Introduction: Giant Wooden Pad Lock and Key
So this build is in my hit list for around 1 year and I am so desperate to build this lock. But somehow I kept busy in my other task and forget this. But when I always saw my old key hanger it always reminds me to build it. So my initial plan was to build a lock and over it, I am going to hang my keys. But I like the design so much that in the end, I decided not to drill any hole to mount my keys and made a separate key hanger which is a giant key just to fulfil my task. Overall said I am pretty happy with how this thing came out and it's really a very eye-catching item in my home. I installed it at the entrance and whenever someone comes he can't stop without asking any question. This is a completely inspired build from other makers and I watched a bunch of images over Pinterest for the inspiration. I am not the original inventor of this type of lock, Tim Detweiler is the founder of this wooden lock. The files I made didn't tell the exact dimensions because I just made it by eyeballing but it makes the job done. If you have any suggestions please let me know, so that I can improve my skill.
Supplies
Material and tool used.
Here is the list of material I used to make these lock and key
1. Teak wood 1" thick
2. Wenge wood 1⁄2" thick
3. Pinewood
4. Wood glue
5. Epoxy resin
6. Wood Stain
7. Linseed oil
8. Stainless steel pipes 1⁄2" and 3⁄4"
9. Wood screw
Tools used
1. Jigsaw
2. Scroll saw
3. Drill machine
4. Hand planer
5. Orbital sander
6. Chisel
7. Files
8. Drill bit
9. Hole saw
10. Spade bit
11. Clamps
12. Carving knife
Step 1: Material Cutting
The wood I am using is teak wood which is 1" thick and I specially bought for this. Since the wood is cut from the bandsaw so that's why there are bandsaw marks over it and before cutting it I decided to plane down the wood. At first, I thought that it's good to use a plane it first and then cut but surely with hand planing it's not a good idea. The problem is that the hand planner took reference from the wood and if there is too much bow in the wood then it would be needed lot more of work to do, also when you needed small pieces then it's good to cut the wood first and then plane it. By doing that you can also able to save the material. For the main outer body, my plan was to use a double-contrast wood and I have a piece of wenge wood so I use that. To cut down the material I uses a jigsaw and being an irregular material I recommend never to user tables are unless you have a crosscut sledge. if you are like me and have a very limited to and using a hand plane to plane down the wood then make sure to check the blade regularly because during the hand planning the Blade gets dull pretty fast when you have rough cut lumber or either spend some money on a good material blade that will surely save your a lot of time
So the body of the padlock is divided into three layers. The top layer and the bottom layer is made with two different kinds of wood glued together and the total thickness is 38 millimetre. The middle portion of the padlock in which the mechanism needed to be fitted that is going to be 44 millimetres in thickness. The overall dimension of this padlock is around 12" in width and 16" in height.
Step 2: Glueing the Wood and Template
For glowing the wood I used PVA glue. After spreading the glue I decided to climb it so that if there are any visible ups and down left then with the help of clamping force I am able to close those gaps. What's the glue is completely cured I stick the template on to the peace accordingly but here I use the regular wood glue and I surely not recommend you using a wood glue to stick the templates onto the wood. The problem with wood glue is that it gets absorbed by the wood fibres and when you are going to remove the the template then it would be extremely difficult to do that especially when you already spent a lot of time to do the hand planning of the wood. To do the maximum utilisation of the wood I cut the pieces quite close to the required dimension so I have to pay much attention to stick those templates but I highly recommend to leave and extra material when you have to to use template to cut down your material.
Step 3: Cutting the Material According to the Template
So to cut down that material if you don't have scrolls are then you can surely do it with the help of a jigsaw, that will also give you a better result. But I recommend you to use fine teeth blade on to the jigsaw because wenge I would easily get chipped away so you need to take extra care for that. In my case, I use my trusty scroll saw. The advantage is that you can cut down your PC is quite precisely but since the Blade thickness wasn't too much that's why you need to move slowly. But with the scroll saw you need to do less work. I cut down both front and backplate with it. Also I cut down the middle portion as well. The hollowed-out area from the middle portion I use it to make the leaver of the lock since it remains in the inside, both have same thickness.
