Introduction: Giant CFL Light
This project stems from my love of the bare-bulb trend in home decor and my love of oversized things. The result is almost a caricature of a lamp. I really love the look and lines of regular or Edison-bulbs, as do a lot of people, and I think it is interesting to see the development of more environmentally friendly lighting trying to mimic this. One of the main inspirations for this project are the well-known Plumen bulbs, that managed to make CFL bulbs stylish. Only, I wish they came in XL-sizes!
For this project I relied on my 3D printer, because it allowed me to create the exact look I wanted, but at the end of this instructable I have some suggestions to recreate the look without a 3D printer.
Step 1: Materials and Tools
Initially I planned on using EL wire for the CFL tubes, since it is a continuous light similar to CFL's. However, they don't seem to sell EL wire thicker than 5 mm diameter, which would look out of proportion for the size I wanted. So my next plan was to feed the EL wire through 3D printed tubes. Unfortunately, the end result was not bright enough to be distinguishable if there was any other light around, however in the dark it looked pretty good. I did want something a little brighter so I chose to use LED strips instead, but for use in a darker surrounding I would suggest using the ultra-bright EL wire (in the image the EL wire looks much brighter than in reality).
I used the following materials:
- white PLA filament
- black PLA filament
- appr. 1.75 m led-strips with connector (I bought a plug-and-play set), at least 60 LEDs/meter, 12V
- cord or wire for hanging the lamp
Additional tools:
- (access to) a 3D printer (or check out the suggestions at the end of the Instructable)
- hot glue gun (optional)
- string
- safety pin
- strong magnet
Step 2: About the Design
All parts were designed to fit in the build volume of my 3D printer (Ultimaker 2+), so they don't exceed approximately 20x20x20 cm.
I played around a lot with the design of the tubes. There are many possible options! The design that I went for has two identical tubes rotated 180 degrees from each other, although having two different ones is certainly also possible.
I wanted them to be interlocking, so they "spiral" around each other. Of course, there are lots of designs possible. I think it would look great to cluster a couple of the oversized bulbs with different designs of the tubes. It should be fairly easy to create custom designs that fit in the base I created, they are created in Solidworks by sweeping a circle of 14.90 mm outer diameter and 1 mm thickness.
The base consists of an upper part and a lower part connected by screw thread. The lower part is used to feed the light strips through, while the upper part houses the wiring. By using screw thread all the electronics are hidden and can easily be accessed.
Step 3: 3D Printing the Parts
I've attached the stl-files of the parts that should be 3D printed:
- base_top (1x)
- base_bottom (1x)
- tube (2x)
The two base parts are printed in black PLA, but any color would work. They are easy to print, I used the following print settings:
- layer thickness: 0.1 mm
- wall thickness: 0.8 mm
- no supports, no raft
The screw thread has a tolerance of +/- 1 mm, this should be sufficient for most printers, but it will depend on the printer. After printing, carefully screw the parts together, if they get stuck go back and forth a little. If that doesn't help try sanding it a little more.
The tubes where a bit harder to print than the base, since they have to be hollow tubes that curve in two directions. I tried a few different ways to get the best results, including printing them in one go and printing them in different pieces. Printing them in different pieces creates very visible 'seams' when shining a light through them, so I wouldn't recommend it. The color of the filament should be white, since this is just translucent enough to let light shine through. A translucent (colored) filament might work as well and give a cool effect, but it would also show the LED-strips on the inside.
I printed the tubes in white PLA with the following settings, the screen shot shows the best position to print them in:
- layer thickness: 0.1 mm
- wall thickness: 0.8 mm
- supports (touching buildplate): the round tube is self-supporting so internal supports are not necessary. I am a fan of Cura's experimental 'tree support' setting, which takes much less time to print and is easier to remove.
- brim/raft
This means the support material had to be removed. After thorough sanding it is still al little noticeable, but not as bad as having seams.
Step 4: Preparing the Light Source
Depending on your preferences, you can use EL wire or LED strips. At first I was planning to use EL wire to get a continuous light strip, which fits the 'CFL like' look. Unfortunately the regular EL wire that I got didn't give enough light to really penetrate the tubes I printed. Only in a completely dark environment was it visible. In addition, EL wire tends to make a high pitched beeping noise, which can be annoying as a light source. This is why I chose to use LED strips instead, but if you prefer EL wire I would suggest getting the brightest option.
The LED strip I used was warm white, which gave enough light to be visible through the tubes. The first strip I tried had 30 LEDs per meter, but since there is little room for the LEDs to diffuse they show up as individual dots. Therefore, I would recommend getting at least 60 LEDs per meter, or even 120, which is what I used.
LEDs shouldn't heat up much, but in this design there is very little cooling. In that case, according to the instructions of the LED set I got, do not leave them on longer than 8 hours in order not to shorten the lifespan. They shouldn't build up enough heat to melt or damage the plastic (PLA only softens at around 90 degrees C, while LEDs shouldn't reach a temperature higher than 50 degrees C). Still, use with caution and don't leave them on unattended.
The LED strip I got was plug and play, so it was very easy to connect. If you are building your own set, remember to first feed the cable through the hole in the top of the base.
Step 5: Assembling the CFL Light
With a plug and play LED strip, assembling is pretty easy. The most difficult part is feeding the LED strip through the tubes. I've uploaded a scheme showing how to insert it.
First, take the base, and insert the tip of the LED strip through. The end with the connector should stay inside the base. Now the strip needs to be fed through the first tube. To make this easier, get a regular piece of string longer than the total tube length, and attach a safety pin on one side. Attach the other side with a safety pin to the LED strip (in the backing). Using a strong magnet from the outside, pull the first safety pin and the string all the way through the first tube. Pull carefully so the LED strip follows. Feed it back into the second hole of the base. Press the tube carefully into the holes in the base so it is attached.
Then make a loop (not to tight) and feed the LED strip back out though the third hole, and into the second tube. Make sure that the second tube is already in the correct position, so intertwined with the first tube. Use the same strategy to feed the LED strip all the way through and into the final hole in the base. Cut to the correct size.
Connect the LED strip as indicated by the manufacturer through the top part of the base. Any excess wiring can be hidden in this part. Take the robe or cord from which to hang the CFL, make a knot in one end and feed the other end through the top hole. Screw the top half on the bottom half. In case the tubes are not connected securely enough, use some hot glue from the inside to secure them.
Hang the CLF bulb in a nice location and enjoy!
Step 6: Other Designs
I think it would look great to cluster a bunch of these oversized CFLs with different designs. Since I had a lot of fun designing the tubes, I added some other designs I came up with that I haven't made yet. If you make one, please share a photo!
Step 7: Recreate the Look
Although using a 3D printer would be most convenient, it may be possible to create a similar look without it. For the base, a lot of easily accessible materials could be possible, such as cardboard tubes, metal cans or plastic bottles. Paint them to get a uniform look. For the tubing, my initial idea was only using EL-wire, which will look different but could also be cool. Another suggestion would be to use flexible tubing, for instance used for electronics, and bending them into the desired design.
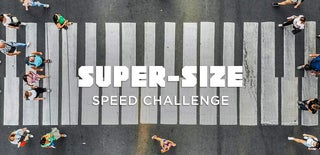
First Prize in the
Super-Size Speed Challenge