Introduction: Enlight3d - Triple Light Fixture
This is a light fixture that I call "Enlighted".
The design is made with Autodesk Fusion 360 and I made a video series that is a step by step guide of how I designed this 3d printed lamp. Autodesk Fusion 360 is the best designing software that I can think about. User-friendly and comes with everything that a designer, a machinist and a 3d printer enthusiast needs. It's also free for Students and Hobbyists.
The design is made having in mind that it will be printed with an FFF or FDM printer which is the most common and affordable household desktop printer type. The filament is Pla which is the easiest filament to print.
I have to note that I am a beginner at 3d drawing software and your comment are welcome.
I also made this project for the 3d printing contest so good luck to everybody.
Step 1: Bill of Materials and Tools
- 3d printer.
- Filament for the 3d printer: 1kg PrimaValue PLA 20$
- 1kg Excelvan PLA 20$
- 2x Led economy bulbs so they operate at low temperature especially if you print this with PLA: 6$ for both
- A circular fluorecent light. I picked the one with the smallest perimeter and it is 22watts: 5$
- A mechanical ballast, a starter and a socket for the fluo lamp and for the starter: 5$
- 2x E14 socket for the light bulbs with their locking nut and a screw : 4$ for both
- 3x on off switches for the lamps: 1$
- Led strip (less than half a meter). I used 20pixels/meter neopixel: 9$
- A microcontroller for the led strip. I used the adafruit trinket mini 5v: 6$
- some dupont connectors and wires
Tools
- pliers
- files
- sandpaper
- soldering iron
- exacto knife
- flat head screwdriver
- glue
Total cost:74$ for succesfully printing the parts at the first try
Step 2: Designing With Fusion 360
The whole designing part is captured at a video series that made as comprehensive and short as I could. The whole idea and experimenting with fusion to have that design took me about a month. I learned a lot about fusion 360 from instructable class with jon-a-tron and he deserves a great respect.
Please keep in mind that the offsets may need some alternating depending what your 3d printer can print.
I may need to change some dimentions especially at hinges and wiring tunnel.
I also loved the cloud rendering feature of fusion.
Correction: At the flap mirror function use it for body and not for component that is seen on the video. This gives less components and makes one body from the original and the mirrored one. later you can promote that body to component.
PS:sorry for the same video.move to the youtube playlist to see all of them
Step 3: Wiring Diagram
Sorry for the free hand drawing but it is pretty straightforward.
The microcontroller I used is the adafruit trinket. In their site there are plenty project and tutorials about it so it's pretty simple to connect the ledstrip and start playing with the leds. For now I just used a library for the ledstrip, but there is gonna be an update really soon with a code for the led strip.
Be very careful while working with main voltage it could be deadly.
Step 4: Printing Intro
While designing the lamp I didn't realize how much filament will this thing need and I run out at half.
You need more than 1.5 kg of filament for the whole project. And that is only if you succesfully print all the parts on the first try. I had some failed parts unfortunately and waste a lot of material.
Which slicer to use?
I haven't set with a slicer yet but the parts have been printed with the cura engine embedded at the Repetier Host. Although I would like to use the latest version of cura or the type A cura which have some nice features like cubic infill patern and a dozen of option for every aspect of the printing procedure. Anyway printing with the latest cura resulted at extruder cloging, temperature failing and other ugly things. I will experiment furthemore with tha latest cura sometime.
At the embeded videos I choose support and overhang at 89 degrees. This means that only the horizontal faces will be printed with support and crossed fingers for the other surfaces. I have to mention that the flaps came out better with no support. I mean the hinges of the flaps.
I have to note that my printer is a home made frankenstein machine that is not the most reliable but it's the only one I have for now.
Also I have to emphasize something to people that making their own 3d printers: DO NOT buy chinese stuff. They will fail before they leave china. Buy branded products and support the people that contribute to the development of the 3d printing community.
Step 5: Printed Parts and Fusion Files
In order to fit the parts to my bed I splited them at fusion at 4 parts for the main body.
My bed dimentions are 340x190mm so the large parts fit ok.
But I understand that the average hobbyist has a printer with a 200x200mm so I splited the main body at 6 parts
The parts are available with the addition of the fusion drawing so anyone can tweak it.
Attachments
arm.stl
bottom_1.stl
bottom_2.stl
bottom_flap.stl
bottom_hinges_1.stl
bottom_hinges_2.stl
nut.stl
pulley.stl
screw.stl
top_1.stl
top_2.stl
top_flap.stl
bottom_1small.stl
bottom_2small.stl
bottom_3small.stl
bottom_4small.stl
bottom_hinges_small_1.stl
bottom_hinges_small_2.stl
bottom_hinges_small_3.stl
bottom_hinges_small_4.stl
top_1small.stl
top_2small.stl
top_3small.stl
top_4small.stl
screw_spacer.stl
Step 6: Printing the Parts
The top part came out with some artifacts (some ugly some not to be concerned) maybe because I was experimenting with the speed during the print. I printed it with 130mm/s but I found out that 120 was stable so I set that speed with the bottom part and it came better than I expected.
There are a lof of z axis artifacts by the way like wobbling and waves but that's what I my printer is capable for the moment. Althought I have some upgrades in mind.
You can see the comparison between the support structures on the photos. The grid support resulted in flatter surface but the line support was faster to print and easier to remove.
I also changed the color during the print for the part where leds are placed and it was amazing thought I should have used white filament but I liked the constrast between grey and green.
The grey filament has a matte finish in constrast with the green that is more shinny.
The enlighted letters printed just great on the bottom part but the logo on the top part is not acceptable.
The flaps printed both with and without support on the hinges. I have to admit that without support the were cleaner and maybe more detailed on the hinges.
The screw and nut for the moving flaps printed nicely after some alterations on the fusion drawings that are updated on the uploaded files.
check the video for the "motion link"
Step 7: Post Processing
Just remove cut file and be patient with the supports.
I used a 150grid sandpaper strip for the flap cylinder and come out perfect and polished like it was injection molded.
The top part has been sanded on the corner because it has lines of filament but it is still bad.
Step 8: Assembly
So how this thing is kept in place? You can glue the parts together it will work ok after some sanding on the surfaces. But the screw is needed to revolve freely and the nut to be guided up and down. The screw is kept in place between the locking nut of the E14 lamp socket and the bottom body. there is more. The bottom E14 and the top E14 socket must be connected and so that the top locking nut keeps everything in place.
On a big printer it could be just two parts. One top and one bottom so the locking rings of the E14 sockets will keep everything tight without the need for glueing. With this way the lamp is serviceable.
I also needed a spacer for the bottom socket in order to give a little space to the nut to revolute freely.
The circular lamp is placed on top of double sided tape.
The arms and flaps are fitted and functioning good enough.
Step 9: Semi-Final Object
Sorry folks but after some failed prints I run out of filament and can't demonstrate the whole object but I made my best from the parts that came out good.
I will definitely update the whole finished lamp as soon as I print the rest of the parts and fix my extruder that wear out after 3 full days of printing (chinese stuff).
Step 10: Future Updates
I am looking forward to finish the whole print but I also have some other things in mind.
I am planning on using a esp8266 for the ledstips and the 3switches for the lamps.
It would be great to control the whole thing from a smartphone app.
Also a personal ambition is to make this project a final product but will see until then keep making stuff.
Thanks.
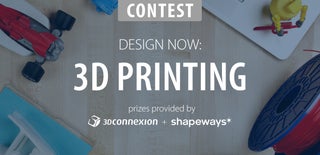
Participated in the
Design Now: 3D Design Contest 2016