Introduction: Herring Bone Industrial Coffee Table
I don't know about you, but I love the Herringbone pattern. I’ve been obsessed with it ever since I saw a tile floor done in a herringbone pattern a few years ago. I had been trying to find the right project to use a herringbone pattern for some time when I got a call from a friend of mine.
He works for a company that makes large custom wood projects. Think big board room tables for companies and big wooden installations for retail business. Anyways, he told me that they had just finished a big project and were going to be throwing out a ton of old offcuts of white oak and black walnut.
He said they were mine if I could come pick them up before the end of the day. Naturally, I dropped what I was doing and drove right over. I backed my truck up to their loading dock and started piling all of their little offcuts into the bed. I finally had the materials I needed for that herringbone project!
Oh and hey, if you like what you see here, consider checking me out on Instagram. You can find it at @zacbuilds (direct link: https://www.instagram.com/zacbuilds/) I post all of my projects there, along with any tidbits and morsels of information that I glean along the way. Hopefully helping others to avoid making any of the same mistakes I’ve made. So please check it out, and if you like what you see, consider dropping a follow 🙂
Step 1: Supplies
This wheelbarrow full of wood scraps is what I got from my friend. I wasn’t too discriminating, I grabbed every scrap of wood I could get my grubby hands on. I am definitely not too proud to dumpster dive for wood like this!
Getting all the wood for free really brought down the cost of this project. I spent just a hair under $100 dollars to get it all done.
Outside of the woods scraps, I bought about 20 feet of 1 1/4", 1/8" thick, angle iron steel for 50 bucks. As well as some 1" bolts and nuts, some wood glue, spray paint and a can of clear coat.
Step 2: Cutting the Wood
The first step was to mill all of the wood down to a uniform size and cut off any defective bits (like knots and cracks). Remember this was all scrap wood, so it wasn’t in the best of shape. With most pieces, I had to cut 2 sides of the wood before I was left with anything usable.
All of the pieces I used for this project were cut to 1″ x 3/4. Again because they were all scraps they all had different lengths. The pieces I ended up using for this project were between 20-30″ long, but I’ve still got tons of shorter pieces left for another project.
Step 3: Prepping for the Glue Up
To form my coffee table top I had to glue all those pieces freshly cut pieces of wood together.
I started with a little bit of prep work. All glue-ups require clamping, and clamping things in a herringbone pattern is a little trick. To make things a bit easier I screwed the first two starter pieces of the herringbone pattern to my work table. That way when I went to clamp everything together I had a strong, fixed base, that I could clamp everything to. When you’re doing a herringbone pattern it’s really important that every piece is exactly 90 degrees perpendicular to its neighbor. So I used a big framing square to make sure my starter pieces were a perfect right angle. Somehow I still managed to screw this up, and my starter pieces were slightly out of square. This caused me some headaches, but we'll get to that later.
You might also notice that I’ve covered my table in a layer of plastic. I do that because once you clamp the wood together it squeezes out a lot of glue. If you aren’t careful, that glue will adhere whatever you’re working on to the table. Carpenter’s glue doesn’t really stick to plastic though, so the drop sheet makes it really easy to remove the tabletop once the glue is dry. Also, it makes clean up super easy.
Step 4: The Glue Up
Once I had my two starting pieces locked in position, I started the gluing process. Each piece of wood got a generous bead of carpenters glue.
I made sure to apply glue to the side and the end grain of each piece. The butt joint where the end of one piece meets the side of the next piece is integral to holding everything together in a herringbone pattern. All of those butt joints running down the center of the tabletop are really the only thing that holds the two halves of this project together.
Originally, I wanted to make the whole tabletop in one big glue-up, but, during a test layout, I quickly realized that wouldn’t work. Even in this photo, you can see that the clamps are pretty far from the center of the herringbone pattern. The more pieces I tried to clamp at once the further it pushed the clamps to the wings of the pattern.
Once I had 16 or so individual pieces laid out I clamped everything back to my two starters pieces. I tightened down the clamps until I saw some glue squeezing out from all of my joint, I gave the clamps another half turn, and then I let it sit for an hour or so so the glue could setup.
Step 5: Glue Up Phase 2
Glue, clamp, wait. Rinse and repeat 3 times.
Eventually, I had these 3 smaller intermediate pieces of herringbone pattern.
The last stage of this giant glue-up was gluing those 3 intermediate pieces together. I applied glue to the joints between them and clamped everything with this elaborate web of clamps.
Just as I finished tightening the last clamp I heard a loud crack. Shit. Remember how I said my starting pieces were slightly out of square? Well, the 3 intermediate pieces didn’t fit perfectly together. When I clamped them together it applied quite a bit of force to the seam down the center.
You can see, right at the bottom of the second photo, the center seam ripped itself apart. Thankfully this didn’t affect the final build since that part pattern was always going to get cut off. I got really lucky here, if it had cracked at the other end I would’ve had to start all over again. Let that serve as a lesson to you kids at home, always double and triple check your angles haha.
Step 6: Cutting the Table Top
After the glue was dry and all of the clamps were removed I was left with this giant chevron-shaped piece of wood. Pretty cool, but I needed something a little bit more rectangular for this table.
