Introduction: Glowing Thunderstruck Guitar
Introduction
Got a boring old guitar? Wish it had glowing lightning bolts in it? Then this is the Instructable for you.
This Instructable starts with a complete, finished guitar and details the process of burning in lichtenberg figures (the glowing veins that look like lightning), then filling them with a glowing resin.
Never heard of lichtenberg figures are? Watch the video!
SAFETY WARNING:
The electricity used in the production of lichtenberg figures is extremely dangerous andcan be lethal. Do not attempt this without sufficient knowledge of electrical safety. Even with the knowledge, it's necessary to be extremely careful to avoid touching live wires or conductive materials. Assume anything that is not thick, dry plastic (i.e. damp wood, any metal, any wire even with insulation), has live current running through it.
Note on Photos
There aren't photos of every single step for this exact guitar. For completeness in this Instructable, photos from several other projects are used throughout. So, don't be surprised if the shape of the guitar changes or the wood changes species from one picture to the next. The process remains more or less the same.
About the Author
Thunderstruck Studios specializes in custom vehicle conversions, handmade furniture, and daring projects. You can see more photos of this guitar and learn about our other endeavors on our website.
Step 1: Tools and Materials
Tools
- Micro screwdrivers
- Adjustable wrench
- Wire strippers
- Simple Multimeter
- Soldering iron + tin-free solder
- AC Transformer rated for 20 A @ 120 VAC
- Spray bottle
- Cabinet scrapers
- Belt sander with 80 grit sandpaper
- Finishing sander with 80 - 400 grit sandpaper
- Heat gun or blow torch with MAPP gas
- Brass brush
- Respirator mask with P100 filters
Materials
- Solid body guitar
- ArtResin Epoxy Resin or EcoPoxy UVPoxy Epoxy (about 16oz of either)
- Photoluminescent (glow) pigment powder
- Baking soda (Buy at any grocery store)
- Citristrip finish remover
- Painters tape
- Disposable 12oz plastic cups
- Disposable plastic knives
- Disposable gloves
- Shop towels
- Wood finish like Rubio Monocoat or Odies Oil
A couple notes:
> In general, these links are the actual tools and materials used in this build. They are not just random links from the internet but rather tried and tested equipment that is known to work well.
> This process can be done on a hollow body guitar, but the risk of damaging the guitar is significantly higher.
> The soldering iron linked is expensive at $60, but it's 100% worth it. I used a $10 iron for a few years before making the switch, and it makes soldering so much easier, cleaner, and more effective.
> The sandpaper linked with the finishing sander (3M Pro Grade) is more expensive, but worlds better than cheap sandpaper in terms of durability and clogging. Once you try it, you'll never go back to the cheap stuff.
> There is much cheaper epoxy resin available. The main downside is that it will significantly change from clear to a cloudy yellow over time. The more expensive brands are worth it if you want this to last.
> The most common places to source AC transformers inexpensively are from neon sign controllers and microwaves. If you go this route, be extremely careful during disassembly. In particular, be sure that all capacitors are discharged and there is no power source connected. If you're not sure what that means, you should learn before attempting disassembly.
Step 2: Transformer Setup
SAFETY WARNING PART 2:
Just in case you didn't read the warning in the introduction, the electrical power on either side of the transformer can kill you. If you're at all unsure of what you're doing, do not attempt this.
Transformer Setup
1. Disconnect all power sources
2. Wire the primary coil leads (thicker wire spool) to a standard 120 VAC male plug.
3. Wire the secondary, high voltage coil leads (thinner wire spool) to two long wires, about 5 feet long. The wires should be about 10 AWG to avoid excessive heat and stranded for flexibility.
4. Terminate the 5 foot long wires on the ends of long, non-conductive holders with a raw steel screw or similar. 1/2" PVC works pretty well for this. The holders should be 18-24" long.
5. Install a heat sink and fan to keep the transformer from overheating.
6. Electrically insulate all exposed wires and connections.
Step 3: Preparation for Burning
If you missed it in the introduction, there is more than one guitar pictured in this Instructable due to a lack of process pictures for the main guitar.
Preparation is key to achieving a successful finished product and avoiding any damage along the way.
Preparation for Burning
1. Disassemble and remove non-wood parts from the guitar. This includes pickups, knobs, wires, batteries, screws, brackets, and strings. Take pictures as you go to help when you forget where everything went.
2. Remove the finish using Citristrip and the card scraper(s).
3. Remove any residue from the finish or Citristrip.
4. Tape off any areas that you do not want to be burned on the guitar with painters tape.
5. Mix a solution of baking powder and water (approximately 1:20 by volume) in the spray bottle.
6. Thoroughly wet all wood parts to be burned using the spray bottle.
7. Wait at least 10 minutes, reapplying the baking soda solution as needed to keep the wood wet.
Step 4: Electrical Burning
SAFETY WARNING PART 3: SERIOUSLY, READ THIS!
