Introduction: Forging a Hot Cut Blacksmiths Tool
Hi there.
In this instructable I will show you how I made a hot cut tool for blacksmithing. The base material is 51CrV4, which is a tough steel intended for making springs and cutting tools. It might not be the best one for this application but it holds up well. You could easily replace it by using an old hammer which has most of the work already done, you just need to forge the blade.
The hot cut is a cutting tool mounted on a wooden handle and is intended for hot work. The smith places the cutting edge where he intends to cut it off and the striker hits the hot cut with a sledge hammer, thus cutting the steel. It is important to keep cooling the tool in water, so it doesn't loose its hardness. It is an all round practical tool and its relatively easy to make.
Supplies
I used:
-hammer 2,8kg
-sledgehammer 4kg
-forge
-anvil 60kg
-punching tool
-drift
-hardwood for a handle
-angle grinder
-belt grinder
What you can use:
-any hammer you can find
-forge (you will need it)
-heavy chunk of steel as an anvil
-punching tool ( it can be held by hand and doesn't need a handle)
-a simple drift
-file (all the machines I used for grinding can be replaced by a good file)
-any piece of wood that is somewhat hard
Step 1: Starting to Forge.
I am using a bar of 51CrV4 which is 25mm thick and 15cm long. The first step is to heat the bar and start upsetting one end. This will serve as the back of the tool and any excess material is welcome. I used about three heats to get enough material. The more material there is in the back the better. It will get worn over time and form a mushroom. More material means it will last for longer, because you need to grind the mushroom away so it doesn't break off.
The next step is drawing the material out. This is done with a hand hammer and a striker. On the first heat I turn the round bar square and start to draw some of the material out for the blade. This can take a bit of time and patience to get it perfectly square and symmetrical but it isn't to difficult.
Step 2: Punching and Drifting the Hole.
Punching the hole for the wooden handle is probably the hardest part in this build but it isn't that difficult with the right set up. In the picture you can see me use a punching tool which is similar to the one I am making here. The main difference is the blade shape. The punching tool has a point on it whereas the hot cut has a blade.
I start by marking the hole on both sides of the bar by lightly striking the punch. Then on the next heat significant force is used to punch the hole quickly. One every three strikes I pull the tool out, cool it in water then insert it from the other side and repeat. This takes about three to four heats.
Once the hole is punched through I insert a drift. A drift is a simple tool intended for changing the shape and size of the eye. I decided to use a rectangular one for this project. The bar is once again heated up in the forge and the drift is inserted. The drift must be inserted from both sides so it produces an hourglass shape of the eye. This helps to hold the wooden handle more securely once it is wedged in.
Step 3: Forging the Blade and Grinding.
Once I am satisfied with the eye shape I move on to forging the blade. This is done on a guillotine tool by isolating one end of the bar. As you can see in the picture, the guillotine tool helps isolate the material with two dies which are round in shape and about 10mm thick. As a lot of other blacksmiths tools this one to needs to be struck with a hammer to move material. I isolated the blade to about 10mm at the base. Then with the help of a striker I draw it out lengthwise. There is no set length I am going for, but a longer blade means it can be sharpened many times before it becomes useless.
After all the forging was done, the tool was left in the charcoal embers and ash to slowly cool down and anneal somewhat. I usually leave it overnight and then continue next morning. All that is left to do before heat treating is to grind it into shape. First I use an angle grinder with a grinding wheel to quickly remove material and all the scale that has formed. Then I move on to a belt grinder. The belt grinder isn't really necessary but it helps to produce sharp lines and a clean finish. I use 40gr zirconium belts for rough grinding before heat treating.
Step 4: Heat Treating and Stamping.
The tool is now rough ground and ready for a heat treat. But before that I need to stamp it with my makers mark. Once the tool is hot I position the stamp with a pair of tongs and the striker hits it with a sledge hammer. It doesn't need to be hit too hard, a solid tap will do.
After that process, the tool is left to cool until it turns from a red color to black. This process is called normalization and is repeated three times in all. This helps to fix/relax the grain structure after all the forging it went through.
After normalization the tool in heated to a red color and is quickly cooled in sunflower oil. I am quenching only the blade and leaving the other part hot. Doing this enables the remaining heat to travel back towards the cutting edge allowing me to temper it with the same heat. Tempering is the process of heating the steel back to around 200-250 C after quenching. This takes away some hardness in exchange for a lot of toughness. In the end I am aiming for a slightly lighter straw color.
With this the work on the steel part of the tool is finished. All it needs now is a wooden handle.
.
Step 5: Making the Handle.
I have some hazel wood that I cut down some time ago so it should be ready to work with. In reality hazel wood is not really the best for this job, its just what I had and decided to work with it. In my experience ash would be the best for this application, its hard and durable.
The piece of wood is cut down to desired length and shaped with a hand plane and grinder. A slot is cut in one end of the handle, for a wedge that comes later. The surface of the wood is nicely polished and the tool fitted on the handle. The fit should be tight so everything stays in place and has no chance of moving. I then make a wedge out of some scrap ash wood and drive it down the previously cut slot. This really anchors everything into place. The hot cut is now ready to use.
Step 6: Finished.
The hot cut really came out great. It an easy project that captures a lot of blacksmithing aspects. From rough forging, punching, drifting, heat treating... . It is a fun project for any beginner or seasoned smith and the tool itself is a must have that comes useful in many situations.
I really hope you learned something form my writings and I encourage anyone to try their hand at blacksmithing or metalworking in general. It is a fun hobby that connect people from all corners of life.
Thank you for reading.
Luka
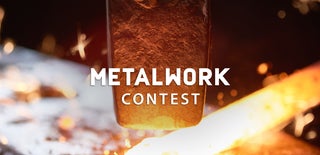
Participated in the
Metalworking Contest