Introduction: HexaGrow Dense Agriculture System for Microgravity
*This project is being submitted to the Grow Beyond Earth contest under the high school category.
There has never been a mission in which astronauts have traveled into interplanetary space. It is inevitable, but before it happens, there are some issues needing to be addressed. There are capabilities we lack, and before the first crew rockets past the Moon, these capabilities must be gained. Among the many problems needing to be solved are radiation poisoning, astronauts' physical and mental health, communication, and food. These are widely considered to be the top five obstacles needing to be overcome for astronauts, and for many, the issue of sustainability stands out. Resources are limited in space, and a key part of sustainability is growing food in space. This Instructable will address the issue of growing plants in space efficiently by maximizing the amount of food produced and simultaneously minimizing the space in which it is grown.
I chose to make this instructable because I am incredibly passionate about engineering the future of the space program, and I saw this as a wonderful opportunity to make a difference. This project has gone from a 3D design to vector files to a real structure, and finally to testing, all to ensure that this design can grow plants in a simulated microgravity both more effectively and more efficiently than any other design having previously been used in space.
Supplies
For this design, the tools needed are:
- Scissors
- ShopBot with 0.25" bit & 60-degree V-Bit
- Miter Saw
- Impact Driver with Phillips Insert Bit
- Driver with 5/32" Drill Bit
- Tape Measure
- Sharpie/Pencil
- 1 1' Irwin Quick-Grip Clamp
- 28 1.25" Cabinet Screws
- 12 1" Cabinet Screws
- 60 #12 x 0.5" Pan Head Sheet Metal Screws, Full Thread, Phillips Drive
For this design, the materials needed are:
- 28 1.25" Cabinet Screws
- 12 1" Cabinet Screws
- 60 #12 x 0.5" Pan Head Sheet Metal Screws, Full Thread, Phillips Drive
- 12 8" drawer sliders
- 4' x 8' sheet of 3/4" oak plywood
- 11ft of 0.5" x 1" Oak Wood
- 4ft of 1" x 1" Oak Wood
- 18 Zip-Loc Bags
- 18ft of 1/4" Clearn Rubber Tubing
- 1 Roll of Duct Tape
- 2 1' x 2' sheets of Rock Wool
- 4 50W Red-Blue adjustable LED Grow Lights
For testing, the materials needed are:
- NutriGrow Plant Solution
- 1 Motor capable of 200lbs of torque or greater (Optional)
Step 1: Choosing an Efficient Design
CONSTRAINTS:
- The design must provide the plants with everything needed to survive (water, nutrients, light)
- The design must fit into a 50cm cube (approximately 20")
The key consideration in this project is choosing an efficient and simultaneously effective design that saves space when growing plants in microgravity. This design revolves around the idea that, due to a lack of gravitational effect in space, multiple rows of plants can be facing multiple directions - even upside-down. In other words, multiple rows of plants can be positioned around one central light, and the plants will grow towards the light do primarily to forced growth direction and phototropism.
This design features a hexagonal prism with plants grown on all interior sides and 4 central lights facing outward in 4 directions. This way, one central light system can supply light to as many as 3 times the amount of vegetation in the same amount of space as the current system on the ISS (this is as opposed to a vertical setup, i.e, plants on the bottom and lights on the top). Why is a hexagonal prism the most efficient?
Using math to calculate interior surface area, the ideal shape for this design can be chosen. For the following calculations, the assumption will be made that plants will be planted in rows, each row is 20" long, 5" wide, and with the plants rising a total of 7" from the bottom of the row. The assumption will also be made that walls of the design are 3/4" thick. The most space-efficient design is a hollow hexagonal prism, providing 6 interior walls for plants to be grown. Each interior wall is 20" x 10", meaning a total of 12 5" rows of plants can be planted. The reason behind this is that a hexagon optimizes the ratio of the number of interior walls to the area of each interior wall. This is also easier to manufacture than a hollow cylinder with infinitely many interior sides.
Image Credit: Geeks for Geeks
Step 2: Refining the Design
A Hollow hexagonal prism may be the most space-efficient design, but efficiency means nothing if the design does not function.
