Introduction: Ghostbusters PKE Meter
There was one cartoon in particular that seems to dominate my childhood memories and that was The Real Ghostbusters. Ray, Winston, Peter and Egon were armed to the teeth with really cool gadgets, among them the PKE meter. This was my favourite of all their tech and it basically detected the ghosts they were trying to hunt.
What I am going to do is make my own fully functional PKE meter.
Supplies
- 3D printer (although there are plenty of services which will print and post)
- 3D model files found here.
- Raspberry Pi 3B+
- Night vision camera
- Sense Hat
- 3.5” Monitor (I’ve found a cheap alternative to official Pi screens which need a bit of modding but works great)
- Wires
- Screws/bolts
- Battery pack found here.
- Buttons (I used some left over from an arcade project)
- GhostBox Code (included in Step 6!)
- A word library (included in Step 6!)
Step 1: Printing the Case
The 3D model I used is printed off in parts, most of the smaller bits I didn't even print off. I am only using the handle, the main box, the lid which houses the buttons and screen and also part of the antenna.
The 3D print originally intends the use of little arms coming out of either side of the main antenna but I have decided to attach a night vision camera to mine so that I can see in pitch black whilst using the PKE meter.
To attach the handle to the main box I used two nuts and bolts, pretty thick ones. This is better than using super glue in case you need to take it apart again. For the time being leave the top part off the box, we still need to fit the monitor.
I found that the case was printed with a lot of excess plastic on the inside but its easy to trim it away with a sharp knife.
You can find the model here.
Step 2: Preparing the Screen
I have searched the internet high and low but couldn't find a suitable screen which would fit the 3D print. That's when I resorted to looking for RCA composite screens.
There's a lot of screens on Amazon designed to be used with car reversing cameras. These types of cameras are the perfect dimensions for this project and they only cost around £15. This is less than half the price of normal LCD's designed to be used with the Raspberry Pi. They require some modding before it can be used with the Pi.
The quality of the screens isn’t as good as an LCD but it gives that retro effect that I think fits perfectly with this project.
The monitor is designed to be used in a car with a rear view reversing camera. We won’t be needing any of the wires or the case.
There are four screws securing the case, one of which will most likely be under the warranty sticker on the back. Just poke the screwdriver through to get to the screw. Once you have removed all four screws then the cover should become loose. Open it and carefully remove the screen assembly from the case. You will need to cut the wire just above the point it enters the outer case to remove it.
Once this is done you can work on the pcb more easily. Use a soldering iron to neatly remove all the wires. Once this is done you should have a screen with the pcb on the back.
As you can see in the featured picture, the design of the pcb can vary as I’ve ordered a couple of these now (through trial and error damage!. These are the two variants I’ve come across so far and the orientation of some of the components differ from one to another.
First things first you need to solder a wire between one of the legs on the chip circled in the picture to the left most contact at the bottom of the pcb.
The contact that you just soldered the chip to is also being soldered from the same contact to one of the free 5V GPIO pins on the Pi. The black wire on the second contact connects to one of the free ground GPIO pins and the yellow wire on the third contact is being soldered to one of the contacts under the RCA jack underneath the Pi as pictured.
I used jumper wires with a male plug on the side which goes towards the Pi so I could connect female to female wires to the Pi and plug them straight into the monitor. This is a safer approach due to the monitor pcb has a tendency to break if you pull it about too much.
Now your screen should register the Pi's output when you turn it on. When you need to fit the screen you will find it fits really snug inside the PKE meter lid without needing to fix it in place.
Step 3: The Buttons
I made the mistake of fitting the Sense Hat before I put the buttons on. Its easier to sort the buttons out before doing this so ignore the Sense Hat in the pictures.
To display the Sense LED matrix I cut out a hole the same size as the matrix into the top of the 3D printed box of the PKE meter. It took time and patience so try not to rush this as you will have to 3D print the lid if it goes wrong. I used wire cutters to clip in between the holes that are already in the plastic and then I used a Stanley knife to carefully slice away the edges until I was left with a suitable square hole.
I am using two buttons which I got from an arcade machine kit that I bought from Amazon. They fit nicely over the holes where the buttons should go on the meter and I used a little superglue to fix them in place in case I need to get them off again.
There should be a small hole in the bottom of each button-hole which you can feed two wires through. These will both be attached to the button contacts. Once you have soldered the wires to the buttons and glued them in place, attach them to suitable GPIO pins.
