Introduction: Entry Portal Arches
I was referred to a client by a friend that was requesting a few pieces for their moving Yoga exhibition. After some discussion we decided that I was a good candidate to build the arches they were imagining. This would be my biggest project on the CNC and the biggest project since designing and building the CNC, shown in my first instructable.
Supplies
Step 1: Client Expectations and Delivering the Bid
These are the drawing provided to me by the client. Using these I made some quick drawing and calculations about how big a three piece arch could be made from 4x8 sheets of plywood. I then sent these back to make sure they were happy with the adjustments needed and then I proceeded with the bid. The turn around time was very quick so after getting materials approximated I sent them a number that reflected that I was about to drop everything and work 16 hours a day for the next two weeks. They accepted the bid and I proceeded.
Step 2: Basic Design Elements and CAD
The big challenge for this was that the arches would need to be dissembled and moved from event to event. The attachment points needed to be seamless. The side pieces would slide onto the angled insert on the base plate and when the top piece was affixed using hidden furniture locks the arch would not be able to move in any direction.
I then began the long task of designing an arch in cad (SolidWorks) with inner supports and grooves for skinning. The lower parts were reinforced with mulitple cross brasses for the interface with the support base knowing that people would be bumping into them and they would get beat up during their many assemblies and disassembles.
When the arch design was finished I made copies and then modified them to get the different sizes and then modeled them as a group. Following that I began the long process of laying out all the parts into flat cut sheets. I believe there were 18 sheets.
Step 3: Tool Paths in ArtCam
Using the Flat models from solid works I exported DXF files and imported the DXF files into ArtCaM. For most of my wood CNC projects I use 1/8th inch 2 flute upcut bits. The simple line picture shows the edged of the work in black and the tool path created for the 1/8th inch bit in maroon. The color photo shows the simulation done by ArtCam of the parts cut from the sheet stock. The tool paths are then saved as Gcode in a .TAP extension file which Mach3 can interpret.
Step 4: Cutting on the CNC Router
Before Cutting I had to choose a plywood to use. I visited my local retailer and viewed the options. In the end I chose a 1/2in Luan because it is very light but quite strong. I was put it between bass wood and pine. Be careful though it splinters naturally and they are very sharp.
While the basic idea of loading a sheet and a file into the machine are simple enough, the actual process of remembering which sheet you are on, which step on that sheet and keeping all the parts straight takes significant effort. Go slow and triple check. One simple mistake could cost days.
Step 5: Assembly of the Parts Into Sections
With all the parts coming off the machine well labeled, the parts were sorted into piles and then the piles were process one by one into sections. I used lots of clamps, wood glue and a brad nailer to hold the wood while the glue dried.
Step 6: Weld the Aluminum Bases
I decided to make the bases out of mulitple pieces of 1"x 2" 1/4 wall rectangular tubing. The angled vertical piece was two lengths of 2x2 square tubing to make a 2x4. I capped the ends with 1" x 1/4" strip.
I chose multiple pieces of tube because the extra inner walls would provide the needed extra strength. The problem here is that aluminum shrinks a lot when welded and as I progressed across the piece it began to bow upward. I countered this by matching welds on the bottom to bring the piece back to flat.
Step 7: Initial Assembly of Sections in to Full Arches
Here are the pictures of my first assembly of the arches. Before they were skinned I affixed the hidden hardware inside them and put them together. The picture of the many small parts on the CNC table are the bits I used to mount the hardware into the arches. I failed to take a picture of the step where I took all of those little parts and made a jig to hold them in place to route out the lateral hold from the other side. As you can see from the simple cad picture there is a hole from the top and the side.
Step 8: Skinning and Finishing
After the arches were assembled we began the process of skinning the inside and outside of them. In the fist photo you can see the bottom section is skinned while the top portion is still open. We skinned them in an assembled state to ensure we had nice tight gaps between the sections. After the skinning was complete we filled all the holes and gaps with wood filler and sanded them smooth. I then gave them a simple white base coat so that the vinyl they would be covered with would have a nice surface to stick to.
Step 9: Build the Crates
Since the Arches would be moving around the country they needed nice crates to keep them safe. This was quite the process given that all the pieces were curved. I spaced them off the ground so that a fork lift could get under them and made them nice and sturdy to protect my precious cargo. The arches were separated from each other using bits of carpet.
Step 10: Ship Them Out and Enjoy Your New Entry Portal.
The client wrapped the arches with white vinyl on the outside and red on the inside and then up-lit them. I am very happy with the outcome.
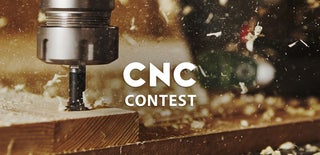
Participated in the
CNC Contest 2020