To accomplish this I started by finding a centerline through the pattern. That might sound easy, but the herringbone pattern can play tricks on your mind. Finding the centerline was a trial and error process for me. Once I had my centerline figured out I measured all of my other lines off of it to keep things nice and symmetrical. The rectangle I drew ended up being 22″ wide and 36″ long. I choose 22 inches because I felt that fit my living room/couch the best and I used the golden ratio to work out the length of the rectangle. You know about the golden ratio right? It’s supposed to be the ratio between the width and length of a ratio that is the most visually appealing. In other words, it looks the most “rectangle-y”. That’s a word, right? Rectangle-y. Ya, I’m pretty sure that’s a word.
Using a track saw I cut along the lines I just traced onto the wood.
As it turns out track saws are just as good for cutting bevels as well they are for straight cuts! After the straight cuts were done I used the track saw to cut some 10-degree bevels on the two ends of the tabletop. This was necessary in order to make the tabletop fit into the legs I was about to make. I wasn’t originally planning to do this detail, but I realized my tabletop wouldn’t fit tightly into the legs I had sketched out if I didn’t. I’m glad it turned out to be necessary though because the bevel became one of my favorite details in this build.
Step 7: Sanding
I wish I had a giant planer. It would save me so much time. Alas, my planer is only 13″ wide, and not nearly big enough for this tabletop. That left only one option for me, the belt sander.
I did my best to make sure every piece of wood was properly aligned before I clamped everything together in the glue-up, but invariably, there’s always some pieces that stick up a little higher and some pieces that sit a little lower. To remove that variation between pieces I sanded them off with an 80 grit sanding belt and a bit of patience. Ok, more like a lot of patience. This process took me at least a couple of hours, and frankly, it wasn't that interesting. To help pass the time, I listen to a lot of audiobooks and podcasts while doing these projects.
The belt sander is great for removing a lot of material quickly, but it leaves the wood pretty rough when it's done. To give my tabletop that silky smooth finish I crave on all of my project I started sanding with my random orbital sander. 80 grit sanding pads to start and then I slowly worked my way up to 220 grit. 220 grit leaves the wood with a really nice smooth feel to the hand, but there are still enough micro-abrasions and surface imperfections that the varnish will adhere to it nicely.
Step 8: Clear Coat
Is there a better feeling than rolling a finishing onto freshly prepped raw wood? Because I sure as hell haven't found it, haha. I just love how the color and texture of the wood are instantly transformed. The tones and shades of the wood just immediately pop! I love it.
For this project, I used a satin floor varnish. Satin is a nice middle ground between a glossy finish and a matte finish. It hides flaws better than a glossy finish would, but it’s also super easy to wipe down and clean if it ever gets dirty. Which is important, because I eat most of my meals at my coffee table and I’m a known spiller. This particular varnish I use dries really quickly so I’m able to do multiple coats in a short amount of time.
To save time, and avoid cleaning my tray and roller between coats, I stick them in a garbage bag, squeeze out most of the air and then seal the end. This helps to prevent the varnish from drying and clumping up in the tray.
If you just leave your tray and roller uncovered and sitting out between coats, you'll come back to find it half skinned over and filled with tiny "snots". Once the varnish starts to dry like this, it’s basically unusable.
I ended up applying 4 layers of clear coat to my tabletop and I sanded between each coat to ensure a really nice smooth finish. Anything more than that and you probably wouldn’t be able to see the texture of the wood through the clear coat, and that would just be criminal.
Step 9: Measuring Out the Legs
Ok, that's the top done with, let's talk about the legs.
They're made from the steel angle iron. It’s basically commodity-grade steel, I bought 40′ feet of it, for this project and another project, at The Metal Supermarket. I thought the Metal Supermarket was only a thing in my city (Toronto), but it turns out they have locations all across North America. If you need any metal for a project I highly recommend them, it’s WAY cheaper than buying steel at Home Depot or Lowes. They were also nice enough to cut all my pieces into roughly the right lengths, so if you don’t have the tools necessary for cutting steel (and I know most people don’t) it’s a great option.
As I said, my angle irons were cut to ROUGHLY the right length but I still had some measuring and cutting to do back in the shop. I knew I wanted the legs to be a trapezoid shape, so I had to do a little bit of geometry to figure out my angles. I think the last time I did any geometry was back in the 9th grade. Come to think of it, I’d like to take a second and apologize to my 9th-grade math teacher. Mr. Glenn, It turns out you were right, there are some real-world applications for geometry haha. That being said, I still hold that calculus was a waste of my time.
After some quick sketches and a bit of research I figured out the interior angles of my trapezoid legs. The two at the top would be 100-degrees and the two at the bottom would be 80-degrees.
To make a 100-degree inside corner I needed to cut a 50-degree miter onto my angle irons. So I set my handy digital angle gauge (seriously, everyone needs one of these, they are really cheap!) to 50 degrees and then traced a line onto the angle iron.
Step 10: Cutting the Metal
With an angle grinder and a cut off wheel, I freehand cut my miters. I was a little worried about this step, but it wasn’t as bad as I thought it would be. Still I would’ve preferred to make these cut with a metal miter saw, but I don’t own one of those.
