Introduction: HUGO : the 3D Printed Electric Bike
HUGO, The DIY 3D printed electric bike that makes YOU-GO!
When life gives you a pandemic, build an electric bike. That was the thought that popped into my brain when Washington State announced that we would be restricted to our houses and essential activities. With all the extra time inside I can't help but imagine all the possibilities! My mind runs wild deciding what bike to use, all the electronics, hours and hours of 3D modeling, saving to the SD card then to the printer then back to the computer to improve!
My name is Gabriel McGaffey and this is the story all about how I used 3D Printing to make an electric bike! Please join me in the making of HUGO, my new companion.
I also want to give a huge shout out to Tom Stanton for his incredible YouTube channel.
Supplies
- Bike
- 3D Printer
- A Lot of Time
Step 1: Modeling the Frame
As a maker of things, one of the rules that I follow is that things are always more enjoyable when you didn't break the bank to make it. So after hours of searching Craigslist and Facebook Marketplace, I found a $40 fixed gear bike that checks all the boxes.
- Cheap
- Good Condition
- Fixed Gear (Fixed gear worked best for me because of the minimal components in the drivetrain)
After getting the bike home I shot a few photos of it from the side trying to keep the camera as level and steady as possible. I was then able to upload the photos into Solidworks and start to model the bike frame. This is one of the most important steps because everything will be designed around the frame so accuracy is important.
Step 2: Designing the Battery
Next, it was time to design the battery. If you've ever looked at buying an electric bike battery that is premade then you know that it is very expensive and it certainly did not fit inside my budget. Luckily I found "a guy" who had thousands of Panasonic 18650 cells that were harvested from retired electric scooters! It literally doesn't get any better than that!
There are two 5S 5P batteries on this bike that are connected in series to create one 10s 5p battery pushing 36 volts nominal. This will be plenty of power paired with the 190kv 6374 brushless motor outputting up to 3000 watts.
My main goal for this project was to create an electric bike that could be 3D printed by anyone but looks like a product you could buy online. So when designing the battery I had 2 constraints in mind.
- Visually appealing
- User Friendly
Keeping the batteries simple made them attractive and adding accents like exposed hardware really brought the look together. To make the batteries user-friendly I wanted them to be plug and play or in other words, they needed to be easy to remove to charge but also be sturdy while on the bike. I also added an LCD screen with a momentary switch that displays the battery percentage.
Step 3: Engineering the Drivetrain
After an awesome few days of designing the batteries, it was time to jump into engineering the drivetrain. I was eager and excited to tackle this new challenge and hit the ground running. I ran for a while and was able to see it all coming together in my head until the whole thing came together. At least it looked good on the computer.
3D printing is very strong when used in the right way and one of the ways to greatly improve the strength of the print is to add brass inserts. These allow the use of screws in the assembly and are super easy to install. Just design a hole slightly smaller than the diameter of the brass insert and then once the part is printed just melt the insert into the part with a soldering iron.
Once all the parts were printed and inserts added it was time to assemble!
Step 4: Assembly
I love SolidWorks so much because it gives me the ability to assemble the whole project virtually. Fingers crossed that everything goes as planned in the real world it was time to assemble. So far so good only a few hiccups such as a misplaced hole or slightly off dimension but nothing that set me back more than a day.
Then it came time for a test ride. I was feeling pretty confident even though I had rushed a few things out of excitement. Unfortunately, confidence doesn't make a bike move:(
The first test run failed and then the second and the third and the fourth and so on. I learned a lot in this phase of trial and error but there were some moments that were seriously frustrating and very discouraging. As you could imagine 3D printed gears don't grip steel axels very well, belts don't align even if it looks great in the SolidWorks assembly, and 3D printed parts snap under the torque of the high output motor.
Step 5: Redesign
I really didn't want to give up on the original design of the drivetrain because it was the center of the bike and everything stemmed from it. Although with a bit of courage and a few hours of 3D modeling I was able to make a few slight changes that greatly improved the strength of the 3D printed components and I was actually very surprised. After what felt like the 30th time taking the whole thing apart and putting it back together it was finally done.
Step 6: Put It to the Test
What would be the point in making such a machine if it just sat in the corner collecting dust. It deserves to be pushed to the limits and refined and then pushed again until it is perfect. Sadly I don't have the time for that but It works really well and I encourage anyone out there to build one of their own!
Thank you for reading!
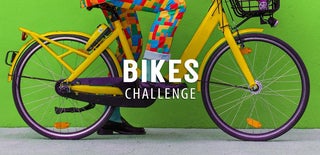
Participated in the
Bikes Challenge