Introduction: Faux Bois Handrail
I thought I might try my hand at Faux Bois, (French for fake wood).
My front porch stair handrail has been rotting and was pretty much useless as any sort of safety device.
This is my attempt at a small home improvement in an artistic style that goes along with my desire to do more outdoor sculpting.
I will be updating this instructable over the next week or so as I am doing my back porch step also. check back often and dont forget to vote. Thanks a Lot.
Step 1: The Reason
these photos are representative to why I needed to do a repair/improvement.
the stairs and deck were built back in about 94 or 95 and the handrails were failing because of constant exposure to the climate here in Oregon.
I did try a repair a couple years ago with some epoxy putty and screws, but the damage was already too great
added 9/7/15 the photos of the back step. more rot and deterioration
Step 2: Building an Armature
first I needed a solid armature, so I used welded steel and attached it to the deck at the upper end and buried the bottom end into the soil (I did not set it in concrete at this time as I will come back at some point soon (I hope) and replace the stair stringers and treads. the middle post is sitting on a pier block.
there are rules and regulations to post spacing so check your local codes, especially if you are planning on selling soon.
I will be adding to this as we move into fall, so the project is not complete at this point
the main portion of the rail is built from 2X3 steel welded together and some 1X1 tubing for smaller branches, followed up with some 3/16 rod just wired in with tie wire.
added 9/7/15. the armature for the step. made with 40 feet of 3/8 rebar and expanded metal lath. the rebar cost me $4.00 a 20 ft stick, so I have about $12.00 into the armature with the metal lath
Step 3: Apply Metal Lath
the next step was to cut and wire on some expanded metal lath purchased at my local hardware store for about $6.00 for a 2X8 sheet.
this was cut into strips with my cutoff grinder but snips work just as well.
I then wrapped it around the steel and held it with tie wire.
added 9/7/15 a close up of the tie wire. the photos show the wire bent into a J shape, pushed through the lath and pulled back up to go around the armature and back through the lath then a couple twists and cut with some end nippers
Step 4: Lath Applied
this is our handrail ready for concrete
added 9/7/15 and back step
Step 5: Concrete
there are a few websites out there posting different recipes for sculpted concrete.
I use 1 part Portland Cement to 5 parts sand with some fiberglass shorts. you can cut up some fiberglass matte and shred it in. I purchased a bag for reinforcing concrete from a local concrete company, it was about $8.00.
you can also add an acrylic additive made for concrete to help make it a little stickier. I used Dap concrete bonding additive. another brand I have heard good things about is Tru Pac X, it is a dry mix that helps with vertical adhesion.
http://www.walttools.com/tru-pac-x-mortar-convert-...
I adjust my mix according to feel, and how well it stays up on the undersides of the armature. sticky but moist.
I did not get pictures of this step as it is messy and I got busy with the project and forgot.
squish it into the lath to eliminate air pockets and then apply enough to carve into when the cement sets up enough to carve.
added 9/7/15 I used a couple different mixes as I went about doing the back step. for a finer texture and quicker set up use a 1 to 1 mix of portland cement and sand with a little fiberglass, this mix was much smoother in its finish and set up much quicker allowing carving to be done in minutes. but act quickly. at one point I used only cement and fiberglass to do some small patching, we'll see how it holds up
also, I was using a 3/8 drill and paint mixer, slow and not good at mixing. I went and bought a used 1/2 drill motor and mud mixing paddle, much easier and did a better job of mixing. you can still mix it by hand with a hoe or shovel in a wheel barrow or even on the ground as is done in many places in the world to this day.
Step 6: Carving
after the concrete has had some time to set up, up to 2 hours depending on mix and temperatures, it's time to carve it. it should be firm like a good clay.
carving can be done with tools as simple as a stick and a nail, or plastic spoons and forks, along with wire brushes. old paintbrushes are useful too to brush away crumbs and even smoothing the surface a bit. and even a spritz of water to get a smoother texture.
added 9/7/15 as mentioned before finer mixes with less sand result in finer textures. the added photos show the wood from my back step, I like the texture and used it for inspiration
Step 7: Closeups of the Back Step
I put the step in place before I was done to double check it hadn't grown too much. one thing to remember when building your armature is to build it undersize (I didn't do that). Tonka is overseeing the fitment
the other photos show the difference in textures with the different mixes. I also added a nail head with the concrete and fiberglass mix
Step 8: Practice, Practice, Practice
this is a practice piece I did last year,
it is lath attached to a piece of plywood, and sculpted concrete applied. it was then painted with acrylic house paints.
Step 9: Signs and Outdoor Sculpture
this is a piece I did for a local resale store called PackRatz. the base is sculpted concrete to look like a tree stump, the rest of the sculpture is epoxy clay over a wire armature.
its about 5 feet tall
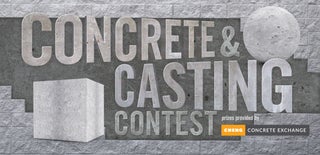
Participated in the
Concrete and Casting Contest