Introduction: Handmade Wooden Bicycle
CONTEXT
College had just started and amidst the madness of timetables and classes, I was searching for ideas for the woodworking class. That's when I found a jazzy bicycle picture on Facebook. At first my carpentry teacher refused to take on such a complex project but soon enough he gave in to my naïve enthusiasm. We quickly realized that recreating an identical model in wood needed a different design approach than a typical bicycle made from steel, aluminium and carbon fibre. We took this into consideration while making the preliminary sketches of various parts that would someday be crafted and put together to roll smoothly.
Step 1: Preparation
Since we lacked the expertise of a cycle mechanic, the first and most obvious thing to do was to learn everything about a typical bicycle. I took a week-long workshop at a local cycle store where I stripped an old cycle it to its essentials and examined the scattered fragments.
All the different bearings were carefully noted as well as the functioning of the axles, the bottom bracket, the crankset and the chainset. After having repainted the frame, every tiny washer and bearing were assembled in the reverse order of dismantling to resurrect the old cycle with a new touch of life.
Step 2: Limitations and Final Design
Back in the woodworking workshop we studied the various tools available for use and their limitations. The Lathe for example could hold a maximum diameter of 11”. Furthermore, the availability of primarily red cedar (used in guitars, pianos, and other instruments) meant that it would not be ideal for crafting minute artistic details nor would slim pieces be very sturdy.
Our final design was no longer a full-sized wooden bicycle, but a smaller one, ideal for children between the ages of 5 and 9. However, provided you have a larger lathe, you can go ahead and make a full sized one too!
Step 3: Material Needed
Most of the machines and tools used can be easily substituted for more sophisticated ones or more elementary ones. None of the machines and tools were automatic or programmable in our workshop. This added a hand-made element to it!
Machines:
- Lathe
- Drill Press
- Drilling Machine
- Sander
- Jigsaw
- Electric Plane and Hand Plane
- Chisels and Hammers
- Files and Rasps
Materials:
- Thermocol (from packaging)
- Red Cedar
- PVC pipe (discarded)
- Cloth
- Sandpapers
- Mild Steel rods/pipes
- Wood glue
- Araldite
- Sealer
- Polish
- Thinner
- Wax
Step 4: Prototype
A full-scale model was first made in thermocol to grasp the challenges in our design. We used a chainset consisting of a freewheel, a sprocket and a chain attached to a shaft made from PVC pipe. It also gave us the opportunity to reinterpret the concepts from the bicycle workshop and apply them to the wooden context. Several factors still remained uncertain regarding the nature of the axles, the shafts and the bearings.
Step 5: The Beginning
We started the woodworking with the largest pieces first. We carved out the wheels, then the three parts of the frame followed by the front fork and lastly, the sprockets and the pedals. The design of some of these parts evolved organically over the period to accommodate the uncertainties. The wheels and the rear forks were formed by glueing two pieces back to back in a way such that their grain runs criss-cross. Since wood breaks more easily along the grain, this additional piece drastically increases its strength. We could have easily used plywood instead since it follows the same concept, but we wanted to work and remain inspired by the natural qualities of the red cedar.
Step 6: Joinery and Metal
Once most of the pieces were ready we got down to exploring the joinery between the wooden components. We also realized that some use of metal will be inevitable in the form of axles, bearings and shafts. These too were made at our workshop. Apart from ball bearings and washers we did not purchase any other parts. Even the bolts were custom made by using taps and threads. You can plan the axle ends differently so that you don't have to custom make too many small parts.
Wooden Joinery
Our preferred method of joinery was a Mortise and Tenon Joint. We also used biscuit Joints to piece together the main frame with the the rear fork.
Ball Bearing
12mm inner Dia needle-racer bearings were perfect for our use because of their elegant and compact look. You can substitute these for any other type of ball bearings that fit your size.
