Introduction: Homemade CNC Router Build
Hello and warm welcome to all instructables community...............
If you like our project than please don't forget to vote,Share & follow me for more projects.The total cost of this build is around $550.
So this time I presenting my Seventh project which is a CNC router machine in front of you.
This is the toughest project for me among all of my previous builds and also consumes my lot of money and time, but the end result brings a huge smile on my face when I saw the complete build. I have never made any CNC machine ever and even didn’t make any project regarding electronics. When I saw the end result I have no words to express that moment. I think a person who dreamed to have a CNC made by himself, taught by himself can understand my feelings.
The whole build journey of my CNC have many ups and downs. I have a little bit knowledge about CNC machine like how they work, what are the things needed to make a CNC machine, what type of parts used to make a CNC machine. Before starting this project, I know that this is very difficult project for me but even than I took a risk to build my own CNC machine because its my dream and I want to fulfill it at any cost.
Before started building this machine I research a lot at you tube, watch many CNC builds videos and all of them are of different designs and dimensions. So rather than coping them I decided to make my own design which makes me comfortable during my build and because of that I used wood rather than metal to make my CNC.I know it have a disadvantage that it absorb moisture and deform time to time but it’s easy to work so I Decided to go with it because I have to paint it in my own color theme which will definitely prevent moisture absorption.
The overall cutting area of my machine is 760 mm X 670 mm X 180 mm.
During this build I damaged some of my electronics parts. I hope you can learn some important things from my project and prevent accidental damage to your electronics component. During the frame build I also do mistakes many time but I used wood for my CNC build so didn’t bothered me anymore. If you are using metal than be careful while making arms design and gantry because in my case I make many mistakes while makings gantry and arms these needs to be rigid because complete machine depend upon this gantry arm. During this project tour I show you my mistakes and also the improvements you can made with your machine.
Step 1: Basic Concept and Design
A CNC router (Or Computer Numerical Control router) is a computer-controlled cutting machine in which hand held router used for cutting various hard materials, such as wood, aluminium, steel, plastics, and foams etc.
There are basically five different types of CNC machines:
1. CNC Plasma Cutting Machine.
2. CNC Laser Cutting Machine.
3. CNC Milling Machine.
4. CNC Router Machine.
5. CNC Lathe Machine.
Although plasma & laser cutting CNC looks similar but the differences between plasma,flame and laser cutting. CNC Flame cutting machine: it is a type cutting equipment that use gas with oxygen or gasoline in metal materials with oxygen cut. Laser beam to the work piece surface, reach melting point or boiling point.in laser cutting most of case CO2 laser used.
I made CNC router machine whose basic concept is similar to milling machine.it has vertical machining center having movements in 3 directions x, y & z. A hand held router is attached to its Z axis which is used for doing machining.
For the movement in X, Y & Z direction I used 12mm ball screw + ball nut, 16mm linear road and linear barring’s and stepper motors. There are also some other methods you can use for the movement of your axis. Rather than using ball screw you can also use belt driven method, you can also use rack and pinion method for the movement of your axis. You can use these alternate methods for large area CNC and even for small area CNC. Main disadvantage of ball screw is that it comes in fixed length and difficult to find it in longer length more than one-meter.
Stepper motors comes in different shapes and sizes and also they have different torque. In my case I used nema 23 stepper motors which generates 10kgm torque to run my machine and the board I used to run the motors is 3 axis driver board TB-6560.It is a chines board which alone is able to run all motors. For the power supply I used 24v dc power supply.
For design purpose you can use any type of design according to your imagination or you can find bunch of design on google but here i posted my own design.The CAD file contains all axis drawing including holes position.Unfortunately I lost my sketchup file which include all data which I used in CNC making but i posted some images showing you all the detail.If you have any doubt I am always feel happy to help you.I hope drawing clears your questions
Attachments
Step 2: Mechanical Material & Hardware Used
I purchased my material & Hardware from Aliexpress.com.here you can find every item at very low cost.before ordering any item from Aliexpress first check your local hardware store, may be you could get these hardware at cheap price in your local hardware store.
