Introduction: Harry Potter Floating Shelf
Hey guys, as a Harry Potter fan, I wanted a place to proudly display all of my Harry Potter swag. So I made this floating shelf based on the Deathly Hallows symbol from the Harry Potter series (https://www.pottermore.com/explore-the-story/the-d... I built this using some scrap pieces in my shop, and used epoxy to join them together to make. It was a lucky accident that I realized epoxy was the perfect medium to customize which house I belonged to!
Be sure to check out the Youtube video above, which should help with better understanding each step.
Materials
Walnut Hardwood: (3x) 33.5"x6"x3/4" (LxWxT)
Padauk Hardwood: 32" x 4" x 3/4" (LxWxT)
1/2" MDF: 48"x48" sheet 3/4" Plywood: 48"x48" sheet
Epoxy w/Slow Hardener: https://amzn.to/2Efn89z
Sheathing Tape: https://amzn.to/2UCzMVO
Pigments: https://amzn.to/2ryoSDb
Tools
White Marker: https://amzn.to/2Efn89z
Circle Cutting Jig: https://amzn.to/2LcSxuO
Flush Trim Router Jig: https://amzn.to/2ErVB5G
Jointer Push Block: https://amzn.to/2Efn89z
Microjig Gripper: https://amzn.to/2Efn89z
Disclosure: All links above are Amazon affiliate links. There are no additional costs to the buyer. The small kickback I receive from qualifying purchases helps me to further invest into my channel and help to support my craft.
Step 1: Prepping Lumber for the "Cloak of Invisibility"
Since I was working with live edge offcuts, I picked out pieces that were all roughly the same length and cleaned the loose materials off of the pieces using a chisel and followed up by sanding the edges with 80 grit sand paper.
Next, I ran each piece through the jointer to get a flat face, and then through the planer to get all the pieces down to the same thickness. Lastly, I used my table saw to cut all the pieces down to the same length.
Step 2: Epoxy Pour for the "Cloak of Invisibility"
With the lumber pieces prepped, it's time to pour the epoxy. First I cut up some MDF panels to make the form to contain the epoxy. Then I applied sheathing tape on all the MDF pieces, which will help to prevent the epoxy from sticking to the form after curing. After attaching assembling the form together using bradnails, I sealed the gaps with some silicon so the epoxy won't leak out.
With the wood pieces clamped down to the form to prevent it from floating up, I began mixing epoxy with colored pigments. For the larger pour I picked green and silver to represent my house, the Slytherines. For the smaller pour, I added a bit of gold to the green and really liked how the two colors came out. Once the pours were done, I set everything aside to cure.
Step 3: Making the "Resurrection Stone"
While the epoxy is curing on the side, I began working on the "resurrection stone", which are made from 1/2" and 3/4" MDF rings. I first marked lines that represented a 29 1/4" diameter circle. Then I set up my circle cutting jig with a 1/4" straight bit. Line up the edge of the bit with the line that was drawn, and then simply let the circle jig to guide the cut. I first cut outer diameter on the 3/4" MDF and then adjusted the router to cut the inner diameter of the ring. The width of the ring is roughly 1 1/4". After the first ring is complete, I cut another ring out of the 1/2" MDF, but slightly larger so that I could flush up the two rings easily.
After the rings were cut, I glued them together using brad nails to hold them together. Once the glue had dried I used a flush trim bit on my router table to flush up the 1/2" ring to the 3/4" ring. This is a lot easier than trying to cut two rings to the exact same size.
Step 4: Making the "Cloak of Invisibility"
After the epoxy has cured, I broke the boards out of the form using a pry bar. I sent them through the planer to clean up the all of the overflow epoxy and bring all the boards back to the same thickness. Next, I cut all three boards down to same length using my crosscut sled on my table saw.
To cut the 30-deg miters on each board to form the equilateral triangle, I had to use a Multi-Purpose Tenoning Jig that I built awhile back. By setting the table saw blade at 60-deg and running the boards vertically through, it will result in the 30-deg I was looking for. It's all geometry!
