Introduction: Geodesic Dome With Cardboard Tubes and Laser Cut Connectors
In this instructable I’m going to share my experience with you on how I’ve made this huge geodesic dome. It’s 8m in diameter, almost 5m tall and made entirely out of cardboard tubes and wooden connectors.
I made this for a local small music festival, to create a “chill zone” where people could hang out between the various live performances.
Step 1: Research: Dome Frequencies & Sizing
I started this project by doing some research: rather quickly I found a bunch of information on the domerama website and I learned about the different frequencies a dome could have. Everything starts with a 1v dome, here all the rods have the same length. If you go to a 2v dome you have 2 different lengths and the construction starts to look like an actual dome shape. The higher the frequency, the more your dome shape will approximate an actual sphere, but it comes at price, because it will result in a more complex build, with more pieces and more material and time needed to produce them. So in the end I settled for a 3v dome, because it seemed the best trade-off between roundness and complexity to me.
On the domerama website there are also a bunch of calculators that help you to design your dome. I chose the 5/9 Kruschke method, this will result in a dome with a flat base and will be slightly taller than an exact half dome, thus giving us a bit more volume inside the sphere, because the sides will be more vertical. For the size I chose a diameter of 8m (26ft) which resulted height of 4,7m (15,5ft). This is the highest I wanted to go, because otherwise it might be too high to put together.
When I enter the 8m diameter in the calculator I automatically get all the dimensions and quantities of the struts that I need. In this case it tells me that I should have a total of 165 struts with 4 different lengths.
While this still is a dome with a frequency of 3 (and you would only expect 3 different lengths) The Kruschke version has an additional length to make sure that the bottom is perfectly flat.
Now that I know all the dimension of the struts and how much pieces that I need, the last thing I need to solve is choosing a construction material and a connecting method for these different pieces. I did some more research and got inspired by the open source concept i found online under the name of "domenico". There they used cardboard tubes and CNC’d connectors.
Since the budget for this project was very limited I settled for this method, I was able to convince a local cardboard manufacturer to sponsor us all the cardboard tubes in exchange for a picture of the end result and a timelapse of the building process. And because I work for a FabLab, I have access to a laser cutter as well.
Step 2: Design
I based myself of the connectors of the domenico project, they have the STL files of their connectors on their github, I imported them into Fusion 360 and started modeling my own version with a focus on a laser cut process instead of a CNC-milled one. We don’t have a big CNC machine at our disposal and I figured if i made the design in thinner material it would work just as well, since the domenico connectors were designed for a dome up to 14m in diameter. Using a laser cutter instead of a CNC mill also results in less setup time and a faster prototyping process overall. All the angles of the connector are crucial, if they are only the tiniest bit off, this will result in a cumulative error when all the pieces are connected to each other. Using the laser cutter will make this easy. I can enter all the correct dimensions and angles in my design, test it virtually to see if the whole build is going to fit together nicely, and only start making the connectors afterwards when everything is working out perfectly in the tests.
Because the domenico.cc project used 18mm plywood (¾ inch) and we could only cut up to 8mm plywood with our laser, I decided to make a prototype to see if my design would hold up. Everything seemed to fit perfectly and the construction also looked sturdy enough. I modelled all the pieces and copied them in a huge pattern to double check that I didn’t make any mistakes before I order all the cardboard tubes and made all the connectors. For the cardboard tubes i ordered the quantities and dimensions I generated using the calculator. And made sure to subtract 240 mm of each tube length to compensate for the length taken up by the connector.
The tubes have an inner diameter of 50mm and an outer diameter of 56mm and are coated with a polyethylene layer, to give them a little bit of water resistance which might come in handy if there was a little bit of rain on the day of the event.
