Introduction: HDPE Pocket Knife
A pocket knife is a handy tool, how many times have you needed to cut something and didn't have a knife on you? Too many times I'd say. So why not make one out of plastics you have laying around. Cleaning up the environment while making a handy tool.
I have provided the 3D printable or JPEG file if you would like to print the outline template.
Supplies
- Oven
- 2 Flat Pieces of Glass
- Sandpaper
- Scissor
- Stencle Knife
- Pencil
- Marker
- Screwdriver
- Sandpaper
- Soldering Iron
- Pliers
- Drill
- Dremel
- Spray Paint
Materiels
- HDPE Plastic Bottles
- 3 Screws
- Metal Rod
- Metal/Plastic Fine Mesh
Step 1: Preparing Plastics
I started by removing all the labels and wash and rinsing the bottles thoroughly. The plastics used are HDPC plastics which are used to make a variety of bottles.
Step 2: Outlining Blade
Once the bottle has dried, I outlined the blade using the template. You can use the template provided to make your own or create a new template if you would like to create a different or larger blade.
Using the marker, outline the blade on the plastic bottle. Repeat this step at least 3 times. The more layers you use the thicker and stronger your blade will be.
Step 3: Cutting Out the Layers
Once you have outlined the layers, use your stencil knife or scissors to cut out the blade outlines. I used 3 layers to create my blade.
Step 4: Trimming Layers
Once I had the layers cut from the bottle, I used the scissors to trim the edges to get all 3 layers more evenly symmetrical. Cutting along the outlines and removing any rough edges.
Step 5: Sanding Blade Layers
Using rough grade sandpaper, 120 or lower. Sand both sides of the layers to remove the smooth surface.
Step 6: Outlining Mesh
I used mesh layers between the plastic layers for the blade to improve strength and rigidity. Using the marker to outline the template onto the mesh.
Step 7: Cutting Mesh Layers
Use the scissors to cut out the mesh layer. You can use metal or plastic mesh however, metal mesh is recommended.
Step 8: Stacking Layers
When stacking the layers, the mesh layers should always be between the plastic layers. Start with a plastic layer, add a mesh layer, then another plastic layer, then a mesh layer, then a plastic layer and so on. Finish off with a plastic layer. Once complete, you should have a plastic layer visible on both sides.
Step 9: Marking Out Handle
We will need to repeat the steps for marking and cutting out the blade for the handle as well. Place your template on the bottle, and outline with your marker. I used 3 layers for each side of the handle, so a total of 6 layers were needed. For a thicker handle, more layers can be used.
Step 10: Cutting Out Handle Layers
Cutting out the layers for the handle will be the same process as used to remove the layers for the blade. Use a stencil blade or scissors to cut around the outline. Once the layers are cut from the bottle, trim the layers down and remove any rough edges with the scissors.
Step 11: Sanding Handle Layers
Sand the layers for the handle using sandpaper, 120 grit or lower to remove any smooth finish.
Step 12: Stacking All Layers
I stack the layers for the handle, 3 for each side. I did not use any mesh support in the handles as the additional strength was not needed.
Step 13: Loop Support Layer
Using your stencil knife, cut the bottom from one of the bottles then cut it in half to create 2 layers. This will be used to sculpt the end of the knife and allow you to attach it to a key chain.
Step 14: Preparing for Heat Treatment
Stack all the layers evenly atop each other for the respective parts that they will be sculpted into.
- The blade is made up of 5 layers, 3 plastic layers, and 2 mesh layers.
- The handle is made up of 3 plastic layers and 2 handles will be needed.
- The loop layer is made up of 3 layers.
Step 15: Baking Layers 1
I backed the layers in an oven at 450F/230C for 10 minutes. Place the layers in the oven on a glass surface. The glass surface is to prevent the plastic from sticking to it when heated and to help create a smooth even layer once backed. Allow layers to bake and fuse for 10 minutes.
