Introduction: Fuse Bead Pokémon - Machamp
Want to make a giant Pokémon? Who wouldn't! It was Christmas time once more and so, one of the many gifts I needed to organise was something for one of my friends 10 year old son.
He's mad on Pokémon, as we all are aren't we? I'd seen a few clips online of people making small Pokémon sprites from various mediums, including fuse beads.
Intrigued by the idea I did a bit of research and realised there's more than one method and many many different types and colours of fuse beads.
It did look like you could get some good, detailed results though, depending on how big you made your designs and what type of beads you used. I'd never made anything like this before, but was confident I could produce something he'd like.
After finding out what Flynn (my friends son) favourite Pokémon was, which he initially said was Garchomp, I deemed that too difficult for my first fuse bead outing, so asked for his favourite original 151 Pokémon assuming they'd be easier to reproduce, as he'd pick something like a starter or Pikachu, but obviously he chose Machamp, which was more difficult than the Garchomp I'd ruled out!
Anyway I decided I'd give Machamp a go rather than ask his third choice, how hard could it be? Find out below.
Supplies
Materials & tools wise it all depends on what Pokémon your going to produce and the size you want it, but everything I used for Machamp is listed below:
- Hama beads midi size (5mm) in various colours - I used black, Pastel Blue, Icy Pastel Blue, Cream, Grey and a mixed bag containing most of the colours for the small details.
- Transparent peg boards - based on the size of my design I worked out I'd need 9 of these
- Masking / painters tape - I used a wider tape for ease, low tack options will work better as long as they hold the beads in place well enough.
- Machamp design printed out to the correct size
- Tweezers (optional)
- Scissors / knife
- Iron - I just used my standard clothing iron, but you can get special craft irons with larger surface areas and adjustable temperatures, but this worked fine for me it just takes a little longer.
In addition to Machamp I also made a frame to display him in, here's everything I used for that:
- Super glue & activator
- 38mm x 25mm x 2400mm timber baton
- 5mm x 15mm baton
- Large washers
- Woodscrews
- Large clip frame
- Chalk paint
- Wood stain
- LED light strip - I got a colour changing one with a remote and app control off Amazon
- Drill
- Chop saw / Japanese saw / Band saw
- Palm router
- Carpet tape
Step 1: Design Machamp
The first step in this project was to design Machamp, so that I could then re-create him in the fuse beads. After some research I decided to use Hama beads of which there are 3 sizes, 10mm, 5mm & 2.5mm.
To get better detail in your design you either need to make the design big or use smaller sized beads. Due to medication side effects I often have shaky hands and find detailed work difficult sometimes, so with that in mind I chose the 5mm beads as 2.5mm would have been far to complicated to try and place on the pegboards and the 10mm I would have lost definition in the design, unless it was a meter tall which was a bit big for what I wanted.
With the bead size decided I then looked online for images of Machamp that I thought would look good, as you can imagine there are thousands, but I found a couple that I liked.
Now there are some websites and software that you can upload images to and it will convert that image into a fuse bead design for you, listing the colours and giving you a pattern to follow. Some even let you select the brand of bead you're using to give you exact colour names, based on the image you upload and the colours it detects.
One I tried was called Pixel Beads, I uploaded my image and put in a size in beads for width. As I wanted my Machamp to be about 500mm tall I entered 100 beads tall (100 x 5mm beads = 500mm) and the result it gave is shown in the image.
It wasn't too bad, but there were a lot of random colours in the design, 17 total and it reckoned I'd need 10,000 beads for the whole piece, which seemed a lot and was a bit of a daunting prospect for my first go at this and I had no idea if that was even correct. I didn't want to order 10,000 beads then find out I only needed half that many.
After trying a few sites, I eventually gave up and decided to try and draw my own design using Microsoft Excel.
Step 2: Excel Design
To start my design I inserted one of my images of Machamp that I'd found into excel. The peg boards I'd seen said they were 29 x 29 pegs square and used 5mm beads, which meant each board would be 14.5cm square.
On the worksheet in Excel I sized each row & column height and width to 5mm (for some reason you can only have 5.08 or 4.87mm there is no 5mm exact sizing option, so after typing 5mm Excel set them to 5.08mm). Also the sizing needs to be done whilst in page layout view, otherwise the worksheet is sized in pixels and the rows and columns have different pixel dimensions. 5 pixels high isn't the same as 5 pixels wide.
