Introduction: Extremely Low Cost 3D Printable 3D Printer / Plotter / CNC Machine
In this Instructable I will talk about how to build a basic three axis CNC machine. the machine itself relies on easy to find parts and the mechanical parts are all 3D printed. all of the 3D printed parts are designed by me and the files are provided, though they may need to be slightly modified depending on your specific parts. I don't intend this as a "Build this it is the best machine ever" type of Instructable. I am simply trying to dictate what is truly possible using free easy to use sdesign software and a little time. I am a 17 year old with no training on CAD at all and this shows how advanced 3d design has become, and how accessible it is to anybody. This is truly an educational Instructable, but the machine also does work.
Just a quick reminder before we get started, this instructable is being entered in the Dremel 3D Design contest, so if you enjoyed the work that I put into this and learned something from it, or just liked the machine, feel free to vote for me. Thanks, it is greatly appreciated
Step 1: Overview of Parts
--Printed parts-- (all files for the parts, with matching names to each part are provided below)
-X-Axis Assembly
-Y-Axis Assembly
-Bed Mount- this could be used as a bed for simple things like pen plotting, but if you need a really flat bed, this has mounting holes to attach a leveled bed ontop.
-Z-Axis Assembly
-Z Assembly Stilts (2 Of These)
-Z Stilts Connecting Rods (2 Of These)
-Motor Mount Pins- these are little pins that get glued in to hold the motors on. it makes it so you dont need to buy screws, just print and glue on.
-Stabilizer Piece- This is sorta optional, but if there is wobble in any axis, these can be glued on to the slide to tighten it up and make it slide really nicely.
OPTIONAL: Pen Mount Z Piece- This was a test for the Z axis that is a simple pen mount and moves on the Z.
---------------------------------------------------------------------------------------------------------------------------------
--Non-printed parts--
-Base Piece- Simply grab a decently big piece of flat wood, and that will work great for mounting everything.
-Motors**- The motors are simply DVD drive head motors. they are super easy to get out of dvd drives and already have a screw on them to move the different axis of the machine
-Linear Rods**- These rods are taken directly from the DVD drive laser assembly. you can get them out of the same drives that you get the motors from.
-Ribbon Cable- This ribbon cable for wireing the motors can be taken out of an old computer. if you are already taking old computers apart for the DVD drives, this should be super easy to find in the form of IDE cables.
-Driver Board- This will be a RAMPS board which is easily found on ebay
Here is a link to a search that will bring you options to choose from for the driver board - Link
**These parts are taken from old DVD drives. in total you will need three DVD drives.
---------------------------------------------------------------------------------------------------------------------------------
**update on current electronics setup**
As requested in the comments, i am going to really quickly explain what i am using to drive my build of this machine. For my testing i am currently using L298 motor drivers and an arduino mega. i decided to do this for testing instead of go with the RAMPS because i had the parts on hand. i still recommend using the RAMPS boards because of the easiness of setup with standard 3d printing software. if you have any questions on how to get everything wired and working, feel free to drop a comment!!
---------------------------------------------------------------------------------------------------------------------------------
--Tools--
The tools for this project are very simple, you will need a phillips screwdriver, a hot glue gun, and a 3D printer.
Attachments
Step 2: X Axis/Base
This piece holds the x and y assembly's. the whole piece is 3d printed and prints on its side without any support. the motor mounts on using the motor mount pins that can also be printed using the provided files.
Step 3: X Slide and Y Motor Mount
This part slides on the x axis under power of the X motor, but also holds the y motor
Step 4: Assembly of the Different Pieces Into Bigger Components
By now all we have talked about is the different pieces of the machine. we have not gone into detail on how it should go together. Assuming that you are using the same parts as me, which may not always be the case, this is relatively easy to do.
-------------------------
--Motor Attachment--
Start by taking your motor and placing it in the motor mount in the position it will be attached. then take the motor pins that you printed and place them first through the motor holes, then through the mount. You should have a small piece of the pin protruding through the back.. Hold your motor firmly to the mount, and aply hot glue to the protruding pin on the back. Hold until the glue is dry. Repeat this step with the other motors. the steps are the same for each axis.
-------------------------
--Attaching the X and Y together--
Start by taking your linear rods and pushing them through the press fit holes about an inch through (picture above). Once the rods are through, take your Y piece and push it on. After the Y piece is on, simply push the rids through to the other press fit. Repeat this step on the Y axis to attach the bed.
-------------------------
At this point in the process you should a piece that looks like the 5th photo.
-------------------------
Step 5: Bringing Those Bigger Components Together
In this step we will finish the whole mechanical aspect of this machine.
-------------------
First we are going to start out by mounting the X-Assembly, with the Y and Bed on top, onto the wooden base. I did not design any mounting holes into the X-assembly, so you can drill holes to screw it down, or simply hot glue it down. The most important thing is that its flat. and as level as possible. This is described by the first photo, but I can help if needed.
-------------------
Now we will attach the whole Z-Assembly as one piece. Take the stilts and use the mounting holes and some small machine screws to attach it to the Z-Assembly. Now take the pieces of the connecting rods and put some glue into the holes and press them together. depending on what glue you use, you may have to let it dry for a while. glue the Connecting Rods into the notches in the Stilts. The second two photos show the screws, as well as the gluing of the connecting rods.
-------------------
Now we will mount the Z-assembly onto the Base. Place it over the X and Y and line center of the large hole up with the corner of the bed as seen in the photo. Now take screws and screw it to the wood base. if you don't have wood screws, just hot glue it down. You can see in the fourth photo how the center of the circle is lined up with the corner of the bed.
--------------------------------------
You should now have a device with a with a freely moving X, Y and Z, as seen in the last photo on this step. try to move them by hand and make sure they move freely and smoothly.
Step 6: Taking It Further, Ideas for Future Expansion / Conclusion
Up to this point I have simply spoken about the mechanical aspects of getting a 3 Axis Gantry system built. This design could easily hold a 3D print head and be converted to a 3D printer, though all we went into detail about here was getting the basic mechanics done. The above photo is from the other 3d printer I own. It is simply the hot end, which could be mounted and used with my gantry design. all that wold be need is a mount. It could also possibly hold a small machining head and be used as a CNC router. The possibilities for a well build gantry system are virtually limitless. The important thing to remember is the power of 3D modeling. all these parts were designed over the course of a week by a 17 year old (me) on sketch up. With more time, you can literally design and build anything these days using free software, as long a you are willing to put in the effort. I hope you enjoyed my Instructable. Thanks for taking the time to read!
Just a last reminder that this is being entered in the Dremel 3D Design contest here on Instructables. if you enjoyed the work I put into this, please feel free to vote for me!
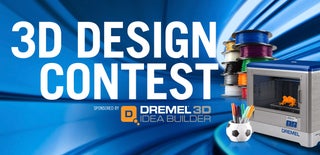
Participated in the
3D Design Contest
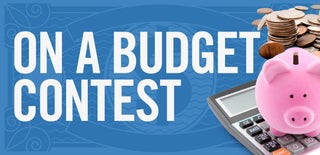
Participated in the
On a Budget Contest