- The complete design details a hexagonal prism, in which there are 6 drawers about a center axis, each of which can be pulled out to allow access to the plants contained in the drawer.
- The 6 drawers will be positioned around two hexagonal endcaps on either end, bound together by a central joist running down the center of the prism.
- Drawer slides will be used to allow each section of the design to be pulled out.
- The entire structure will pivot around the center joist, rolling from front to back to allow access to all pullout drawers.
NOTE: This design is completely scalable. The requirements needing to be met for this competition constrain this design to a 50cm cube, and as such, this is a miniature version of what more industrial-scaled design could look like.
Step 3: Modeling the Assembly
This design can be created from several 2-dimensional cut-out areas, most accurately created via the use of a ShopBot. There are several other parts needing to be made by hand, however. This design requires the following shapes:
NOTE: All areas are cut from the ShopBot from 3/4" oak plywood in this design. However, other materials could be used.
Cut from ShopBot
- 2 Hexagons
- To be positioned on either end of the design
- Outer-circle radii of 8.97"
- 6 Rectangular Pull-Out Walls
- To be positioned around the hexagonal endcaps
- 19.69" x 9.84" base
- Cut on the two longest sides of the rectangle with a 60-degree V-bit.
- Two holes on either end to allow clearance for the drawer slides
- 12 Trapezoids
- To be positioned on either side of the 6 Rectangular walls
- Base of 8.97"
- Height of 3.00"
- A 60-degree taper on both sides
Additional material to be made without ShopBot
- 1 Oak Central Joist
- To run from either end of the two hexagonal endcaps, screwed into the center of each
- 18.12" long
- Cross-sectional dimensions of 1" x 1"
Step 4: Cutting Shapes From the ShopBot
The attached Aspire file contains all shaped to be cut by the shopbot. All 20 shapes are arranged on a 2' x 8' Oak Plywood sheet (a 4' x 8' sheet cut in half down the middle).
Aspire File Attached Below
- Use a 30-degree V-bit for the indicated vectors on the file
- This bit will be used for 12 cuts (the 12 vectors referenced are the two longest sides on each of the 6 rectangles
- Use a 0.25" bit for all other vectors
When all 20 pieces are cut out, sand all cut sides.
Attachments
Step 5: Cutting Shapes by Hand
Now, there is only 1 additional shape to be made, without the use of a shopbot.
- 1 Center Joist
The 1 center joist can be made by taking a small Oak beam, 1" x 1" in cross-sectional area, and cutting to 18.12" with a miter saw. Cut on the outer edge of the marked line, leaving a beam just over 18.12"
Sand all cut sides (This will account for some of the extra length from the cut).
Step 6: Assembling the Main Structure
The Main structure of this design requires the following materials:
- The 2 Hexagons
- The Center Joist
- 4 1.25" Cabinet Screws
- Sharpie
- Impact Driver with Phillips Insert Bit
- Driver with 5/32" Drill Bit
- Grab one hexagon, measure its center (7.75" from two opposite sides of the hexagon), and mark with the Sharpie.
- With the 5/32" drill bit inserted into the driver, drill two pilot holes into either side of the center mark on the hexagon, 0.5" apart from one another. Repeat for the other hexagon.
- Grab the center joist, position vertically on the ground, and set one hexagon atop it. Center the two pilot holes above the joist.
- With each hole positioned squarely above the joist, extend each pilot hole by another 0.25" into the joist.
- Next, grab the impact driver with the Phillips insert bit, and drill 2 1.25" cabinet screws into each pilot hole, sinking each screw
- With the joist and 1 hexagon attached, flip the structure 180 degrees, so that the hexagon is on the ground and the is joist extending vertically into the air.
- Repeat steps 1 - 5
The main structure has now been completed. Next, the drawers will be assembled and inserted into this main structure.
Step 7: Assembling the Drawers
The 6 drawers of this design require the following materials:
- The 6 rectangles
- The 12 Trapezoids
- The 12 Drawer Slides
- 24 1.25" Cabinet Screws
- 24 #12 x 0.5" Pan Head Sheet Metal Screws, Full Thread, Phillips Drive
- Impact Driver with Phillips Insert Bit
- Driver with 5/32" Drill Bit
- 1 1' Irwin Quick-Grip Clamps
- Position 2 trapezoids upside-down (with the top down), approximately 1.5 feet apart. Place one of the rectangles the upside-down (with the taper facing downwards) atop the two trapezoids.