Once all the cells were sized I could then draw out a grid of squares 29 x 29 to match the size of each individual peg board. I then set the paper size to A2 to reduce the amount of sheets I need to print out later on. The bigger your design obviously try and print on as bigger paper as you can, saves time later trying to line individual sheets of paper up.
As I initially wanted my design to be around 500mm tall I positioned 9 peg boards on my excel sheet which gave me a height of around 435mm and filled a sheet of A2 which was plenty big enough.
From here there were now two ways of creating my design, I could either copy along with the image I'd inserted to the worksheet, which is what I did, first drawing the outline of Machamp using filled in squares, trying to copy the design from the image on the page next to me as best I could.
The other way and probably slightly easier, if you can size your inserted image correctly, is to increase the opacity of the image so that the gridlines of the worksheet begin to show through. You can then fill in the squares over the top of the image to give you your design, kind of like how tracing paper works.
My design ended up around 3647 beads in total, which was good enough to include all the detail I wanted, whilst not being too big that'd take ages to complete. Once I finished copying the outline in black I could then start to fill in the rest of the squares with the colours of Machamp to bring the design to life.
At this point I'd not ordered any materials as I had no idea how much of anything I'd need, but now I had a design in Excel I knew how many peg boards I needed by which squares Machamp covered. To calculate how many beads I'd need I used Excels ability to write formulas.
After I'd coloured in each square a different colour, I then assigned that square a corresponding colour code, 'k' for black 'db' for dark blue, 'b' for blue, so on and so on. I'd managed to only use 10 colours, but I still needed to buy these 10 colours and as they come in bags of 1000+ I didn't want to overorder on colours I didn't need many of.
To get the exact amounts of each colour I used a count formula, using my colour codes as the criteria to give a total for each individual colour. For those interested the formula was as follows:
=COUNTIF($A$1:$CI$87,"k")
$A$1:$CI$87 is the area my design occupies on the worksheet i.e. it starts on cell A1 and covers all cells up to cell CI87. The "k" means look for that colour code and only count cells with that code in. For the other colours all I had to do was replace the "k" with the other letters for the other colours, "db", "b" etc.
My first formula above, returned a value of 1002 which meant I'd need 1002 black beads for my outline of Machamp, this and the two blue colours were the highest totals all over a 1000 beads each.
I've attached my Machamp layout drawing so you can see it in more detail, sadly Excel files aren't supported, so its in pdf format.
Attachments
Step 3: Order & Wait
With my design complete and the totals for each colour of beads calculated, I ordered my beads and peg boards online.
I ordered from a place called Rito Hobby which was by far the cheapest place I could find these beads, located in Denmark, although it only took a week to arrive to the UK in the end. Loads of other places also sell them, Amazon, eBay etc online and some high street shops too, not necessarily Hama branded, Ikea have a version, but sadly not in the colours I needed. The other main one I came across in shops was Perler beads, usually mixed colours, so for bespoke, large designs you're better off ordering which colours you need.
As I said my biggest three colours were the black, dark blue and blue, so for those I ordered a bag of 1000 of the black and 3000 each of the two blues. For the rest of the colours I ordered a mixed colour bag of 1000, hoping that I'd be able to get enough from that to make up everything else. Unfortunately once I started I did realise I'd not have enough grey or cream beads, so I did have to order 1000 each of those in addition to finish the design. In hindsight I should've just ordered a 3000 mixed bag and that would have done me, but as it was my first foray into this its all a learning curve.
With everything ordered the week before Christmas, it was just a matter of waiting for it all to turn up. Luckily I wasn't seeing Flynn until the New Year, so I had time for slower delivery and time off over Christmas to put it all together.
Step 4: Hand Cramp Time
With all my materials finally arrived I could make a start getting this thing put together, the first step was arranging my template.
I'd printed off my Machamp from Excel on A3 paper (no A2 in the work printer at the time) and he'd covered 4 sheets. When you do print make sure its at 100% and doesn't resize it to fit on the paper, otherwise you could end up with a smaller template.
With it printed I cut off any margins and stuck the 4 sheets together with Sellotape, so that I had one large sheet with my design on.
I could now fix my peg boards together over the top of the design, so that it could be seen through from underneath and I could place the beads in their corresponding locations. If you are going to do this as well make sure you buy the transparent peg boards as the white ones and other colours you will obviously not be able to see through and will have to copy by eye alongside.
