Introduction: Epoxy Resin and Walnut LED Night Lamp
This time I had the main goal to try a very first-time epoxy resin casting. I’ll show you how from epoxy resin, American walnut, and cheap electronics I made this stunning LED night lamp.
How I did it - you can check by looking DIY video or you can follow up instructions bellow.
For this project you will need:
Materials:
Walnut 20x20x120mm and 20x20x200 ( or other your preferred wood)
Wood glue, CA glue
Transparent epoxy resing for deep casting
Fairy string LED light
Plastic sheets for casting form (mold)
Hot glue
Micro USB connector
Buffing pad and automotive polishing paste
Danish oil for wood finish
Sandpaper 400, 800, 1000, 1500 grit.
Electric tape
Tools:
Belt sander with 80 grit sandpaper
Miter saw
Palm router
Orbital sander with 120, 240 and 320 grit sandpaper
Drill and bits
Clamps and some other usual bits and bobs which is laying around the workshop.
Cutters
Soldering iron and solder
Step 1: Materials
One of the main materials will be those American walnut pieces. Since I don't have a thickness planer - I ordered to prepare all workpieces of the required size. They all are in 20 by 20 millimeters. Talking about length - the longer ones are in 200, and the shorter in 120-millimeter length.
Step 2: The First Glue Up
The very first step is to glue every 4 pieces together by misaligning them in a random pattern. The same procedure was done with longer pieces too.
When the glue was dried - prepared the surface for the next glue-up by sanding down to get a nice flat surface.
Step 3: The Second Glue-up
The second glue-up was similar to the first one. The only difference was that this time I glued 4 already pre-glued boards to a solid rectangular wood block.
Glue dried and I got two solid walnut blocks.
Step 4: Flattening Ends
Used miter saw and flattened one end of each block. Sacrificial plywood pieces helped to avoid any walnut tear outs.
Cleaned cut ends with the sandpaper. Take a look at that nice end grain!
Step 5: Few Holes for Electronics
I used a palm router and milled a hole on the flat walnut block end. Here will be hidden all electronics parts.
Drilled 3-millimeter hole all the way thru the block. Thru this hole will be wired LEDs from top to bottom.
Step 6: Preparing Wood Surface for the Epoxy
I mixed a small part of the same epoxy resin which will be used later and covered all wood surfaces which will have a contact with epoxy resin pour. This should seal the wood and prevent the formation of bubbles in the casting.
Step 7: The Electronics
I bought this fairy string LED light with 100pcs of individual colored LEDs connected inline. It could be powered from any USB power source, like the power bank, smartphone charger, laptop and etc. My fairy string light version had a controller that gives a few different operating modes. However most of the time I’m planning to use this one - constant light.
Cut the power wire and managed it all the way thru. I used hot glue to seal the hole and fixed the wire in it.
Step 8: The Casting Mold
From random plastic that layed around I start making the outer form for epoxy resin pour. Placed on the side a straight reference and adjusted to my preferred spacing of wood pieces. To seal up all edges I used hot glue. All seams should be weather tight because the resin will find the smallest hole or crack and will follow out. I take my time and sealed all joints to avoid the mentioned situation. On the top, I made a small barrier to keep epoxy resin overfill.
Step 9: The Epoxy Resing
Ok, the epoxy resin. I bought locally this highly transparent and UV stabilized epoxy casting resin. It’s designed to use in deep pours, like up to 10 centimeters. Mine will be only 8 centimeters deep so I should work just fine. I poured the resing and hardener according to the indicated mixing ratio and mixed very very well. After that, I gave a light transparent color tone by adding a few drops of turquoise pigment. Once again a bit of mixing and I poured the resin into the form.
This is very slow curing epoxy resin so all bubbles will escape naturally. Here is the casting after 20 minutes - I can’t see any of bubbles (last picture).
Step 10: Taking Out
This epoxy requires 3 days to fully cure, but I left it a bit longer. One week later the resin was rock solid and it was the perfect time to remove from the mold.
Step 11: Lot of Sanding
To clean all sides I used a belt sander and 80 grit sandpaper. When the job was done here I changed it to an orbital sander and passed with 120, 240, and 320 grit sandpaper.
After that moved to the finer grits and sanded by hand. Started with 400 grit, then 800 grit, 1000 and finished with 1500 grit sandpaper.
Step 12: Polishing the Epoxy
To bring back the shine I used 8 centimeters buffing pad on a drill and a regular automotive polishing paste. After good 20minutes of polishing the shine is back.
Step 13: Working on Electronic Part
It is time to rework the electronic part so, that It will fit in our prepared place. First of all, I need to desolder a power on/off button and relocate it. Second - I no need this USB connector anymore, so it should be desoldered too. All electronics should fit inside this hole.
Step 14: Some Soldering
To fix the power button in needed place I desoldered from the mainboard and made a simple housing with extended two wires. To fix it in the palace I use CA glue and activator. Soldered micro USB port to the power IN terminals, extended wires from the ON/OFF button, and lastly soldered the fairy light wires.
Step 15: Closing the Internals of Light
Finished up with some electric tape and hidden inside the hole. CA glue helped to fix permanently the micro USB port in needed place. With the thin piece of walnut and a few drops of wood glue - closed the hole.
Step 16: Finishing the Wood
Finished up with some electric tape and hidden inside the hole. CA glue helped to fix permanently the micro USB port in needed place. With the thin piece of walnut and a few drops of wood glue - closed the hole.
Step 17: The Result
And here it is - clear epoxy resin and walnut fairy string LED lamp.
As for the very first project with the epoxy resin casting - the result exceeded my expectations. Despite a few small mistakes made during the project - I’m more than happy with the finished product. It’s a pity that the camera cannot transmit a real view of how it looks in real. If you ever tried to film a lamp or any light source, you understand my pain.
Step 18: BONUS
By the way, do you remember those two offcuts left by flattening the main pieces? They weren’t thrown out. I made another smaller and darker lamp version.
I used epoxy resin made for casting for the first time, but certainly not the last. I will definitely use it again in the future, especially in projects where I will combine several different materials by using epoxy resin.
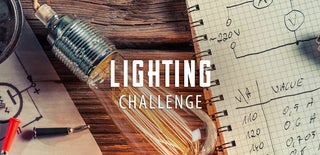
Grand Prize in the
Lighting Challenge