Introduction: Handmade Kiridashi Knife From a Metal File
Humans have been making and using bladed implements for millennia. Our earliest ancestors shaped the materials at their disposal into tools that allowed them to survive and thrive in what were often harsh and untenable environments. Among those earliest of tools were stone knives. Cultures throughout the centuries have made knives in vast varieties and styles to suit their specific purposes and bladed instruments have a long and storied history of use as tools, status symbols, religious instruments, accessories, and much more.
Among my favorite types of knives are kiridashi. Originally designed in Japan as a woodworking tool, these simple yet elegant blades are perfectly suited to a modern lifestyle as a pocket knife, box opener, paper cutter, craft assistant, nail cleaner, or, of course, even a woodworking tool. Sleek, stylish, simple, and incredibly useful, the kiridashi has taken on a life and genre all its own in more recent years. A quick google images search for the term will return many unique interpretations of this simple knife and a lot of inspiration for aspiring knife makers.
This project is a great place to begin for anyone looking to get into knife making. It is challenging enough to be interesting, but simple enough to be doable and the finished product is a tool that is both useful and beautiful.
This instructable will walk through the basic steps needed to make a simple kiridashi from a metal file. While I often forge my knives, this project requires no forging and very few tools, so it is perfect for the beginning metal worker.
Step 1: Cautions
As usual, there are a few considerations to be made. You are about to begin making a knife. Knives have a little bit of danger inherent to them. They’re sharp when they’re done. Sometimes they’re sharp even before they’re done. Please be careful handling the sharp piece of metal.
Also consider that at various points of this project, you will be heating the steel to roughly 1100-1300 degrees (that's literally red hot) then to around 500 degrees (still really hot). Hot things hurt if they’re touched. Please use tongs and don’t touch the hot piece of metal with any part of your body.
Last but not least, there are power tools involved. Drills put holes in things, cutoff wheels and saws cut things, and sanders and grinders sand and grind things. None of those are practices that someone should be trying out on their own body so please don’t hurt yourself with the spinning, whirring, grinding cutting things.
Step 2: Tools and Materials
For this project, you will need a few tools. Substitutions can be used in place of some of them, but using these keeps things relatively simple. The following are the tools and materials I used plus the substitutes that I have successfully used in the past.
Tools
- A Belt Sander (I have used files and sandpaper successfully but they make the process take forever. A bench grinder will also work, but will make it more difficult to get a consistent grind)
- A Gas Torch (anything that will bring steel to a red heat will work, but having recently bought the MAPP gas torch in the picture, I have discovered that it is absolutely wonderful and everyone should have one. The best $60 I’ve ever spent)
- Tongs (long handled pliers will work as well)
- A Cut Off Wheel (a sawzall with a metal blade or hacksaw will also work, but both will take a little longer)
- A Drill (there’s really no replacement for this. If you don’t have one already, go buy yourself something nice: a drill)
- A Set of Drill Bits (see comments regarding drill)
- A Wire Drill Brush (this can theoretically be replaced with steel wool, but, again, will make things take longer)
- Oil in which to quench (dunk) your piece during heat treatment (I use old motor oil, but you can also use vegetable oil, mineral oil, or even water)
- Water to cool the knife during grinding
Materials:
- A File (or another high carbon steel piece. It is important that your steel be high carbon or the finished knife will not hold an edge. Metal files are always high carbon tool steel. They have to be to file other metal. Because of this, they are a consistently safe material choice)
Step 3: Getting Started: Normalizing and Cutting
Our first step is to normalize the file so we are able to cut and shape it. This is important because files are generally very hard since they are usually meant to cut and shape other things and are not, themselves meant to be cut or shaped. To normalize the steel, take the torch and heat it to red hot, then set it aside in a nice, non-flammable location and let it cool off on its own. This will remove the original heat treatment, but never fear, we’ll be putting it back in a few steps. Do not dip the piece in water or anything else to speed up the cooling. That will defeat the purpose by immediately re-heat treating it. You can normalize the entire piece, or just sections. I chose to only do sections mainly because it was incredibly cold and I could not get the whole piece red hot at once.
Once the piece is normalized, you can cut your basic shape or blank. For my purposes, I removed the tang (long skinny handle part) of the file, and then cut the bar in half along a fairly sharp angle. This saves some shaping on the sander later and gives us a good indication of where our grind needs to go. A sharper angle will make a more traditional cutting edge while a flatter angle will provide more of a scraping or chiseling blade. There are advantages to both, it really just depends on what you want.
Finally, once your cutting is done, if you did not heat up the entire piece before, but would like the option of drilling holes in your handle for scales, a lanyard hole, or any other reason, go ahead and normalize the handle as well.
Step 4: Shaping and Grinding
Now the fun part. Start by shaping your piece of steel (also called a blank) into your desired shape. Use the sander or grinder to clean off any burrs that were left behind when we cut it and grind away excess material in areas where you want your handle to be more shapely. I typically like to grind a little finger grip into the handle to make it fit more nicely in the hand. Continue cleaning and shaping your knife until you are happy with how it looks. Make sure to move the blank around on the sanding belt, or you will wear away the grit on the belt or wheel and be left with a weird, striped sander or grinder.
