Introduction: Growing More Lettuce in Less Space Or... Growing Lettuce in Space, (More or Less).
This is a professional submission to the Growing Beyond Earth, Maker Contest, submitted through Instructables.
I could not be more excited to be designing for space crop production and posting my first Instructable.
To start, the contest asked us to..
“...submit an Instructable detailing the design and build of your plant growth chamber which (1) fits within a 50cm x 50cm x 50cm volume, (2) contains all the features necessary to sustain plant growth, i.e. artificial light, an irrigation system, and means of circulating air, and (3) makes effective and inventive use of the interior volume in order to fit and successfully grow as many plants as possible.”
After reading the contest requirements and FAQ's, I made the following assumptions in the design process.
Once weekly planned interaction with “the project” by an Astronaut would be acceptable and not void the automatic control aspect in the contest criteria.
The PSU for “the project” can be housed outside the 50cm3, as the ISS would supply power to the unit, if the unit were in space. Cooling for the LED's inside “the project” can originate outside the 50cm3, as the ISS can supply cooling to the unit, if the unit were in space.
“User” can have unrestricted access to top and 4 sides of the 50cm3 volume for the planned weekly maintenance, but not exclude unplanned issues, should an unplanned issue arise with “the project”.
Next, I gathered the parameters for the contest
Project Data
Water: 100 mL/plant/day (suggested)
Lighting: 300-400 𝜇mol/M2/s within PAR 400-700nm (suggested)
Light cycle: 12/12
Light type: LED (suggested)
Air circulation: for 2.35cf/0.0665m3 (my design's growth area)
Temperature on ISS: 65 to 80˚F / 18.3 to 26.7°C (for reference)
Type of plant: ‘Outredgeous’ Red Romaine lettuce
Mature plant size: 15cm high and 15cm in diameter
Grow system: (Designer's choice)
Supplies
We're going to need supplies!
(These parts are used for proof of concept, they probably are NOT space travel approved)
1 – 0.187” 48”x96” White ABS
3 – Micro controllers
1 – 1602 LCD display
1 – Data Logger shield for Nano
3 – Photo resistors
4 – AM2302 sensors
1 – DS18B20 temperature sensor
1 – EC sensor,
1 – 15mA 5V Optical Liquid Level
1 – DS3231 for Pi (RTC)
...and more supplies
1 – Peristaltic dosing pump
1 – 12V water pump
1 – Piezo buzzers
3 – 220 Ohm resisters
1 – DPST switch
1 – 265-275nm UVC Sterilizer
24 – 1½” sanitary caps
1 – Liquid/Air magnetic stirring stage
1 – Drip control head, 8 line
1 – Drip irrigation tubing
1 – Replacement water container
1 – ½ ID PVC pipe
70 – Screws for attaching LEDs
18 AWG & 22 AWG Wire
1 – Shrink tubing
1 – Aluminum for LED heat sink
5 – 6mm tall tactile switches
4 – 1 Ohm, 1 Watt resistors
1 – Pkg seeds “Outredgeous” lettuce
...and more
1 – 400W Boost board
32 – 3W White LEDs, (6000-6500k)
1 – 24V / 12V / 5V / 3.3V PSU
8 – 40mm computer fans
11 – 5V Opto isolated relays
10 – 1N4007 flyback diode
24 – Rockwool plugs
1 – Hydroponic nutrients
1 – Nutrient container
1 – Mylar sheeting
...and tools
Solvent for gluing
Saw
Hole saws
Soldering iron
Solder
Drill
Drill bits
Screwdrivers
Computer
USB cable
Arduino IDE software
Step 1: Comparing the Current “VEGGIE” System
The “VEGGIE” system on ISS can grows 6 heads of lettuce in 28 day (4 weeks). If “VEGGIE” ran for 6 months, (the average time an astronaut is on board the ISS) it would grow 36 heads of lettuce with an additional 6 heads that were two weeks old. For a crew of 3, that's fresh veggies twice a month.
The GARTH Project will grow 6 heads of lettuce in 28 days (4 weeks). BUT.. if it ran for 6 months, it would grow 138 heads of lettuce, with an additional 18 heads in various stages of growth. For a crew of 3, that's fresh veggies 7½ times a month, or almost twice a week.
If that grabs your attention... let's take a closer look at the design
Step 2: The GARTH Project
Growth Automation Resource Technology for Horticulture
(Photos of the GARTH Project are of a full scale mock-up, made from Dollar Store foam core board)
The GARTH Project maximizes productivity through the use of 4 separate optimized growth areas. It also includes automatic control systems for lighting, air quality, water quality and water replacement.
