Introduction: Great, Easy and Cheap Hose Repair for the Garden and Elsewhere
I have a big garden, with lots of hoses, and a big mower that all too often hits the hoses which then require repair. I have a lot of experience with different methods ( usually in the form of different connectors and clamps ) for repair. Pretty much all these involve a short tube that goes inside the two hose ends and 2 clamps that secure the ends. If you buy repair kits you typically get both parts, but you can often mix and match and/or make your own. The cheapest is to make both the clamps and the tube but you can choose to make just one or the other. The standard kits are easy to buy but are sometimes ridiculously expensive for what you get, shopping around can make a big difference. I have also found that making clamps results in a better repair than the purchased ones. This instructable tells you how to do a great job and at little expense.
Step 1: Getting Started
First inspect your hose and decide if it is worth repairing. Eventually a hose gets tired and fixing one break just results in a new one. If the break is near the end and the connector there can be easily moved you may want to just move the connector and shorten the hose a few feet. If you have a long hose with a break in the middle you may want two shorter hoses by adding a male and female pair at the break. In any case make sure you have located the break or hole and that there is not a another issue near it. Cut out the bad stuff, make the cut nice and square on the part you are keeping.
We use the usual hand tools here including screw driver, pliers, wire cutters, knife and similar. A plumbing torch is useful if you are working with well pipe or making your own connectors.
Supplies will depend somewhat on your approach, if you make the clamps you will need .041 stainless steel wire ( one source is Harbor Freight http://www.harborfreight.com/0041-inch-stainless-steel-lock-wire-1-lb-coil-8895.html ) and a clamp tool which you can make or buy. There are more details in the body of this instructable.
Step 2: The Repair Tube or Connector
This is is usually a rigid plastic or metal tube with barbs that help it grip the wall of the hose. It is inserted inside the hose on both ends and clamped. For best results the inner diameter of the tube should be as big as possible for good water flow, but if too big then you cannot get the hose around it. Tubes made for either of ½ and 5/8 hose are necessary a bit smaller than they need to be to fit a 1/2 hose. It is best if the part is made for your specific hose size. The connectors often come a part of a kit with clamps. Kits are a few dollars. Instead of the straight through connector you can add a new female connector on one piece a male one on the other and then screw them together. This turns one longer hose into two shorter hoses.
Step 3: Making a Connector
The cheap option for connectors: make your own. The following is for 5/8 inch hose, it might not fit ½ hose ( which in any case should generally be avoided because of its poor water caring capacity ) I do this by taking copper water pipe ( size ½ inside diameter ) and cutting off a section about 2.5 to 3.5 inches long. For a while I just used it as it was and made the clamp real tight. This works, sometime, and then only for a while; so do not do it. Next I simulated a barb, one on each end of the tube and this seems to do the job. Here is how: ( and please look at the pictures )
- Cut the water pipe ( a special wheeled cutter may be used for this, or just a hacksaw. Make sure the cut is fairly smooth, if not file, grind, or sand it.
- Clean the pipe so the bright copper shows, you only need do this at the two ends.
- Use copper wire ( of about 24 gauge wire, you can salvage wire from solid cat5 strands ) and wrap it three times around the pipe and twist off the ends. It should be nice and tight and lie in a nice flat layer.
- Paint with solder flux
- Solder ( I use a torch, I doubt a smaller tool would work )
- Cut off the pigtail twist in the wires.
- Grind or file off any lumps in the wire ( the end of the twist, a solder drop )
- When cool wash away the flux.
Step 4: Various Clamps
There are three types of clamps that I have used most often but have now discarded. I will cover them here as you may want to use them and not make your own.
- split plastic rings that are held together with 2 screws. The kits with these are often the cheapest ( they seem to be puny plastic, but I have rarely had one fail ).
- stainless steel bands with a built in screw to tighten them
- tabs that are attached to the tube and crimp down on the hose and tube.
At various time I have like one or the other best, but now I like making a wire clamp than any of the others; the clamp is just a modest length of .041 stainless steel wire that costs just a few cents. ( there is one catch here, you need a fairly expensive tool, the clamptite, for this type of clamp – the tool is well worth it, or you can make one )
To understand why this is such a good clamping method it helps to understand some of the limitations of the other clamps ( none of which apply to the wire clamp ):
- All of them are fairly expensive ( a dollar of more per pair ),
- All but the stainless steel bands must be the right size to work, and even the band is a bit messy if it is much oversize.
