Introduction: Fliptable LowRider CNC
As an active builder/maker for home or even co-workers projects, a CNC machine was something I knew I always wanted to make use of, but didnt have the budget for one.
Approximately total cost of my build (for Table & LowRider CNC): $650 (approx)
About mid 2018, my brother (https://www.instructables.com/member/IJustLikeMaki... and I were musing and looking seriously into how to acquire one that would work for our budgets. And thats when we found V1 Engineering (https://shop.v1engineering.com/)
What is a CNC (Computer numerical control). Basically it's an input-output machine, you input coding and it outputs movement. Then by mounting the desired cutting tool you (hopefully) end up with the desired outcome.
Building your own CNC is definitely a marathon, not a sprint. This project took me close to 7 months to get to a comfortable and consistent cutting point. This could be done much quicker, however I'm a father of 2 girls at the time and work a full time job on top of house work, I found myself really only haveing time to work in spurts for a few hours at a time.
The designer/engineer, Ryan, over at V1 Engineering basically had the same problem. CNC machines generally have a pretty high end intro price that so many just cant afford to get into. So he designed, prototyped, and eventually built what is considered a hobby grade DIY CNC machine known as the MPCNC and later the LowRider. Not only is the price more affordable than other machines out there, but I personally liked the customization and expansion abilities as long as your up for the task. This is no plug and play.
The model I chose was the LowRider V2, as I am more looking at utilizing full 4’x8’ sheets and other larger format CNC-ing projects.
So Ryan at V1 basically gives away his engineering for free, but also creates easy shop options for all the parts. I looked into buying pieces separately, and it's just cheaper to go with Ryans bundles (and you know it's got what you need). There's even a compiled list to make it easy, and I'd defiantly refer to his list and instructions on lowrider assembly over mine!
(https://www.v1engineering.com/lowrider-parts/)
Supplies
> LowRider V2 25.4mm 3D printer files: https://www.thingiverse.com/thing:3026040
(3D prints were done by my brother)
> LowRider V2 CNC Bundle from V1 Engineering: https://shop.v1engineering.com/collections/lowride...
> Rambo smart controller screen: https://shop.v1engineering.com/collections/lowride...
--> Print files for smart controller screen: https://www.thingiverse.com/thing:1562144
> (3) 1" Stainless Steel Round TUBE (tube is important. it's not conduit): https://www.ebay.com/itm/1Stainless-Steel-Round-Tu...
> Trim Router (the LowRider is designed to use a Dewalt 611. I modified the router plate for this one off amazon: https://www.amazon.com/gp/product/B07H79C1PB/ref=p...)
> Lots of screws and misc hardware
> (2) 4'x8' sheets of 3/4 MDF (Menards sheets are more like 4'-3" x 8'-3". I just used it as is)
> (2) 2x4 @ 10ft
> (9) 2x4 @ 8ft
> (1) 4x4 @
> (4) 2" steel swivel Casters (since mine rolls around)
> (2) 4" door hinges (for the flippy top)
> (4) light duty hinges (for added table legs)
(keep in mind there might be a few odds and ends I already had, so my list may not be complete. If you plan on making something similar, just be aware you might need more lumber/hardware than I have in the supplies)
Step 1: Design / Prep
I'm an AutoCAD Designer, so drawing up my design in autocad wasnt too difficult.
My primary concern was space. If my cutting space is 4ft x 8ft, the entire table is definitely going to take up more room. Total space is around 5ft 6in x 8ft 6in give or take. I had looked into a wall mount, but being able to roll the table around could be a huge benefit for my garage/shop/children's-carport.
So then I designed my table top to "flip" or rotate to save space when not in use. (see examples).
Looking back, this flip top is mostly not as useful as I had thought. The intent was to be able to save space so cars can get back into the garage when not in use, but honestly as of now it pretty much just stays in the flat position.
Final Table design: While I designed something beefier in autocad, the legs became a as built design. Ended up using 2 4x4's for the vertical legs using a T structure to keep it from tipping and someplace to put the wheels. The table top secures to the leg structure using the door hinges. but we'll talk more about that in assembly.
I dont have the actual size/dimensions listed here, as it basically is just sheet goods as purchased with the frame being split evenly to make a makeshift torsion table. note it's not a true torsion table, but I was also trying to not make it super heavy so I can actually move it around.
Step 2: Glue LowRider Flat Parts
1" (.065 wall) SS Tubes came in a week ago (wanted to have these in hand so I could accuratly measure and make sure they were in deed 25.4mm OD)
So I then have my brother print the 25.4mm lowRider parts.