Step 4: Sanding and Cleaning
For sanding, I use a Velcro pad in a grinder and use it to remove the rough surface from the workpiece. The grinder I am using is a variable speed grinder and running at slow speed so do not perform it with your regular grinder that would be dangerous. Also if you are going to send down the wood then the material removal rate it is much better at a slow speed as compared to a fast because in fast speed instead of removing the material the sandpaper burns the wood rather than removing the material. For some of the areas, I need to use files wrapped with sandpaper and use it to smooth out the inside area of the lock.
Step 5: Making the Latch Bolt
making the latch bolt is pretty easy to work and for that, I use a piece of wood and stick the template over it. Then I cut it with the scroll saw. The smoothing process is done with the help of a block plane. So the main mechanism of the bolt is to lock down the shackle. The thickness is to be kept the same like the leaver. Both the thickness of leaver and the latch bolt is just kept slightly lower so that they didn't create much friction with the top and bottom plate, otherwise, it's pretty hard for the key to rotate the lever and move the latch bolt to open the lock. The one end of the latch bolt is pointed just in such a way that it can capture the shackle. There is also a slot made in the bolt to insert the spring. For the pointed end, its size is 1/3rd of the height but in thickness, it almost equals to the latch bolt body. The end is kept tapered so that there will be less material needed to be removed from the shackle.
Step 6: Making the Shackle
For the shackle, I glued the template and cut it onto the scroll saw. The shackle is like the semicircle but the one end is going straight rather than curved so that it can be easily entered or exit. Also, it kept straight so that it can accept the latch bolt. So once I cut down one piece I use the same to make the second half of the shackle. Now if you have a thicker wood no doubt you can do this with that. But since I have only 1" thick so I use two of them by glueing together. Once both the pieces of the shackles have been cut down I glued them and allow it to cure. from thereafter with the help of angle grinder I send it down the outer periphery e of the shackle. I also use hand file wrapped in sandpaper to smooth out the inside area of the shackle. With the help of flat chisel, I clean off the and where the latch Bolt it has to be entered. I wanted the shackle to be rounded so that's why I use a 3⁄4" round-over bit in a router to round off the shackle. This works extremely well, but be conscious while doing that. Make sure to take care of grain orientation otherwise the wood might get chipped away a or you may also get some kickback. rather than holding the wooden piece in the hand, I recommend you to clamp it down to the workbench and then do the routine work. Once it's done with the help of sandpapers I sanded down the shackle.
Step 7: Making a Keyway
For this, I follow the template and drill down two holes one is 25 millimetre and another whole is 12 millimetre although it's good to drill down the holes with the spade bit, I didn't have a 25ml spade bit so I use a step-down drill bit for that. So once the drilling operation has been completed throughout onto front side I remove the rest of the material onto my scroll saw. Photo decorative purposes with the help of hole saw I outlined the area I need to remove from the front plate and then with the help of router remove the inside area which has been marked with the help of hole saw. Then I made a layout of the circle onto a piece of wood equals to the size which I removed from the front plate. I cut it with the scroll saw because I didn't have the right size of hole saw for that. Then I mount it onto the drill press and make it completely round. I kept it slightly tight and then fitted it in the area with some light blow of mallet. Now I again have to make the keyway but now I just drill a hole so that I can insert my flush-trim bit and use it to remove that material. The bearing in the bit follows the path at the bottom and create the same size of keyway onto the new inlay piece. Along with that I also round of the front and backplate of the lock, as I did for the shackle. This process makes the entire lock looks smoother and soft. Be sure if you are using a hardwood pay some attention during the routing process because during this the grain orientation changes and the wood might get chipped away. Along with this, I sanded down the surface up to 150 grit with the orbital sander.
Step 8: Drilling the Holes
Drilling the holes is really the most crucial process in this. If you go a tiny bit here and there than you might get trouble. The first hole is kept under the key area and the second hole is to drill adjacent to it so that the lever can pivot at its axis. When the key gets entered through the keyhole and you rotate it then it rotates the lever that engages the latch bolt and opens the shackle. These are 12mm holes. These are not the through-hole, just at half the thickness. I also drill the holes in the lever so that it can pivot inside the pipe.