Once again, the electrical power you're working with here can kill you. If you're at all unsure of what you're doing, do not attempt this. Remember that the high voltage will conduct through most things, including anything that gets wet during this process. If it's not plastic and perfectly dry, don't touch it!
Process
The process is pretty simple here: plug in the transformer, touch the leads of the high voltage coil to the wood in two different places, and watch it burn.
After you're satisfied with the burned patterns, unplug the transformer and move on to the next step. Watch out - the transformer and any wires connected to it will likely be screamin' hot for a while.
Step 5: Preparation for Resin
Follow these steps to get ready for the resin pour:
1. Let the burned ash dry completely. Even if it looks dry on the surface, there may be moisture underneath. This typically takes about 12 hours or more with cold or wet weather.
2. Carefully brush out all of the ash with the brass brush.
3. Remove any remaining ash from the surface. Anything left on the surface will discolor the resin.
4. If any wetness is still present, let it dry longer.
5. Tape the edges and any pockets. The idea is to create a barrier so that the resin will only go where you want it to. It will be roughly the viscosity of motor oil when pouring, so it will flow. Take your time here or you'll spend a lot of extra time sanding off excess resin.
Step 6: Resin
Time to pour some resin! The process is the same regardless of which brand you go with.
1. Lay out all of your materials: disposable cups, knives for stirring, pigment powder, shop towels to clean up any spills, and your heat gun or blow torch.
2. Put on some disposable gloves.
3. Mix the two parts (epoxy and hardener) in a disposable cup. This is typically a 1:1 mix by volume, by not always. Read the instructions on your resin to make sure.
4. Stir the resin mixture really well. About 6 minutes stirring by hand is a good guideline to follow.
5. Add a little bit of pigment at a time and mix it in. It's ok to leave it not well mixed; it adds some variation in the final color which adds depth to the look.
6. Pour the resin over the burned areas on the guitar. Be sure to add extra for any deep burns.
7. Go over the resin with the heat gun or blow torch to pop any air bubbles. Ideally you will do this every 10 minutes for the first hour.
8. If you haven't already, move the guitar to a clean (no dust), dry, level, warm place. Generally warmer is better for a faster resin cure - 100 deg F would be great, but a 70 degree room is fine.
9. Wait for the resin to cure. This depends on the temperature and poured resin thickness, but 48 hours is generally sufficient.
Step 7: Sanding and Finishing
Now for the worst part: sanding ='( The photos here show the guitar after sanding is completed then after finish is applied (i.e. there are no photos of the actual sanding process).
SAFETY WARNING PART 4:
Sanding resin is a pretty nasty business. You don't want to get it in your lungs as there are many known health effects. Some resin particles can be carcinogenic. I highly, highly recommend wearing the full-face respirator and filters linked in the Tools section.
Sanding
After the resin cures, you'll have a nice thick crust of hard resin. We have to do two things: remove the excess, then sand the surface smooth.
1. Start with the belt sander and 80 grit sandpaper to quickly remove excess resin. Be careful of the rapid material removal, as you don't want to sand away your nice lichtenberg figures.
2. Move on to 80 grit with the finishing sander. This will likely be the longest sanding step. It's crucial to remove all sanding marks from the belt sander at this step. Don't worry that the resin will be opaque at this point.
3. Progress through 120, 150, 220, 320, and 400 grit sandpaper with the finishing sander.
4. At each grit above 150, vacuum/wipe off any dust, apply clean water to all the wood surfaces, then let it dry. Repeat the same grit before moving on to the next one. This "water popping" raises the grain of the wood and results in a smoother finished surface.
Finishing
1. Decide on a finish. You generally get what you pay for here. The two linked finishes in the Materials section are expensive, but give a fantastic looking, durable oil finish with minimal work.
2. Apply the finish to the raw wood and resin. How you apply finish will depend on which finish you use.
3. Wait for the finish to fully dry or cure.
Step 8: Reassembly
Now that the wood and resin is finished, it's time to reassemble any parts you removed.
1. Reinstall pickups, knobs, brackets, and batteries.
2. If any wires had to be cut for disassembly, re-solder them now.
3. Reattach the strings.
4. Test that everything is working correctly by rippin' a quick riff or two.
Step 9: Finished Photos
All done! Now to take some photos of the finished product. Here are some tips:
> In order to maximize the glowing effect, place the guitar in direct, bright sunlight for several hours.
> Take photos of the glowing effect in a dim (not completely dark) room.
> Play with the light settings on your camera. As you can see from the photos here, different settings make for a completely different look.
Thanks for reading! If you had half as much fun reading this as I had writing it, then I had twice as much fun as you! If you'd like to learn more about Thunderstruck Studios, visit our website.
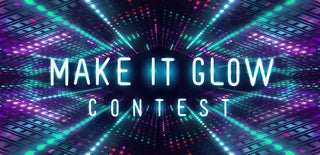
Second Prize in the
Make it Glow Contest 2018