Introduction: Heavy Metal Wood Cutting Board
I started this project as part of a Christmas gift for my brother in law who is obsessed with the band Slayer! He is a chef for his profession but a rocker at heart.
This year own both sides of my family we decided to build/make things for Christmas instead of buying things. I have been working with wood as far back as I can remember, learning things by experiment or looking through woodworking books.
Never had any training so please go easy, if I don't do things the "right" way. I just find what works best and learn from there.
I find making things that people will use a daily basis very fulfilling and each project I have done has allowed me to better hone my craft.
Hope you all learn a little something from this Instructable, and make your own variations! Can't wait to see them!
Step 1: Material List / Tool List
Here is a list of items I used to build this.
Materials:
- (4) Walnut - I had all different lengths but just make sure you use a hard wood for cutting boards.
- (1) 2' x 3' x 1/8" piece of Hard Maple - For the inlay.
- Tribond 3 - good to use for anything to do with food preparation.
- Mineral Oil
- Beeswax
Tools:
- PATIENCE and a steady Hand
- Router
- 1/4" plunge bit
- 1/4" Round over bit
- Jigsaw
- Hand Planer
- Hammer
- Regular / Soft
- Chisels
- Table Saw
- Sand Paper
- Sanding Block
- Orbital Sander
THIS GOES WITHOUT SAYING BUT MAKE SURE TO USE ALL REQUIRED SAFETY PROTECTION WHEN USING TOOLS. NOTHING SCREWS UP A CHRISTMAS PRESENT LIKE BLOOD SPLATTER, IT A MAJOR BUZZKILL.
Step 2: Figure Out Your Design
As stated in the intro I went with the "Slayer" band name and logo design because my Brother in Law is a huge fan! For my other cutting board I am making an inlay of a Mallard duck for my other brother in law who is an avid hunter.
- I started online researching the most popular layout for the band name then saved a picture of it into Microsoft Word.
- I double checked the size of the cutting board I was looking to make then correctly sized the design to fit inside those parameters.
- Print out the design and use a tape to double check that everything printed out correctly
Step 3: Prepare the Wood!
I was given different lengths and widths of walnut to work with so I really took my time which ones looked best together. Because the pieces of wood I use were scrap pieces they were all different heights, lengths, and widths. I saw this as a challenge so I decided to tackle it head on.
NOTE ABOUT CUTTING BOARDS:
- The actual surface of the cutting board can be made of out different parts of the same piece of wood.
- End Grain cutting board are the best type of cutting boards for frequent use. This is due to how the grains are standing on end and will not have as much of a chance to be "broken" by dragging a knife across it all day.
- I decided not to go this route with the board only because I really enjoy how the walnut pops once it is complete. My board may require more maintenance over time vs the End Grain cutting.
OKAY back to work.
- Grabbed four pieces that looked good together and prepped them to be glued together.
- Gets your clamps ready! I used 4 clamps all together but 6 would of been nice.
- Put glue on each side of the wood and then put the clamps on to tighten
- MAKE SURE YOU DO NOT GET A "BOW" IN YOUR WOOD. Take a look at it from the side and make you are getting equal pressure from the clamps and that the board is flat.
- Wipe away the excess glue as best you can.
- Leave it alone for 24 hrs.
Step 4: Make the Thing Flat!
After the glue is set up you will notice (if you have different height wood pieces like me) that your board has ridges all over the place. We need to make this thing flat before we do anything else.
- Choose the desired height on your hand planer and GO TO WORK slowly.
- Once flat use a table saw or hand saw and square the cutting board to the desired length you need.
- You should now have a rectangle, flat piece of walnut itching for your inlay!
Step 5: Inlay Time
Prep your jigsaw, make it ready for battle, I use a table top jigsaw for my project. After cutting out your design on paper place those templates on the hard maple and trace those outlines with a pencil.
Cut those designs out with the jigsaw as close as you can to the actual lines but take your time. A mess up here isn't devastating but it will take more time to fix then the extra time it would take just to cut it out slowly initially.
Any parts that are too hard to get into you can always clean up with sandpaper later.
Take Your Time.
Step 6: Prepping Your Wood for the Inlay + Routing Out the Design!
Once your inlay is prepped go ahead and place the cut pieces on the cutting board exactly where you want it for the final outcome. Trace those designs onto the cutting board and stand back to make sure that is exactly how you want it to look once completed.