Step 16: Baking Layers 2
Once the first 10 minutes have passed, remove the glass surface with the plyers and allow 25 minutes for the layers to completely cool to the touch. Flip the layers over, turning the side that was facing upward, down onto the surface of the glass. Reheat the oven and allow the layers to bake for another 10 minutes ant 450F/230C.
Step 17: Pressing Layers
Once the layers have been backed for a second time for 10 minutes, remove the glass surface. Place the second glass surface atop the layers and apply pressure to compact the layers. This will improve strength and improve the bonding of the layers. Allow 20 minutes for the plastics to cool.
Step 18: Outlining Mold
Once the plastic has cooled to the touch, use the template to outline the shape of the blade and handle, as pressing and melting will have warped the shape somewhat.
Step 19: Cutting Outline
Once we have the outline on the molded layers, we cut along the lines creating the shape of the blade and handle. I used a soldering iron with a flat tip however almost any cutting tule can be used.
Step 20: Sanding
Once the outline of the blade has been cut, sand the blade mold with 120 grit sandpaper. Sanding the edges to create a smooth finish, then sand the sided of the blade to ensure they are even. At this stage, we will start to file in the outline of the blade along the bottom edges.
Step 21: Aligning and Drill Handle for Sanding
Align the 2 halves of the handle. 3 Screws will be holding the 2 parts together. I used a 3mm wide and 10mm long screw for the main screw holding in the blade and 2 2mm wide by 8mm long screws to join the ends.
- Align the 2 halves for the end.
- Using a 3mm wide drill bit, drill a hole in the middle of the top end where the blade will be placed between the 2 halves.
- Leave the drill bit in place or screw the 13 wide screw in the hole to hold the 2 halves in place.
- Using a 2mm drill bit, drill 2 holes at the end of the handle, following the outline.
Step 22: Securing Handle Halves
With all 3 holes drilled, secure the 2 halves together with the 3 screws. The 2 smaller 8mm screws at the end and the larger 10mm screw in the middle of the opposite end.
Step 23: Sanding Handles
One both halves of the handle have been joined, sand along the edges to bring out the outline and curves of the knife. Use 120 grit sandpaper or lower to cut away excess material and create the edges. For any sharp, hard edges, use a file to carve out material until you've created the desired shape.
Step 24: Testing Fitment
Once the basic outline of the parts has been created. Put the blade beside and on top of the handle to ensure it fits in the profile of the handle. If the blade is 2 large, file it down to a smaller size until it is able to fit.
Step 25: Sanding Handles 2
With the outline created with the first phase of sanding, separate the 2 half of the handles by removing the 3 screws. Starting with 120 grit sandpaper, sand the sides (broadside) of the handle until the desired flatness has been achieved.
Step 26: Blade and Handle Alignment
At this stage, I will be aligning the blade with the handle to create the hole in the blade for the main bolt. Place the blade between the 2 halves of the handle, aligning it evenly. Hold the blade and handle in place and drill through the holes drilled into the handle previously and through the blade.
Step 27: Blade and Handle Fitment Testing
Once the hole has been drilled, secure the blade and hangle together with the 10mm long screw. Fold the blade in and out to ensure it fits between the profile of the blades.
Step 28: Drill Support Rod Hole
Once the fitment has been tested, we will need to drill a hole to support our support rod hole.
- Open the blade to its operational fixed position.
- Drill a 2mm hole above the hole that secures the blade to the handle.
- Close the blade into the handle.
- Drill through the 2mm hole you made earlier in this step. This will drill through the blade only, creating 2 holes in the blade and 1 hole in the handle above the hole that secures the blade to the handle.
Step 29: Mark Blade Cut Points
With both holes drilled into the blade. Remove it from the handle. Mark along the 2mm holes drilled into the blade. This will be the areas that will be cut away to allow the blade to fold once assembled.
Step 30: Cutting Blade
Cut the blade at the marked areas, cut into the holes drilled into the blade. Cut the back of the blade where the support rod may interfere with the blade when folding with a Dremel, knife or any cutting tool.
Step 31: Testing Fitment
Connect the blade to the handle using the screws. Fit the 2mm drill bit used to drill the hole into the handle. Fold the blade in and out to ensure the blade folds freely.
