Introduction: Giant Alphabet Blocks
Some really close friends of ours just had a baby and as a Christmas gift to them, we decided to make some wicked big alphabet blocks with their kiddo's initials! We wanted to use the X-Carve CNC to make some really neat animal carvings, some letters, numbers and of course some skulls! Because...babies love skulls.
There were some really interesting challenges in this project, such as what material to use, how to put the cube together, how to paint/finish it in a non-toxic kid-safe way, and some other fun stuff.
We also created a video (see above) with a lot of detail that you can watch along with reading through the guide here!
TOOLS USED:
- X-Carve (https://bit.ly/2vyBZGM)
- Circular Saw
- Table Saw
- Pencil
- Tape Measure
- Random Orbital Sander
- Paint Brush
- Planer (Optional)
MATERIALS:
- Pine
- Wood Glue
- Blue Tape
- Milk Paint (5 Colors)
- Black Spray Paint
- Shellac
Step 1: Prepping the Wood!
To keep the three giant alphabet blocks lighter and to keep the costs down we went with white pine, which is a soft and light wood. We got the pine boards from the big box store and carefully looked through the pile of 1" x 10" x 8' boards and picked the cleanest, straightest ones we could find. It was okay that they had some knots in them because we marked all the knots and then cut them out and ended up with a bunch of short blanks with clean wood.
From there, all of the boards went through the thickness planer to get them all uniform and clean them up. This part is optional, but it helps a lot if you have the means to do it.
From there, every board got ripped and cross-cut to exactly 9" square and in no time at all, we had 18 boards that were all exactly the same length, width, and thickness!
Step 2: Carving the Designs!
Carving the Animals
This part was a lot of fun! We used the X-Carve CNC to create some really awesome shapes on all the sides of our alphabet blocks.
Each cube was going to have 2 letters, 2 animals, 1 number and 1 skull. For the animals, we found a really nice pack of animal vector art that we purchased and then in Adobe Illustrator we edited and simplified the artwork to customize it to exactly what we wanted.
From there, the vector art gets imported into the Easel software for the X-Carve and we can move it around and size it appropriately for our 9" square pieces. The animals were carved to a depth of 1/8".
We used a 'V-Groove' bit for the carving, which, instead of a flat line gives you a really interesting V-style edge. It's also nice because it comes to a perfectly fine tip and is ideal for carves with a lot of small detail.
Since we wanted to paint the inside of the carved lines but leave the face of the wood unpainted, we used blue painter's tape to mask off the entire thing and then let the machine cut away the areas that would be painted.
Each animal took about 30 minutes to carve. We ended up carving:
- Alligator (A)
- Bear (B)
- Chameleon (C)
- Jaguar (J)
- Octopus (O)
- Yeti (Y)
We chose A, B, and C because they're classic for this project and we chose J, O, and Y because with that combination of 6 letters we could spell the baby's initials and a good number of other words.
Also, our friend thinks Bigfoot and Yetis are real...so it seemed like the perfect choice. ;)
Carving the Letters & Numbers
We also carved the corresponding letters for each animal by using three layers of cut depths in Easel. The lowest layer was a large square set to 3/8" deep. The middle layer was a series of stripes on top of the bottom layer that lay across the middle set to 1/8" depth, and then on top, we put the letter itself but set the cut depth to zero. This "cancels out" the carving in that area, so the letters are actually left alone while the space around them gets cut away. Really cool technique!
The numbers were really simple. We cut them all at a single depth of 1/8" and each carve took about 60 seconds each.
Step 3: Cutting the Miters!
For the cube to go together, we cut miter joints on the inside of all 6 pieces that would all come together as the cube is assembled. This means 4 miters per piece, 24 miters per cube and 72 miters total! If any one of these was crooked or not cut well, it would be difficult to put these blocks together so we carefully cut the miters to ensure as much accuracy as possible.
Using a digital angle gauge we ensured our blade was set to exactly 45 degrees and then used a sled we made on the table saw to accurately cut the miter joints on each piece. A stop block on the fence helps us to cut all of them at exactly the same length.
Before cutting all 72, we did some test fits using blue tape to ensure the blocks would go together, and it worked!
Once the testing was done, we cut all the miters and it didn't take long at all.
Step 4: Painting the Carved Pieces!
With all the prep we did, the painting was super simple! Using a can of black primer spray paint, we spray it from several angles to ensure we get paint in all the nooks and crannies.
After it dries, we peel away the tape to reveal the AWESOME results!
There was a tiny bit of paint leak under the blue tape that we ended up not being able to get off in the end, so we've since learned that there are better ways to do this such as pre-finishing the wood so the paint can be easily removed if it leaks under the tape. We're super happy with the results here but we're going to try it a slightly different way next time!
Step 5: The Biscuit Joints!
To hold the cube together as well as to help align the pieces during assembly, we opted for biscuit joints. These are small slots cut into the joint (using a Biscuit Joiner) where you insert 'biscuits' (see image/video) that hold the pieces together.
