Introduction: Entertainment Center With Floating Speakers Built Using Pocket Hole Joinery
For anyone with a home theatre system an entertainment center is a great way to organize and display your various components. However, the problem I had was finding one that would fit in the limited space I had available. For that reason I decided to design and build one myself. The goal was to give it a compact yet distinctive appearance while having it complement some other furniture I had made for our family room. To accomplish this I angled the front of the unit giving it a terraced effect and hung the speakers to make them appear to float off the floor. I built the project using pocket hole joinery which is a relatively easy and effective method for creating casual furniture pieces such as this.The steps that follow will document the process for building this entertainment center or one of your own design while, hopefully, illustrating the basics of pocket hole joinery.
Step 1: Tool & Materials List
The list of tools to complete this project include a pocket hole jig. For those new to pocket hole joinery, the Kreg company makes a very nice, moderately price pocket hole jig that I have used on a number of projects. While I highly recommend it, I'm sure there are probably other similar products to choose from.
Tool List
Table Saw
Miter Saw (optional)
Router (optional)
Kreg Pocket Hole Jig
Power Drill
Clamps (minimum of 4 heavy duty 3' clamps)
Random Orbit (or other) Sander
Rubber Mallet
Materials List
4' x 4' sheet of 3/4" Oak plywood for shelves (for this size table)
2 - 4" x 4" x 48" long S4S Oak for the legs
1" x 4" x 10' S4S Oak board for shelf fronts, side trim, rear trim and lower top trim
1/2" x 3' S4S Oak board for top trim
Kreg Pocket Hole Screws (1 1/4" fine)
Wood Glue (to attach trim pieces)
Stain (color or colors of your choice)
Finish (Watco brand oil preferred)
3/8" Thick Glass Top (size determined by overall entertainment center dimensions - mine was 18" x 37")
Optional: Oak for Table top (in lieu of glasstop mentioned in the previous step)
Step 2: Planning the Design
When designing a woodworking project, a basic drawing of the piece including dimensions is an important first step. However, many times some additional pre-production preparation also proves helpful. Since the angled front legs in my design added to the complexity of the project I decided to incorporate the following procedures:
- First I drew a full size layout (side view) of my project. Using this template as a guide allowed me to check the accuracy of my parts (primarily the legs and dados) both before and after any cuts were made.
- Next I made a test sample of the overall form from scrap lumber (prior to cutting any pieces from good material) to make sure I was on the right track.*
(*Note: Building a test sample convinced me that I could improve the appearance of the unit by changing the location of the dados so the shelves projected past the front legs rather than being placed behind them.)
Dimensions: Since audio and video components come in a variety of shapes and sizes, the dimensions for an entertainment center will always be determined by your specific home entertainment system. For this reason, the dimensions listed below are meant to serve only as a general guide and provide an understanding of the thought process in how I designed my project.
Component List / Shelf location
Bottom shelf: stereo speaker
2nd shelf: audio receiver
3rd shelf: multiple CD player
4th shelf: blue ray player and Apple TV
Dimensions and Shelf Spacing
Overall width of the unit = 24 1/4" from the outside of the legs (excludes glass top supports and glass top)
Overall height of the unit = 24 3/8" including the 3/8" thick glass top
Width of shelves between the legs = 18 1/2" (overall width of 20" before being set in 3/4" dados in legs)
Spacing between the shelves:
Space between 1st and 2nd shelf = 6 1/2"
Space between 2nd and 3rd shelf = 6 1/2"
Space between 3rd and 4th shelf = 4 1/4"
Space between 4th shelf and glass top = 1 3/4"
These dimensions allowed a minimum of approximately 1/2" spacing between the component and the inside of each leg as well as 1/4" to 1/2" clearance between the top of the component and the bottom of the shelf above it.
Step 3: Creating the Legs - Cutting to Length, Determining the Angle & Milling Leg to Thickness
The legs are cut from two pieces of 48" long 4"x4" S4S oak. S4S material is surfaced on all four sides and is sold pre-packaged at many home centers. This type of wood, while more expensive, eliminates the need for additional complex milling requiring planers and jointers, equipment not often used by amateur woodworkers and hobbyists.
Steps to create the legs:
- Square both ends of each 4"x4" by removing a small amount of material with your miter saw.
- Cut each 4"x4" so there is a difference of an inch (or more) between the two halves. The extra length is needed when making angle cuts on the front legs since doing so affects the actual height of the leg (as seen in the attached photos).