32, White 6000K LED lights provide the suggested PAR requirements. A two fan air circulation system and a four fan vent system were incorporated to maintain the interior environment, and an automated, self optimizing Nutrient Thin Film (NTF) hydroponic system was chosen to feed and monitor the plants. Evaporation replacement water is held in a separate reservoir in the upper storage area near a constantly stirred liquid nutrient reservoir, needed to maintain the nutrient level in the hydroponic system with out assistance from an astronaut. All power enters, operates and is distributed from the upper storage area.
Step 3: Design Features
The four growth areas
1st Stage (germination), for 0-1 week old seeds, approx 750 cc of growth space
2nd Stage, for 1-2 week old plants, approx 3,600 cc of growth space
3rd Stage, for 2-3 week old plants, approx 11,000 cc of growth space
4th Stage, for 3-4 week old plants, approx 45,000 cc of growth space
(The 1st and 2nd Stage areas are combined on a removable tray to facilitate planting, servicing and cleaning)
Step 4: Lighting System
Lighting was tough without access to a PAR meter, fortunately the contest had Mr. Dewitt at Fairchild Tropical Botanic Garden, to go to with questions. He directed me to charts that were very helpful and those charts also lead me to led.linear1. With the charts and the website, I was able to calculate my lighting and circuitry needs.
My design uses 26.4V of source voltage to run 4 arrays of 8, 3 watt LEDs in series with 1 ohm, 1 watt resistors. I will use a 24V supply and a Boost converter to raise the constant current to the 26.4V. (On board the ISS, my design would use the 27V which is available and a Buck converter to lower the voltage and provide the constant current of 26.4V)
This is the parts list for the lighting system.
32, White 6000-6500k, 600mA, DC 3V–3.4V, 3W LEDs
4, 1 ohm – 1W resistors
1, 12A 400W Boost converter
1, 40mm fan
1, thermistor
1, DS3231 for Pi (RTC) or datalogger
18 AWG wire
...and this is how I plan to use those thirty-two, 3W LEDs.
One LED in Stage 1, four in Stage 2 and nine in Stage 3. The last eighteen LEDs will light Stage 4 and bring us to a whopping total of 96 watts of light at approximately 2.4 amps.
Step 5: Air Circulation and Venting System
(Please remember the plumbing and electrical wiring is not complete. These are photos of a mock-up of the proposed system)
Circulation is achieved with two 40mm fans. A push fan that blows into the 4th Stage from the duct at the upper left rear. The air will flow across the 4th Stage and into the front of the 3rd Stage, then through the 3rd Stage and out the rear (up and around the 1st Stage, via a short duct) into the rear of the 2nd Stage. A pull fan in the duct above the 2nd Stage, will draw the air through the 2nd Stage and out the right front top corner. Completing the journey through the air circulation system.
The 4th Stage venting will be directly out the upper rear wall. The 3rd Stage will vent through it's upper rear wall as well. The 2nd Stage will be vented straight through the top and the germination Stage (Stage 1) will vent out the rear wall, similar to Stages 3 and 4.
Step 6: NFT Hydroponic System
(The EC probe, temperature probe, liquid level sensor, hoses for evaporation replacement from freshwater reservoir and hoses connecting the sump pump to the channels, all will be located here in the sump but were not shown in this photo)
The system includes a 9,000+ml/cc sump, a 7,000+ml//cc freshwater reservoir for evaporation replacement, a 12V 800L/hour water pump, a UV-C sterilizer to kill any algae in the water entering the 8 port adjustable flow manifold, an aeration tower with opposing flow fan to aerate the down flowing water from Stage 2 and stirring stage exhaust water, a liquid level sensor, an EC sensor, a water temperature sensor, a peristaltic pump dosing from the nutrient reservoir, a stirring stage that keeps the nutrients in solution in the reservoir and five growth troughs or channels. The five growth channels, the stirring stage, the aeration tower receive water from the 8 port adjustable flow manifold.
When the hydroponic system needs to be serviced, a double pole single throw (DPST) cutoff switch located on the front panel will shut the power off to the water pump, UV-C sterilizer and peristaltic pump nutrient doser. This will allow the "User" to safely work on the hydroponic system without endangering themselves or the crop.