For an entire dome with a 8 meter diameter you need:
30x "A"-struts with a length of 1078mm
35x "B"-struts with a length of 1289mm
80x "C"-struts with a length of 1446mm
20x "D"-struts with a length of 1524mm
Step 3: Make
Now for the tedious part: laser cutting all the pieces and putting them back together. This takes up most of the time... We need 61 connecting pieces and I designed 6 different connectors: 3 four-way connectors for the bottom, 1 five-way connector and 2 six-way connectors.
In total you need these connectors:
For the bottom row:
5x 4C
5x 4CDCB
5x 4BCDC
For the rest of the build:
6x 5A
10x 6C
30x 6BABCDC
You can find all the .dxf files for laser cutting these pieces here, this is a design for 8mm thick wood. Red lines should be cut and blue lines should be engraved. I've cut everything out of poplar plywood. Birch might be a stronger (but usually also more expensive) alternative. I used regular wood glue to glue all the pieces together and only sanded the center part of the connector because you wouldn’t see much more once everything was assembled. I've also included the 3D-models of the parts (.F3D-files). You can use Autodesk Fusion 360 (free for hobbyist and non-profit use) to change the design if you like, for example if you want to use a sheet material with another thickness.
Step 4: Build
Now for the moment of truth, since we had all our pieces only just before the event, we could only put everything together for the first time at the event itself. This is normally the one thing you should absolutely avoid, because a little bit more testing earlier on in the design process could have saved us a huge potential headache now. But because of the production time of the cardboard tubes and the plywood connectors, I only had just enough time to get everything exactly right in time for the actual event. So I had to make everything as good as I could within this timeframe and budget and then just hope for the best.
At first we had a bit of a debate whether we were going to build it starting with the top piece and pushing everything up. This would mean we wouldn’t need any ladders and might make the assembly process a bit safer. We would need more people to lift everything up for the last layer, but that was something we could take care off. And despite the fact that nearly all the videos that I saw online started from the bottom and worked their way to the top, it at least seemed us worth the try.
We were in only one layer and already 2 of the connectors snapped. It’s a bit too late for a “back to the drawing board”-moment now, but we were able to mend all the broken pieces and tried the bottom up approach. And this seemed to work a lot better. It took us about one and a half hour, mostly because we had a little bit of rain during during the setup, to put everything together, the first layers went fast. As we made our way up it became a bit harder, because you had to put all the pieces together while standing on a tall ladder.
Step 5: Final Result + Afterthoughts
This is wat the dome looked like during the event. The whole construction is sturdy when everything is put together, but building the whole construction without snapping some arms of the connectors isn't always that easy. I highly underestimated the forces that are exerted on the connectors during assembly. The cardboard tubes are all longer than one meter, so if you try to move one end of a tube while the other end is already connected to a laser cut piece, you've essentially created a giant lever. A lever that can easily break the arms of the connecting pieces apparently. :/
Some of the tubes got a little bit of rain inside of them during the event, which caused them to expand. This, and the fact that the factor of safety of the laser cut pieces is just too small, caused the construction not to be so reusable for future events. Which was quite a bummer, considering all the work I put into it.
If i would make this dome again, i'd use aluminium or steel tubing. This way, you can avoid having to make the very complex connectors and you only have to worry about the right lengths of the tubes. You can simply squeeze the ends together with a vice or hydraulic press and as long as the distance between the two holes at the ends is correct, you don't need any complex angled connectors, because everything will work out perfectly as long as you're connecting al the tubes in the right order. In this case you can just use nuts and bolts to put everything together, which is fast, cheap, easy and sturdy. The only problem in this case is that you have to get hold of a couple of hundred meters of steel or aluminium tubing, which usually makes this a more expensive option.
All in all I'm very happy with the end result though, I received a lot of compliments about it and it served its purpose perfectly during the event.
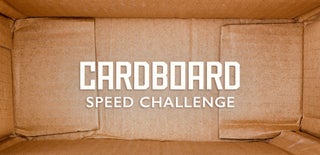
Second Prize in the
Cardboard Speed Challenge