While I await for those to finish printing and for him to come visit next month, I went to cutting out the flat parts.
Start this by first gluing the printed templates to some 1/4 MDF and 1/2" MDF.
Step 3: Cut the Flatparts.....somehow
Depending on your shop setup, you'll have to cut these flat parts out. Ideally you'd use a CNC machine, but well, thats how we got into this mess.
So choose your instrument of terror and hack away!
Step 4: Actually Cut the Parts
But really. Just use a Jig saw, band saw, or scroll saw.
I ended up using the Scroll saw mostly, as the tiny band saw I had access too wasnt deep enough.
High accuracy is nice, but just get as close as possible. worst case, once you get the CNC running you can cut you some better flat parts.
Step 5: Sand Those Flat Parts
You can sand the flat parts, but in reality its not necessary. just helps make it pretty and less snaggy.
Step 6: Speaking of Unessary
I had some wood vineer lying around and couldnt help myself.....
But hey! they look pretty good right?!
Step 7: Table Top Frame Assembly
No matter what your design, you'll want to build the top first. I'd recommend assembling WITH the MDF top, but I didnt have the space to store another large sheet. So I added it after the entire frame was built.
If you go simple and just add regular legs or be extra (like me) and do this flippy top, assembling the top will just make sure you create a base to fit the top (as it's the top thats the important part).
Cut as per my CAD plans (I actually stuck to my plans for the top).
Ryans design has you running the CNC on top of your table. This has the benefit of your gantry being level with the spoilboard (top layer of the table top). However you also lose some tabletop for workspace.
Honestly it's alot less hassle, and if I was to do it again I'd just follow Ryans Design.
So after building the cutting area of the table, and I built some offset rails by ripping the long a 2x4s to create a flat edge for the gantry to ride along. This offsets where your rollers are, so it rides on the 2x4 "rails" instead of the table top. I gain full access of the 4'x8' cutting area, however now it's wider.
These rails show up better in later photos.
Step 8: Build Table "Legs" and Attach to Top
Once you have the top, it's currently a big waste of space taking up the floor. BUT you have a good frame of reference to build the legs from.
I built the legs upside down onto the bottom of the table top frame. Originally designed 3 main supports, but ended up going with 2 and just adding some supports.
Once assembled, I just flipped the whole table frame onto it's feet/casters.
Again I did have some sort of design, however the legs really ended up being more of a as built design. The real world just reacts differently than modeled on a computer (looking at you Bethesda)
Step 9: "Space Saving"
Quick check to make sure it fits in it's planned location (at the time. ended up moving later in the year).
It fits fantastically!
Sticks out a tad further than expected. but thats just how it goes sometimes. My "rails" are actually longer than needed, so maybe someday I'll trim them if the need arises.
Step 10: Velcro
I tend to over complicate things (in case you couldnt tell).
Because the table "flips", it needs some temporary supports to keep it from flipping when laying flat. So I added 4 legs on the corners that fold up flat against the underside of the table top made from scrap 1x4 I had laying around.
I had designed at least 6 different options. Slider locks, crazy woodworking latches, ect.
Then my wife asked what was taking so long. I explained the problem, and with 1 word 3 seconds after me explaining she solved the problem.
.....Velcro.......
Needless to say, Velcro is now used in our house whenever I'm over complicating the situation or project.
Added a few strips of Velcro to the bottom of the table and side of each leg. holds em up great.
I also added some 4x4 at the base of the support legs to give them some girth and cut a 45d slice off the face side for ease of folding.
Step 11: Installed MDF Table Top & Spoilboard
So this step should have been done while building the torsion top. It would have saved me from more irregularities of the wooden frame causing dips or bows in the table top (in case you didnt know, a flat top is crucial to a good finished CNC project)
but I'm me, and well, Velcro.
2 sheets of MDF later, making sure to add screws on both layers, and we have something that actually looks like a table now (well, except the funky flippy part).
Really came together nicely, mostly flat (again my fault), and adding a few supports to the legs due to the added weight it stands vertically very well and doesnt feel like it wants to fall over or anything (which is good).
Just make sure the height from it's pivot point to the edge of the table are far enough away. the wider the table top the taller the table will be. Luckily I'm 6'-2" so having the table taller than normal is great.
Step 12: Assemble Hardware Like Legos
I grew up in a household of boys, and we played lots of legos. Lots and lots of legos. so this was probably my favorite part.
https://docs.v1engineering.com/lowrider/
Following Ryans assembly guide (which is important), you put together bearings to wheels, screws, motors, ect. At this point in the build you need the 3D printed parts as well as Ryans kit.