Step 7: Automatic Nutrient Delivery System
I'm using the “Self Optimizing Automated Arduino Nutrient Doser” developed by Michael Ratcliffe for this project. I've adapted his sketch to my system and hardware and I'm utilizing Michael's “Three Dollar EC – PPM Meter” as my EC sensor.
Information or instruction for both of these projects can be found at: element14, hackaday or michaelratcliffe
Step 8: The Electronics of the Automation Systems
The Lighting system will use an Arduino micro controller, one DS3231 for Pi (RTC), one 4 relay module, four 1 ohm – 1 watt resistors, thirty-two 3W White LED's, one 400W Boost converter, three photo resistors, one 40mm computer fan and one thermistor. The micro controller will use the RTC to time the lights in a 12 hour on, 12 hour off cycle. It will monitor the light levels in the 2nd, 3rd and 4th stages with photo resistors and alert with an LED/piezo alarm, if it detects a low light level in any stage, during a lights on cycle. The temperature of the LED driver board will be monitored by a thermistor connected in line to the 40mm fan and will automatically start cooling when enough heat is detected.
The Nutrient Delivery system was developed by Michael Ratcliffe. The system uses an Arduino Mega, one of Michael's EC probe ideas, one 1602 LCD keypad display shield, one DS18B20 water temperature sensor, one 12V peristaltic dosing pump and one 5V opto isolated relay. I added one optical liquid level sensor. The system will monitor the EC and water temperature and activate the peristaltic pump to dose nutrients as needed. The micro controller will monitor the water level in the sump and alert with an LED/piezo alarm if the water temperature of the sump is beyond the user set range, if the EC sensor data is beyond the user set range for longer than the user set period of time or if the water level of the sump drops below the user set level.
The Air Circulation system will consist of an Arduino microcontroller, four AM2302 sensors, six 40mm computer fans (two air circulation fans for the 2nd, 3rd and 4th Stages and 4 vent fans), one UV-C sterilizer and six 5V opto isolated relays (for the fans). The controller will monitor the air temperature and humidity in all 4 Stages and automatically start the two fan circulation system or the individual stage vent fans as needed to keep the temperature and humidity within the user set ranges. The controller will also set and control the UV-C sterilizer timing and maintain an LED/piezo alarm in case the temperature or humidity go beyond the user set levels in any of the 4 Stages.
Step 9: The Build
The 50 cm3 case, the channels, the freshwater evaporation replacement reservoir, the aeration tower, the central air circulation duct, the 1st & 2nd Stage drawer, the roof braces (not shown) and most other supporting structure, will be built from 0.187” Black ABS. The front curtains for the stages are shown in Mylar film on the mock up, but would most likely be made from reflective coated acrylic or polycarbonate on the actual prototype. The lighting (not shown but consisting of 4 arrays of 8, 3W LEDs in series) will be mounted on approximately 0.125” aluminum sheeting with 0.125" copper tubing soldered on top side for liquid cooling, (that cooling would enter and exit from the back of the unit to separate non-contest related cooler). Plumbing of NTF water to Stage 1 & 2 (is not shown in any of the photos but) would attached via a quick connect at the front of the 2nd Stage.
The boost converter (shown in the photo of the top storage area) may be relocated underneath the germination tray (Stage 1) to provide additional heat for germination. The AM2302, temperature and humidity sensors (not shown), will be located high in each Stage (out of the regularly planned air circulation path)
The design may appear to not be thinking about space at all,
but that is not the case. My NTF system described here is not optimized or modified for space, but NTF hydroponic systems are serious contenders for the unique needs of space crops in microgravity and I do have ideas for it's space optimization.
The contest asked us to design a system that grew more plants in a defined space and automate the design as much as possible.
The designs selected for Phase 2 will need to grow plants her on earth first. I believe my design fulfills all the requirements of the contest and does it while respecting the true space needed for plant growth, air circulation, automated environmental controls and a weeks worth of consumables for the plants. All within the 50 cm3 space we were given.
Step 10: To Wrap It Up
The automation of The GARTH Project reduces needed attention to once a week.
A seven fold decrease in maintenance, compared to the "VEGGIE" system.
Six plants started weekly in The GARTH Project.
A four fold increase in production, compared to six plant started monthly in The “VEGGIE”system.
I consider these changes Effective, Inventive and Efficient.
I hope you will too.
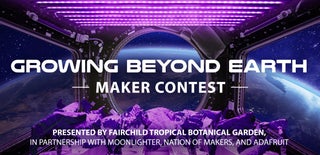
Runner Up in the
Growing Beyond Earth Maker Contest