Step 32: Additional Trimming
If the blade does not fold freely, cut away the intersecting area with a Dremel, knife or any cutting tool.
Step 33: Folding Test Fitment
Test fit the blade and ensure it folds into the handle freely.
Step 34: Additional Sanding
At this stage, the outline of the blade is complete. Sand the blade with 320 grit sandpaper to smoothen any rough edges.
Step 35: Creating Loop
We will now create the loop by placing the mold for the loop between the 2 halves of the handle. Using the 2mm wide drill bit, drill through the holes in the end of the handle into the mold for the loop.
Step 36: Securing Loop Mold
Once the holes have been drilled, secure the mold for the loop onto one side of the handle using the 8mm long screws.
Step 37: Cutting Out Loop
With the loop secured to the handle, use the Dremel, soldering iron or any other cutting tool to cut a line towards the outside of both screws holding it in place. Once the vertical lines have been cut, cut along the top of the mold at the desired height.
Step 38: Removing Loop Mold
On the backside of the mold, mark 2 lines inward of the holes drilled through it. Loosen the screws and remove the loop mold.
Step 39: Cutting Mold 2
Using the Dremel, soldering iron or any other cutting tool, cut through the middle of the mold, along the inside of the lines that were drawn on earlier.
Step 40: Cleaning Up Loop
Using a stencil blade, cut away any excess material to clean up the mold.
Step 41: Sanding Loop
Sand the loop using 320 grit sandpaper to create a smoother finish.
Step 42: Final Sanding
Using 500 grit sandpaper to sand all the parts of the knife and create a smooth finish. This can be done wet or dry.
Step 43: Preparing for Sanding
Wash off any dust from sanding and allow parts to dry.
Step 44: Coating Handle
I used rubberized undercoating to create grip and a two-tone look. Spray a generous coat to both outer sides of the handle and allow it to dry.
Wet sand with 320 grit then 500 grit sandpaper until the desired finish is achieved.
Step 45: Cut Support Rod
Measure the rod to the width of the blade and both sides of the handle. Cut the rot to the measured length using the Dremel or plyers.
Step 46: Assembling Parts
At this stage, we will be placing all the parts together. Ensure all your various parts are clean and organized.
Step 47: Assembly of Parts (Loop)
Assembly of the parts starts with joining the loop to the handles.
- Place the loop on the inside of 1 side of the handle.
- Place the second side of the handle on top of the other with the loop in the middle.
- Screw on of the 2mm screws into the hole that goes through the handle and the loop.
Step 48: Assembly of Parts (Blade)
Place the blade between the handle and screw it into place. Place the second screw into the handle and tighten all 3 screws.
Step 49: Securing Support Rod
The support rod should be large enough so it fits into the hole above the one holding the blade in place snugly. Place the rod in the hole and push it in place to secure it. If the hole is a bit large, use a bit of glue on the ends to secure it. If the hole is a bit small, drill it out a bit more to fit the rod.
Step 50: Molding Grip
To be able to easily pull the blade from the handle, I cut a groove on each side of the blade where the gap in the handle was cut. I used the soldering iron to cut the plastic away on both sides however this can be done with the Dremel or stencil knife.
Step 51: Grip Sanding
Smoothen the grips cut into the blade using 500 grit sandpaper.
Step 52: Sharpen the Blade
With the knife fully assembled, sharpen the blade using a wet filing stone or 500 grit sandpaper until the desired sharpness is achieved.
Step 53: Completed Pocket Knife
Now with the knife assembled and sharpened, its time to get cutting. Attach it to your keychain or belt loop, assuring it's with you when you need it. Recycled, stylish and useful pocket knife. Cut on the go while helping to save our environment.
I hope you enjoyed this instructable, let me know what you think.
Have a great one.
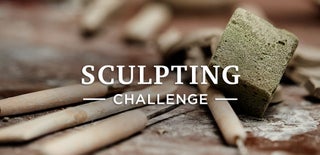
Participated in the
Sculpting Challenge