Introduction: Hex Nut LED Flashlight
For several years I have been planning on doing this project, but it wasn't until now that I actually tried it. My plan was to make a miniature LED flashlight out of hex nuts, using them as the casing. I would use a matching screw as the cap for the battery compartment, and add a keychain to make it easy to carry around.
Here's how I did it.
Here's how I did it.
Step 1: Supplies
Things I used:
- Soldering iron and solder
- Third hand
- Electrical tape (heat shrink tubing would be much more effective)
- Clamps
- Needle-nose pliers
- Two part epoxy
- Super glue (Krazy glue would be better)
- Heavy duty scissors
- Scissors
- 6 18mm nuts
- 18mm bolt
- 20mm nut
- Washers
- White 5mm LED
- Tactile switch
- Switch cap
- Wire
- Ring for keyring (I don't actually know what that is, I just found it in my junk box)
- Small spring
- Positive terminal plate
- 3 1.5V button cells
Step 2: Modifying the Parts
The first part to making the flashlight was modifying the nuts and the screw.
For the nut with the switch, I drilled out a hole that would be big enough for the switch and the cap.
For the battery compartment I also had to drill out the nuts, because even though the cells would have fit inside, I couldn't fit in the insulation.
For the nut with the switch, I drilled out a hole that would be big enough for the switch and the cap.
For the battery compartment I also had to drill out the nuts, because even though the cells would have fit inside, I couldn't fit in the insulation.
Step 3: Button
To attach the switch to the nut I used super glue to glue it in. If you do this, be careful that you don't get any glue on the button itself, or you won't be able to press it in anymore.
Then I attached a wire to one lead of the switch, which would go to the positive battery terminal.
To make sure that the switch stays, in place, I jammed in a small piece of cork (wood or plastic would work just as well).
Then I attached a wire to one lead of the switch, which would go to the positive battery terminal.
To make sure that the switch stays, in place, I jammed in a small piece of cork (wood or plastic would work just as well).
Step 4: Battery Holder
To the white wire connected to the switch I attached the positive battery connector. I made a small hole in the side of the connector to let the negative connector wire through (next step).
To insulate the battery compartment I rolled up a small piece of paper pushed it inside the drilled out nuts.
I glued a piece of paper (insulation) to the sawed off end of the screw and glued a small spring on top of that.
To insulate the battery compartment I rolled up a small piece of paper pushed it inside the drilled out nuts.
I glued a piece of paper (insulation) to the sawed off end of the screw and glued a small spring on top of that.
Step 5: Glueing It Together
I used two-part epoxy to glue all the parts together, but the most effective way to do it would be with silver solder. To let the glue set I clamped the parts together.
For the smaller parts of the flashlight (like the switch, the spring, etc) I used Scotch Super Glue, just because it's much easier to use it on very small surfaces, for details. Epoxy is much stronger, though, so use it whenever you can.
For the smaller parts of the flashlight (like the switch, the spring, etc) I used Scotch Super Glue, just because it's much easier to use it on very small surfaces, for details. Epoxy is much stronger, though, so use it whenever you can.
Step 6: LED
If you're good at soldering and you have a good iron this step won't be a problem. But I have neither, so this step was pretty hard. I was planning on making the LED much shorter than this, but it was hard enough at this length. Make sure that your legs are the wight way around (the longer one goes to the positive wire and the short one to the negative).
To insulate the two legs I used electrical tape. Not a very good choice, but I didn't have any heat shrink tubing.
When you get the LED to work you can glue on the rest of the nuts. To finish it off I added some washers at the front. The washers also hold the LED in place.
To insulate the two legs I used electrical tape. Not a very good choice, but I didn't have any heat shrink tubing.
When you get the LED to work you can glue on the rest of the nuts. To finish it off I added some washers at the front. The washers also hold the LED in place.
Step 7: Done
That's it! There's your nut flashlight.
Even though it works, mines had a loose connection. Here are some potential improvements:
Even though it works, mines had a loose connection. Here are some potential improvements:
- Silver solder the nuts together: This will allow electricity to pass through the wall (nuts) of the flashlight, and will make the whole thing much more durable. That way you won't need to worry about the positive wire (the red one) getting entangled in the spring, and will create a much cleaner finish.
- Use heat-shrink tubing instead of electrical tape: My best guess is that the insulation of the LED is what causes the loose connection. Heat-shrink tubing would make it much cleaner and would probably eliminate any short circuits.
- Use bigger Nuts: Bigger nuts would make everything much easier to work with, and you wouldn't have to drill them out for the button cells to fit inside.
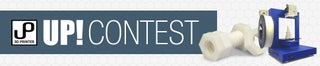
Participated in the
UP! Contest

Participated in the
Pocket Sized Contest