You could put this together sooner, however theres a few parts you gotta be gentle with and it's better to have the table built beforehand.
You want to be careful on the assembly for obvious reasons, however the one that many overlook is the Z screw shaft couplers. Its basically a metal spring that connects your Z motors to the Z screw shaft. you just need to be careful not to accidentally stretch it out.
Step 13: Completed Assembly
Make sure you follow Ryans guide. theres lots of little details that can really mess with you if you assembly incorrectly.
https://docs.v1engineering.com/lowrider/
My few screw ups were:
Installing the Z Bridge Assembly backwards. The printed bridge is supposed to face towards the table, if backwards it messes with the alignment of your Z Lead Screw.
Bolts/nuts too tight or loose. There's a sweet spot, but it can take a bit to find it. too tight and you can break it, too loose and it'll wobble.
Belts too loose. Really these need to be tight. but again, too tight and you risk stretching the belt, too loose and it can cause your drives to slip.
Stepper Motor Gears. While playing with getting the cnc running (later), I realized I didnt tighten the gears enough causing slipping. You want anything connected to the steppers tight, and I added some blue threadlock to keep them from backing out from vibration.
Step 14: Time to Wire It Up!
While I loved the hardware assembly, this is the step I DREADED.....
I'm a pretty good hobbies, with a wide range of abilities. but at this point I've spend close to $600 on a machine and REALLY didnt wanna mess it up. And lets be honest, there's now a MESS of wires.....
Again Follow Ryans instructions, as there's alot there and no need to re-invent the wheel.
I had a few errors, mostly with accidentally swapping a few wires here and there. but luckily no damage and MOVEMENT!
Now to make it pretty, well, as much as one can.
Step 15: Dress It Up
After playing with manually moving the CNC around for a few hours, gotta take it all apart and re-do it but actually make it pretty this time.
I'm super glad I did this, while it takes longer to test without it being pretty, I knew it worked before completing the assembly. One of those times I actually took my time and did it right!
You'll also notice the aluminum rail in the first photo. I happened to have an aluminum tile finished edger on hand and used that as my vacuum hose & router power rail. Ryans design calls for an aluminum angle to route these and someday I may upgrade to one, but for now zip tying my vacuum hose and router extension cord is working for me.
Now that it's looking pretty snazzy, lets make sure it can still fold
(this is actually what happened. I put it all together then realized I never checked to make sure it was going to fit)
Step 16: Oh Thank Goodness
IT FITS!
I know I designed it to fit and all, but still. Good to know I did something right.
Step 17: THE Step I Dont Have Photos For
Biggest improvement came when I surfaced the Torsion table top (the spoil board being the 2nd and top sheet of MDF, but the torsion top is the 1st layer).
I choose to surface the torsion top as I'll likely be replacing the Spoil board over time as it gets cut into, and I'd rather not have to re-surface a full sheet every time.
Projects were coming out ok, but pretty inconsistent when it came to text. So I put on a 1" Whiteside surface bit and went to down leveling the ENTIRE 4ft x 8ft sheet. It took around 2 hours or so, but I was also in charge of the sleeping (well supposed to be sleeping) kiddos and had to take a break a couple times.
Keep in mind, this made ALOT of dust. and with it being MDF, make sure you wear proper PPE. MDF is really not good for the lungs.
Turned out great and really has made me a lot less frustrated with failed carves.
Step 18: Done!
A few sample photos and videos!
I've been cutting with this machine since fall 2019 (it's now August 2020) and it has yet to let me down. Aside from a few tweeks needed here and there for leveling and alignment it's running like a champ!
(which is to be expected for a DIY hobby grade CNC)
Because I already do woodworking, this CNC has been helping elevate my work. Hopefully soon I'll be selling products! I try to post more of what I'm doing on Facebook: https://www.facebook.com/SawdustKC or instagram (SawdustKC).
Hopefully this helps inspire you to look into building your own CNC, as daunting as it is.
Are you interested in CNC?
What hurdles do you face in moving toward that goal?
Did I miss anything you want to know about?
Thanks for coming to my TED Talk and let me know what you think in the comments!
Dont forget to VOTE!
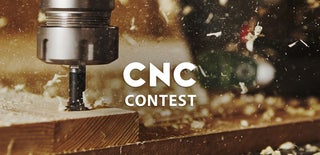
Runner Up in the
CNC Contest 2020