Introduction: Handmade Walnut Clock
My wife has been complaining pretty much since we got married that we needed a clock in the house, that was eight years ago. We’ve looked at clocks at Target and other places and just never found one that we were really happy with, so I finally decided just to make my own. I had the idea running around in my head for awhile so I set out to build it.
Step 1: Cut Clock Face and Layout
I had a nice scrap of walnut lying around the shop that was perfect for this project. My idea was to drill a set of holes at each one of the 30 degree intervals of the clock to represent the numbers. I started out by the piece of walnut to size, using a combination of my table and track saws, which is approximately 10 inches square.
I had a good idea of what I wanted when it came to the amount and size of holes in the face, but this is where I decided the best route would be to use a test piece. This allowed me to test out not only the hole size, but also the amount of spacing so that each hole appears to be evenly spaced from the last one.
The test piece ended up being instrumental in figuring out the final look of the clock. I now had the spacing and hole size laid out, the next step was to lay out a grid on the walnut to give myself indication marks for where I would need to drill each hole.
I started by splitting the piece into four equal parts by finding the center of the height and width and striking an intersection.
I then set my radius for the circumference and the clock- it’s important to be cognizant of where the largest outermost holes fall in elation to the edge of the board. You don’t want to make a mark too close to the edge of the board and have a hole cut into it.
The next step was to layout each 3o degree interval that the rest of the numbers fall on, I used a compass for this task.
I then drew a line connecting each of the number directly across from one another to create reference lines for drilling my holes.
Before going any further it is a good idea to layout the size of your clock movement on the front to prevent interfering with that area. I then started to layout where I wanted to drill all my holes, referencing the test piece that I created earlier.
Step 2: Hole Spacing and Drilling
The hole sizes are as follows: the four main numbers are (largest to smallest) 5/8ths, 1/2″, 3/8ths, 1/4″
All the small numbers are 1/4″. For the spacing: the four main numbers are (largest to smallest) 3/4″, 5/8th’s” 1/2″ spacing for all the rest of the holes including the in between numbers. I used a set of dividers to mark out these locations.
You can set the dividers with a ruler. I then used a punch to make the indention for drilling each hole.
I then took the board over to the drill press and drilled all of the holes from largest to smallest. Be sure to take your time with this step, if you go slow enough the center point of your bits will align itself into the indentations that you made.
Step 3: Clock Movement Recess
While you are at the drill press you can go ahead and use the 3/4″ bit to drill out the recess for the clock movement. Keep in mind that every clock movement is different as far as what it allows for the thickness of your clock face.
The kit I bought was made for a 1/2″ thick face so I drilled a 1/4″ recess.
Step 4: The Frame
To take the look of the project a set further I decided to add a a recessed frame around the clock. I used maple for this and cut each piece to give me an 1/8″ reveal around the clock face. I set the width of the side pieces with the thickness of the interior plywood pieces I was using on the frame along with the thickness of the clock face to give it the 1/8th of an inch inset into the frame.
I used my miter gauge set at a 45 degree angle to make all the cuts and then I glued it up with the help of my band clamp. I used plywood inside the recess of the frame and cut each of pieces at 45 degrees and glued them in one at a time.
To achieve the shadowed look of a recess frame, you have to paint the inside of the frame with flat black paint. By doing this before sanding and finishing, you lessen the chances of getting the paint on the outside edges of the frame.
Step 5: Finish and Assembly
I then sanded the face of the clock and the outside perimeter of the frame to prepare for finishing.
I used danish oil finish for clock face and water based poly for the frame.
I mounted the clock movement to the face and assembled it via the instructions that came in the kit.
After that I attached the clock face to the frame using a couple of screws to the backside being sure to center the face inside the frame.
Step 6: Watch the Video!
For a better understanding of how this project was built, watch the video.
I was really pleased with he final outcome of the clock. It looks great in our living room and now I don’t have to check my phone to find out the time.
One of the unintended cool features of the clock was the little indentations left behind from the center point of the forester bit.
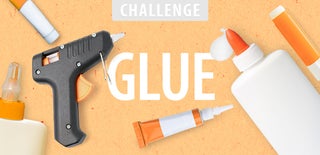
Participated in the
Glue Challenge 2016