Introduction: Have Tele, Will Travel!
There are many great tutorials on building guitars in Instuctables. This project takes a different approach by creating a hybrid travel guitar. Over 10 years ago I was visiting a music store and saw a unique guitar. It was designed as a light weight, portable, electric/acoustic guitar which was small enough to make it convenient for travel.
My initial reaction of “that’s way cool” was immediately followed by “I bet I can make one of those.” Fast forward to last year and I finally got around to creating and making my own version of a travel guitar. It takes its inspiration in part from a Fender Telecaster and the Traveler guitar I originally saw. My requirements were:
- It had to be small enough to travel and ideally fit in a suitcase or overhead bin.
- It would be a single pick up electric guitar.
- The neck had to be full scale.
- It would have a “headless” neck to help reduce its size and increase the “cool” factor.
- Where possible, materials were to be “on-hand” rather than purchased.
Building this guitar is possible for anyone with basic skills, simple tools, and patience.
The finished guitar is displayed next to a vintage suitcase I modified to create an amp.
Supplies
Prior to this build I completed several other guitar projects and had extra parts and material left over from those projects. In full disclosure, I have always used repurposed necks rather than creating one from scratch as this greatly simplifies the process. If you don’t have a neck laying about, one can be purchased on-line for under $30.00 or be brave and make a neck.
Materials:
- Poplar or Ash for the body
- Neck
- Headless guitar neck hardware
- 1 volume potentiometer (Pot)
- 1 tone potentiometer (Pot)
- 1 capacitor
- 1 bridge
- 1 input for the amplifier cable
- 1 plate and 4 screws to mount the neck
- Plastic laminate for the pick guard
- 6 tuners
- 2 strap buttons
Tools:
- Accurate measuring tools
- Table saw or circular saw
- Band saw or scroll saw
- Router & bits
- Drill and bits
- Bench sander, optional
- Random orbital sander, optional
- Jointer, optional
- Thickness planner, optional
- Soldering iron, solder, and flux
Step 1: Process:
The most important factor in constructing a guitar is accurate measurements. For consistency always use the same measuring device and check the accuracy from different positions before cutting. The tonality and playability of the instrument require precise measurements to ensure the proper location of component pieces. Guitar necks come in various standard scales; length of the neck in relationship to the bridge - specifically the length from the “nut” at the top of the neck to the “bridge.” Two of the most common scale lengths for guitars are 25 & 1/2 inches for Fender style guitars and 24 & 3/4 inches for Gibson style guitars. I built this guitar using the 25 & 1/2 scale.
The overall length of the travel guitar is 29 & 1/2 inches vs. 39 inches for a standard Telecaster style guitar. Saving nearly a foot in length and scaling down the body made a significant recuction in weight. The pictures below provides a comparison.
Step 2: Constructing the Guitar Body:
The internet provides many different sources for templates for guitars. For this project I downloaded a Telecaster style template. I took the download to a local copy center and with their assistance reduced the scale to 78% of the original size. The size was a matter of preference as it looked correct to me; and allowed me to use the scale of the guitar neck I had and still fit the other parts on the body. As it says in “Goldilocks” “not too big and not too small, but just right.”
I started by making a blank for the body of the guitar. I used 3/4 inch thick Poplar from a big box store rather than the Ash I had on hand. It was lighter and was cheaper than Ash. To get a sufficiently wide blank I used two pieces of the same size and glued them together edge to edge. To improve strength and stability the growth rings were alternated with one board’s running upwards and the other downwards. The proper thickness was a result of repeating the process and gluing the two blanks together back to back.
While body blank glue was drying one of the body template copies was attached with spray adhesive to a 1/4 inch piece of plywood. A band saw was used (jig saw can be used) to cut near the outside line of the template. A disc sander was used to fine tune the final shape of the template by sanding to the exterior line. (Other methods or tools can also be used for sanding the template to its final shape.) Leave the paper template attached to the 1/4 template.
The next step was taking the body blank for the guitar and registering vertical and horizontal center lines. Since the blank was rectangular, creating these reference points was much easier than doing so after cutting the body to shape. After attaching another paper template to the Poplar body blank I rough cut the body out with the band saw. The 1/4 inch plywood template was attached to the body using double sided tape, making sure the reference line on both pieces were aligned. A pattern bit on a router shaped the body to size. Final adjustments can be hand sanded. Care should be taken to understand the cutting direct of the router bit and the grain pattern. In an earlier build I learned the hard lesson that routing into the grain runs the risk our gouging out a piece of the body. This results in expletives being uttered and starting over on the body. Ouch!
[I find it helpful to make a practice body.and I typically use MDF. This provides a work piece to fine tune measurements, cuts, etc. rather than potentially making mistakes on the actual guitar body.]
Step 3: Modifying the Neck:
Carving a guitar neck and installing frets is a project in itself and requires special tools. To limit the variables that might cause problems, I elected to modify a neck I had in spare parts. Since I was building a headless guitar the tuners are located on the body of the guitar rather than the head on the neck. This required a piece of hardware to modify the neck. This piece anchors the strings much like a bridge on a normal guitar. Buying one was easier than fabricating one so I purchased one on-line; a Dovell 42mm metal string instrument with lock nuts. The price was less than $10.00 and I’ve been very satisfied with the quality. (StewMac and Sweetwater are two good sources for all types of guitar parts and tools.)
To mount the string device I used the band saw to cut the head from the neck close to the nut. I was careful to only remove enough material to allow mounting the device and still provide access to the adjustment nut of the truss rod. The next step was to glue a piece of the head stock back on the the neck to creat a level surface thick enough to mount the string device. After the glue set I removed the excess wood with the band saw. Attaching the string device required sanding the mounting surface to arrive at the best fit. Screws were provided to secure the device to the neck.