Because there is going to be a night vision camera attached to the project I wanted a button which will take a screenshot and save it on the Pi in case anything strange appears on your investigations!
The other button will be for safely turning off the Pi once you are finished with it.
Step 4: The Sense Hat
The Sense Hat is a brilliant hat for the pi which contains multiple sensors reading a number of different things. The code I am using, GhostBox, takes data from these readings and puts it through an algorithm which picks a word from a pre made library and displays it on the LED matrix on the Sense board.
After cutting out the hole in the lid for the LED matrix I pushed the button wires to one side, making sure they had plenty of room to reach the GPIO pins and then attached the Sense Hat to the top of the box using some small screws. This was a bit of a bodge job but the screws can’t be seen from the outside and they seem to hold the sense hat in place really well.
There are a lot of wires everywhere so follow the diagram on the next step of which wires go where and make sure you use the male to female jumper wires. The male end plugs underneath the Sense Hat and the female end connects straight to the corresponding GPIO pins on the Pi.
Step 5: The Camera
The PKE meter in the Real Ghostbusters cartoon features an antenna which comes out of the gadget and flashes. I didn’t have the time to do this so instead I decided to attach a night-vision camera to the end so that the device can be used in complete darkness.
I am using this camera which comes with a stand that I have used to attach the camera to the antenna. I used some long screws designed to be used with the Pi board but there are many other ways to attach the camera to the antenna so just attach it how you find easiest. I then fed the cable from the camera along the antenna and placed it underneath before drilling holes in the antenna and PKE meter and fixing them both together with a couple of screws.
When setting up the Pi make sure you enable the camera in the settings.
Step 6: The Code
I am assuming you have already installed an operating system on your Raspberry Pi, I went with Debian, and enabled your camera. There are plenty of guides on the internet for this.
The code I used for the Sense Hat is called Ghostbox and is fantastic. You can find it here. Basically it takes readings from the Sense Hat and churns them through an algorithm to choose a word from a predefined library. I downloaded one from the internet and made some additions to it such as a few more names and deleted some words which I didn't think were relevant.
Download/copy/whatever the code to your Pi. I went on the Pi's web browser, found the code and copied it to a new text file named Ghostbox.py. You can make adjustments to the code to change the colour of your text, the pattern that appears on the screen etc but the only thing I changed was the sensitivity of the device. This meant that it wasn't sensing me moving the PKE meter and displaying text.
To do this just open the code and go to line #58 and change the percentage from 2.5 to a higher number. Something like 4 or 5 will do. If you are finding it is still too sensitive then increase it as needed.
The code incorporates espeak so if you decide to add a speaker to the project then it will speak out loud the displayed word too. I didn't do this but if you can get it to work let me know how you get on.
To get the screenshots I used the raspivid command.
I have attached my code files to save you going through the stress that I did in piecing it all together like I did. The files ghostBox.py and pkebuttons.py go in /home/pi.
The file ovilus.txt is the library I used. Feel free to add/remove any words you want by simply opening it in Notepad or something similar. This file then goes in /home/pi/Documents
The file rc.txt contains the information to get everything to autorun when the Pi is started. This needs to be renamed to rc.local and placed in /etc/ .
As long as you follow the last couple of paragraphs then you should be up and running. Don't forget to change the pkebuttons.py buttons to the GPIO pins you have plugged your buttons into. I never got around to making a shutdown button so feel free to add this feature.
Step 7: Power
There are a number of options for power but I chose to use this battery pack. I found that it fit nicely inside the case underneath the Pi and you can use a USB cable to plug into the Pi. This means no messing about with more fiddly methods of powering your project. I attached a spare USB cable to the charging port of this board and trailed it out the back of the project so that I can easily charge it when needed.
Step 8: Fitting It Together
For the final step, I squished everything into the body of the PKE meter, making sure the GPIO cables stayed connected, then pushed the lid down. I found that my 3D printer didn't print the parts off amazingly and the lid kept popping off the top. I solved this by using superglue to hold it down.
There you have it! A working PKE meter. If you make this project and take it ghost hunting please get in touch with me and let me know how it works!
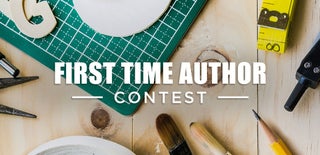
Participated in the
First Time Author Contest