With the peg boards in position it was now just a matter of starting to place the first of the 3647 beads needed to complete the design over the top.
I decided to start with the black to get the outline of Machamp first, starting in the top left corner working across and down until all my black beads were placed.
During this stage I realised my template was off slightly, as the peg boards seemed slightly smaller, maybe it was the 0.08mm extra on each cell of the template adding up to increase the template size. It didn't matter, it just meant I had to move the pegboards around slightly when populating each one with beads, so the pegs were over the correct area of the template. In future I just need to double check my templates after I print them.
Once the black beads were done I could then move on to the other, smaller quantity colours, filling in the areas mainly around the face and waist. I'd picked out the smaller quantities from the mixed bag of coloured beads and luckily, with the exception of the cream and grey, had enough to complete the sections where they were needed.
The next stage was then to start filling in the blues, which made up Machamp's whole body. I started with the darker shade, which imitated the shadowing he'd have on his body stood in the daylight, once all that was filled in all that was left was to fill in any blank pegs with the remaining light blue beads.
I initially started off by placing the black beads using a small pair of tweezers, however after a while it became apparent this was a slow process and it was quicker to place them by hand. The tweezers were useful though for placing certain beads in small areas such as the eyes or retrieving beads that I dropped onto the peg boards or that I put in the wrong place. I suppose its whatever feels comfortable really, speaking of which it took me around 3.5 - 4 hours to place all the beads, which seems like a long time, but in reality that's around 4 seconds a bead. After that amount of time and over 3600 beads your hand and fingers do start to cramp up though, having to pick and place each individual bead. Maybe if I'd stuck with the tweezers for the duration it might not have been so bad? Maybe I'll try next time and compare hand crampiness.
Step 5: Taping & Hole Punching
Now that all my beads were laid down and Machamp was looking good I needed to melt them together to form the image. Online there's many different methods and opinions, preferred or disliked, but a common one seemed to be taping.
With my beads still in situe on the peg boards, I used some wide masking tape to cover up the entire design, overlapping the tape slightly to make sure all the beads were covered and securely stuck in place.
I used the remaining roll of tape to then further press down on the beads by rolling and sliding it over the top to make sure every single one was stuck to the tape. Once I was happy they were all stuck down it was time to poke holes through the tape into every bead location.
The reason for this is so that when you melt it the heat flows more evenly and stops blemishes from occurring in the design on the opposite side, blowouts, burns etc. Some people think this is a waste of time and it was painstaking poking 3647 holes with a ballpoint pen, but after I'd just spent 4 hours laying beads I didn't want to skip this step and possibly ruin the end piece. It didn't take me that long to do it anyway and on smaller pieces it would be a quick step to do.
After I'd poked all my holes I then cut off any excess tape from around the edges of the design, this is to try and prevent it sticking when I attempt to remove it from the peg boards in a second. Placing a large frame over the top I then lifted up the peg boards, holding it firmly to the frame and flipped the entire thing upside down, I could now tease off the peg boards from the beads picking any tape off where it had stuck to the boards to release that section. At this point the beads are only held in place by the tape so I needed to be careful so as not to move any or cause any damage to my design.
Thankfully with some peeling and pulling the whole thing came away and was now sat flat on a plywood board with the design the other way round.
Step 6: Melty, Meltson
Now that Machamp was off the peg boards it was time to heat him up and melt the beads together, I could have done this whilst the beads were in place on the boards and not bothered at all with the taping, but the heat will warp the peg boards and possibly stick to the design. I also planned to do something called a flat melt which closes all the holes of the beads up, so he definitely would have stuck to the boards.
To begin fusing the beads together I had Machamp on the plywood board, flat and level, taped together on the under side. I then used some ordinary greaseproof paper, like you use in baking to stop cakes sticking to their tins, laid over the top of Machamp (I had to use two pieces as Machamp was bigger than the papers width)
I then set my iron to its maximum heat setting, waited for it to heat up, before positioning it over the top of Machamp on the greaseproof paper, slowly moving it around over the various parts of his body, starting with a leg and working until I'd covered all of him.
As I said I was going for a flat melt, which means all the beads melt together and there's no gaps in the design, this requires more heating and applying of pressure, so that the beads kind of squash down a bit and fuse together, whilst closing up the hole in each one with melted material. Once I was happy I'd melted everything together I placed a large, flat, heavy object, which was a mirror I had to hand, on top of Machamp and the paper and waited for him to cool, so I could remove the paper and see how he looked. The weight of the object keeps him flat whilst he cools so he doesn't warp and curl up at the edges.
