Introduction: Escamotable
Hey, how you doing?
Here's a shelf that one can fit anywhere without spending much time. It was a well thought out design which took months of sketching and prototyping. I would like to acknowledge my friends and fellow team members, Ms. Bhavya Gupta and Mr. Sarthak Chopra for their commitment and support throughout the process.
Escamotable is a French word meaning "foldable". Yep, it means that this shelf is a foldable shelf. It began life as an elegant solution to a common problem of urban living. Realizing the limits of my cramped downtown studio apartment, I sat out to create a stylish, high-quality, and versatile shelving system that would be functional while occupying as little space in my apartment as possible.
We traded design work for shop time and materials at our university studio, and hand crafted all of the parts from solid wood. Every shelf is 16" wide X 9" deep and a minimal 1/2" thick. A modular rail-based design along with customization options, allowing it to be tailored to the style or size of any space.
Also this shelf has no nails hammered and can be assembled or de-assembled at ease.
Let's get onto the steps on as to how I made it.
Step 1: Selecting the Right Material
I chose soft wood for the intricate parts that required heavy carving and high finish. Hard wood was used to make the pivots and the rotating mechanism. Wood can be easily worked on and maneuvered.
Infact, the same can be achieved in Aluminium. It is premium and can be given different finishes depending on the interests of the consumer. Also this can just be one shelf among the many. One can create as many required and place them in rows and columns on the wall according to dimensions of the wall.
Each shelf pivots with a smooth drop-resisted movement to reveal its underside, featuring interchangeable, customizable artwork and materials. It can be anything ranging from a whiteboard to a part of a complete painting/artwork. Every shelf can have a part of an artwork/painting/graphic design, when all shelves put together, they appear as a whole. (See the PDF, for a clearer understanding) Even the clean wood/aluminium finishes look damn good.
This shelf has a white acrylic on the underside that can be used as whiteboard if required.
Attachments
Step 2: Components/Parts to Be Made
One basic shelf would have a total of 4 parts.
2 pivots, 1 rail cover, 1 rail, and the shelf.
Step 3: Making the Rail
The rail is the main part of the entire shelf on which all other components fit. Infact, this is the only component that goes directly on the wall with the help of screws.
The rail is made by making a groove on the wood of appropriate dimensions. The grove is nothing but a square slit made on the two edges (longer edges) of the wood. This was achieved with the help of a portable hand operated router machine.
After that the holes were made at every 4" using a drill machine for the screws that would hold the rail against the wall.
Step 4: Making the Pivots
Now, this is one among the "tough jobs".
The pivots are the ones that hold the shelf intact and help rotate them.
As mentioned earlier, hard wood was used to made this part as this part is delicate and tends to break when made with a lighter/weaker material. I strongly advise to use a hard material to make this.
As displayed in the picture, the pivot has a groove cut out that fits exactly on the grove made on the rail. This is something we call the lock-key mechanism. A hole of reasonable size was also made (as in the picture) to fit the shelf. This is how the shelf would actually be able to rotate. On the face of the pivot, a hole is drilled for the screw to hold the pivot along the rail. (also in the picture)
Step 5: Making the Rail Cover
This is the next "tough job" to be done.
The basic purpose of the rail cover is to hide the big ugly screws that are used to hold the rail against the wall.
This part was again made using the router machine, along with the milling machine. Since, this part also slides on the rail, the groove to be made is the same as made in the pivots. As this cant be done easily without some heavy machinery or large scale machines, this has to be made in two parts (as in the picture) and then have to be stuck together using a strong adhesive. Yet again as mentioned, no nails have been used throughout the making of the shelf. The groove carved out of the wood must exactly match the rail and not be loose or tight while sliding on the rail. Small drill holes are made on the bottom of the cover. This would have screws that would hold the cover with the rail and not let them move when the entire shelf is assembled and put on the wall.
No one likes things to get shaky when something is placed on the shelf.
Step 6: Making the Shelf
The shelf is the part that one actually uses to place something on top of a shelf.
This is 16" wide X 8.25" deep. The remaining 0.75" from the total 9" is used up by the rod or the pivot pin (cylindrical protruding part) that fits right inside the holes that were made in the pivot.
This part again is made in 2 sub-parts put together. One is the flat wooden board and the other is the cylindrical part.
The flat wooden board is nothing but a wooden board cut into 16" X 9" dimension with two small squares cut on two adjacent corners along the longer edge.
