Introduction: HV Insulator Pendant Lamps and Other Unique Accent Lighting
I went off on a tangent one day and started making different lamps.
I 3D printed some parts and got most of the rest from Lowes and the dollar store.
Best find was when I saw a bucket of power pole insulators at a barn sale. They were $3 each. Then $2 then $1. After a few trips I finally grabbed the whole bunch and said "how much for all?" He said $0.50 each but gave up counting after two dozen and said "how about $10?"
Love that place. Best deals ever.
Now what to do with them. Just google for images of "power pole insulators" and you'll get plenty of ideas.
A quick trip to the dollar store yielded these nice rose shaped night lights.
Possibly soon to be a color changing USB mood light.
Step 1: Simple Stands
I had some 3/16 brake line left over from my truck so I made a quick tripod stand for one of the larger green glass insulators.
Just a ring I formed by wrapping the tubing around the insulator itself. It was harder to straighten out the coil of tubing to get straight pieces for the legs.
When I got everything tacked together with the mig welder I had to find something to cover the ends so it wouldn't scratch the table. My first thought was to use little rubber automotive vacuum plugs by they are pricey and I didn't want to give up my stash.
Next best thing was to 3D print some feet. I had already made feet for my CNC machine but they were too straight sided so I made simple spheres with a collar and hole for the tubing. You can see the difference between using a 'hull' or a 'union' in the pictures above.
They fit pretty tight but if yours don't a little epoxy or hot glue is fine to keep them on.
I sprayed flat black paint on the stand. After looking at them for a while I think I may make the next one with copper tubing. Maybe even give it a chemical patina. Or just polish and clear coat the raw copper. Both looks have their appeal.
Step 2: Disassembling a Dollar Store Night Light
I didn't want to make the lights 110v so I popped one open.
It's really easy to do with a pair of channel locks. Just a little squeeze on the seam line and they pop right apart. Luckily they use standard red LEDs. They have 4 in series but that's about a 7v drop.
I rewired them in parallel and now they work well from a single lithium battery or even a USB cable. For tips on how to drill a hole in these see step 7.
Since I had them prepped for low voltage I tried the breathing attiny controller from my blue glowy dragon instructable. They run nicely from a single lithium cell but I think thats kind of wasteful.
A USB cord makes more sense. Almost everything today has a USB socket on it. Even my cable box!
Looks really cute. So nice that before I even finished the first one I had 2 people trying to take it home.
Step 3: Low Voltage Lighting Options
I wanted to try some 12V automotive lights. I had some 198 dash lamps in these little twist holders. I modeled a holder for them with a stem that would drop into standard lamp tubing. I even went back and modeled a holder that would take the bulb itself. No need for any threads since hte natural ridges on the filament layers seem to lock the stems into place.
I also found some flashing lighted balls in the dollar store. They were some king of silicone ball with its guts housed in a small acrylic ball so i made a similar stem holder for them. Just remove their batteries and drill a hole to run the power wires out....
Of course. a USB 'bulb' works too with no modifications.
Step 4: SteamPunk Lights
As long as I was drilling holes in glass I took a couple of these dollar store vases and drilled a hole in the bottom of each one. For $2 I was willing to take the chance on shattering them.....
Turns out they cut really quick and easy. The lamp tubing will thread partially into the taper of a 1/8 in pipe thread but I couldn't find a 1/8 to 1/2 bushing so I had to 3D print a couple.
I didn't even bother to paint the fake bushing. I liked it so much I'm starting to model all the pipe fittings for a completely 3D printed "pipe" lamp, well except the globe.... But then again I could 3D print lamp shades instead.....
A neat trick to use a string to pull the wires through the fittings. An easy way to get the string through first is to use a blow gun to blow the string through all the 1/2 in fittings at once. It comes out the other side real easy. Just cover one side and blow a string through to the other. Then cover that side and repeat. Just remember to tie them to something or you may just shoot the strings across the room....
Once the strings are in place manually thread them through all the remaining 1/8 fittings. Now its easy pull pul some lamp cord back. I used alarm wire since I had it on hand. Speaker wire works too since this is 12V.
Just don't skimp if your making a 110V model. For that be sure to use anti chafing bushings or even a long length of heat shrink tubing to protect the wires inside the fixture....
Step 5: 110V Power Lights
The hardest part was cleaning decades of dirt and debris from the glass. I still cant get it all. I tried brake cleaner, clorox, windex, even a wire brush.....
I liked the first lamps I made so much I decided to go and splurge on a diamond hole saw. $10 in lowes. Make sure you get a round diamond bit not a spade shaped carbide bit. Carbide will work once or twice but won't be as clean.
$10 is as much as I paid for the whole bunch of insulators but it's a tool. I have no qualms about buying a new tool to play with.
I bought the 3/8 bit. This means I can use standard lamp parts from the chandelier section at Lowes.
I had two banana trees I grabbed at a yard sale years ago. They made great table top stands for a couple of lights atop my bookcase. A piece of automotive corrugated split loom tubing keeps the wire in check.
I used 25 and 40 watt bulbs without a problem. 25 seemed easier on the eyes.
Step 6: Fake Jewels
Since I was 3D printing stuff anyway I tried making a 'jewel' to make it fancier. It really didn't need it. Here's the files if you want to try......
Step 7: Drilling Holes
Don't forget your safety glasses. BTW, I wouldn't recommend drilling them dry. If you do, get a respirator too. These things are about 1/2 to 3/4 of an inch thick. It will take some time to cut through. you can see the "pills" that were left behind in the bit...
To keep your drill from burning up you need to keep it submerged in water. A little modeling clay can by used to form a wall around the top. Since I didn't have any clay I used duct tape.
Stuff a few paper towels into the cavity so all that water doesn't run through your drill press when you make it through the glass.
Work the drill down 1/16 to 1/8 inch at a time pulling it all the way up to allow cool water to flow over the cutting edge.
Don't push too hard or you may actually boil away the water in the hole. This is real easy to do as you get near the end of the cut.
You'll know because you'll hear the sizzle when you pull it up. I've done a dozen and the bit still cuts like new. Some people like to use mineral oil or soap but I don't
You'll notice a white soapy looking film on top of the water. Resist the urge to touch it. It's just glass dust floating there.
Step 8: Old School Light
I'll end with the simplest one to do...
I also got a couple of $2 hurricane shades at the barn sale. A simple hole through a pipe and a carriage bolt made this the easiest lamp yet.... I used a vinyl washer to keep from breaking the insulator when I tightened the bolt. Its just a piece of leftover vinyl wallboard trim cut with a hole saw.
I hit the candle with a heat gun and it dropped into place....
It probably would have been fine without doing this..
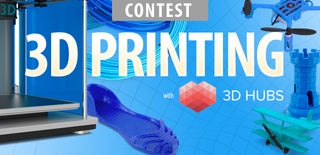
Participated in the
3D Printing Contest 2016