Step 4: Preparing the Guitar Body:
Various pockets were cut into the body for the neck, pickup & controls, the bridge, tuners, and access to the wiring, etc. Plywood templates were created and tested on the practice body. By using the router with a collar I could remove material in successive passes until I reached the desired depth. There are a variety of sources on the internet to help determine the proper depth and shape for the cavities. It is helpful to use a drill and Forstner bit to remove the bulk of the wood before using the router to finish the cavities.
- To create the template for the neck cavity I carefully traced the outline of the heel of the neck onto the plywood. Using a scroll saw I removed the material where the neck would fit. Time, sand paper, and patience dialed in the fit. The plywood template was adhered to the body with double sided tape, taking extra precaution to ensure the center of the template was centered and square to the body. (This is where the layout lines on the guitar body pay off.) Information on the depth to of the pocket is available from various sources on the internet. Using my router with a collar I made several passes until I reached the required depth, making sure to measure my progress after each layer.
- With the neck temporarily in place I measured from the nut and the 12th fret to establish the position for the bridge. The distance from the nut to the bridge should be twice the the length of the distance from the 12th fret to the bridge. If these measurements aren’t accurate the intonation along the neck of the guitar will be off. In other words, if the first string is tuned to E, pressing the first string at the 12th fret and playing it should also be an E at a higher frequency. If it isn’t it will be next to impossible to play in tune lower down the neck. Holes were drilled into the body to fit the posts on the bridge. The bridge should be snug but not so tight it can’t be removed.
- The placement of the pickup is measured in relation to the bridge using common specifications. A plywood template was created, a router bit with a collar was used and the cavity deepened to the required depth. (While the depth of the pocket must be deep enough to contain the pickup, it needn’t be as precise as the neck pocket. Pickups typically have adjustment screws to allow them to be raised or lowered to get a desired distance from the strings.)
- The cavity for the volume and tone potentiometers is on the back of the guitar. It is customarily located on the bottom of the guitar back of the bridge. I used the cover from another guitar to create the template for the cavity. I have an inlay kit for my router which allowed me to create a piece that fit exactly inside a routed hole. This isn’t required to complete the process; it is just one method. In my case it easily enabled me to create a lip to hold the cover. On this project I used plastic laminate for the cover. In the past I have used the same wood as the body to create an inlay that is nearly undetectable. I recommend leaving at least 1/4 inch of wood between the bottom of the cavity and the outside of the top of the body to allow for better installation of the tone and volume pots.
- Creating the space for the tuners was where the practice body really helped. My first idea was to allow access to the tuners from the front like the Traveler guitars. For a variety of reason including structural and esthetic I finally decided to not show the tuner heads. After the initial stringing and tuning, small adjustments are easy by simply flipping the guitar for access. For me, minimal inconvenience in tuning was more than offset by a cleaner look. After determining tuner placement I created a cavity with the use of a template and router. Like the cavity for the pots I left enough material to ensure a solid mount of the tuners. This also required creating a shallow channel along side the tuner heads so they could revolve 360 degrees.
- Wiring required drilling holes from the pickup cavity to the tuner cavity, from the rear of the guitar to the tuner cavity for the input, and from the tuner cavity to the bridge post for a ground wire.
Step 5: Completing the Guitar Body:
- After all the cavities are finished it is time to test fit the components. Then fine tuning and spatial adjustments can be made.
- Using a router with a 1/4 inch round over bit I carefully went around the top and bottom of the body. While I used a router table, you can also use the router by hand or even hand sand the edges to round them over. Then comes everyone’s favorite part - sand, sand, and sand some more. I started with 80 grit and worked my way to 220. A random orbital sander speeds things along but is not necessary and hand sanding is still advisable after power sanding.
- This is the first guitar I’ve painted. Professional builders would use nitrous cellulose paint sprayed on in many layers. That paint is highly flammable, requires strong ventilation, respiration masks, and is somewhat difficult to work with. Keeping in mind the “kids don’t try this at home” I opted for a rattle can and it was simpler than using my HVLP sprayer. My color choice was surf green, a traditional old school color. I constructed a temporary spray booth and primed and painted the guitar in several coats. I used Krylon semi-gloss paint and clear varnish as the final coat. If I build another I may test rolling the paint.
- The pick guard template was created for a full scale Tele Thinline build. It was scaled down to fit the current project. After creating the new template I rough cut the plastic laminate. The final shaping was done by attaching the template to the pick guard material and trimming to the final shape with a pattern bit. After positioning it on the guitar body I drilled pilot holes and attached it to the body with screws. This another step I’d reconsider. I used the same number of screws as on the full scale pick guard and it was overkill.
- The final step before assembly was to line the pickup and control cavities with copper shielding tape. In this case it may be overkill. I won’t be “playing out” with the guitar and there’s only one pick up, so interference shouldn’t have been a problem. The idea in using it was eliminate a variable. Since this guitar was a new approach for me it was better to shield the cavities than finding distortion later and not knowing the cause. I found copper tape in of all places a garden center where it is advertised to repel slugs. StewMac also sells it.
Step 6: Assembly & Wiring:
- Installing the pickup, volume & tone controls, and input jack is pretty straight forward since there is only one pickup. I grounded the assembly by running a ground wire to the bridge.
- After drilling pilot holes the neck was attached using 4 screws, and a back plate.
- The strap buttons were attached.
- Strings are added and after tuning, the string height is adjusted from the bridge.
This completed the build and I am happy with the results. It plays nicely and travels well.
Build your own and plug in and play that funky music!
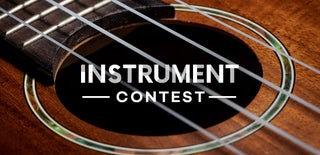
Participated in the
Instrument Contest