Introduction: Hard Drive Clock
This all came about one day when I was taking apart some old computer components which were no longer useful; and not wanting to waste anything, I struck upon this idea of using the old hard drive to make a clock! This was also perfect timing, as I needed a new one, and had already bought some clock modules ready.
This is not the hardest of Instructables to make, but it is one that requires patience and precision - NO CUTTING CORNERS! It should only take a few hours to complete at the most (if you use similar tools to me).
Step 1: Materials and Tools Required
- An old hard drive from a computer
- Clock Module - mine had a 10mm shaft diameter and a 14mm long shaft.
- Clock Hands to fit the module
- Ear Defenders
- Safety Glasses
- A set of small Torx screwdrivers (T6 is the most common one needed)
- Phillips and Flat head screwdrivers
- Hammer
- Circular metal file (up to 1cm ish in width)
- Chisel
- Long Nose and Standard High Leverage Side Cutting Pliers
- Vice
- Pillar Drill
- Various drill bits - 1.5mm metal bit, a 5mm ish bit and an 8mm ish bit
- Small bit of cardboard (just larger than the size of the hard drive)
- Cloth
- Battery
Step 2: Remove Front Metal Plate and Rear Circuit Board
On the metal plate side - this will be the FRONT
- Using a Torx Screwdriver, (mine was T6 for all inside the hard drive), remove the 6 visible screws on the metal plated side of the drive and put them to the side.
- Scrape away the paper sticker, to reveal a final Torx screw, and remove that too.
On the circuit board side - this will be the REAR.
- Using a screwdriver (mine were just small Phillips screws), remove the circuit board, and put this and the screws to the side - they will be needed later. Keep them safe from damage, as the circuit board will be visible.
Step 3: Remove Centre of Circular Plate and Plastic Holding the Arm in Place
- Using the Torx Driver, remove the central screw from the centre of the metal plate. This is give you a circular small plate (KEEP THIS) and a metal ring - this is not needed.
The mirrored plate will still be kept in place by the metal holder at the centre of the drive.
- Use the Torx again to remove the plastic arm holder. Keep this and the longer Torx screw, as these will be needed later.
Taking it out now just enables the mirrored plate to be removed.
Step 4:
Magnet One
- Using the Torx Driver, remove the top right hand screw - this one holds the top magnetic plate. On the reverse of this plate is the magnet; one above the copper coil on the arm, and one below.
- Once the screw is removed, this top plate will totally come off.
- Using a chisel, slide off the magnet from this removed plate - it will only be stuck on with a bit of glue. This magnet is yours to keep now! It'll be a strong Neodymium one.
Magnet Two
- Remove the 3 Torx screws holding the bottom magnetic plate in place (I find this helps the process of forcing the magnet out).
- Move the drive arm fully down, revealing the bottom of the magnet.
- Prise up the bottom of the magnet with a chisel, (it may well break in the centre, but this does not matter), and pull out that half of the magnet.
- Push the arm the opposite way, and repeat the chisel and plier process pulling out the other half of the magnet.
Step 5: Re-attach Magnet Holders
- Screw in the bottom plate again, with the 3 Torx Screws.
- Re-join the top plate, with the 1 Torx Screw.
This should now look like the second picture.
Step 6: Drilling the Shaft Hole - HARDEST/MOST ANNOYING STEP!!
This stage is the most frustrating one, and to a certain extent, is down to trial and error. However, the below is my most successful method.
***USE SAFETY GOGGLES and EAR DEFENDERS***
- Place the drive face up onto a piece of cardboard, and then this onto the drill press table. If you have a press clamp, use this to hold the drive in position, as it is likely to spin.
- I selected a 1.5mm metal drill bit, and slowly drilled down the central hole in the metal circle. Do not use constant pressure on the bit - lift out every few seconds (this means it's less likely to get as hot, and less likely to snap the drill bit).
- Gradually, I finally managed to drill though enough to push out the rear metal pin (as seen in the second picture), and I was able to use the pliers to pull this out from the rear.
Step 7: Remove Central Metal Cap
- Using pliers, pull off the covering metal cap (this is not required again).
- Pull off the copper coil also (again, not needed).
Step 8: Widen Shaft Hole to Fit Clock Module
Now it is time to test the shaft width of your clock module compared to the hole left following the drilling and removing of the centre of the hard drive. Mine needed widening by a few mm.
- This time, place the drive rear up onto the cardboard, on the drill press. I then progressively used a 5-6mm bit, and then a roughly 8mm drill bit to get the hole to the correct width.
- Obviously, test as you go, as you do not want a loose fit.
On my drive, there was extra drive shaft height which I needed to remove in order to get the thread of the clock module clear.
- Using pliers, I pulled off the weak metal of this drive shaft, and roughed it down to a level near flat (as per the last picture).
Step 9: Widening the Metal Cover Hole
Now is the time to dig out that flat metal circle that was taken from the front of the hard drive a few steps ago. It will already have a hole in the centre, but this needs to be widened in order to accomodate the screw ring that holds on the clock module.
***GOGGLES and EAR DEFENDERS***
- I first used the drill press to widen the hole as much as possible. Due to the size of the piece, it did keep spinning off, so I then used a file.
- Setting up the piece in a vice, use a circular file to file out the hole, so that it can fit the inside ring of the module screw ring.
The desired effect is as the last photo - which took me hammering the ring into the metal piece, so that the screw part is flush with the top of the piece.
Step 10: Re-attach Rear Circuit Board and Front Screws
- Using the 5 Phillips Screws, re-attach the rear circuit board to the drive.
- Using the 6 Torx Screws, screw them back into the holes on the front - I think it looks better ultimately with them on.
Step 11: Assemble Clock Module and Screw in Place
- Put the rubber ring the right way round at the back of the module.
- Meet the module up to the back of the circuit board, ensuring the hook (top) of the module is the correct way around, and is straight.
- Using the metal piece with module screw ring hammered in, screw this on the front of the drive, covering the mirrored plated, and once screwed, holding this in place. I used pliers to fully tighten the screw, whilst still holding the back of the module to ensure it was correctly rotated.
- Using a microfibre cloth, (or similar), polish the mirrored plate, removing any fingerprints or smears etc.
Step 12: Attach Hands, and JOB's DONE!!
- Attach the hands in the order of the "largest hole first" - for me; hour, minute, then second hand.
- Whilst the hands need to be well pushed on, don't push them so much that they bend.
- Finally, just check that the hands rotate 360 degrees without obstruction by rotating the adjustment wheel on the back of the module all the way around.
STAND BACK AND ADMIRE YOUR WORK!!
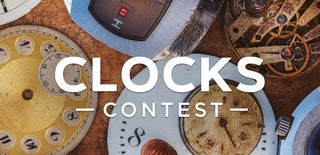
Participated in the
Clocks Contest