Introduction: Giant Brushed Motor
You may have used or even dismantled a brushed DC motor but do you know how they work and would you be able to make one?
In this instructable I will tell you how brushed DC motors work and how you can make your own one which will hopefully work and not shake too much.
Supplies
To make your own brushed DC motor you will need:
- Copper wire. (I bought a lb of 26awg 0.0157" (0.3925mm) gauge copper wire from amazon)
- Copper foil or rather flexible copper sheet.
- Thin plywood or MDF.
- 4 large magnets. (I used ceramic disc magnets with a diameter of 70mm)
- Elastic bands/zip ties.
- 2 Bearings
- Kebab skewers.
- Wire.
- Plenty of batteries. (mine works best with a 15v power source)
- A length of dowel.
- Masking tape/sellotape/electrical tape.
- Double sided tape.
The tools you will need are:
- Glue gun
- Saw/rasp/file
Step 1: How Do Brushed DC Motors Work?
Most Brushed DC motors have a rotating shaft with 3 sets of coiled copper wire perpendicular to it inside a case with 2 magnets of north and south orientations on either side. The current of the coils is changed by the brush system at the end of the shaft where 3 equally sized and spaced copper third collars encircle it and each connect to 2 different coils. These in turn make contact with the 2 brushes attached to the casing and rub loosely on either side of the shaft so that any one time 2 of the copper collars touch one of the brushes. This means that the copper coil which is connected to both of the copper collars will have current and act as an electromagnet and turn the rotor towards the magnet that it is attracted to. Once this has happened as the shaft has rotated the pair of copper collars will have changed and the cycle will continue as voltage is input.
How stuff works has a better and more concise explanation:
https://electronics.howstuffworks.com/brushless-motor.htm
Step 2: How to Make Your Rotor:
For this you first need to make two fidget spinner shaped pieces of wood complete with central and edge holes but ideally with lips to hold the wire (mine aren't as large as would be optimal). You should decide how long you want the rotor to be and attach dowel of that length through the outer holes and a piece of dowel 1.5 to 2 times that length through the middle so that it sticks out further on one side for the brushes.
Next you have to wind plenty of coils of copper wire around the projecting bits of wood. Using my copper wire I found I had enough wire for 600-700 winds around a 97/98mm rotor. I recommend keeping track of how much wire you use on each one by weighing the roll after a hundred or so winds but bare in mind that the winds will get larger on either side. I also would encourage you to wrap some masking tape around the rolls when you have them all completed.
The final stage of making the rotor is to take the start of one coil and connect it with the end of another coil and using this first one as a calibration continue connecting the other 2 ends withe the other 2 starts (you may be able to see this with the rotor from a dismantled motor). You can then thread them through your bearing but not letting the uncovered surfaces touch one another and glue your bearing around the dowel leaving plenty of free dowel length. Then attach the other bearing around the other end of the shaft.
Step 3: Making Your Casing:
To make your casing you first need to cut out your frame pieces. I recommend using plywood as it will look nicer and be a bit more robust than my MDF and also cutting holes through the center of the frames to help secure the magnets. The frames I used were 2 square ones for the sides, a rectangular one (without cut-outs) for the base, a square with protrusions for the pieces holding the rotor and 2 thin strips just wide enough for the bearing with a hole in them for the rotor shaft (I only have one on mine as the second one broke hence the recommendation of plywood).
Next you need to apply glue along the edges of the pieces and position the magnets inside it. You can glue them in place but I used zip ties and before my recent repair I had elastic bands looped around and secured with a piece of kebab skewer. I haven't secured the magnet on the bottom as it isn't necessary and I don't have cut-outs in the base.
Finally you need to put one of your thin strips into position making especially sure that it secured centrally. I also made sure that instead of getting a symmetrical join as with the rest of the frame it is inside the top and bottom pieces so it is held more securely.
Step 4: Attaching the Rotor in the Casing:
For this step you must start by sticking the strip you have remaining onto one of the bearings of your rotor making sure it is very well adhered.
After this you can slide in your rotor so that the shaft goes through the strip already attached to the casing. You must now test that the rotor can spin freely as it can be a faff to fix this once you have the rotor installed.
If your rotor rotates freely you can then attach the bearing to the strip in the casing with plenty of glue. and then attach the strip on the other bearing to the other end of the casing. Your rotor should now spin freely within the casing.
Step 5: Adding Brushes:
The brushes of your motor are arguably the most important part of it and are definitely one of the hardest components to make.
First you need to make sure you have the connections from the copper coils you threaded through the bearing (and that the bearing you threaded them through has a longish length of shaft on the other side of it) and that they aren't making contact with one another you then need to make sure they are folded up and place double sided tape over the length of shaft sticking out. You then fold the connections down onto the double sided tape and cut three pieces of copper foil of the length of the shaft past the bearing and the diameter of the shaft (this is because you need three pieces of foil and a small gap between them and pi is about 3.141592654). You should now put the pieces of foil on top of the connections and wrap tape around both ends to keep it stuck down. Test these by touching any two of the pieces of copper foil with batteries (I would use at least 6v for this). You should ideally have the rotor turning slightly and/or blue/green sparks. But you have probably done something wrong if you get yellow/red sparks.
To make the brushes attached to the casing you need to first layer your copper foil to make it stiffer (my recommendation would be four layers but make sure it flexes but will spring back to the previous position). I then stuck a distorted tetrahedron onto the strip to give me a stiff mount for my brush and repeated on the other side sticking the brush along it. I then stuck a length of skewer down the back of the copper brush and stuck it to the other side on the skewer the brush is attached to.
Step 6: Operating and Conclusion:
The Motor that I have made can work from a minimum of 6v but I find 15v+ works very well (the highest voltage I've run it off is 25.5v as I was limited by battery constraints).
A few things I've added to my motor that you may want to are glue on the zip-ties to avoid scratches, some masking tape around the copper coils so they don't come off, I also bent a tip of the brushes onto the strip of wood so that it is easier to attach crocodile clips and a bead of hot glue around the base as when it speeds up it can shake a bit (a lot) with high voltages and tends to rattle glass and other items if you are using it on a table.
I hope that you enjoyed this instructable and that it has been of as much use to you as it was to me by helping me win my school's science fair without expending too much time and energy.
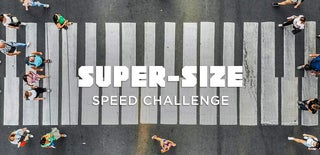
Participated in the
Super-Size Speed Challenge