Introduction: Flexible Biological Silicone Rapid Prototyping System
This is a 3D silicone printer inspired by the video of YOUTUBE. We used a series of video machine design principles and added some optimized designs.
We hope this machine can be used to treat medical external ear brackets. Due to the nature of the silica gel, it can control its processing technology to make its elasticity and quality a true human bone.
Supplies
1. NuSil MED-4735 Silicone
2. Longpi 10 Silicone
3. FDM 3d printer
4. Some print models
Step 1: Introduction
Desktop flexible bio-silicone printers use new silicone materials and are categorized with traditional PLA materials to provide alignment and scalability. Can be used to print such cardiac, cardiovascular and other medical research models. Combined with the FDM fusion stacking technology, the basic original model is scanned by a 3D scanner, and then introduced into Geomagic Studio software for post-repair, which is introduced into the 3D model slice and printed layer by layer, and then rapidly formed by using a hot melt fan. Processed to make the pre-model obtained by scanning more complete, close to the real object, then import and insert PRO-E, Creo and other 3D modeling software to add layers. thick,
Step 2:
All of the models and renderings used in this article were created by FUSHION 360 and worked with TEAM in collaboration with multiple people. Before this feature appeared, our collaborative modeling process was like this: coordinating the modeling part that everyone is responsible for, starting modeling, summarizing the model files created by each person, finding mismatches between parts, modifying Model and then continue to summarize. ..... Since there is no team function, only U disk or network transmission can be used when summarizing parts. Almost slow, and model updates are usually not timely. I often refer to the model of the small partner to modify my model. After the modification is completed, the model of the partner has just been modified, and her own model can no longer match her. The emergence of team functions has solved this problem well, and everyone's models can be updated and shared in real time through the team.
I put the printed model at the end of the article.
Step 3: Show the Overall Rendering of Several Machine Populations.
FDM 3D printer body, X-axis stepper motor, Y-axis stepper motor, Z-axis stepper motor, hot bed platform, extrusion head module, extruder module.
The extrusion system module includes: heating aluminum block, extrusion head structure, air valve, feed pipe, fan.
The paper feed system module includes: a stepper motor, a lead screw, a barrel and an outer frame.
Step 4:
Due to the huge difference between silica and common FDM 3D printer consumables, we have designed extrusion system modules and feed system modules with special construction. Through simulation analysis, we found that most of these parts do not need to be subjected to large forces or high temperatures during operation. Therefore, we made these parts using a 3D printer so that they can be easily replaced and improved.
Step 5:
First, the manufacturing process of the extrusion system module is introduced. The extrusion system modules include: heated aluminum block, extrusion head structure, air valve, feed tube and fan.
Step 6:
In order to cure the silica gel quickly, a controlled heat source should be used to treat the silica gel that has just been extruded. By controlling the 2560 firmware modules of RAMRAP1.5 and ARDUINO MAGE, the output functions of the extrusion head and the hot bed control section are rewritten, the temperature of the double heating rod is controlled, and the calories are controlled by the thermal resistance, and the heating rod is connected to the aluminum with a large amount of cooling. The holes are used to heat the aluminum, and the aluminum is taken away by a fan, and hot air is blown onto the silica gel to rapidly solidify rapidly.
Step 7:
The main body of the extruder consists of three parts. We have a modular construction and its specific dimensions can even be based on your own FDM 3D printer size, motor, coupling, fan, heating block. The choice of extrusion diameter and parameters are up to you.
Step 8:
This is a real picture printer for 3D printed models. We chose a server fan with large wind power and a small motor controlled by a separate switch to drive the stir bar with the coupling. The heating rod on the heating block is connected to the ramps 1.5, one to connect the hot bed pins and the other to the heating rod pins of the extrusion head. For firmware control, you will need to learn the configuration file of the 3D printer MEGA2560 separately.
Step 9:
Then there is the manufacturing process of his feeding system module. The paper feed system module consists of a stepper motor, a lead screw, a drum and its outer frame. We use common contours to make the frame to improve size and structure.
The two components of AB are mixed for the first time in an extrusion system to achieve a 1:1 standard and the same amount of extrusion. Extrusion from the PU hose, mixing the needles by static and then stirring again. Then, it enters the agitation chamber through the PU tube, and the agitator rod is mixed and extruded by the high speed rotation of the motor.
Here, we recommend a 42-step geared motor that can be controlled by the Arduion MEGA 2560 control board. The torque of this type of motor meets the extrusion requirements. If a motor with insufficient torque is used, the silicone will be difficult to push and the effect of extrusion feeding will not be achieved.
Step 10:
Due to the modular design concept of the entire printing system, the printing module can adapt to a variety of medium and large 3D printers, relatively easy to modify, so this part of the modeling is not required, the workload is very large. Simply design the module in the first few steps and you're almost done. Simply fit the two modules to your 3d printer.
Step 11:
Finally, the most important thing is to configure the modification of the MARLIN firmware. In the configuration file, you need to modify the parameters for your own printer. The temperature control module is set to 70°c and you need to calculate the operating parameters of the 42-step motor yourself.
I will share my configuration information for your reference.
If you think this article is not fluent, then Google Translate must have a problem. XD
Attachments
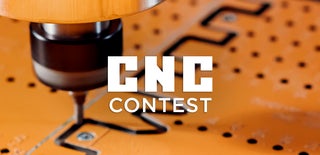
Participated in the
CNC Contest