. The tools I used were as follows:
-Vertical mill and assorted cutting bits
-Micro lathe
-Belt sander
-Assorted hand tools (bit drivers, squares, and clamps).
-Various consumables (glues, tapes, Popsicle sticks)
I should note that there is never only one single way to complete a project. I always believe in improvising to solve problems, but only within reason. A rule I always follow is if something sounds like a bad idea, it probably is. Always follow appropriate safety precautions and never take unnecessary risks. That said, lets proceed with the necessary materials. One final note: I will periodically dimensions such as the size of bits and screws, but always perform your own measurements before making a cut or drilling a hole.
Step 1: Materials
The first picture depicts all the necessary materials. Each one is labeled with an annotation in the picture, an are as follows:
-5/32" OD aluminium tube
-1/8" solid brass rod
-3/32" music wire
-3/8" brass bar stock
-1/8" BROKEN carbide end mill
-3/16 (10-24) stainless steel screw
-cheep flip top lighter (I found these online for under $2)
-Jute twine
-Kevlar cord
As a preliminary step, begin by harvesting parts from the lighter. In the one I had, all that was necessary was to drill out the single aluminum rivet that held the striker wheel in place. The parts you want to save are the spring, the flint, and the striker wheel.
**I learned the hard way that striker wheels only work in ONE direction. Make sure to mount your wheel with so the teeth scrape forward at the flint when you operate it. (See last picture)
Step 2: Lathe Work
After milling, the shape will no longer be able to mounted in the lathe, so we want to do any turning or boring first.
Begin by cutting off a 2.5" section of bar stock. I chose brass, with a 3/8" diameter simply because that's what I had handy. Cut the piece greater than the desired length to allow for facing off each end on the lathe.
**It is very important to face off each end carefully, and make sure each end is exactly square with the length of the piece. This becomes very important in a later step when we begin to mill the sides.
After you are sure each side is exactly square, proceed to bore a 7/64" hole entirely through the piece. This will be the hole that accepts the flint from our lighter. Because the hole is so small, be sure to bore very slowly, stopping often to clear out any chips. For a hole this deep, I like to bore half way through one side, then turn the work piece around and begin again from the other side.
Once the hole is bored, taper one side of the rod. I used the angled edge of a lathe bit, and cut until the small diameter matched the head of my 10-24 screw. In my case, the small diameter ended up being 5/16" across. Once the taper was finished, drill and tap the tapered side of the rod. I used a 10-24 tap, and a 5/32" drill bit. Be sure to tap it so that the entire length of your screw fits into the rod. On mine, I used 1/2" long screw.
This concludes the lathe work, and it is safe to proceed to milling.
Step 3: Milling Work
For milling, I chose to utilize the flat faces on each end of the piece to clamp it down. Before removing the piece from the lathe, use it to make a mark 1/2" down from the untapered size of the work piece. Because we need to mill all the way to the end of the tapered side, use a couple of brass nuts to act as a spacer between the end of your piece and the jaws of your vice. Insert the drill bit into the tapered side, and use it to support the nuts while you mount the piece in the vice.
The key to a successful cut is first making sure all your parts are exactly square, and then ensuring you have a rigid tool setup. Use setup blocks, or just uncut bar stock to make sure that the piece is mounted parallel to the base of the vice. Next. use a square to make sure that the piece forms a right angle to the face of the jaws
**It is extremely important to make sure the piece forms a right angle to the jaws. If it is not mounted squarely, it could pop out of place during mulling. This is also the reason why it is important to make sure the sides of the piece are exactly square.
Be sure that the jaws of your vice are close tightly. Check the piece for rigidity by hand before you begin. If it pops out of place, the set up is not square or is not tightened sufficiently, and must be redone to maintain safety.
It is extremely important to make very shallow cuts, and move the table slowly. Cut from the very bottom of the tapered side, all the way up to the mark 1/2" from the untapered end. On mine, I continued to cut until the bit reached the outside of the 5/16" tapered face. Once this was completed, I proceeded to do the same on the opposite side. The end result should be two parallel flat faces, each extending to the 1/2" mark from the top of the piece.
At the end, your piece should accept the screw you chose, and have two flat faces. Now we can proceed to mounting the striker wheel.
Step 4: Mounting the Striker Wheel
Now that we have two parallel faces, we grip these in the jaws of the vice. Again, ensure your piece is square to the vice. I used a 1/8" scribe tip to center the mill with the hole we bored in step one. Use a 1/8" end mill to cut out a slot for the striker wheel. For mine I had, I cut to a depth of 3/8" from the top of the piece, and also had to widen it to 0.14" to accommodate the striker wheel.
Once the slot was cut, I chose to mount the piece directly to the table with step blocks. Again, make sure all your faces are square. To ensure the drill bit went through the center of the piece, I used a jig to align the chuck. Admittedly it wasn't the most elegant solution, but it worked well enough for me. Find a bit to match the hole in the striker wheel, and drill straight through, placing the center of the hole 1/8" from the top of the untapered side. My striker-wheel accepted a 1/8" drill-bit, but I highly recommend that you make your own measurements.
**Because this is a through hole, be careful not to drill into the bed of your equipment. In my case, segment I was drilling into fit in between the T slots on the table.
Once the hole is drilled, cut an angle that will reveal more of the striker wheel for your finger to grip. To do this, I used a chauffeur cutter with a 60°.
Finally, take a shaft that fits in the hole you just made, (1/8" in my case) and cut it off, leaving roughly 1/16" excess on each side. Use a hammer and tap the ends of the shaft that protrude from each side to mushroom it out slightly. This will ensure it does not come loose. Once this is done, use a dremel or a file to remove any excess shaft that still protrudes, and buff out any scratches with fine sandpaper.
Finally, we can install the glass breaker and key lanyard.
Step 5: **(Please Read)**Mount the Carbide Glass Breaker.
I had originally included the steps to attach the broken shank from a 1/8" carbide end mill to use as a glass breaker. I recently learned that carbide dust is particularly nasty to inhale. Not at all being an expert, I didn't feel comfortable putting the information out without being properly educated. Best wishes to all; please stay safe.
Step 6: Assembly
The last step in assembly is to cut the music wire to size. If you notice, the completed glass breaker (left) has a very short point protruding from the screw. The easiest way I found to size this is to first load the flint and spring from the flip top lighter into the hole. Then sharpen the section that protrudes from the screw, and keep shortening. and sharpening until all the threads screw in.
I chose to add a bracket underneath the glass breaker to accept a keying or lanyard. The lanyard I used is weaved from jute and Kevlar. Each loop is encased in heat shrink tubing to prevent the metal edges from cutting the cord over time. Jute can be used as tinder to start a fire, and the Kevlar simply prevents the cord from breaking too readily. Be careful to make sure that the end of your bracket does not interfere with use of the glass breaker. I had this problem, but remedied it by just flipping it upside down.
Step 7: Conclusion
For anyone still reading I thank you greatly for taking time out of your day to view my project. I know I've much to learn still. Healthy criticism is greatly appreciated. Best wishes, and stay safe.
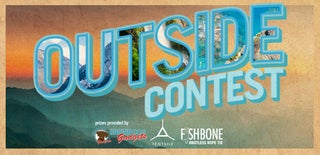
Second Prize in the
Outside Contest