I took it slow and traced the line I marked with a shallow cut. Once I was satisfied that my shallow cut was straight and followed the traced line and applied more pressure until I cut right through the angle iron. As long as you take it slow, it’s actually pretty easy to control an angle grinder cutting through steel like this. Just make sure that when you start the cut you keep the blade straight, it’s very easy for an angle grinder to bind up on a cut like this. I then repeated both of these steps for my 80-degree corners by marking 40-degree miters and cutting them.
Step 11: Welding the Legs Together (and Fixing My Ugly Welds)
With all my miters cut and cleaned up, I was ready to try some welding. I say TRY, because this was my first time welding anything. I was pretty intimidated by the process, but I pushed forward. I practiced on a few scrap pieces until I felt comfortable proceeding onto the legs.
I clamped my angle irons to the table so the miter I wanted to weld was overhanging the edge of the table. I also made sure that when I clamped the two pieces of steel in place they were at exactly the right angle. Once I started welding there wouldn’t be much room for adjustment! As scared as I was to start welding it’s something I’ve really wanted to add to my skillset for a long time, so I’m glad I finally got around to doing it.
Using an angle grinder and a grinding disc I cleaned up my welds. Grinding discs are abrasive discs that you can use to slowly grind away at metal. Just like sanding, except for metal instead of wood. I worked each of my welds until they were decently flat.
I’ve found the best way to get good at doing something quickly is A) practice and B) be the guy whos responsible for correcting any mistakes. Grinding all these welds flush gave me a lot of time to reflect on how I could do my welds better next time 🙂
Step 12: Taping Holes in the Legs
To secure my tabletop to the legs I decided to use some carriage bolts! There's something so deliciously old-school about carriage bolts. Maybe it’s just the word carriage in the name now that I think about it…
Anyways, that meant I had to drill 4 holes in each leg slightly larger than the 5/16th diameter carriage bolts I was using.
Drilling through metal is actually easier than you might think. All you really need is a halfway decent drill, some sharp drill bits, and a lot of downward pressure. Use the slowest speed you drill has, and apply as much downward pressure as you think your drill bit can withstand. I clamped the legs in a vice grip and drilled some small starter holes. I started with a 1/8th drill bit and worked my up to a 3/8th drill bit. The more drill bits you have between the first size and the final size, the easier the job will be.
My tabletop needed a set of corresponding holes drilled in it. Sure, I could’ve measured the holes on the legs and transcribed their locations onto the tabletop, but the tolerances here had to be really tight. I didn’t trust myself not to screw this part up.
Instead, I clamped the legs to the tabletop and drilled through the holes in the legs and down into the tabletop, thereby ensuring perfect alignment!
Step 13: Reinforcing the Legs
At this point, I thought I was basically home free.
I had just done a test assembly of the table, bolting the legs to the tabletop, and was inspecting my work. During this thorough inspection (which consisted of my pushing and shaking various parts of the coffee table) I found that the table had a little too much “wobble” for my taste. With nothing linking the legs other than the tabletop, the whole thing had a tendency to wiggle around. To help stiffen up the whole assembly I decided to install some flat stock steel between the two legs along the ground. By locking the two legs together at the top and bottom I was hoping to add some rigidity to the whole structure. I measured the distance between the two legs at the top of the coffee table and cut the flat stock steel to the same length.
I then wheeled the welder back out and proceeded to log some more welding practice hours.
By this time, I was basically a welding pro and flew right through this part....
Oh, you didn’t think I was being serious, did you? These welds were possibly worse than my first welds. Still, I struggled through the process and eventually got it done
Step 14: Painting and Assembly
Time to strap on the old respirator and shake up that rattle can, it's paint time!
I sprayed on a quick coat of metal primer and then 2 coats of the finest flat black spray paint Lowes had to offer for $6. I picked black because it’s a nice neutral colour, but my intention is to live with the table for a little bit and then re-think it’s colour scheme in a few months. Maybe I’ll stick with black, maybe I’ll do something crazy and paint it bronze.
With the legs painted and the clear coat dry, the only thing left to do was crank down the nuts on the carriage bolts with a socket wrench. And crank I did, as hard as I could. Well not really as hard as I could, because I might've snapped a bolt, but pretty darn hard! With the bolts sinched down, the only thing that was left to do was to load the table into my truck and take it home!
Step 15: Take It Home and Enjoy
That’s it for this build. This was a long post and if you stuck it out until the end, good for you. I hope you learned something along the way.
Hit me with any questions or comments below. I'm actually thinking about re-doing this project with some design tweaks and making a YouTube video about it (youtube.com/zacbuilds) so let me know if that's something you'd like to see.
And again if you want to be one of the first people to see my next build follow me on Instagram. The link is in the first post. Cheers everyone, thanks for reading!
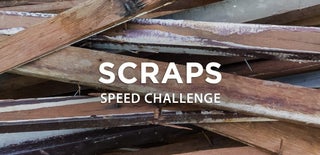
First Prize in the
Scraps Speed Challenge