After around 15-20 minutes I removed the mirror and peeled off the paper, the melting had worked, but there were still a lot of little dimples where some of the beads hadn't fully melted flat, so I re-heated the iron, placed the paper back on top and did a second melt, pressing a little bit harder and using the tip of the iron to work on spots that weren't fully melted after the first pass. When I was satisfied I put the mirror back on top and left him to cool once more.
This time after I removed the paper the dimples had mostly gone and I was now happy with how he looked, more than happy actually with it being my first go.
All I had to do now was flip him back over to the tape side and peel off the masking tape from the reverse.
This proved very difficult, as poking the holes in it meant it was coming off in very small pieces, plus the heat had welded most of the tape to the beads. In the end I used a combination of scrubbing, scraping and sanding to remove the tape, but even that didn't get it all off and I didn't want to go to hard with the sander and damage Machamp with heat build-up.
In this case it didn't really matter if I had left over tape remnants as I was going to mount him on a board in a frame, but if I'd wanted two clean sides, or to melt on the reverse as well, then next time I think I'd try a lower tack painters tape like Frog tape, as the standard masking tape I'd used was very sticky when I'd first applied it.
Step 7: Framing
With Machamp all but finished, I now turned my attention to a frame for him.
The plan was to make a simple square frame to mount him on with some LEDs in to hopefully illuminate him once hung on the wall.
I'd bought a simple clip frame to use that had a back board and a Perspex front and I was going to make a wooden surround to house the LEDs in and hold everything together.
To make the frame I used some 38mm x 25mm timber baton I had left over from another project. I began by cutting the two tall side pieces on my chop saw, the length of which were the length of the clip frame (610mm), plus twice the width of the frame timber (38mm x2) minus the width of a rebate on either side I would cut into the timber to sit the Perspex and back board in (10mm x2) Overall that meant cutting the sides to 514mm.
With the two sides cut I then used my palm router with a 10mm slot cutting bit in and ran it down one side on each of my two frame lengths, giving me two 'L' shaped pieces.
The top and bottom pieces of the frame would need to sit flush against the inside of these side pieces at either end, so using my Japanese pull saw I cut away the routed lip to give me a flat surface to match the top and bottom pieces to. The width of the cut was the same as the width of the frame timber, 38mm from each end.
With the sides cut I could lay them both flat on my bench and sit the back board in between the two, making sure it was sat flush in my routed channels. With the back board in place I could then measure in between the two side pieces at the top and bottom to get my sizes for the top and bottom frame pieces, cutting them to length on the chop saw, before routing the same 10mm channel in each of those.
With all 4 sides cut, I could then lay up the frame ready to assemble. To attach all the sides together I decided to just glue and screw. With the frame laid out I drilled 4 pilot holes through the side pieces, into the top and bottom pieces, one hole at each corner and countersunk the holes to recess the screw heads.
The glue I chose to use was some mitre bond, normally used for quick gluing or cornices and coving in kitchens and ceilings, but I use it for all sorts when I want a quick strong hold. All you do is apply the super glue to one side/surface and then the activator, to make it set rapidly, to the other side/surface. My activator was in the form of a marker, but I've also had the spray ones before and they both work well.
With the glue and activator applied one each to both pieces in one corner, I quickly brought them together and screwed the joint up tight where I'd drilled my pilot hole. I repeated for the other 3 corners until the whole frame was solid and fixed together.
At this point I then gave the whole frame a sand back with 120 grit in my random orbit sander and cut off the excess on the sides of the frame. When I originally cut the two sides on my chop saw I didn't apply the old measure twice and cut once rule and had measured them wrong, thankfully bigger than I needed rather than smaller, so after gluing up I trimmed off the tails with my Japanese saw, flush with the bottom of the frame.
To finish the outer frame and back board before I add the lights and Machamp I gave each of them a little bit of colour. For the frame I used some blue spirit stain I had. I always see these at woodworking shows in loads of colours and I picked this one up years ago, excited to make blue stuff, but I rarely use it for anything, so though this was a good opportunity.
To apply the stain I just used a paintbrush and liberally applied it all over the timber, wiping down with a rag after the first coat. I then applied a second once dry to intensify the colour slightly and left it to dry.