- Position each of the two trapezoids squarely underneath the rectangle, so the 60-degree cut of the rectangle continues smoothly to the 60-degree taper of the trapezoids. Let each trapezoid underneath the rectangle sit 1.25" from either edge of the rectangle, so as the edge of each trapezoid is flush with the edge of each of the cut-out holes in the rectangle. Clamp the center of the rectangle to the table.
- With the 5/32" drill bit inserted into the driver, drill 4 pilot holes into the 4 corners of the rectangle, 2 on either side of the rectangle, each positioned above either end of the trapezoids.
- Drill these holes through the rectangle, and approximately a quarter-inch into the trapezoids.
- Next, with the Phillips insert bit inserted into the impact driver, drill 4 1.25" cabinet screws into each of the holes, sinking the drill head.
- With the 2 trapezoids now securely attached to the rectangle, unclamp, and flip over 180 degrees.
- With the drawer sitting flat on a table, take one of the 8" drawer slides and align vertically up against one of the trapezoids. Align in the center of the trapezoid, with the smaller side of the slide facing up against the wood surface. Let the slide sink into the cut-out hole in the rectangle, so as the make the bottom of the slide flush against the table.
- Extend the drawer slide in place, so as to make visible the screw holes visible. Use the impact driver and 2 of the 0.5" pan head screws to screw the drawer slide to the trapezoid. With the drawer slide attached to the trapezoid, collapse the slide.
- Repeat steps 7 - 8 on with the other trapezoid.
- Repeat steps 1 - 9 for the 5 remaining drawers.
Step 8: Attaching the Drawers to the Main Body
Assembling all components made in the two previous steps requires the following materials:
- Main Body
- 6 Drawers
- 36 #12 x 0.5" Pan Head Sheet Metal Screws, Full Thread, Phillips Drive
- Impact Driver with Phillips Insert Bit
The following is a tricky task, and as such, precision and caution must be followed.
- Position the main body vertically, with one hexagon on a table and the other in the air
- Take one of the drawers, position vertically, and slide into the main body. The drawer should not move.
- Align so that the edges of the drawer line up with the edges of one side of the hexagon.
- Apply great pressure to the drawer slide, pushing it against the hexagon on the table, and slide the rest of the drawer out. If the drawer slide moves while doing this, reset and try again.
- With the drawer extended out and the drawer slide in the correct position on the hexagon, use the impact driver and 3 0.5" pan head screws to secure the drawer slide into the hexagon. Pilot holes are preferred, but not necessary.
- Flip the whole structure 180-degrees and repeat steps 1-5.
- With one of the drawers attached, slide the drawer back into the main body.
- Repeat steps 1 - 7, until all 6 drawers are attached to the main body.
When done correctly, the ends of each drawer slide will form a perfect hexagon around the base of the center joist.
Step 9: Attaching Lights to the Assembly
Materials Needed:
- 4 Red-Blue LED Grow Lights
The lights used, MICX LED Lights, have adhesive backings that allow for easy attachment to surfaces. Four of the lights will be attached to each side of the center joist with adhesive, the cords being fed out through the ventilation gaps in the Hexagon. Any LED lights can be used so long as they are manufactured in lengths, not arrays.
Step 10: Testing
Now that a space-efficient design for growing plants in space has been created, it is time to ensure that plants can, in fact, be grown in it.
Plants need four key things to survive:
- Light - Provided by the lighting in the design
- Space - Provided inherent of the design
- Water & Nutrients - Provided with nutrient solution
- Soil - Provided by Planting Pouches
The plants used in this testing is Dinosaur Kale. Currently on the International Space Station are "planting pouches" - small pouches of soil that allow plants to be grown and watered in microgravity while simultaneously containing the soil in one finite space. This is a simple yet wonderfully efficient solution to growing plants in space, and as such, this design allows for these planting pouches to be used. As duct tape is a product with many uses, even on the ISS, it was used to secure these planting pouches to the inner walls of the design.