Step 9: Spring
Spring is the important part of this whole locking mechanism and to make it I use a thin piece of teak wood. The wood not needed to be too thick neither too thin. Too thick it's not going to provide spring action mechanism and too thin might not be able to retract the latch bolt to its place. So it's mandatory to make it with thin wood, I found that a 1/8" thick plywood also works best with it. I first insert the spring in the bottom cut of the middle portion and then measure how long I need it and then cut it onto the scroll saw.
Step 10: Gluing the Lock Frame Together
Once most of the work has been finished I start the glueing process. The frame has been glued with wood glue and to glue the pins I use two-part epoxy. With the help of clamps allow it to cure for a couple of hours. Along with this I also drill the hole in the shackle so that I can place it also to check whether all of this works or not. To drill the hole I approached from both sides to maintain a straight hole and also to avoid chipping. Then I laid it onto the lock and find a suitable place to drill the second hole. Although it was present in the template I forgot to mark the centre that's why I use this taping technique. I coloured the pipe which acts as a dowel and inserts it into the shackle while the shackle placed onto the lock bottom plate. Then I got the impression and drill that hole. Here one thing you should need to note down is that only the bottom and the middle plate is glued together leaving the third layer because that is going to be screwed to its place.
Step 11: Bolt Catcher
To measure how much I need to cut down into the shackle I measure the dimensions of the one tapered end of the latch bolt and transfer its dimensions over the shackle end and then drill down multiple holes and remove the excess material with the help of chisel. Now like the tapered tip of the latch bolt the cavity in the shackle cut straight and I have to check it multiple times whether it catches the bolt or not. But after a couple of try and error I finally able to succeed in getting the self catching action.
Step 12: Making the Decorative Rivit Head
For the rivet head, I hole saw some pieces of wood and then use my drill press to turn them into a semicircle. I hold the blank in the drill and with 60 grit sandpaper true the perimeter and make all the piece even. I drill a partial hole in that rivet head and glued screws with the help of two-part epoxy. On one side, I glued these heads directly.
Step 13: Making the Key
So here I made two different keys one which opens the lock and second I use to mount the keys. I provide the template for the keys. For the smaller ones, I made it in three different parts not necessary to do this at all. I want to utilize all the material that's why I go with it. I stick the template and uses a scroll saw to cut down the desired shape. For the middle portion of the key, I use a straight piece and use that. For the main key teeth, I use the pattern from the lock plate because the key head needs to be the exact size of that key cavity which I cut into the lock. Then with the help of pins and glue, I connect all the pieces together and it really works great. To make it looks more beautiful I use some epoxy mixed in the glow in dark pigment powder and then filled it in the scroll saw design area. And the whole thing really pops up a lot. Along with that I also made some decorative for the rings and I just cut them with the help of scroll saw and then smoothen them out on drill machine, trim router and sandpaper. Pretty weird stuff to do but its worked well.
Building a bigger key is an extremely simple and easy process. Since I didn't have enough teak wood left so I used leftover pine pieces and use them to make the key. I made a template of the key and glued it onto the wood and then cut it with the help of scroll saw. Now outside areas, you can easily able to cut with a jigsaw but for the inside decorative you need scroll saw. I slowly cut down outside periphery first and then drill the holes for the inside so that I can pierce the blade and start the cutting.
Step 14: Sanding and Finishing
Once all the things are ready I sanded everything up to 220 grit. I didn't felt necessary to go up to 320. Onto the bigger key, I use black charcoal stain to mimic the look of the lock. Then for the top, I use linseed oil to pop out the grains and seriously the wenge wood looks pretty dang good. I bought 1⁄2" board for the coaster set but uses little bit for this and this thing looks beautiful to me.
Step 15: Finally
The final product is in front of you. There I few things which can surely ease my work is either buying a pre paned wood but since those are way more expensive than the rough cut I decided to save money rather than time. If you have any suggestions feel free to post them.
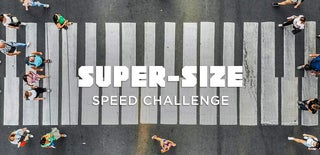
Participated in the
Super-Size Speed Challenge