Here in this step I am showing you all the parts which I used in my cnc making. Although you can prefer bigger size of linear rod and ball screw to minimize sagging because thicker the size of linear rod and ball screw minimum the sag occur. Following are the things used by me: -
1) Linear bearings with block
2) Ball screw with Nut
3) Linear rod
4) Ball Nut housing
5) Linear rod supports
6) Spider coupling
7) Pillow bearing 10mm
8) Pillow bearing 8mm
9) Thread inserts
10) L angle
11) Square pipe
12) Alen cap screw
13) Alen cap screw
14) Wood glue
15) wood screw
16) Plyboard
17) Pine wood
18) Paint
Bill of material for Mechanical items
Attachments
Step 3: Electrical Spares Used
Following is the list of Electrical spare used by me
1. Tosiba TB6560 3 Axis Driver Board
2. Mean Well NES-350-24V Power supply
3. Nema 23 Stepper motor
4. 3 core and 4 core wire
5. Mother board
6. Toggle Switch
7. Push Button
8. Rocker Switch
9. Hard Drive
10. DDR2 ram
11. Power Supply
12.3 pin & 4 pin connector
13. shrinkable sleeves
14. Wire
15. Exhaust Fan
16. Monitor
17. Keyboard & Mouse
Here is the Bill of Material for electrical spare used
Step 4: Tool Used
Here I posted pictures of tools used during my entire project. Although there is an alternate of some tools. You can choose set of tools according to your own need. Following are the tools which I used during my entire project.
1. Miter saw
2. Jig saw
3. Table saw
4. Palm router
5. Drill press
6. Wire strippers & pliers
7. Hand drill
8. Welding machine (for metal work)
9. Drill bits & hole saw (according to your own need)
10. Grinder & cutting wheel
11. Basic woodworking hand tools.
12. Soldering iron
13. Paint gun or spray can also be used as an alternate.
14. Disc sander
15. Set square
Step 5: Y-axis
In starting building CNC the first thing you have to build is y-axis, which here is the main frame of my CNC and the material I used is 36mm thick pine wood and width of wood is 8”. Although it wasn’t the hardest wood but if you are going to use wood than prefer hard wood.
(Note: -These dimensions can be change according to your ball screw and linear rods. Dimensions I used for my build are not perfect you can slightly increase these lengths. It would be good if you buy those rods and ball screw and then cut your wood stock to require length.)
Dimension of wood used for frames
Two longer side=1180mm
Two shorter side=1080mm
If you don’t want to use wood than you may use MDF or Ply wood by sandwiching them and make a thick piece. Base needs to be heavy. For the joinery you can use any type of joint but in my opinion mortise and Tenon joint because it provides more stability and rigidity to your Y-axis. Your Y-axis needs to be square as possible because complete CNC depends upon it. Try to make it as perfect as possible.
Height of frame plays important role in construction because on this linear road holders and pillow bearing are mounted on this frame and gap between linear road and ball screw play’s important role, if gap is less it reduces the stability of X-axis.
Here you can clearly see in the images.
Step 6: Gantry Arms & X-Axis
Making of arms for gantry and X-axis is another major important step in CNC building. In this step the main objective is to make CNC gantry as rigid as possible. For the design purpose you can make any type of design but you have to take care of rigidness. For the material side I choose ply rather than wood because it has more resistant towards moisture and I have scrap piece of ply left over from my previous project having laminate glued on it
During this axis my first attempt was result in a failure.The images posted first are result of failure and after that you can clearly see the improvements.The main reason of rejecting first design was because of instability.The arms bottom area was not sufficiently wide that it lost its rigidity.So if you are designing arm then be careful with the design. Wider the arm less cutting area you get and vice versa.
If you want more cutting space in your CNC machine and to obtain that space, you decrease the bottom width of gantry arm than it will definitely loses its stability during movement. I am telling you these things because I experienced these things while making gantry. In these project you can see I made to made two designs of gantry arms.
You can easily find the drawback of my design which I rejected. I made that design because I want more cutting space. Although I succeeded in getting the more space but unfortunately it wasn’t rigid enough so I choose second one.
When you made your design ready it would be good to take printout in CAD in 1:1 and glued that templet on your work piece. If you want exact pieces of two arms it would be good to sandwich both pieces of wood or board and cut them simultaneously to make two of exact same size and dimensions. If you are making some different design than I suggest you not to make your gantry arm too curvy because if you have straight edge it would be easy to glue templet more accurately than a rounded edge arms.
