Introduction: Faux Butcher's Block Kid's Table
With a few extra 2x4's you can quickly make an easy (or complicated if you choose) faux butcher's block top that's a perfect for a kid's rustic looking table.
Check out the attached video or follow along step by step! Head over to www.LazyGuyDIY.com for more tips, tricks and tutorials!
Tools Used For This Build
- Thickness Planer - RIDGID 13" Thickness Planer
- Table Saw - RIDGID 10" Compact Table Saw
- Miter Saw - RIDGID Sliding Compound Miter Saw
- Drill - Ryobi One+ 18v Brushless Hammer
- Drill Driver - Ryobi One+ 18v Pulse Driver
- Random Orbit Sander - Ryobi One+ 18v Random Orbit Sander
- Brad/Nail Gun - Ryobi One+ 18 Gauge AirStrike Brad Gun
- 36" Pipe/Bar Clamps - Bessey 36" Bar Clamps
Materials/Supplies Used
- (1) 2x2x8 (S4S grade - 4 squared sides)
- (4) 2x4x8
- (2) 1x4x6 (S4S grade - 4 squared sides)
- Wood Glue - TiteBond II
- 2" Wood Screws (for legs)
- 1-1/4-2" brad nails
- Wood Stain and Accent Paint
- Poly Finish Coat - Varathane Triple Thick Semi-Gloss
Step 1: Step 1
Cut your 2x4's to 31"-32" lengths. I left a little extra on just in case the planer took a little snipe out of the ends on a later step. This is completely optional, but I ran the board faces through the thickness planer to get an absolutely flush joint during the glue up.
If you want to get really (pinky out) fancy you can cut the 2x4's to create visible seams when you stain and seal later. Just know that the smaller pieces make for a little extra work during the glue up. What's this? Lazy Guy creating extra work? Yeah, but not a ton.
Apply wood glue between each layer and smooth it out. Drawing pictures and writing messages in glue is a rookie mistake. Don't be a rookie Nuke. I use the Rockler Glue Brush on all of my glue ups (plus you get the satisfying glue peel when it dries). Apply glue to both sides thinly for the best adhesion and then clamp everything up! Because the thickness planer can only handle material 13" wide I made two separate rows of six, but clamped everything together (without glue between the two stacks) to save on using too many clamps.
Step 2: Step 2
If you're one of those people who can't wait to open up their presents, at least give the glue a few hours to dry and set before you move on to the next step. If you want the best results, pick this step back up the next day.
Set your thickness planer up and run your glue ups through taking off about a 1/16th - 1/8th" with each pass. Make sure you pass both stacks through each adjusted depth with the thickness planer. The idea is to have them end up the exact same thickness. You're going to plane them until the top is all one smooth surface.
Step 3: Step 3
Remember that extra length we were keeping on the 2x4 stacks (if you listened to my advice you rebel)? It's time to trim the fat. I used my sliding miter saw to cut the excess off but you can also use a table saw or a circular saw to even up the pieces. Once they are to the same length (30" long)... it's glue up time... again! Once again... don't get impatient. You really need to let the glue up sit for a minimum of a few hours to let the glue set. Clean your shop or something in the mean time. It's quite dusty.
Step 4: Step 4
When your top is fully dried, it's time to ruin it. Okay, maybe not ruin it, but it's time to cut some holes in it. Specifically cut holes for legs. Now, a person who thinks they are smarter than the rest of us are going to look at this step and say I'm just going to cut the original 2x4's to make room for the legs here... Well guess what smarty pants? Since you planed the 2x4's they are no longer 1.50" thick like the 2x2's you're going to use for the legs. So you're going to have to use some craftsmanship and cut the holes with your table saw.
I first used a scrap piece of 2x2 to mark my cuts. I used a speed square to extend the marks so I could line everything up clearly with my table saw cuts. Then I ran everything through the table saw, making sure the blade cuts through the top of the table first to avoid tear out. To make life just a little easier, I attached a scrap piece of wood to my table saw miter gauge and passed it through the saw to see where the cut would hit. Then with a pair of speed clamps, I attached the table top to the scrap piece and rip cut the ends. For fun, I sprayed a little WD40 on the saw deck to make it extra slip and slide'y.
Step 5: Step 5
Notice the aged look I got on the top of my table with the different colored leg tops? Here's how we get there. Stain your table top with a medium/light stain. I think I went with MinWax Special Walnut. Remember not to use the stain and poly mixes. Those are for people lazier than me.
After the stain has dried (yes you have to wait again. Go hug a kid or something while you wait. But your kid, not some strange kid...) apply a top coat or two of poly to seal the stain. I used Varathane triple thick semi gloss poly. Yeah that's right, three coats at once. It's like they know me.
Step 6: Step 6
That nice and square 2x2 you've been storing in the corner is ready for it's time to shine! Cut 4 pieces to 18". Now flip the table top over and place the pretty side face down on a flat surface. Attach the legs with wood glue and if you're feeling really ambitious pre-drill holes and attach wood screws to make this sucker bomb proof. Once again it's time to pull out a bunch of clamps and let the legs dry solidly. Even with screws. The top is heavy, the last thing you want is for the legs to pop off when your toddler is coloring on it and then errr... have your toddler's legs pop off too...
Step 7: Step 7
Now for the forgotten 1x4's! If all your cuts went according to plan, the dimensions of the table should be 30" x 18". If that's the case, cut the face aprons to 30" and the side aprons to 19.50" and attach directly to the 2x4 top with wood glue and brad nails. Patch any holes or gaps with wood filler, then sand smooth once it's dry.
Step 8: Step 8
With the legs and aprons securely attached it's time to age this thing and give it some character. The method is simple, paint the aprons and the legs your base color. Let it dry. Then sand all the edges and areas within the flat surfaces with a random orbit sander. Use 220 grit sandpaper for only a little removed, use a lower grit count for a significant amount removed. You are going to pull a dark stain over top so anything you expose down to bare wood is going to pick up the stain.
For the top I hit the edges and seams with 220 grit as well pulling back some of the poly coat I already applied. With everything sanded I used a foam brush and a dark stain and coated the entire piece and wiped off the excess. The painted areas darken and the stained top gets a weathered and aged look. If you want, you could also distress the top before staining to make it look like it's been well used. The dark stain will highlight those marks. Once the poly is dry, re-coat the entire piece with at least 2-3 coats of poly. Remember to lightly hand sand with 300+ grit sandpaper to get the smoothest finish.
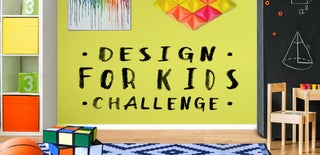
Participated in the
Design For Kids Challenge