- All but the crimp make a sizable lump in the hose, if the stainless band is not wrapped in tape, the lump and end of the steel band can cut you when you slide the hose through your hand.
- All leak far to often, some may be fixed by tightening but sometimes this fails.
- The stainless band strips its threads far too often, then it is toast.
If you want to buy a kit best deals I have found on the web for the metal parts are https://www.plumbersstock.com/product/189008/orbit-56184-aluminum-repair-hose-mender/?gclid=CKKViO6Vp7YCFQjf4Aodgn4A6w and http://www.sprinklersystemstore.com/p-432-orbit-58-aluminum-water-hose-repair-kit-with-hose-clamps.aspx , you will find that shipping is going to add a large percentage to the prices on these pages.
Step 5: The Wire Clamp
With the wire clamp wire is wrapped really tightly around the hose, folded over on itself to hold its position ( this whole thing hardly enlarging the diameter of the hose ) and covered with electric tape.
- Inexpensive ( once you own or make the tool )
- Very tight, I have had no leaks so far, even on 100 psi air hoses
- One size wire fits large range of hoses
- Not bulky even after electrical tape -- this makes hose very easy to handle.
- Seems to work first time - every time.
- Useful for other types of repairs
Step 6: Tool for Making the Clamp
You have a few options here:
Buy It
There is a commercial tool for making the clamp called a ClampTite you can find it at: http://www.clamptitetools.com/ While it may seem a bit expensive I am very happy with my purchase.
A nice instructable on the tool can be found at Hose Clamp Magic by GeeDeeKay https://www.instructables.com/id/Hose-Clamp-Magic/
Make It
Make the tool, use one or both of these instructables.
Wire clamping tool ( DIY ) https://www.instructables.com/id/Wire-clamping-tool-DIY-/
Wire Clamp Tool by MartinMakes https://www.instructables.com/id/Wire-Clamp-Tool/
Or you can use some rivet tools as shown in this instructable.
Wire Hose Clamp by graydog111 https://www.instructables.com/id/Wire-Hose-Clamp/
Step 7: Making the Wire Clamp and Fixing the Hose
The clamp is made in place right on the hose so the process of making the clamp is part of the repair process. In this step I will just do one end of the connector, you need to repeat this for the other piece of tape unless you are putting on a male or female connection which needs only one clamp.
( you need the clamp tool like the clamptite, wire, wire cutters, pliers, pocket knife, tube from above, black electrical tape and some other misc materials mentioned in the text )
Cut the hose off clean and square. Then look into the hose. Some have a rib sticking up ( see the picture ). This rib will interfere with the joint and should be removed for an inch or so. I nick it with a razor knife and then pull it out with pliers.
Insert the repair tube, sometimes it resists there are a few aids: Lubricate it ( I use a bit of soap ). ( some hard plastic pipe like well pipe may benefit from a hit of heat from a torch ). I sometimes use a tool like the old pliers shown in the picture to expand the end of the hose an make it easier to get the connector in. Heating in hot water will soften many hoses without overheating or burning.
Pay particular attention to the pictures for the next step, the descriptions do not really stand on their own. You may also want to refer to the directions that come with the tool or the other instructables using the clamptite style tool.
Take the wire ( length 4 turns around the hose plus 12 inches ), fold in half and wrap the hose with it putting the two ends through the loop where it is folded over, your clamp now has 4 wraps of wire around the hose.
- Insert the tool the nose has a slot that fits into the loop of the wire and fasten the wire to the clamp as shown in the picture.
- Tighten the nut on the clamp, I make it almost as tight as I can with just my hands.
- Fold over the tool and wire you have pulled thru the loop.
- Loosen the nut, cut off the wire about ¼ inch after the loop.
- Press the wire ends down against the hose.
- Repeat for the other piece of hose.
Wrap the whole thing tightly in plastic electrical tape, this makes it smooth and protects you from the wires ends. I use black tape but you can get electrical tape in many colors if you want something special.
Step 8: Results and Final Thoughts
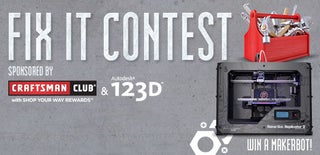
Participated in the
Fix It Contest