For cutting straight lines try to use circular saw. If you have curvy area than you can use jigsaw to cut those parts you can use even band saw but I don’t have band saw so I use jigsaw to cut that round part. Don’t cut to the exact shape just cut it by giving some room for hand sanding. For the sanding of curved part, I use round bottle, wrap the sand paper around that and start sanding and after sanding for few minutes I got what I wanted. A nice gantry arms.
Step 7: Z-Axis
Same thing happened in this case.But the design was not wrong , only problem was that I ma not getting more cutting space in Z-axis.The photo uploaded first have limited cutting depth.But the final design provide more depth of cut. The images i posted clear your doubts.Although I forget to click final photo of Z-axis during the building time but it wasn't too complicated.Photo clears all.
Making the Z-axis Is not so challenging task in CNC making. In this project I made two type of Z-axis. The major difference between both of the axis is that one is having varying reach and other is having varying reach.
Z-axis doesn’t contain any complex shape but don’t cut it too early because it will depend upon gantry arms. You have to make arms first and then make the Z-axis. You have to take linear rod little bit thick than what I have Because if your z-axis made little bit heavy than rods didn’t sag too much. Although I manage to prevent sagging in my case by making z-axis light as possible.
Now in the images which I provided below you can see two completely different designs. In both case working is completely differently.
In the images you can see completely two different construction of Z-axis.
Step 8: Gluing the Templates
Templets plays vital role in CNC making. Before making any templet you have a little bit knowledge about the parts used in the cnc manufacturing like linear rods holder, pillow bearing and linear bearing and also at what distance their holes are located. Although you can find their varying dimension on the basis of their size in charts.
With the help of those charts and part dimensions you can prepare your own templates like I do. Outside perimeter of these parts are not necessary while making templates but proper distance between holes are needed to take great care.
While making any type of templets you always make a reference line in the center of your drawing to align it perfectly because it will help you a lot while you are gluing it on the wood. In the below images you can see clearly that how I use those reference lines to align my templates. If you have to make a bigger template than reference lines are also important to properly align those templates and make a bigger one. Here I use square by taking one side as a reference and align my template and I repeat these steps for all type of projects. You can see that I also use clips to hold my template to its desired place temporarily, if I was satisfied with it then I started gluing it in parts.
For gluing templates, you can use spray glue, wood glue or paper glue like I use in my project because it’s very easy to apply and remove.
Step 9: Drilling Holes and Inserting Thread Inserts
Drilling holes for fasteners is the easiest and critical part in CNC making. Don’t take this step lightly because if you do this wrong your bearing and other parts are unable to fit at exact position.
So whenever you are trying to make holes for fastener it is necessary to center punch according to your templet. This will prevent the drill bit movement and provides direction to your tool. Don’t use hand drill for drilling holes in CNC making. Always tried to prefer bench drill to perform this task. Don’t take it lightly otherwise you will ruin your entire project because drilling square holes is necessary.
At some place I drill some holes for mounting pillow bearingand linear rod holder and then fasten M5 thread inserts.From images you can see how I use them to fasten my fitting with base frame, arms and some other areas.
Step 10: Motor Mounting Spacers & Router Mounting
Although you can use already build spacers available in the market or you can make them by own. In my case I made the spacer block by my own and then mounted motors on them.
This is also a thing about which I didn’t think during designing. For the material choice, I choose ply sheet cut them into required dimensions and then with the help of hole saw I drill some holes More than the size of the motor coupling and then make a cut for accessing screw used for tightening the coupling to the ball screw and motor.
For router mounting I sandwich two pieces of ply and apply templet and with the help of hole saw and jigsaw I cut it down according to the required design.
Step 11: Installation
In this step I told you how to install bearing with the arms and other part.I am showing this in Z-axis because procedure is same for all axis.First thing you have to do is that hang those linear rod on the rod holders and tighten them but don't forget to insert the bearing in the rod. Align those bearing in that position where you want to install. Then hang that piece which you want to attach.Don't tighten them too tight give some space and always install screw diagonally. Don't screw it with the ball nut housing or do the ball screw installation later so that you can final your this step first.Now attach all the screw but keep them lose.Now start tighten them one by one and moving them back and fro repeatedly. Be sure that your bearing have a very smooth movement.By doing this you can judge that which screw creating trouble so you can leave that one and tighten the other one. If you are satisfy with the movement than you can fasten the ball nut with that portion.