For the back board, I wanted a fairly neutral colour so the vibrant Machamp stood out. Looking in my paint cupboard I found some slate grey, chalk furniture paint which was ideal. This stuff is thick and gives a nice even finish usually in just one coat, so I used a small roller to apply the paint to the back board and left it to dry. After it had dried it looked good and well covered, so I didn't bother with another coat.
Step 8: LEDs
With the frame built I now needed to add my LED light strip inside the channel I had routed out. The LED strip has a self adhesive backing, so it was just a case of peeling and sticking it to the side wall of the channel inside the frame.
I started the run from the bottom of the frame, however I needed a place for the cable to come out so that the LED light controller was on the outside at the bottom of the frame. This was so that the remote control for the lights could see the infrared sensor and change the lights colours and modes.
To get the wire to pass through the frame I just cut a slot out using my Japanese saw, wide enough for the LED tape to pass through, allowing me to glue the controller on the bottom of the frame and then run the lights through the slot to the inside of the frame.
With the controller glued I started running the LEDs, making sure they were firmly pressed against the frame so they were stuck tight. As it was a tape, in the corners I could simply bend it round, until I had the LEDs running all the way round the inside of the frame.
With the LEDs attached I then tried in my Perspex and my backboard. Unfortunately at this point I realised that they would sit too low in the frame, meaning the LEDs wouldn't be seen from the front as they'd be behind the backboard once everything was in place. I was hoping the thickness of Machamp sandwiched between the Perspex and back board would raise the backboard enough so it was above the LEDs, however that wasn't the case.
To remedy this issue I decided to cut some small blocks that I could glue in place on the frame between each LED on the light strip, then my Perspex and backboard would sit on top of these blocks raising them above the LEDs so that they would then shine out on the front and illuminate Machamp.
The blocks were cut from some 5mm x 15mm timber I had and I just ran these through the bandsaw at 5mm lengths. I cut 18 blocks in total, 5 for each side and 4 for the top and bottom. I simply glued these in place with my mitre adhesive on the frame in between the LED locations. The glue dried pretty much instantly with the activator, meaning I could stain them in the matching blue straightaway.
With all the blocks glued in place I then tried in my Perspex to make sure it sat above the LEDs, so the lights would hit Machamp, which thankfully it did.
Now I just need to assemble everything together.
First thing was to stick Machamp to the backboard, initially I was going to use my hot melt glue gun for this, but then I saw I had some double sided carpet tape, so decided to use that instead. I cut some pieces off and stuck those to the back of Machamp on each area of his body. I then peeled off the backing tape, before positioning him over the back board in a central location. I then stuck him on to the back board applying pressure, so that the tape bonded to the board and held Machamp in place. A quick stand upright to make sure he didn't drop straight off and we were good to go.
I placed Machamp inside the frame over the top of the Perspex. To hold the backboard and everything else in place I modified some washers so that I could screw these to the back of the frame, with the washer overlapping the backboard, effectively clamping it in place. To modify the washers I simply drilled a small hole in each on the outer part of the washer, that allowed me to get a screw through into the frame. I used 8 of these positioned all the way round the back board to securely hold everything together.
With everything assembled I could now stand the frame up to check it and test out the LEDs. I plugged in the USB cable to a power socket and the LEDs lit up and started cycling through each of their colours. I could use the remote to pick an individual colour, or use some of the pre-sets modes to flash, strobe etc. The other cool thing about these LEDs were that they had Bluetooth connectivity meaning I could link them to an app on my phone and use that to set the exact colour and brightness that I wanted. It also had other feature like change the lights according to music playing or set timers for the lights to go on and off at.
Step 9: Machamp
Here is Machamp all finished and ready to be hung on the wall. This was a fun build to do, although the fuse beads can be fiddly and the melting process tricky to get right, you can pretty much make anything you like and get some really good detail with the beads.
I have already made a Pikachu template, so I'll likely have a go at him next, maybe not on the same scale as this, something slightly smaller I think.
Anyway hope you enjoyed reading through and it inspires you to get the beads out.
See you on the next one!
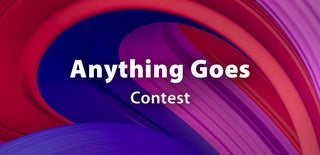
Participated in the
Anything Goes Contest