As for the watering of the plants, 1/4" rubber tubes were looped throughout strings of these planting pouches, and a 100mL syringe was used for watering. Three planting pouches were attached to each other in a line, rubber tubing fed through the root systems with holes cut, and each set of three plants was placed on each interior wall. 50mL of NutriGrow nutrient solution were given to each string of three planting pouches every 24 hours, to ensure proper nutrition across the duration of the entire experiment. This system of watering is similar to that used on the ISS. This design was created for easy assimilation into the ISS, using very similar methods of plant maintenance.
Convection, airflow, and heat transfer from the lights can all have an indirect effect on how the plants grow. Thus, it is imperative that these qualities in the test also be recorded. The setup and execution of the experiment are detailed in the following steps.
Step 11: Germination Preparation
To begin this experiment, plants must first be germinated. Before this can happen, however, the germination environment must be prepared. To begin, arrange 18 (or more if preferred) cubes of rock wool in a small rectangular dish, face up.
- Next, PH Up and PH Down must be used to adjust 500mL of deionized water to a PH level of approximately 5.
- Once this PH level is reached, the solution can be poured over the top of the rock wool cubes in the tray. The rock wool must soak up the solution for one minute.
- Afterward, any liquid in the tray can be poured down the sink drain.
Step 12: Germination
- Once the rock wool has been prepared, use tweezers to open up the pre-made holes in each of the cubes,
- Next, use the tweezers to place 2-3 Dino-Kale seeds into each hole, letting them fall to the bottom.
- Lastly, use the tweezers and pinch each hole approximately halfway closed.
Once this germination has been completed, the tray of rock wool can be left under grow lights or outside a window until testing.
Step 13: Growth
After 2-3 weeks of growth, the plants should have grown to approximately 2-3 inches tall. By about week 4, the plants will be ready for experimentation. Watering procedures for this experiment included pouring 200mL of nutrient solution into the tray every three days. This tray was also kept by a window and under a grow lamp for the duration of the growth period, for optimal UV exposure.
Step 14: Transferring Plants
From the germination tray to the planting pouches, the plants must be carefully transferred into Ziploc bags. The materials needed in the following steps are:
- 18 Ziploc Bags
- 18ft of 1/4" Rubber Tubing
- Plants
- Scissors
- Duct Tape
- Rock Wool
Step 15: Planting Pouches
With the plants now large enough for experimentation, (after approximately 4 weeks), they must be transferred from growth in the tray to growth in planting pouches. In order to accomplish this, some short steps must be followed.
- Rip a small hole (approximately the size of a half-dollar) in the side of a Ziploc bag, making sure not to puncture both membranes, only one.
- Place the plant's rock wool base through the hole.
- Stuff the Ziploc bag with excess rock wool (crushed and separated) around the base of the plant.
Step 16: Planting Pouches and Watering Tubes
After each Ziploc bag has been stuffed with plants and excess rock wool:
- Use Duct tape to secure any holes in the Ziploc bags, such as the one made, and the large opening at the mouth of the bag.
- Fold around any areas of the bag that have loose space, and duct tape.
- Now with compact planting pouches, they can be placed together in 6 rows of 3.
- Next, cut 6 segments of 1/4" rubber tubing to approximately 30".
- Thoroughly duct tape one end of the tube, so as to prevent any fluids from coming out of it.
- Make 3 holes at 4" intervals, starting at the end of the tube just recently duct-taped.
- With force, push the end of the tube with Duct tape through the middle of a set of 3 planting pouches. Make sure to align each hole with each planting pouch as accurately as possible. Secure the tube in position within the string of 3 planting pouches with duct tape.
- Repeat steps 4-7 with the last 5 rows of 3 planting pouches.
Now with 6 sets of 3 planting pouches, one for each interior wall of the design, they can be incorporated into the experiment.
Step 17: Incorporating the Planting Pouches
Once made, place each set of three planting pouches in the middle of each interior side of the hexagon, and duct tape into place on either side. Ensure that the tubing sticking out of the planting pouches reaches outside of the design, for easier watering.
