Introduction: From Firewood to Mallet Using Only Hand Tools
I am not a hand tool guy per se but I do like a good challenge. I wanted to see if I could make a plastic mallet using only hand tools.
Supplies
Lumber
Axe
5lb. Hammer
Hammer
Bench Vice
Hand Saw
Trim Saw
Hand Plane
Rasp
Chisels
Sandpaper
Epoxy
Casting Resin
2-1/2 inch PVC
3/8 Dowel
3/8 brass Tube
Lighter
Marker
Hot Glue
Packing Tape
Razor or Utility Knife
5 Minute Epoxy
Mold Release
Acetone
Step 1:
First step is to split the firewood using an axe and 5lb. mini sledge hammer. This is basically like splitting firewood along the grain except you keep splitting the wood until you get a manageable piece you can work with. Its like whittling only less accurate and more crude results.
Step 2:
Next I have to trim the wood to length so I chuck the wood in my bench vise. I don't have an exact measurement for any of this, I'm just going by what looks and feels right. After cutting it to length I needed to rip the piece to remove the excess thickness, the blue mark shows approximately where I want to make my cut.
Step 3:
Now the piece is a little more manageable and taking shape. I use my chisel to remove some large piece of gnarly wood then I take my rasp and start to sort of give the piece shape. At this point I realize that I will have to follow the grain and contour of the wood in order to be able to use this piece. I have two flat-ish sides and two sides with some pretty wild curves. So I used my hand plane to flatten the two sides that are somewhat flat and then use the rasp and sandpaper to refine the curved sides.
Step 4:
After working on the handle I felt like the handle was still too thick so I chucked the piece in my bench vise and ripped it again. You can see in the second pic that the handle is about 1 by 1 inch on the top. I reworked the flat sides with the hand plane again and sanded all of the handle up to 220 grit starting with 80 grit.
Step 5:
In order to attach the handle to the hammer head I needed to make a 1/2 inch peg on the top of the handle. I used a 1/2 piece of brass tube to draw a circle on the top of the handle as a reference. Then I used a trim saw and a rasp to shape the peg. The handle is done for the moment so I set it aside to work on the hammer head.
Step 6:
I take a piece of 2 inch PVC pipe and measure and cutoff a 3-1/4 inch section. This will be my hammer head mold. Since my cut was not very straight I had to use a file to clean up my cut line.
Step 7:
Next I mark the center of the PVC pipe and using a Zippo lighter I heat up a 3/8 inch brass tube and use that to make a hole at my mark. Make sure to wear proper PPE and work in a well ventilated room as PVC fumes are toxic and you don't want to breath them in.
Step 8:
In order to prepare the mold I use packing tape to seal off one end of the PVC pipe. I liberally spray the pipe and the dowel with mold release. Then I used the lighter to heat up a glue stick so that I could seal off the dowel hole. I wanted to make sure that I wouldn't have any leaks.
Step 9:
This is the fun part. I mix equal parts of the casting resin in a container, this stuff has a very short working time under 2 minutes so you have to work fast. Before you start mixing make sure you have everything ready to go for the pour, you don't have time for mistakes. I mix the resin for 30 seconds and then pour slowly straight in to my mold. It hardens in 10-15 minutes, the stuff is amazing it cures really fast and hard.
Step 10:
Once the resin cures its time to demold, be careful because it will be hot. Since I used mold release the dowel and the hammer head blank pop right out with no really issues. I use my razor knife to trim any flashing.
Step 11:
The reason I used a 3/8 inch dowel for the mold was because I planned to use a 1/2 inch tap to thread the hole in the hammer head. Then I use a die to cut some 1/2 threads on the peg of the handle. These didn't come out so great but they were good enough to still be able to thread the hammer head on the handle.
Step 12:
There were some surface imperfections on the hammer head ends so I used a flat piece of MDF and sandpaper to clean them up. I sanded the ends up to 600 grit. Then I used the sandpaper again to chamfer the edges here again I sanded up to 600 grit.
Step 13:
Once I had finished sanding the hammer head I mixed up some 5 minute epoxy and I poured some of it in to the hammer head peg hole and added a liberal amount to the peg on the handle. Next I threaded the two pieces together and cleaned up any squeeze out. Then I used a screw clamp to hold the hammer upright while the epoxy cured over night.
Step 14:
I will be the first to admit the handle is a little unorthodox but it feels really good in the hand. The bottom curve has a nice palm swell that fits inside my hand just right making it super comfortable to hold. If I need to choke up on the handle I just turn the handle over and the top curve provides another really nice palm swell that also fits just right. I honestly didn't expect it to feel as good as it does and since the curves follow the wood grain I don't think there will be an structural integrity issues. I am really happy with the end result. I hope whoever reads this might discover a tip or two they can use. Happy Making!
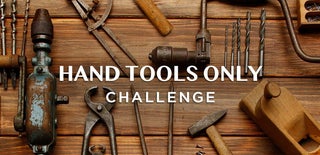
Second Prize in the
Hand Tools Only Challenge