Introduction: Fiber Optic Snoot!
In underwater photography light is very important, often the small
flashes found on point and shoot cameras are not sufficient. At depth colors can look washed out and blue, to combat this problem off-camera strobes are commonly used. These powerful sources of light can be very expensive and take some time to get used to. While they have a wide angle of coverage (100-110 degrees or more), the light emits from one side and can often cause harsh shadows. When I was getting more into underwater photography, I had one strobe but I wanted to try some different lighting techniques for macro photography, but felt limited.
I came up with the idea to use fiber optic cable as a flexible way to focus and redirect the light from one strobe and have the light split into two light sources. All I needed was to figure out how to position the fiber optic cables against my strobe and create a unit to mount it to the strobe.
I was able to buy some fairly inexpensive supplies online and at the hardware store to create a way to redirect and focus the light coming from my single strobe. The result was the ability to split the light from one strobe into two different directions allowing for even light coverage similar to having two strobes. The unit also allowed for some creative lighting options such as light focused snoot photography. The fiber optic snoot was born!
The project assumes that you will already have an underwater camera with
a housing and a strobe. My strobe type is an INON D2000. The sizing and positioning of several components could change depending on the make/model of the strobe used.
I originally did a small write up on an underwater photography forum (May 2010) but thought I would do a proper step by step here.
Step 1: Supplies and Tools
I have broken the instructable down into multiple steps and thought it would be best to start with a supplies and tools section. Please see and refer to the 2 photographs and expanded diagram to get an idea of how everything fits together. We should think of the assembly as 2 main parts:
1. The main unit body consisting of the PVC storm water reducer, end caps, pipes etc. Basically everything needed to hold the unit together and hold the fibers in position over the strobe flash points.
2. The fiber optic assembly consisting of the fibers themselves and the loc-line arms which attach to the main unit body by screwing into the female/female couplings.
Main unit body supplies and tools
- PVC STORM WATER REDUCER (100mm to 90 mm) which fit my strobe
- 2x PVC STORM WATER END CAPS which fit the reducer, I used two of the end caps mainly to allow for greater stability when coupled with the internal layer of thick plastic.
- 2x IRRIGATION PIPES/tubes (15 x 150 mm or approximately 6 inches originally; I did trim these down slightly so they did not touch the strobe) + 2x FEMALE/FEMALE COUPLINGS for the irrigation pipes (*these also fit perfectly to the loc-line arms and had the exact thread size; please note that loc-line has 2 thread types including a US standard which seems to be the more available type here in Australia for hardware/irrigation needs and a British/UK style thread).
- Small piece of foam, 5 mm thick. I used a FOAM LAYER in between the 2 end caps to help reduce light from the strobe coming out the holes for the pipes
- 4x Plastic HOSE CLAMPS as extra support for the pipes, these were mainly used on either side of the storm water end caps to provide some stability, so that the pipes did not easily pull out. In the end there were not needed as the unit was fairly solid with a little adhesive glue. Again, I did not end up using epoxy as I wanted the unit to be serviceable in case there were any issues later. I put some time and effort into the planning stages and possibly over engineered the assembly and unit to be fairly robust and ensure that it worked.
- 10 mm HEAT SHRINK TUBING (mainly just to enclose the fiber optics, keep them together, and help slide them into the loc-line arms).
- SURGICAL TUBING for one end of the fiber optic cables in the arms.
- BUNGEE CORD for securing the assembly/unit to the strobe. While the fit of the storm water reduced is snug and stays in place, I thought an extra precaution was needed as I did not want it floating away or for any alignment to shift while in use.
- Aluminum bar and stainless steel bolt + nut – this is used to lock the 2x FEMALE/FEMALE COUPLINGS so they do not rotate during the manipulation or positioning of the loc-line arm.
- Quick dry (5 minute) 2 part epoxy.
- Plastic sheet, approximately 3 mm thick – I scavenged this from a plastic container (Plexiglas or another thick plastic would work as well). This was used to add stability of the irrigation pipes., think of a 3 layer sandwich with a pipe down the middle this is called a PLASTIC DIVIDER in the photo showing the disassembled unit and parts.
Fiber optic assembly supplies and tools
- Fiber optic cable: For this project I purchased 70 feet of "unjacketed", 1.5mm diameter end glow fiber optic cable. This is the online shop where I purchased the fiber optics from, they sell by the foot and were very helpful in discussions about what I wanted to do: http://www.thefiberopticstore.com
- Large nail clippers – to cut the fiber optic cable.
- Jeweler loop or a small magnifying glass – to view the ends of the fiber optic cable
- Sand paper in fine to very fine grit – to polish the ends of the fiber optic cable. I purchased medium grade sand paper (400) for the first polishing step, finer sand paper for step 2 (1200), and a very fine abrasive paper approximately 3 micron (try fiber optic suppliers) for the final polishing step.