Duct tape was used to secure the planting pouches in place in the experiment for ease of addition and removal. Further iterations of this design will involve integrated hexagonal drawers, in which these same watering tubes are built into each drawer, out of each hole in the tube protruding a small plastic nozzle. The sides of each drawer will be build upwards and inwards, turning each drawer into a trough. Planting pouches can then be slid into this trough from either side, with holes in the bottom of each for receiving the watering nozzle. Plans for this design have already been made, and remaining grant funding will be used to see it through in the coming months. For the purposes of design testing, this system of planting pouch integration is functionally identical.
Now with the plants incorporated into the design, the experiment can begin.
Step 18: Testing: Results
Throughout the duration of the experiment, the lab was rotated 1/6th of a turn every hour during the day. Dually, a 200Lb capacity Rotisserie Motor could have also be used to rotate this structure constantly. However, due to concerns of the institution at which this research took place, the North Carolina School of Science and Mathematics, the rotisserie motor was not allowed to be used. A stand was created, a motor purchased, and a rounded central axle installed into the design. Further continuations of this research may incorporate this motorized rotation, but this experimental trial detailed manual rotation. However, this process was still effective at exposing each string of planting pouches to gravity in different directions.
Additionally, each string of 3 planting pouches was watered with 50mL of NutriGrow solution every 24 hours with a syringe, as is done on the ISS. The red-blue lights remained on for the duration of the experiment.
The plants used in this experiment were approximately 4-weeks old, to allow for edibles leaves to be present in the experiment. Already Germinated plants were used in this experiment as it is more difficult for plants used to gravity in one direction to then be exposed to gravity in varying directions. Because of this, it is easier for plants freshly germinated in the design to adapt. Despite this difficulty, the plants thrived. Throughout February 2020, further testing will be done with freshly germinated plants.
Results
After 30 days of this experimentation, the plants grew very well, maintaining structure and vitality. Fully grown leaves were cut off the plants before they came into too close contact with the grow light and shriveled. These leaves were even eaten after harvest. Root structures grew stronger after having been grown in this design (a side effect of gravity), but this is irrelevant as this will not be the case in a microgravity environment. Stems and stalks were slightly weaker than they had been before transfer into the design, due to gravity acting on each plant in six varying directions. However, the plants remained growing in one direction for the one-month growth period. Again, this will not be the case in a microgravity environment as there will be no gravitational stress to have an effect on the plants. When in microgravity, freshly germinated plants in this design will sprout towards the light, and continue to grow in such fashion.
As each plant experienced varying gravimetric conditions, a simulation of growth on the ISS was achieved in this experiment. Thus, if sent to the ISS, a dense agriculture growth system like this design could prove to be very effective.
Step 19: Implementation
With an extended central axle and a surrounding infrastructure to receive this rounded axle on either side of the hexagon, this design could be rotated around 360-degrees in a 50cm modular space. By feeding the wires through the central axle and being received by a rotating electrical adapter, this implementation will be successful. Once the experimental period ended, at which time remained excess institutional funding and excess time, this implementation was tested and found successful. However, this is irrelevant to the primary design, as an implementation of this design in space will be very different than on earth.
Step 20: In Conclusion
The purpose of research and experimentation is not to redesign something that already works well, but to add to and advance it in the areas in which it doesn't. Plants can currently be grown in space, and with great efficacy, but not necessarily great efficiency. In the coming years, more and more plants will have to be grown in the same amount of space to satisfy the growing demands of astronauts aboard long-duration missions.
Astronauts have limited space to live and work aboard the ISS, and currently, plant environments are small, modular cube-shaped spaces with light at the top and plants on the bottom. This is by no means the most space-conscious design. This project can easily fit into one of these modular spaces and allows for three times the amount of plants to be grown in the same amount of space that is currently alotted for vegetation on the ISS. As such, this design is a prime candidate for further research and development, as it can effectively and efficiently grow plants in microgravity environments.
Image Credit: NASA/Fairchild Gardens Grow Beyond Earth Contest
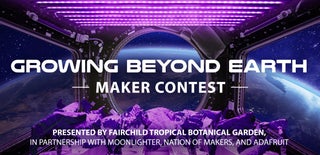
Third Prize in the
Growing Beyond Earth Maker Contest