Introduction: Green Core XY : a 3D Printer With Recycled Components.
Hello, i am happy to present you my first instructable.
First, i am sorry if my English is bad, i learned English at school 15 years ago. I try my best.
I used a lot of tutorials and forums for having solutions or ideas but i never contribute. That is why i am happy to start my contribution with you.
My project is a 3D printer build with recycled components and cheap materials. This project started with my son when i started to learn him how recycling and fixing are important for his future and the earth. 3d printer is for me a formidable machine that can contribute for a responsible consummation. It can contribute to the development of imagination and is a good approach to mechanical, programming, electronics, engineering ...
My specifications :
- A compact design.
- Easy to move and use.
- The print area is 10 cm x 10 cm x 10 cm.
- Filament roll stored in the machine (250g spool).
- Compatible with regular nema17 steppers and GT2 belt.
- Modular head.
- The must important : use a maximum of scavenged components and 3d printed parts with PLA (biodegradable).
However, i don't want a poor machine, it must have good prints. So i had to buy some parts like bearings because i didn't find better solution. All parts i bought are cheap but do their job. I chose the coreXY arrangement because it corresponds to my specifications and it need only one motor for the Z axis.
The printer size is 26cm height, 26cm width and 24cm depth. I designed all the parts except the bowden extruder (by Schlotzz) that i customized and the clamp for linear bearings (by Dagoma).
As you can see in the picture the first user is my son. In the first photo you can see everything the machine printed (tests and fails comprise). The machine can print with 0.15mm resolution and the longer print i do was 3 hours (motors are very small so they heat faster than the classic nema 17).
Step 1: Bill of Materials :
- 2x nema 17 steppers with belts and bolts for XY axis (i found them in olds Espon C20 printers).
- 1x nema 17 stepper with bolts for z axis (Epson C20 printer).
- 1x nema 17 stepper (you can find strongest in big photocopier machine).
- 1x coupler 4x6.
- 1x 608zz bearing.
- 16x 623zz bearings (i recently found them in server's cooling fans).
- 8x LM8uu linear bearings.
- 1x pneumatic connector PC4.
- 1x driver gear.
- 1x e3dv6 hotend remote bowden 1.75 12v.
- 1x kit Arduino mega + Ramps 1.4 + 4x polulu 4988.
- 12V 5A power supply (i am trying to convert a computer power supply).
- 12V power jack plug.
- USB cables.
- 2x DVD drives (1 for the door).
- 1x endstop switch.
- 8mm linear shafts.
- 6mm threaded rod.
- Screws, bolts and nuts (M2, M3, M4 & M6).
- Springs (found in printer, machines).
- MDF or plywood offcuts.
- Plexyglass offcut.
- 12mm flexible tube (you can use PVC flexible cable pipe).
Step 2: Woodworking
I built the box with 10mm thickness MDF (but plywood is better because less toxic) and 3mm plexiglass for the door. I got it in a carpentry workshop, they are offcuts that they don't use because to small. I cut it with a circular saw. The door frame is cut with a wood router.
Sadly, i accidentally deleted photos i took during this step. however, with the dust and bad light they were not very exploitable. I apologize for this lack.
I used 25mm M3 screws.
You can choose to leave the wood apparent or to paint it. I finally painted mine with a white paint found in my garage.
Attachments
Step 3: Linear and Threaded Rod
Maybe the most sporty part of this instructable !
I picked up my linear rods from a demolition. I found in an old fax 6mm diameter linear shaft compatible with lm6uu bearings. You can modify the 3d files to adjust. The 3mm rod is in the DVD drive.
8mm diameter linear shaft (mine are not rectified but fortunately it works great) :
- 2x 225 mm (X axis)
- 2x 180 mm (Z axis)
- 2x 200 mm (Y axis)
6mm diameter threaded rods :
- 1x 135mm (Z axis)
3mm diameter linear rod (optional) :
- 2x 30mm (hinges)
Step 4: 3D Printing
Now it is time to use your 3d printer ! That is why I said this is a formidable machine. You can duplicate your printer, upgrade it, print mechanical elements ... but you need one to start this project. Maybe the 3d printer paradox ?