To get a decent edge on your knife, line up the edge so it runs perpendicular to the edge of your sander or bench grinder. An optimal grind angle is 15-20 degrees. Kiridashi have what is called a chisel grind meaning they are ground mainly down one side. Hold the knife steady at your chosen angle and work at grinding away the material down toward the flat side. Because files have ridges, we will have to cheat just a little and also grind the other side down a small amount or the blade will have tiny, frail serrations in it. Work your grind down toward the flat side and once the tiny serrations start to appear, alternate between the sides until you are able to grind the serrations out. This will take a little patience and practice, but the material is pretty forgiving at this point. I recommend doing the grinding bare handed in order to tell when the piece is getting hot. Be careful not to let it get too hot or you will burn your fingers. When it warms up too much to be comfortable, cool it off in some water (or ice if your shop is frozen over like mine).
Technically, kiridashi come in left and right handed orientations depending on which side the grind is on. The knife in the pictures is left handed since the grind was made on the left side whereas one with the grind on the right side would be right handed. The reason for this is that, since these were originally used to mark wood for cuts, the woodworker would need to see where the mark was being made. With the grind on the same side as the hand, the woodworker can see where his mark is going. This orientation is something to consider while you are making the knife since you will most likely want it to suit your dominant hand.
Step 5: Drilling Holes
Step 6: Heat Treatment
Once you have gotten the edge close to your liking and have created the shape you want for your knife, it’s time to heat treat. To do this, heat the edge to a dull red color and quench (dunk) in oil or water. If the color gets brighter, closer to orange, let it cool down a bit and then bring it back to dull red before quenching. This process of heating and quenching will make your knife’s edge very hard, but also very brittle. If you were to strike the edge with a hammer, the steel would most likely break like glass.
Remember our little talk about high carbon steel before? Here’s why it’s important. In as much as I understand it, steel behaves like this because there are crystalline structures present in the material caused by the interactions between the carbon and iron molecules that together make up steel. When steel is heated to red hot, these structures are fluid and in motion. When the steel is dipped in oil or water, it cools rapidly, causing the structures to crystallize within the steel making it very hard. The reason normalizing works is because the steel is heated, making the structures fluid, but since it is not cooled rapidly, the crystalline structures don’t harden, and the steel stays soft.
There’s actually a great series of instructables about all of this from this maker: https://www.instructables.com/member/takeitfromablacksmith/ if you want some more in depth information.
Step 7: Tempering
To take away a little of the brittleness in our blade, we have to temper it. To do this, first polish away a bit of the oil residue on the bevel that we ground into the blade earlier. Follow the same procedure, holding the knife at the chosen angle and cleaning away the oil so you have a nice shiny surface again. We need the blade to be shiny so that we can see the colors that are about to come into it.
Once your bevel is polished back up, use your torch to heat the knife’s edge again. Don’t put the blade directly in the flame this time or it will heat too fast, undoing the nice heat treatment we just did. Sort of kiss the back of the bevel, up away from the edge itself, taking your time and watching carefully for the colors to come in. They will start as a very faint yellow, then darken to a sort of darker straw yellow, and then move into a sort of purple color. When the transition from yellow to purple starts to happen, quench the knife again. Congratulations! You now have a fully heat treated knife.
There is some fascinating metallurgical reason why steel makes these colors but I don’t know what it is. I do know that the yellow/purple color comes in at roughly 450-500 degrees meaning, if you don’t want to risk ruining your initial heat treatment with the torch, you can do this step in just about any home oven. Just make sure to clean all the oil off beforehand or you will wind up smoking out the entire house and, if you’re married, have a significant other, a mom, a roommate, or anyone else who lives with you, you may very well wind up sleeping outside.
Step 8: Cleanup and Polishing
At this point all that is really left to do is to clear off the leftover oil residue, polish the bevel, and clean up the sides and edges of the knife. I use the drill brush to clean off oil residue and I like to use a finer grain belt to do my final polishes as it leaves a nice, smooth, brushed appearance. If you struggle to get the edge just right, never fear, these things take some time and practice. Be patient, take your time and work on the technique. I usually finish off the sharpening with a whetstone and then a kitchen knife sharpener and these do a pretty good job for me.
Step 9: Final Notes
The beauty of these little knives is in their simplicity. As you can see in the pictures, I finished this one off with some little leather and copper handle scales, but I left its two siblings plain. I’ve also done leather cord wrap, twine, metal scales, wooden scales, and others so the possibilities are virtually endless.
The principles in these instructions also go for making other types of knives. All knives have to be shaped, heat treated, tempered, and, of course, sharp, so applying these concepts to different shapes and sizes of blades will work just fine. Experiment and develop a personal style. That’s half the fun!
Knife making is an art and a craft that I am still an amateur in at best, but making and creating things that are actually useful and fun is one of the best ways I know of to learn. This may not be the greatest thing you ever make, but it will be a useful tool and it will be uniquely yours. Not only that, but you will also have the opportunity to join centuries of humanity in an age old trade and that is something truly remarkable.
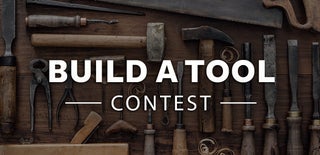
Participated in the
Build a Tool Contest