The pivot pin (cylindrical) is made using a milling machine (as in the picture). A hard wood must be used for this. For those who don't have a milling machine, can either get this part made separately or make this the harder way, that is, by using a flat file for wood. Again one has to make sure that the pivot pin fits just right in the pivot hole. Even a slightly loose or tight behavior can ruin the mechanism. On the two sides of the wood make the cylindrical rods and all along the middle keep it slightly curved matching the pivot. (see the pictures for a clearer view)
Step 7: Grinding and Smoothening All the Surfaces
Now that all the components have been made, its time to make them smooth along all the surfaces. Make sure that you wear protective glasses and mask at all times while doing this. An angle grinder is used all over the surfaces of all parts from top to bottom to smooth the rough wood. Make sure that the rotating disc you attach to the grinder has a fine grade specially used for wooden surfaces. Using a tougher grade disc would simply eat up your wood and would leave a depression on the wood. One has to constantly keep the angle grinder moving.
After the angle grinder has been moved all over the surfaces of all the components, I used a very fine 6 grade emery paper and rub it uniformly all over the wooden surfaces. After doing so I used a superfine 9-10 grade emery paper and repeated the same. By now the wood had become so smooth that one could move his hand on the wood without feeling anything stopping.
Step 8: Trial (assembling All Parts to Check They're Working)
Assembling all the components/parts to check if the mechanism is working smooth, to check if the screws fit the drill holes perfectly ...
Also mount the shelf on the wall or any surface possible just to ensure that the shelf is perpendicular to the wall while its open and right parallel to the wall while its close.
Also the rail cover and the pivots should be able to slide smoothly on the rail without exertion of much force. Screw and tight all the parts together.
Step 9: Cutting the Acrylic Sheet for the White Board
Using the shelf, take the markings of the dimensions on the white acrylic sheet. (see the pictures) Use the try square to check if all edges are at perfect right angles.
After the markings are made on the acrylic sheet, cut it using a jigsaw cutter.
Stick this cut out on the underside of the shelf using a strong adhesive.
Once that's stuck tight, using an angle grinder smooth the edges of the sheet. Give the finishing touches with an emery paper.
Step 10: Applying Varnish and Wood Polish
On every wooden part of the shelf apply a thin layer of varnish using a clean cloth. Make sure to clean the surface of any dust. Let it dry in the sun as only then the real shine would appear. If required put a second coating of varnish after the first coat completely dries.
After all the coatings of varnish dries completely, prepare the surface for wood polish by sanding the surface of uneven or excessive varnish layers by using an emery paper. Wood polish is an oil or wax which help protect wood. Wood polish should be applied at least twice. Do not take and apply excessive polish on the surface. Little at a time is enough.
Now what many don't really know is the process of rubbing real smooth metal, preferably stainless steel at the end. Rubbing smooth metal on the wooden surfaces supresses all the wooden grains and makes the surface as smooth as melted butter. The process of smoothing and leveling intermediate layers of finish is known as cutting back. This is done with the help of steel wool. If one could get the steel wool then that's great, otherwise, a smooth steel metal piece is also fine.
Step 11: Putting All Parts Together on the Wall
After all the hard work, it's now time to assemble all parts together and finally put the shelf on the wall.
The first and the only part to go on the wall using screws and drill holes on the wall is the rail. Each unit should be installed on a flat and smooth wall surface with enough strength and structure to support the weight of the shelves. Use countersunk, flat head mounting hardware appropriate for the wall material. Attach the rail to a smooth and flat wall surface.
Starting from one end of the rail, slide over and attach one pivot using a flat head screw. Starting from the opposite end of the rail, slide over the rail cover followed by another pivot. Position the shelf (bottom facing down) between the two pivots and slide the pivot pins into the matching pivot holes. Insert a flat head screw into the pivot and tighten. Continue the steps if more such shelves are there.
Its normal for all shelves not to lay completely flat and even. However, the set screws beneath the rail cover can be tightened to raise and adjust the shelf that is too low. Slightly tighten each set screw a bit at a time until the shelf is at the desired height.
The shelf is finally put up on the wall.
Happy Shelving.
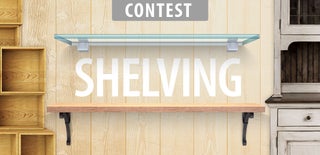
Participated in the
Shelving Contest 2016