Rear Shaft
The 12mm Dia rear shaft which would usually link the cogset and the rear wheel has threads at the end so that it can be fastened by nuts.
Centre Shaft (Bottom Bracket)
The 12mm Dia centre shaft used instead of the bottom bracket has keyways at the ends so that the pedal cranks can be locked onto them. It also has threads at the ends so that the cranks can be bolted to prevent them from disengaging outward during motion.
Front Shaft
The 12mm Dia front fork shaft is the least complicated and is simply glued to the inside of the fork and remains immobile. The wheel rotates freely because of the bearing inserted at the centre.
Handle Tube
The handle bar was connected to the front fork through a 16mm dia waste iron pipe with a cotter pin or a wedge in the form of a custom-made brass nut bolt.
Belt Drive
The chain-driven idea was reimagined into a belt driven system. This was partly inspired from the lathe which functions on a similar concept. It also simplified the whole process of making gears and chain links which would anyway have been extremely brittle. Luckily it blended well with the rest of the design, minimalistic, experimental but grounded. You can very well use a ready-made chainset if it satisfies your aesthetics.
Step 7: Dry Fit
Once all the pieces were ready, a dry-fitting was done to find any mistakes. We realized that the central axle was going through 7 holes and the rear through 4 and neither was aligned. This led to covering up of 3 holes and redrilling them to get the alignment right. We also realized that the left side of the cycle was heavier than the other since the belt driving mechanism was fitted on that side. We solved this problem of balance by adding a heavy metal shaft in the right pedal and keeping a wooden one in the left. You could add a concealed counterweight anywhere you wish. Finally, the handle tube was secured to the handle bar by a custom-made brass nut and bot. A new rear sprocket was made, slightly larger than the previous as the length of the belt purchased was found to be slightly longer after the assembling.
Step 8: Sanding and Polishing
Most of the edges were smoothened using a file and a rasp. This was followed with several grades of sandpaper to make it ready for polish, where the whole project literally came alive.
- Aluminium Oxide 80
- Aluminium Oxide 100
- Emery 100
- Emery 220
- Emery 320
The polish with a mix of sealer was applied over several coats with sandpaper (Emery 320) in between every coat during the first stage.
- Stage 1: 3-4 coats of sealer mixed with thinner applied with brush.
- Stage 2: 3-4 coats of sealer mixed with polish applied with brush.
- Stage 3: 2-3 coats of polish applied with brush.
- Stage 4: 1-2 coats of polish applied by soft cloth.
- Stage 5 (optional): application of wax followed by buffing.
Step 9: Final Fitting
All the components were once again brought together to check for any discrepancies. Only minor ones were found which required widening of certain holes by a few millimeters and the addition of more washers to avoid surfaces rubbing against each other. The fork, the frame, the seat and the handle bar were glued together individually using wood glue. The axles were screwed to the sprocket and the freewheel along with araldite. Finally, all the glued components were fitted together to achieve our final result.
Step 10: Next Step
While some proportions were overlooked, we tried to strike a balance between developing the skills of using the tools efficiently and creating artistic connections. We also concentrated on getting the handmade joinery and alignment to work as perfectly as possible while keeping the bigger picture in mind. We tried to preserve the grain, colour and character of the wood while bringing it alive into a new form for a new purpose. The final result was far from perfect and very different from where we started off and it included lots of compromises and trial and error which could have been avoided by better planning and more expertise. Although it looks more like a showpiece it can be ridden perfectly. It would be very thrilling for the children to ride a bicycle without breaks but it would definitely be my nightmare. Hopefully they’ll be discouraged by the feeling of having a flat tire and a lack of suspension!
It would be an exciting development to make a suitable breaking mechanism, I'll be looking forward to hearing from you!
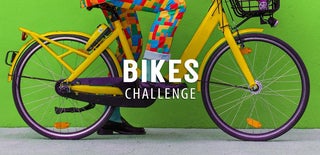
Second Prize in the
Bikes Challenge