- Loc-line arm kit - Loc-line produces a great assortment of designs for mainly industrial, construction, automotive, or aquarium water flow applications. They are pieces of plastic that fit together into a rigid yet flexible arm/tube and can come complete with threaded ends and nozzle fittings. I purchased 2 of the 1/2 inch style kits. (http://www.modularhose.com/Loc-Line-12-System/12-kits/50813). The loc-line arms stay in position where directed, are light in weight, and relatively inexpensive. I was able to find their catalog online and very detailed product dimensions and blueprints online. This feature was very helpful when calculating the maximum number of fiber optic cables and optimizing the possible surface area exposed to the flash unit and light source.
Additional tools and supplies
- Drill and drill bit
- 15mm corer bit
- File
- Saw blade (hack saw)
- 4x cable ties
Optional
- Photocopy of strobe face for position and alignment
- Paint marker
Step 2: Main Unit Body Fittings
For the main unit body, I purchased almost everything in the previous supplies and tools section from a hardware store. I took my strobe into the hardware store in order to ensure the fit of the appropriate pieces. Other than some strange looks, there were a number of options to choose from. The fit does not have to be perfect if your strobe is a different size/shape as you can always add some foam later for a perfect fit.
Step 3: Drilling and Alignment of Main Unit Body
I used a photocopy of the strobe to estimate where the irrigation pipes should be placed, trying to be as directly over each flash point as possible. I cut out the photocopied strobe paper and drilled small alignment/guide holes through the 2 end caps in order to make sure they were in alignment. Please refer to the expanded diagram in the "supplies and tools" section to see how everything fits together.
The reducer had a slightly larger diameter, so for the plastic layer inside the main unit body, I drilled the small holes using the PVC end caps as guides. Once the alignment holes were done I was able to use the 15mm corer to make the larger holes. With plastic, care needs to be taken during drilling so that a little snag will not possibly crack the plastic. To smooth out the edges and clean up the holes, I used a file afterwards.
After drilling the holes for the irrigation pipes through the end caps, I put the 2x end caps and pvc reducer together in order to estimate how much to cut off the end of each pipe (with the female:female coupling attached at the end of the pipe). Please refer to photos 1, 2 and 3 above. I cut the ends using a hack saw blade and smoothed the edges using a file.
I then started to build the main unit body layer by layer, starting with:
- The irrigation pipes and female couplings inserted into the first (outside) end cap.
- Hose clamps were attached to the irrigation pipes effectively holding the pipes in place to the end cap (photo 4).
- I then included a foam layer, this was used to block any stray light from the strobe not directed into the irrigation pipes and fiber optics (photo 5).
- The second end cap was added and stacked on top of the first. These fit together easily with some small pressure applied (photo 6).
- A second set of hose clamps were attached to the irrigation pipes (photo 7).
- Next the 2x end caps and pipes were fitted into the PVC storm water reducer (photo 8). This photograph also shows the edge of the reducer where the plastic divider will rest. Please note that I measured and cut the irrigation pipes to ensure that they did not touch the strobe.
- The plastic sheet (plastic divider) was then added to the PVC storm water reducer (photo 9). This is one layer which I glued in place using the 2 part epoxy. Again the irrigation pipes were measured and cut so that they did not touch the strobe when the main unit body was fitted. The irrigation pipes were approximately 5-6mm protruding past the plastic sheet (photo 10). The addition of the plastic sheet helped to stabilize the pipes from moving side to side in addition to the other two end cap layers.
- Finally I measured and cut 2 flat pieces of ALUMINUM BAR. This was drilled and held together with a stainless steel bolt + nut. I placed these on either side of the black female/female coupling ends which stick out of the PVC end caps (photo 11). During my initial use, I found that through positioning the arms some turning/rotation of the pipes occurred. To prevent this from happening I used the aluminum bar to effectively lock each pipe to the other.
I put everything together and pulled it apart several times to make sure it all fit and was aligned the way that was needed prior to putting the hose clamps in place and gluing it together. I only used the epoxy in a couple of key points as I wanted this unit to be serviceable should the need ever arise to make changes rather than gluing it all up and having to chisel or break it apart just to alter something or make one minor adjustment.
Step 4: Fiber Optic Cable Cutting and Polishing
Cutting:
To cut the fiber optic cable I used the large nail clipper to cut the fiber optic cable into lengths. I briefly trialed cutting it with a box cutter or a wire cutter, but neither was able to make a straight cut. Care should be taken while cutting the fiber optic ends to try to get the as straight as possible, this helps not only for the subsequent polishing but also ensures the light source hitting a flat and optimum surface area, I would also suggest safety glasses for most of these steps as flying fiber optic plastic could be a hazard.
I originally cut the fiber optic cable into 40 pieces at approximately 20 inches a piece, this allowed for 20 strands to be used for each arm. With the combination of Loc-line arm kit and the main unit assembly to hold the pipes in place over the flash points on the strobe, I felt that 20 inches allowed some margin/flexibility if needed from the polishing process (approximately 13 inches total + 5-6 inches for the irrigation pipe + 1 inch spare). While I measured the overall length needed with a wire in the first instance (down through the Loc-line arm to the strobe), I was still a little unsure so I decided to be cautious and made them just a bit longer than needed. I ended up trimming a little off later and re-polishing those ends, but better safe than sorry.