Set your plunge router bit to be slightly less then the thickness of your inlay 1/8" thickness. I shot for 1/6" plunge depth on mine. Lock it down and get ready to get nice and dusty (Love that smell.....)
Tip of the Day: You guessed it - Take your time!
Second Tip of the Day: Keep reading ahead for more information.
Clamp down your cutting board and get ready to route out those designs.
Route out each of your designs, being careful not to route outside the lines and watching your corners in your design. Once you are done, covered in saw dust and feeling good about yourself, be sure to go back and clean up corners with your chisels.
you're almost there.....
Step 7: Insert That Hella Good Inlay
First do test fittings of all your pieces, use sand paper to clean up edges on the inlay pieces. Make sure everything fits snug and again double check that all of your pieces fit correctly.
TIP: check, double check, then double check your initial double check of all of your fittings. Once you place glue down there is no going back.
P.S. Okay there is going back but its a pain in the arse so just ummm how you say......TAKE YOUR TIME.
Place glue into the inlaid slots and push each inlay into position, using a soft hammer to make sure they are snug as a bug in a rug.
Place two pieces of wood horizontally on your cutting board (1 on top and 1 on bottom that over hang your cutting board). Clamp those down on the end to create lateral pressure across your board. Next place two pieces of wood vertically on your board and again clamp down to create more pressure on your board. See picture for better explanation.
Let sit for 24 hours..........listen to Slayer that entire time........it will be worth it.
Step 8: Lucy, You've Got Some Planing to Do!
and by Lucy I mean you.
you will notice once you remove the pressure boards your cutting board looks awesome but not usable as a cutting board.
Don't give up here you only have like hours upon hours of planing sanding routing and sealing left! that's it!
Get out your hand planer and get to work, it took me a lot longer then most but that is only because I have never used a hand planer before and had to teach myself.
Once I did get the hang of it, it worked out great!
- Get your inlays to be as flat as you can to the orginal board with the hand planer and then get out your sander.
- Use 80 grit for the majority of the board (don't forget the underside)
- once the majority is complete sand the board with 120 then 220 grit.
- being sure to wipe away dust after each change of sandpaper.
- feel with your fingers over your board with your eyes close. if you can feel ridges or feel "humps" start the process over until you can't.
Step 9: Edge Work
This step is optional but I think the cutting board looks better with a rounded edge.
Use your router for this and depending on the depth of your cutting board, set the correct depth to your round over bit. go in the clockwise fashion around your board to avoid chip out.
Now there was supposed to be something I was supposed to tell you.....hmmmmm.....O yeah take your time and use test pieces first so that you are not surprised when you use the real thing!
Step 10: Seal It Up and Display/use It!
You need to make your board water repellent as best you can and one of the cheapest ways is to use a mineral oil primer with a beeswax butter protector.
- Wipe down your board with a clean rag, to take off any remaining dust
- Heat up some mineral oil on the stove.
- Using a clean rag, cover your board with mineral oil and allow it to soak in for a few hours.
- I did this 3 times before I did not have anymore "dry" spots
- Wipe off the excess and repeat the process on the other side of the board.
Once the board is primed/sealed with mineral oil be sure to give it a protective coating. I used a beeswax butter mixture.
- Pour 1 cup of mineral oil into a mason jar
- Add 25% to volume of Beeswax (1/4 cup)
- Put into a pan full of water and slowly turn up the heat.
- Be sure to keep stirring until all the beeswax is dissolved.
- Once dissolved, take a clean rag and with little circles rub the mixture into your cutting board.
- Allow it to cool and dry on the surface
Once done you will have a thin film of residue on the surface, simply buff out with a clean rage in the direction of the grain.
STAND BACK look at your creation and let out a "Hell Yeah!!! Look at what I have created!".....if you want.
Thanks for reading and please vote for my instructable in the contest !!!
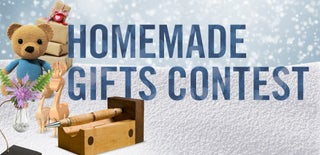
Participated in the
Homemade Gifts Contest
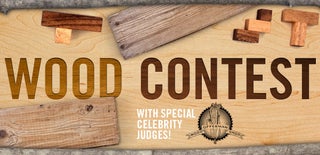
Participated in the
Wood Contest