I used my 3D printer Discoeasy200 by Dagoma with Gracious green and black PLA Filaments by ICE and White Chromatik PLA Filament by Dagoma. The project need 220g of filament.
Print settings :
- Supports : no
- Resolution : 0.2 mm
- Infill : 20%
- Filament : PLA
All files are directly printable with the best orientation. I recommend you to start with the Test.stl file. Indeed, this part got all different assemblies present in the machine. It is a good way to verify if your printer is properly calibrated to don't make the mistake to print all parts for nothing.
Attachments
Test.stl
E3DV6 Holder.stl
E3DV6 Parts.stl
Extruder arm.stl
Extruder.stl
MB box.stl
MB rail.stl
MB Support.stl
Spool holder.stl
Wire hole.stl
X Carriage.stl
X Left.stl
X Right.stl
Y Back Left.stl
Y Back Right.stl
Y Front Left.stl
Y Front Right.stl
Z bottom.stl
Z carriage.stl
Z plate.stl
Z Top.stl
Z Endstop.stl
ZMotorSupport.stl
Door Parts.stl
Bed Knobs.stl
Wires clamps.stl
Cooling Parts.stl
Step 5: Stepper Motors
For my project I used 3 stepper motors scavenged in old Epson C20 printers. Generally, printers are thrown in the trash because print heads are clogged, however, all the other parts in the machine work well. You can scavenge stepper motor, M3 nuts and bolts, belt, linear shaft, springs, buttons ... Fortunately, in old Epson printers motor steppers are nema 17. Apparently in big photocopier machine like Ricoh you can fo1nd more powerful stepper.
To prepare steppers you need Dupont connectors, old USB cables and your soldering material. You need two motors with drive pulley and another without (Z axis).
Wires length :
- Stepper front right (with pulley) : 73 cm
- Stepper front left (with pulley) : 50 cm
- Stepper bottom Z : 23 cm
Your motors can be connected like this to your Ramps but I preferred make an intermediate cable for this reason : If you want to connect your motors to another motherboard you have to disconnect only a big Dupont connector instead of three (six with the endstops).
Step 6: End Stops
For this step I try to use 3 different components : two are found in the DVD drive and one is a classic end stop (old project). You need old USB cables and soldering materials.
Wires length :
- Classic end stop (Y) : 29 cm
- Button (X) : 51 cm
- Three foot switch (Z) : 32 cm
You will connect each end stop with a female Dupont double connector during the wiring step (after the pre assembling).
Like motors, these end stops can be directly connected to the ramps, but I preferred the solution for a big connector.
Notice I tried to use an LED with the three foot switch but i failed.
Step 7: Wiring
As i said all my wires are from old USB cables.
I chose to have an intermediate section of wires between the Ramps and the steppers/end stops. If i want to change the board i only have to disconnect the two big connectors. If you want to alternate the Arduino Mega and the Ramps with the Arduino Uno and the CNC shield it will be easier and fast.
However, you can directly connect the motors and the end stops to the Ramps. The extruder is directly connected with the Ramps.
To make the nodes i used sleeving heat shrink tube but, you can use tape or a hot glue gun.
Step 8: The Bed
Here is a special step for the bed. It is not hard, but i prefer separate this step for a better readability.
Take care to be sure that the M6 nut doesn't move. Use paper or tape to add thickness if needed. I used for the bed an aluminum panel cutoff, but you can use another strong material that doesn't curve. I suggest you to use Blue tape on the bed for a good adherence with the first layer.
Like the box I painted the wood in white.
Step 9: Pre Assembling
It is time to test your dexterity !