- Using your miter saw, set the angle for the front legs. Mark the direction of the cut at both the top and bottom of each leg so you don't make a mistake. The angle used on my front legs was 12 degrees (note: the greater the angle the smaller the top shelf will be). After cutting the angles on the front legs, place them on the template (at the proper angle) and line up the rear legs to determine how much material to remove so they are the same height as the front legs.
- Mark and cut the rear legs. Re-check, as seen in the photos to assure all legs match and are the correct length. If necessary re-cut.
- Finally, rip the four legs on the table saw to you desired thickness. I chose 2 7/8" square legs.
Step 4: Creating the Legs - Cutting Dados for the Shelves
Cutting the dados in the legs is perhaps the most important and challenging step in building this project. The angle of the front legs needs to be precisely replicated in each dado for the shelves to be level. This task is complicated by the fact that the angle on miter gauge will have to be reversed and the opposite miter slot used when cutting the opposing front leg on the table saw. For these reasons, think this step through very carefully and, most importantly, take your time!
Note: The dados are cut on the opposing inside edge of each leg with only the front leg dados being cut on an angle.
Marking the dados on the work pieces
The pictures included here should be helpful in lining up the dados.
- First, using a straight edge (I used a piece of wood) to set the legs on a level plane, put a front and rear leg in position (photo #2).
- Next place a 3/4" thick piece of plywood on top of the legs at the bottom shelf position, measuring carefully to make sure it is the proper distance from the bottom of both the front and rear leg (photo #3) and mark the location of the dado.
- Place a second piece of 3/4" thick plywood in position, measure and mark the location of the second shelf (photo #4).
- Repeat the process until the dados for all the shelves have been marked (picture #5).
Cutting the dados on the table saw
The most important thing to remember when cutting the dados is that each front leg will be cut using a different miter slot on the table saw and that the angle set on the miter gauge will also have to be reversed. As seen in photos #6 and #7, the accuracy of the angle set on the miter gauge can be confirmed by placing a board in the miter gauge slot and, using a square to make sure it is perfectly vertical, butting the bottom of the leg against it. If they don't meet perfectly, the angle on miter gauge will need to be adjusted.
Photos #6 through #9 illustrate using an auxiliary fence and stop block on the miter gauge to guarantee accurate positioning while avoiding chip out on the work piece. A clamp is also recommended to firmly secure the work piece to the miter gauge.
Cutting grooves to mount speaker brackets
If you want to "float" your sound system speakers you will need to purchase generic metal brackets at Home Depot or another hardware store. Just make sure your bracket is fairly sturdy and has at least four mounting holes. Speakers tend to be heavy and can sag without proper support. More on this later. The last two pictures should provide a basic idea of what you need. Finally, measure carefully and cut a groove (the thickness of the bracket) in each rear leg at the desired height (note: take the size of your vacuum cleaner power head into consideration - your wife or girlfriend will appreciate being able to vacuum under the speakers, if possible). Finally, position the brackets in the grooves, mark the hole locations and drill the mounting holes. Doing this before assembling the project will alleviate the potential problem of trying to drill the holes in a very tight space.
Step 5: Making the Shelves & Adding Pocket Holes
Before I explain how I made the shelves for this project I want to point out that there are three different approaches you can take - with mine being the most involved. For that reason you may want to consider these suggestions:
Option #1 - Use a pre-packaged roll of oak veneer (thin strips, pre-glued for easy iron on) to hide the raw plywood edges of the shelves. Benefit: Using this method will simplify construction by eliminating the need to make solid wood trim pieces for the sides and back of the shelves.Trade off: The front edge of the shelf will have a less distinctive appearance without a bevel to set it off.
Option #2 - Cut small pieces of hardwood ( 1/2" to 1" thick) that can be glued to the front of the shelves. Benefit: You can bevel the front of the shelf and have it look identical to the shelves I made with a lot less work. Trade off: If you want to maintain a consistent look to your trim you will have to fabricate twelve individual trim pieces for the sides and back of the unit. The alternative option would be to use oak veneer strips on the sides and back of the shelves.