Polishing:
I ended up using 3 different grain size (*or grades) of abrasive paper. After the fiber optic cables were cut they need to be polished as some chipping, gouging, or burring may have occurred. In order to transmit the light the most efficient way, care needs to be taken to even the surface area of the end of the cable. For each cable, I polished both ends, and inspected them after each step with the different abrasive papers. Each time I polished the fiber optic cable end I did so in a figure 8 pattern and was careful to hold the end steady and perpendicular to the abrasive paper. I read that the evenness of the surface is important in capturing and then transmitting the light down the cable. I would estimate that I did the figure 8 pattern 15-20 times back and forth. Over a few cables you could actually feel when the unevenness was gone and using a jeweler loop or a small magnifying glass it is possible to view the cable end for the desired effect. Do the best you can, any way I could help increase the efficiency of the light transmittance in my mind was worthwhile doing well.
Step 5: Fiber Optic Assembly
For each loc-line arm there are 20 strands of 1.5mm fiber optic cables. Once the cables are cut and polished, we are ready to assemble the fiber optics and each loc-line arm.
- Place one end of the polished cable inside a length of surgical tubing (photo 1). I wanted at least one end to be fairly stable and decided that the end being positioned over the flash point would be the easiest and the best end. One point which I had not expected was that as the loc-line arms are positioned, the fiber optic cables tend to slip and slide occurring which would make some of the strands appear slightly longer (because of the curvature).
- Insert the fiber optic cables into a length of heat shrink tubing and add 2x cable ties to keep in place (photo 2 and 3). The heat shrink is mainly used to keep the fiber optic cables semi-contained and to provide some casing to slip them up into the loc-line arms.
- Insert the heat shrink enclosed fiber optic cables into each loc-line arm until the cables reach the nozzle end (photo 4).
- Ensure that the cables in the surgical tubing are flush and even with the end (photo 5). We want the light to hit the cable ends evenly.
Step 6: Unit Assembly
We are now ready to assembly the unit together.
- Insert the surgical tubing end of the fiber optic assembly into the irrigation pipes on the main unit body (photo 1).
- Screw down and tighten the loc-line arm on top into the female/female coupling (photo 2).
- Admire this crazy looking contraption you just put together (photo 3)!
Step 7: Testing, Options for Use, and Pre-dive Conditioning
In this section I detail several key usability points that are very important to proper use of the fiber snoot.
Once the assembly is finished, care needs to be taken to line up the irrigation pipes with the fiber optics perfectly with the flash units on the strobe. If the alignment is not exact, there may be an uneven distribution of light transmitting from the two snoot arms. For my unit, I used a paint marker to add alignment marks would use
pre-existing points on the particular strobe type used. Please see the arrow pointing to a fixed point on the strobe and a silver line on the fiber snoot unit in photo 1. I would suggest practicing with the fiber snoot before taking it underwater. Get comfortable with using it, aiming, and adjusting the arms. For an example, I have included a photo where the angle of the nozzle was not aligned properly (photo 2).
Ideally with time and practice you will be able to use your fiber snoot for wide angle, macro, and creative lighting techniques. Photos 3 and 4 show how I would take an image for wide angle with both arms in use. Photo 5 is the resulting image. This illustrates how the unit can simulate the even lighting conditions that would generally require 2 strobes.
I have also included an example of single arm (snoot) use (photo 6) and the resulting image (photo 7). My purpose was to give this subject a small kiss of light from above. A variation of single snoot use could be utilized by back lighting a small subject such as a blenny or nudibranch. With the use of macro lenses a smaller field of view, the arms could easily be redirected to illuminate a subject from a variety of angles/positions.
Prior the first dive, I soaked the entire setup in a bucket of water. I wanted to remove any glue residue with an initial soaking so that most of the dissolvable compounds would be gone prior to taking it underwater and in direct contact with my strobe. I thought that this extra step could possibly protect my strobe and the fibers, rather than thinking later it could have been preventable. I also added a length of bungee cord around the unit to stretch around the back of the strobe. While the fit onto the strobe was firm, I thought an extra precaution would be good to prevent it from floating away should the unit become dislodged.
Step 8: Future Considerations
While the unit may appear a bit cumbersome, it is fine for underwater use and I have enjoyed using it for creative lighting techniques.
I offer to you, that if I were to make a change for version 2.0, I would try to scale back the main unit body to something a little more streamline. Perhaps a CNC machined disc or 3D printed disk that bolted onto the diffuser mount. This would be providing that he overall weight of the whole assembly was low enough to accommodate the fittings. Perhaps you will have a chance to explore other options and share them here too.
Finally, thank you for allowing me to share my fiber snoot with you!
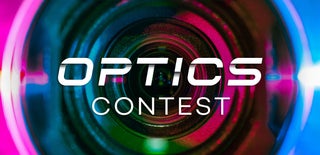
Runner Up in the
Optics Contest