These assemblies are intuitive and quite repetitive. So if you pass the first element you will success the other.
Take care with the Z axis' motor, his shaft moves and it can cause troubleshoots during printing. That is why you have to pinch it with the coupler.
Notice that in the illustration some parts are not updated.
Step 10: Power Supply
The minimum needed is 12V 5A. I am not reassured that a machine works during 3 hours with a diy power supply, especially if my son is around ! That is why i use a power supply used for Christmas lighting. However, i am working to build a secure diy power supply from an old computer.
Be careful with electricity, it can burn your house and kill.
Step 11: Firmwares & Softwares
For software I use Repetier Host for this reason :
- It is free.
- It is easy to use.
- It can slice and pilot your printer.
- You can use Cura and Slic3r to slice.
- You can easily configure it for a CNC or a Laser.
- It is compatible with Marlin firmware.
If you want another solution you can use to slice Slic3r or Cura and to pilot Pronterface for example. They are free and have a big community.
You need to install Arduino IDE to transfer the firmware (Repetier or Marlin) in your Ramps.
I give you my Marlin and Repetier configurations they work both.
Step 12: Arduino Mega and Ramps 1.4
I chose these two elements because they are cheap, well known and if you get a problem, with luck you only have to change one of them. Nevertheless, when you are working on the Ramps be sure that there is no electricity
(12V or USB connection). Be careful and verify your connection before powering the shield. I did the mistake and I think i killed a component in the Arduino (my 5V outputs are 3V now). You have to plug stepper drivers to control the motors. I chose the pololu A4988. They are cheap and work well.
After plugging the jumpers and the pololu, attach the Arduino with the printed motherboard rail. Then plug the Ramps in the Arduino Mega. Depending your power supply you can like me, attach a 12V power jack plug.
We will verify the steppers :
- Dispose the motors like if they were in the box.
- Only plug the motors on the Ramps.
- Verify all then connect the motherboard to your computer.
- Power the Ramps.
- Launch Repetier Host and connect the printer.
- Go to the manual control.
- Test to go to the right, and look the motor's rotation.
- Compare with my schema. If one turn in the bad direction disconnects the printer, unplug the USB and power supply.
- Invert the connection of the motor on the ramps.
- Do it with the other motors (Z goes down).
Now it is time to adjust the steppers :
- You will do the following steps.
- test to go to the right.
- With an isolate screwdriver, slowly turn the little screw on the pololu in anticlockwise.
- test to go to the right.
- When the motor stop to work turn 1/4 in clockwise.
Do it with the other motors (Z goesdown).
This method looks archaic, but works for all steppers I used.
Step 13: Assembling
It is time to assemble all the parts before giving life to your printer.
Take care with the belts tension : the quality (regularity on the hight) of your prints depends a lot of this step.
Step 14: Calibration
Folow the instruction for the steppers steps per mm and the bed leveling.
Notice you can move the head with the software, or with the hand if you unpower the motors in the software (for the bed leveling).Personally i prefer the second solution.
After this step your printer is operational.
Step 15: Transformations
I designed this printer to be transformable in CNC, plotter or a Laser engraver.
You can disconnect the Ramps 1.4 and use a CNC shield, you can unplug the Hotend and plug another tool.
I tried with a motor with a drill bit, a dremel and a pen. That works !
Step 16: Conclusion
As you can hear it is quite noisy but i am always impressed to see it working ! Finnaly, we can consider this printer is built with 70% of scavenged parts. It is sad to see that many equipements are going to trash while there is generally only one element that is dead.
I hope you enjoy reading my first instructable. It is a hard work, but i am happy to share it. I will update this instructable. Tell me if there is something wrong.
Thank you.
Rémy
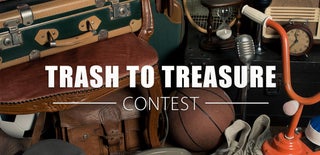
Participated in the
Trash to Treasure