Introduction: Hickory and Walnut Jewelry Box
I made a hickory and walnut jewelry box for my daughter Mimi for her 13th birthday (which was last week).
Outside dimensions of the box proper are 6”x10”x3.5”. Wall thickness is just under 3/8”. The Lid and bottom are 1/4" thick and overhang the body of the box by about 3/8" all around.
This is my second jewelry/keepsake box and the first time I’ve used hickory. I found hickory somewhat difficult to work – prone to burning easily and some chip-out issues; but, I was able to overcome most of those issues with smarter cutting and a lot of sanding.
Supplies
Materials:
- Hickory
- Walnut
- Glue
- Stain
- 2" Hinges (It may take some hunting to find hinges that are not too deep for the thickness of your stock. In future, I will buy the hinges first, to ensure I don't build box walls too thin to use the hinges I have available.
Tools:
- Table saw
- Band Saw
- Router
- Clamps
- Belt Sander
- Random orbital sander
- Sanding blocks
- 80, 100, 220, and 400 grit sandpaper
- Chisels
Step 1: Making the Top and Bottom
The hickory came from one 6’ 1×4. The walnut was salvaged from an old bed frame.
One of the attributes I wanted in the box was to incorporate book-matched grain to present the “M” pattern in the hickory board for the top, for my daughter's first initial. After selecting the section of hickory I wanted for this, I cut the section out using the miter saw. My small bandsaw has a maximum resaw of 3-1/8". so, I had to trim the hickory to fit under the blade guide using the table saw.
For any who have not worked with hickory, this is a very hard wood - used in baseball bats and axe handles, I had never really considered making anything decorative from it, and honestly don't recall knowing anyone who had. (I've since learned there are many).
I don't have a jointer or planer; I most times will use my router when I need one of those. That was the case with the two halves of the top and bottom, I ran the two long sides through the router using a fence, to create square and straight edges and then glued up the two pieces (each).
I trimmed off a 1/4" x 3/4" piece from the walnut bed frame, to sue for the framing, This worked out pretty well as the hickory was just shy of 3/8 when I was done resawing, then flattening the glue-up and sanding out the band saw marks brought hickory to right around 1/4" thick. I then set these pieces aside while I went to work on the box.
Since this step is about the top and bottom, I'll skip ahead in time to complete these parts.
After I had finished the glue up of the box body, I was able to get the final dimensions for the top and bottom - I wanted about 3/8" of the walnut showing around the base. With the walnut strip being cut to 3/4" wide, I needed to trim the field for both top and bottom to provide that reveal, that meant trimming the hickory so that it would just fit inside the box.
Framing the hickory top and bottom with walnut was pretty straight forward - remember if doing this to dry-fit continuously and make incremental "micro-cuts" to sneak up on the perfect fit. My glue-up included putting 90° plastic L jigs in opposite corners and clamping down all four sides at once.
Now to the sanding. The band saw left some serious marks in the hickory (and a few burns)
When I edge glued the top, my "M" was stunning, I thought this is going to be perfect. Then after sanding, I realized that the material removed was enough to mess up the aesthetic a little. (I know I need a better band saw and better re-saw blade with fewer tpi.).
A lot of sanding later and the top and bottom were nearing completion. I'll admit I resorted to using the belt sander on the hickory, the random orbital sander was excruciatingly slow with wood this hard. Because the belt sander is so aggressive, I may have removed a bit more material than optimal; but, I think it was a decent trade for time.
I wanted to ease/round the edges of the top/bottom; but the smallest quarter round router bit I own wouldn't work, due to the thinness of the material. My solution was to build a sled to hold the panels vertically for routing, rather than run them horizontally on the router table, allowing the guide bearing to do it's job. (I know this isn't a picture of the lid and isn't the right bit; but, you get the point).
Step 2: Making the Box
The box itself is 6"x10"x3-1/2" - not too big and not too small for a dresser..
I wanted to see if I could wrap the grain al the way around the box' so I took a guess as to how the ends of the section of board I was going to cut would match.
First step was to resaw the 3/4 board to 3/8", I opted for the table saw for this one, I set the fence to 3/8, then went to work pecking at the center-line of the board, making multiple relatively quick passes with about 3/4 inch of material being cut with each one. Reasons for this include: the saw blade gullets cant' handle too much material and making deeper cuts slows down the feed rate, increasing contact time for the wood and blade resulting in excessive burning.
I had a bit of trial and error with this wood...
After resawing, I moved on to the miter saw. After determining which side I wanted to the outside, I cut a 45° on the end and then the at the 6" mark (here realizing I had reversed my sides somewhere and out was now going to be in). After cutting the first 6" piece, I reversed the board to cut the matching corner for the 10" front - this removed little more than the kerf and continued this around the box.
After aligning and gluing up the body of the box, I decide to try another first for me and to put splines in the corners. I had seen a number of jigs for spline groove making, and put one together in about a half hour. I made it to push with my miter guage and align with the left edge of my saw table.
My splines were going to be simple for this one, just the width of the saw blade. I found the 1/3 mark for all 4 corners and marked them with pencil. The pencil mark are visible through the cut out in the jig made by the blade, aiding alignment. (I suppose I could have clamped on a stop too, that didn't occur to me at the time.)
I cut a thin strip of walnut, just wider than the kerf to insert as splines. these I hand sanded until they fit snuggly, then glued them in place. when the glue was dry, I used my chisels to remove the bulk of the extra walnut, working to get one side smooth with sanding, then took the other sides to the router and flush cut bit.
At some point, I managed to chip one of the corners, so I decided to run the box corners through the same round over bit used on the top and bottom.
Following some initial sanding, I glued the box to the bottom panel.
Step 3: Interior
Inside the box I place a 1-1/2" x 1/4" end cap on both ends to hold up the tray. The tray is constructed of 1/4" x1-1/2" deep frame and bottom with 1/8" dividers. The bottom was glued up from the cut-off from resawing the sides. The frame is lap jointed and the dividers are butt jointed (They should hold as long as she doesn't force something into the compartments.)
I lined the bottom half of the interior of the box with 5 individual pieces of felt (four sides and bottom), and used individual felt pieces to line the sections of the tray.
The stain is Minwax Wood Finish in Golden Pecan. I applied the stain and wiped back off within 2-3 minutes, to bring out the grain but not darken the box too much – two coats.
Step 4: What I Know Now That I Didn't Before Starting the Project
I'm pretty pleased with this box, and so was Mimi. I think this came out about as well as my tool set would allow.
Making this box really emphasized my need to replace my table saw (ancient 9” Craftsman) and band saw (Ryobi with max resaw of 3-1/8”), and maybe most critical is getting an electric planer – thicknessing with a belt sander is dicey.
Make sure you have the hinge size you need or size the project to the hinges you have. They can be hard to find in small sizes and can take some time you hadn't planned if you need to order them.
The hinge screws were longer than the thickness of the top and had
to be cut down – I tried to find replacements; but no store near me carried #4 screws with heads that would countersink. Next time I’ll get hinges with a 95° stop.
I am far better off using the router to recess the hinges than cutting by chisel, I find it hard to get flat and have issues with chip-out.
Thanks for checking my project out.
- Horus
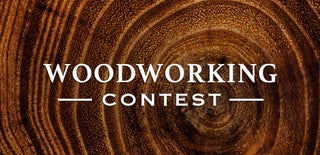
Participated in the
Woodworking Contest