Introduction: Home-made Robot Wheel
Hello every one........
I love creativity. Every people have their on creativity. But in reality only 10% of the people found their creativity. Because they take the easy path. Creativity is a thinking ability, it develop by experience, observations etc... For example, When we trying to make a simple robot, we search the pre-made parts for it (online, hardware shop). That is, we only done the assembling part. That is, we hide our creativity. Most of the people like this. But i don't like it. Because it will destroy our creativity. So here I am trying to make a robot wheel by using easily available items. By this way we can increase our creativity. So, I wish that, it will help you to take the true path in your journey.
I repeatedly tell that CREATIVITY is the most wondering thing in our world. Try to increase it. Definitely it will help you great in your future. So stay creative.
Here I am making a robot wheel using PVC and some screws.
Step 1: Wheel Plan
Here I explain what are the wheel parts and how arranging it. The wheel arrangements,parts and material needed are given in the figures.The wheel have an outer rim, rubber Tyre is fitted to it. Here it is made by a 4" PVC pipe. The spokes ,which is used to connect the rim and the hub. Here it is made by long screws. Then an inner rim is used to strengthen the whole thing. It is then connected to the hub by small screws. The hub is the center part, which is connected to axle. Here the axle is a small PVC pipe.In the axle 2 gears are connected at each wheel to coupling the power from the motor. It is made from a PVC end-cap. Here only PVC and screws are used to make the wheel.
Outer Rim - 4" PVC
Inner Rim - 2" PVC
Hub - 1" Coupling
Spokes - Metal Screws
Axle - 3/4" PVC
Gear - 1"PVC end-cap
Step 2: Materials & Tools Required
Material
The material used here is found in garbage or also available in any hardware shop. All expenses are less than 100 Indian rupees.
PVC pipe :: 4" - 1/2 feet
2" - 1/2 feet
1" - 3/4 feet
3/4" - 1/4 feet
PVC coupling:: 1" - 2 nos.
PVC end-cap:: 1" - 2 nos.
Metal Screws:: 1.5" - 48 nos.
3/4" - 24 nos.
Tools
The needed tools are given in the figure. The tools are not mandatory because it is your commonsense. Right tool for each job is fixing by you. OK. So, in the absence of any tool don't upset. Use the appropriate tool in your toolbox for that work. OK. Limited resource is boost your outcome. So take it silly.
Step 3: PVC Cutting
The PVC is cut by using a hacksaw blade. First mark the appropriate length using a metal ruler and permanent marker. Then cut through the marking. Do not apply extra force to the blade because it cause blade to snap.
- Mark 5 c.m. in the 4" and 2" PVC pipes in two times
- Cut through the markings by using hacksaw
- Obtain 5 c.m. length 4" and 2" PVC of 2 pieces each
- Mark 3 c.m, 3 c.m., 16 c.m. in 1" PVC
- Cut through the markings
- Obtain 3 pieces of PVC
- Clean the edges of the PVC using the hacksaw or knife
Step 4: Drawings and Marking
We prepared the material for the construction. Now we start the work. But before it we need some drawings to align the spokes correctly. The spokes are screws. The plan is that, drill some holes on the outer ring (rim) and it is screwed to the middle ring. Then drill some holes on the middle ring and it is screwed to the inner ring (hub). For this we mark the drilling hole correctly on the PVC. For this we use a drawing. For drawing compass and pencil. Steps are given below.
- Take one A4 sheet
- Draw 6", 4", 2", 1" circles with same center by using compass and pencil
- By using protractor draw the angle lines given in the figure
The drawing is over. 2 rows of spokes is used here. In the outer ring 24 screws in 2 rows is used. So 360/12=30 degree apart each screw. In the middle ring 3 rows of 4 screws is used. Each screw is 45 degree apart. So now we mark the hole position in the 2 PVC (4", 2") and in the 1" coupling. The marking procedure is given in the figures.For marking the correct alignment of PVC with the drawing is important(PVC inner diameter aligned to the drawing).
- Outer ring PVC has total 24 hole marking, each 30 degree apart
- Middle ring has total 24 (2 rows with 30 degree) + 8 (2 rows with 90 degree apart) + 4 (1 row with 90 degree apart) hole marking
- Inner ring has 8+4 hole markings
- MARKING PROCEDURE IS CLEARLY GIVEN IN THE FIGURES
- All PVC is aligned in the same manner as the outer PVC
Step 5: Drilling of Holes
Drilling is done by hand drilling machine. But I don't like it, because for beginners it is not good. So here I am explain another way without using power tools. The hole position is already marked. The hole drilling size is given in the figure. Hole making is a heavy work because large no of holes are needed. But I believed that it is a very good experience. The drilling steps given below.
- Burn a candle
- Put a small screwdriver or similar sharp edged object in the flame
- After some time stabbed it to the PVC in the marking
- If got a hole , follow same procedure for other holes
- The obtained hole is very small, So it is enlarged by an old scissor rotating in the hole
- The obtained hole is cleaned and finished by using a small knife
- Similarly done all the holes
The finished work is given in the figures. The hole size is important , read it carefully
Step 6: Gear Making
The gears using PVC???? It is very interesting. If you are completing it well, you will definitely done the basis of gear making process. It is little bit harder and time consuming than other steps. It need well concentration through out the process otherwise failures happen. Our plan is that first fix the gear teeth number, then draw a circle with gear radius and divide the total 360 degree into gear teeth number. Then mark the points into the gear and complete the gear cutting. First you see the figures and and understand it well. I need the steps given below.
- For gear making we use an PVC end-cap (edged cap is needed(see in figure)). One of its end is closed so cut into hollow by using hacksaw.
- Fix the gear teeth number as 36. So, draw a circle with radius of end-cap and divide it into 36 parts(1 degree)
- Correctly align the end-cap and mark the divisions
- Then by using a hacksaw cut the markings into a small depth of 3 m.m ( here given in the larger PVC because I loose the pictures of end-cap work, so you definitely done it in the end-cap)
- After cutting all the grooves, the obtained teeth are in rectangular shape, it is changed to triangle by using a small file (3 corner file). Done it carefully otherwise damage the teethes
- Then clean it by using small knife
- Work is completed, gears are obtained, 2 gears are needed so do same in the other end-cap
Step 7: Assembling
Assembling is not a hard one. It is simple. The steps are given below. all are given in the figure.
- Take the finished parts, screws and a screw driver
- By using the 3/4" screws connect the PVC coupling and 2" PVC by 12 screws for each set
- Arrange the coupling at the correct center and not too much tighten the screws
- Then connect the 2" and 4" PVC using the 1.5" screws.
- Keep the 2" PVC at the center
- Now the wheel assembling is over. Now connect 1" PVC to the coupling and in the other side of the PVC gear is to be connected
- Now connect the 2 wheel together by a 3/4" PVC. It is its axle. In this case, take care about that the wheel are freely rotates in the axle
- Completed the wheel assembly
But there is a problem, the wheel are not fitted in the axle, they just coupled. So how fix it ????
Find best solutions.
I give an answer in my next part of robot making. This is the first part. OK.
Step 8: Conclusion
Finally a good quality robot wheel made at home. From this we conclude that Engineering is not a single method. Each people can find there on methods. I believed that it is useful for you. If anyone think that it is useful for me, please reply to me.
This is not a full project. It's second part is coming soon. In that I will connect the whole thing to a chassis and motorized it.
See you again................
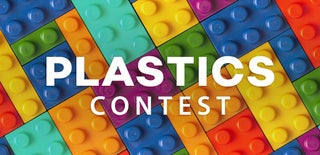
Participated in the
Plastics Contest