Introduction: High Trestle Table - Including Prototype Table
Tools used
- Miter saw
- Drill
- Chisels
- Planner
- Router
- Block Plane
Materials Used
- 18 mm Birch plywood
- 100 mm x 44 mm white deal
- Handful of screws
- Wood glue
- Clear satin water based varnish
Step 1: Trestle Legs
The trestle legs material I used was standard planned 100mm x 44mm (4 x 2) white deal wood. This was readily available from the local building suppliers. As you can see from the design sketches, both ends of the legs required a compound miter. These 2 angles (82 degrees and 76 degree - see sketches) is all that is required to prepare the legs for the tables. The angles required to make the cuts is 14 degrees with the head of the saw tilted at 8 degrees
Step 2: Centre Brace
All solid wood is white deal. That's the beauty of these tables, all material used for the trestle frame is readily available to everyone and most importantly affordable. All that is involved is to cut a halving joint 100mm from each end of the trestle centre brace
Step 3: Table Top Supports
Next up for cutting is the table top supports. These supports will house the legs. A halving joint cut into the centre of the supports will mate with the halving joints cut earlier in the centre brace. There was further notches cut to house the tops of the legs. These were straight cuts with the saw head tilted to 14 degree. All halving joints were machined using the dewalt miter saw to half the thickness of the white deal (22mm). All those notches and halving joints will look a lot clearer in the next step when I start the assembly.
Step 4: Trestle Assembly
This step I hope will make everything very clear. The halving joints cut in the centre brace and table top supports fit nicely together with a tap from a hammer!!! I glued and screwed this joint together. Next up was the assembly of the legs. When it comes to screwing the legs in place, it is important to screw in the direction of the leg and not perpendicular to the table top supports. This is because the 100 mm screws used would penetrate the side of the legs if they were screwed perpendicular to the table top supports. I find it best to drill pilot holes in the direction I would want the screws to intersect both parts being assembled.
Step 5: Reinforcement Plate
A birch plywood plate was needed to reinforce the trestle table legs and to prevent them from splaying outwards. This was secured in place using 6 screws (5x50mm screws). This plywood plate not only prevents the legs from splaying apart but prevents both sets of legs from splaying along the table length also. This is achieved when it is secured up against the centre brace. A drop of glue during this reinforcing makes a very strong trestle frame.
The table top I decided to go with was birch plywood. This again is readily available from the local builders suppliers store. I used 18mm birch plywood. This was cut to 2000mm long to 900mm wide(sorry for using millimeters - I find it best and most accurate). I didn't do much more to it only to sand any sharp edges by hand.
Step 6: Secure Table Top and Finish
The table top for the prototype table was secured to trestle frame using 5 X 50mm screws. Over all I was happy with how the table turned out but I felt it needed improving in a few areas. How would it react to constant use? People leaning on it with their laptops, lunch, etc. Also could I make it look more elegant? Two of these prototype tables were made and placed in a breakout area with our office space.
Step 7: Trestle Table Improvements
I was quite pleased how well the prototype trestle tables turned out and how sturdy they felt. However they looked like prototypes. They still looked like stretched out trestles you would see on a building site. I decided that the best way to make any improvements and to make them more elegant was to improve aesthetic look of the table top and to eliminate or reduce the table top support in some way.
I could not afford to reduce the thickness of the table top material so I went about creating a feathered edge reducing to 6mm (1/4inch) to the table edge. This was achieved by securing a 6mm rip of plywood to the work bench and using this as a depth stop to run my planner along. The 6mm plywood rip would prevent me from removing any material below this line. Remember to choose the clean side of the birch plywood for the tabletop surface. Therefore do not plane the feathered edge on this clean knot free surface.
Final clean up of the feathered edge was carried out with a block plane and sanded.
Step 8: Hidden Table Top Supports
With table top reduced to what looks like only 6mm, I had to come up with a new way of supporting the top and securing to the trestle frames. I could not use the previous supports as used in the prototype tables. They would look horrendous. My only option was to use some steel. 1 piece to be secured along the centre brace and 2 lengths to be welded across to act as the supports for the table top.
A router was used to accommodate the steel into the centre brace of the trestle frame. This was secured in place with screws which would all be hidden with the table top in place. The construction of the trestles this time around did not require any halving joints as I had no wooden table top supports so it reduced the work load to screws. As you can see the construction was somewhat different but is very obvious from the pictures.
Step 9: Securing Table Top to Trestle Assembly
Having welded the supporting steel as a lap type joint, I had to router the steel table top supports in to the table top. The trestle frame was them screwed to the table top through the pre drilled holes in the steel.
Two coats of a clear satin varnish was applied to the tables.
Step 10: Tables in Place
I hope you have enjoyed this instructable and that it has inspired and given an insight into what can be made from readily available cheap building material. The over all project took me 2 days in total. You can not underestimate the importance of prototyping as it showed me really quickly how to improve on my design both structurally and aesthetically. Thanks for reading........
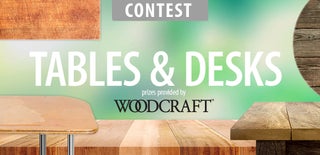
Third Prize in the
Tables and Desks Contest 2016