Before gluing up the three sides, I put a bevel along what would be the front edge of the shelf. Then I used some clamping jigs to clamp the three boards together to form the triangle. You may also make your own jig to help clamp these miter angles so you don't have to get what I used.
Step 5: Cutting Joinery for the "Elder Wand"
This step is probably the most difficult step in the project. The "Elder Wand" and the "Cloak of Invisibility" will be joined together with a crosslap joint. First I marked where the cuts needed to be made on the triangle. Then I used a straight edge to help me guide my saw. Then I used a coping saw to connect the cuts to clear out the joint. I then put in the padauk and marked where the cuts needed to be on it. Using a hand saw and dado blades, I cut the joint on the padauk.
In the video I used hand tools to cut the joints, but after having made a few of these for sale, I've come up with a way to make these cuts with power tools. You can find it on my Instagram here
Before the glue up, I cut bevels on the edges of the "Elder Wand" that would face the front of the shelf. The I glued the two parts together.
Step 6: Cutting Dados in the "Resurrection Stone"
After the "Cloak of Invisibility" and "Elder Wands" have been glued together, set the assembly on top of the ring made earlier for the "Resurrection Stone". Once you are happy with the placement, use a pencil and strike lines along all of the edges where the two assemblies intersect. These lines are what helped me to position my router.
I'm using a router that can be used with a track, but you can do this by placing any straight edge along the lines and just keep the router pressed against the track. Even though there were a total of 8 intersections, you only need to adjust the fence 4 times, since every two intersections were formed by one board.
I placed the circular offcut in the middle of the ring so my track won't flex in the middle and it'll help support the track through the cuts. This is important to do so your cuts will all come out the same depth. I set the router bit to cut 3/8" deep, which is more than enough to make a strong joint between the assemblies.
Step 7: Painting and Finishing
After the dados have been cut, cover up the dados with painter's tape and also put tape on the glue surfaces of the triangular assembly. This step takes awhile to do, but it's very important because if glue and finish gets on the glue surfaces, the glue will not bond the wood correctly.
Once the tape has been applied, I used some black satin spray paint with primer to cover the ring assembly. If your spray paint doesn't have primer, then apply some primer before spray painting since MDF sucks up paint.
While the paint dried, I applied finish to the triangular assembly. This is the most amazing moment because not only did the finish bring the beautiful grain and colors of the wood to life, it made the epoxy colors so much richer. The bright colors of the epoxy will pop against the dark rich colors of the wood!
Step 8: Final Glue-up
I gave the paint and finish a day to dry after the last coat. This can be as short as a couple of hours or as long as a couple of days, depending on the finish and paint you used. Either way, I took off the painter's tape applied previously on both of the assemblies. Put a liberal amount of glue into the dados in the ring. Then I set the triangular assembly into the dados and applied clamps at every glue joint. I got a bunch of glue squeeze out, but I just waited for the glue to dry before cleaning it up since the glue won't adhere to the paint or the finished surfaces.
Step 9: Hang the Shelf!
The final thing left to do is drilling two holes into the assembly for hanging the shelf. I tried several different methods to hang the assembly, including using floating shelf hardwares and frame hanging kits, but none would have been feasible due to the asymmetrical shape of the shelf. I ended up settling on drilling and countersinking two holes in the locations shown in the image above and spray painted two #10 3" long screws. The color of the screws matched that of the ring assembly. Find a stud in the wall and screw the assembly into the wall. The top and bottom screws are lined up, so I only had to find one screw. The entire assembly is very stable and the locations of the screws can't be seen unless someone is looking for them.
With the shelf hung, start populating it with your Harry Potter swag and wait for all the exclamations from your guests!
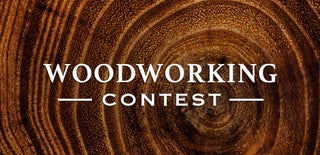
Participated in the
Woodworking Contest