Each miter had 2 biscuit slots, meaning we had to cut 144 identical slots...so we set up a neat jig for this on our bench. There's more detail here in the video, but essentially we set the tool to its 45-degree setting and then we aligned the biscuit joiner on a T-stop clamped to the bench and aligned the workpiece to the same edge. We cut all 4 slots on one side, then moved both the tool and the workpiece to the opposite side of the T-stop and repeated the process. This helped us cut 144 biscuit slots in about 10 minutes. Awesome!
The size of the biscuit slot you cut corresponds to the size of the biscuit you're going to use. We learned the hard way that if the biscuit is too big...well, bad things happen. :( Nothing will go together and you'll have some big problems trying to assemble your pieces. Make sure you're using the right size biscuit for the slots you've cut!!
Step 6: Assembling and Gluing Up the Blocks!
Assembling the blocks was something we worried would be really difficult and prone to a lot of errors, but in the end with the correct preparation and planning it went smoothly. Mostly...
We carefully aligned the 6 pieces for each cube and made sure they were rotated correctly and all in the right place. From there we marked each side so they didn't get mixed up and then flipped them over so the bottom was facing up.
Since there's a lot of surface area to glue up in a short time, we used a glue roller to apply the glue along the miters. One trick we like to use is to roll blue tape around the roller, which can be removed later and allows us to use the same roller many times without the glue ruining it on first use.
Using non-toxic wood glue, we rolled it across all 24 surfaces, inserted biscuits with a bit of glue on them into each slot, and then slowly put the cube together all at once. In order for it all to go together, all 6 pieces had to come together at the same time. Luckily we had no major issues and we clamped it up from all sides and let it dry.
Step 7: Fixing the Corners!
One of the hallmarks of working with wood is that it moves and can twist and cup. Sometimes rapidly and in ways you don't want it to. :( After a few days of sitting in the shop, some of the pine boards we so perfectly prepared had started to warp and curve a bit. This made it so that when we assembled the cubes not all of the corners came together perfectly.
No big deal though we can use wood filler for this. But...wood filler is very toxic and gross and we don't want the baby to eat it. So, we used a wood glue and sawdust mixture, created a slurry and rubbed it into each of the corners where there was a gap. This works just like a wood filler but is non-toxic, dries the same color as the wood, and is incredibly easy to make and use. Also, it's free because you have sawdust all over the place. :)
Before applying the sawdust filler, we went to the router table and used a round-over bit set to about half its depth. This rounded over all of the corners "halfway" which was enough to expose the corners so we could easily fill them. Once the sawdust mixture was dry, we went back to the router table and repeated the round over but at the full depth.
If we had filled the corners prior to doing any rounding over, we might not have gone deep enough and may have still had gaps once we rounded the corners over later. Similarly, if we had rounded them over entirely, we'd have to do it again to clean up the excess filler once it dried. This method let us ensure we filled it deep enough to not be seen in the end.
Step 8: Surface Preparation!
Next up was sanding and surface prep! We used a random orbital sander to clean everything up and smooth out the surfaces. We made an effort here to remove some of the paint on the edges of the animals and numbers that had soaked below our masking tape, but as you can see in the image/video, we couldn't remove all of it.
Not every project turns out exactly how you planned...but hey...keep going!
Some compressed air helps get all the sawdust out of the carves to get them ready for painting.
Step 9: Milk Painting the Blocks!
To paint the alphabet blocks, we used milk paint! It's pigment mixed with a milk protein which is not only non-toxic and fine for kids but it's also PERFECT for painting on raw wood. If you've never used milk paint and you work with wood a lot, we highly recommend you try it!
We picked out 6 colors but our "yellow" was basically invisible on the pine so we tried to mix an orange using our yellow and red...but just ended up with a gross peach color that we didn't like. In the end, we repeated the turquoise on 2 letters and didn't use the yellow or peach mix.
After carefully masking off the letters on each block, we used a soft paintbrush to apply the paint to the bigger surfaces and then used a stiff bristle brush to carefully paint the edges.
When the paint was dry, each block was finished by spraying on a few coats of non-toxic shellac and then hand polished with some 0000 steel wool.
Step 10: The Results!
I don't think we could be any happier with how these came out. They definitely maintain that classic, well-known look of an Alphabet Block you'd see at the toy store but still have that Wicked charm and style. Not to mention they're HUGE! :) Unique, awesome and a lot of fun to make. Highly recommended project!
We hope you've been inspired to try something like this. Be sure to check out the video as well and let us know what you think of the build in the comments below. Thanks for reading!
Now, go make something!
Want to see more of our stuff? Come follow us!
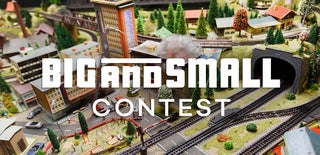
Second Prize in the
Big and Small Contest