Option #3 - Make the shelves the way I did:
Why did I do it this way? I'm still asking myself the same question! Actually, since I had some nice Oak hardwood boards already on hand I decided why not put them to good use. Also, I thought it would look better not to have a seam showing where the trim met the shelf. At 3 1/2" wide, any seam that might show would be covered by the equipment. Doing it this way also gave me the opportunity to see just how well I could join two boards together using pocket hole joinery. So, in actuality, it was a learning experience as well as an experiment.
Note:3/4" plywood is not a true 3/4" thick (it's about 1/16" less than that). This is important because if you are using 3/4" hardwood as edging you will need to mill it down to the thickness of the plywood. For this reason, be sure that the dados cut in the legs are the proper thickness! Even though I was aware of this I mistakenly cut 3/4" dados in the legs. Details on how I resolved this problem will be explained in the assembly step
DRILLING THE POCKET HOLES
As seen in the photos, pocket holes need to be drilled at the outside edges of the shelves. The holes are drilled in pairs, with one pair required for each of the four legs.
(Note: Because my trim was 3 1/2" wide I drilled the pocket holes in the front trim pieces before assembling the shelves. After the shelf pieces were glued and screwed together I drilled the back holes in the plywood. The pocket holes running the length of the trim pieces were used to screw the trim to the plywood shelves)
Using the Kreg jig is very simple:
The depth of the hole is based on the thickness of the work piece, in this case 3/4". This is set by locking a depth adjustment ring to the drill bit using a guide on the Kreg jig.
The pocket holes are drilled on the underside of the shelf and will not be visible after assembly. Make sure you remember to flip the shelf over before doing any drilling!
Determine the position of the first hole, clamp the shelf in the jig and drill the hole. Then, reposition the shelf and drill a second hole. Space the holes to provide solid contact with the leg when screwed together. My shelf holes were centered in the leg and were approximately 1" apart.
***Additional photos of the pocket holes can be found in the assembly step***
Step 6: Staining & Finishing
I'm a big believer in staining and finishing all my project parts prior to assembly. While doing so is especially relevant when using more than one color of stain on a project, it's a process that makes this critical step much easier and can save you a lot of grief on almost any project you build.
I have just a few simple suggestions when it comes to staining and finishing this project:
- I prefer using an inexpensive foam brush instead of a bristle brush to apply wood stain and also when applying a water based polyurethane finish. These brushes are very inexpensive and can be thrown away after use.
- When using oil as a finish on a project I apply it using a rag.
- When applying stain, first brush it on against the grain. Then brush the same area again, this time going with the grain. Doing so guarantees complete coverage. I remove excess stain with a rag after several minutes, rubbing with the grain.
- Finish all project parts using Watco Danish Oil. It is super easy to apply and provides excellent results. Watco also makes finishes in a number of colors so you can stain and finish in one step if you like.
- Using a water based polyurethane finish, I gave the shelves two coats for a little added protection. You can skip this step if you prefer as it really isn't critical.
Step 7: Assembly
Assembly of this project is relatively simple:
NO GLUE REQUIRED: Pocket hold joinery creates an extremely strong joint without the need to use wood glue. This is important due to the rather lengthy assembly time required for this project. For this reason, I recommend that the entertainment center be fully assembled before adding any screws. This 'dry fit' gives you the opportunity to confirm the structural integrity of the unit and a chance to make any minor adjustments should they be needed. Even a slow curing glue would begin bonding before the unit was fully assembled and make this step impossible.
First: Lay a front and rear leg on a flat work surface and carefully insert the four shelves, beginning with the top shelf. I positioned the shelf in the front leg first and then made sure the back edge of the shelf was perfectly flush with the back of the rear leg. The shelves should fit snugly in the dados if they have been cut correctly.*
* Remember that I mistakenly cut my dados a full 3/4" wide instead of the thickness of the plywood. This meant that the dados on my rear legs were too large to securely hold the plywood. The pictures in this section (numbers 6 &7) show how I solved that problem and are included only for the purpose of illustration. As long as you mill any hardwood for your shelves to the thickness of the plywood you won't have to do the extra work shown here, so make it easy on yourself and learn from my mistake!
Second: When all the shelves are in place, carefully add the other front and rear leg to the shelf assembly. You may need to use a rubber mallet to tap the legs fully into the dados so be sure all the shelves line up properly. Photo #5 shows how I visually checked my shelf alignment.
Third: Stand up the assembled unit and clamp securely before screwing the assembly together with pocket hole screws. You will need four clamps: two for the front legs and two for the back legs. Locate the clamps between the bottom two shelves and the top two shelves (I mistakenly deleted my clamping photos, sorry). Be sure to check that the legs sit perfectly flat on your work surface and that the shelves and rear legs are level before you begin the final assembly.
Fourth: Screw the unit together using 1 1/4" fine Kreg pocket hole screws. When finished, remove the clamps. The next step will be to add trim to the exposed plywood edges.
Step 8: Trimming the Exposed Plywood Edges
After assembly, the exposed edges of the plywood (sides and back) of the unit will need to be covered with matching oak trim. How simple or elaborate you make these pieces is up to you. It should be noted that, with the speakers mounted and the entertainment center placed in a corner or against a wall, there is very little that can be seen. That makes using a simple oak veneer a very easy and practical alternative. However, never one to do things the easy way I made my trim pieces out of solid oak. Once cut and finished I glued them to the plywood and used painters tape to hold them in place until the glue dried. The attached pictures are included to provide an overview of the approach I took. However, the size and shape of any trim you choose to make is really up to you.
Photo 1: Assembled unit without side or back trim pieces
Photo 2: A cardboard template to use as a guide when cutting the trim pieces to size (one for each shelf) and a finished piece of trim
Photo 3: Side trim added to bare plywood edges. Held in place with painters tape.
Photo 4: Painters tape on left leg used to position the back trim for each shelf properly
Photo 5: All rear shelf trim glued in place
Photo 6: Rear view of trim with painters tape removed
Step 9: Adding Supports for the Glass Top
The final step in the construction of this entertainment center is to trim out the top of the legs. This is done by adding pieces that connect each front leg to the matching rear leg. This decorative and functional oak trim adds strength to the unit, improves the appearance and serves to better distribute the weight load on the glass (or wood) top.
I used two pieces to accomplish this task. First, I glued and screwed a piece of 3/4" oak with a bevelled edge to each pair of legs. Next I glued a slightly larger piece of 1/2" oak on top of the first piece (see the accompanying photos).
Finally, I purchased a 3/8" thick piece of glass (18" x 37") to place on top of the supports. If you prefer a wood top I would suggest 3/4" thickness. I sized the glass so that it just covered the stereo system speakers.
An interesting fact about using glass for the top:
Online calculators will tell you how much weight each different thickness of glass can support. The 3/8" thick glass in the size I ordered supports up to 208 pounds which is more than adequate for my 90 pound flat screen television.
Step 10: Some Pointers on Mounting the Stereo Speakers
As I said earlier, I wanted to have the speakers appear to float off the floor since I thought it would add a really cool and distinctive appearance to the project. However, it wasn't as easy as I thought it would be. Even my relatively small speakers sagged because their weight. For this reason, if your system speakers are too big (or heavy), floating them will require the fix outlined here or, in some cases, may not be an option for you.
How I solved the problem:
As you see from the attached photos, I glued small pieces of wood to the back of my speakers allowing me to fasten the speaker to the mounting bracket with two screws rather than one (I had tried a single screw first). Unfortunately this didn't completely solve the problem so I fabricated wooden support brackets to glue to the rear legs. Placed in the bottom corner of each speaker and hugging the inside edges (side and bottom) of the speaker frame they prevent the speaker from sagging and keep it level.
Attaching the speaker support brackets:
Have a hand clamp ready at the ready. Add glue to the back of the wooden support bracket. Then, before pressing the bracket to the leg, carefully position the speaker so it is level. When positioned to your satisfaction, press and hold the bracket in place. Quickly add a hand clamp to hold the support bracket in place until the glue dries.
Step 11: Add Your Components, Sit Back and Enjoy
Pocket hole joinery is a wonderful option when building casual furniture pieces and provides great results with only a limited skill set and basic tools being required. While often disparaged by experienced woodworkers it is a perfectly acceptable construction technique when traditional woodworking methods aren't critical to a project. Look around your own home and you will find that today's mass produced furniture often incorporates this construction technique.
A custom entertainment center like this is a relatively easy project to build and will give your audio and video components a beautiful home. If this instructable inspires you to create a unit of your own then it was well worth the time and effort it took putting it together. Good luck and happy woodworking.
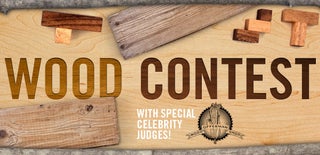
Participated in the
Wood Contest