For the installation of the baseboard I install 2"X3/4" thick ply 1.5" down from the top around all four side so that my board can sit in that flush throughout all sides.For motor mounting I made my own spacers having hole inside it. This whole is used for tighten the coupling to the motors.
Step 12: CNC Base Stand With Leveling Provision
To support whole structure and provide a rigid base to the
machine top I use metal stand rather than using wood because it provides more strength.
For the construction of the table I use box pipe and steel angel Both having 2”X2” dimension. For the cutting of angle according to required length I used grinder and metal cutting wheel (prefer chop saw for the cutting of your metal stock). It gives you clean cut and its very easy to join during the welding process.
For the joinery, I used arc welding machine and No: -10 welding rods. To fit my machine into the base you can see that how I use the frame to take the reference for my bottom frame and then tack weld the joints. After that remove the it from frame and complete the rest of welding.
If you have holding magnets than its very easy to weld the legs to the angle frame. Don’t do the complete welding at once. First do the tack weld and then complete the remaining welded joints. For the adjustable height of the whole stand I used 16 mm bolts welded at the base of the legs so that when you turn the bolts it move up and down and keep your table in level.
Step 13: Material and Component Used for Making Controller.
Although the choice of material depends upon you and your design. There are so many industrial design of CNC Controller you can also check them on internet to improve your own design. Frankly I didn’t see any design. I am saying this not for taking credit in fact it’s the real truth. When I completed my build, and started making the document for the project then I come to know that my design is almost similar to the professional design. Following are the material used by me in controller making.
1) Ply sheet
2) Wood glue
3) Screw
4) Paint
5) Sand paper
Following are the list of electrical component used for the controller making
1) Motherboard
2) Power supply
3) Driver card
4) Driver card power supply
5) Exhaust fan
6) Rocker Switch
7) Toggle Switch
8) Push Button
9) 4 pin & 3 pin Connector
Step 14: CNC Controller
There are so many things in my cnc which I didn’t design in fact they are just discovered by me this control panel have the same situation. This is the part of CNC which I never think about when I started this project because my thinking was that I use cpu cabinet and make it like that I fit some components inside it but it doesn’t full fill my all necessaries. I also have an old dead screen which I think to use for my CNC and I repaired it by changing some transistors and now the screen is ready for the use.
When I started to fit my components in one body my first idea was to make a drawer underneath the CNC table in which all the components are installed but the idea didn’t suit me. Then I decided to make my own cabinet made up of ply. But again, there is some issue with the screen mounting. Then I decided to make a hybrid of drawer and cabinet having custom screen mounting over it. This idea full fill my all needs than I arrange all the electronic component in such a way that they consume as less space as possible. I don’t want to make it like a normal box so I made a custom taper front panel which definitely increases its beauty. I made the controller in double layer to get rid of all electrical wiring because if it’s on the upper portion than it looks more messy.
The front portion of the cabinet contains all the controls of the components installed in the cabinet. The drawback of the design is that it doesn’t contain any vent for the hot air removal so in the front portion I made a hole in which I installed the fan which is an AC fan and have more exhaust.
Step 15: Controller Components Installing and Wiring
The controller doesn’t have too much space because I made it look small and portable so now the main work is to assemble the components in the custom-made cabinet. For the motherboard, I cut some area behind the cabinet to fit IO shield behind the cabinet. After that I fit power supply of the computer having fan face outside. I mode the power supply by solder three wire from inside and connect it internally with the power supply. I also mount a button to on/off the CPU power.
Now next to the power supply I made two slots for the VGA connector and D-25 pin connector. This is the place where TB-6560 board is connected. This is the main brain of the CNC. For the CPU motherboard, I use my old frontech board having core2duo in it. Also, it has 2 GB of ddr2 ram.
Moving toward the front side I installed power supply of the cnc motherboard. Next to that there is 18-watt AC fan for exhaust and then next to that there is Samsung 160 GB hard drive. For the electrical wiring, I drill at the bottom of the panel to hide all the wires so that it looks clean. Every component is connected to separate switch.
At the back side of the cabinet there are 5 connectors each having different role. The three-small connector is used for the motor signals and two bigger one are used for the main power and to provide power to the router.
For the port of CNC board, you can see how I take the reference of the ports and then transfer that on the masking tape and use that tape to cut outs the vent on the back panel. For connecting wires to the board, I used some lug to connect the wire properly so that it will never get damaged. For the joints, I used solder and shrinkable sleeves to make joint more secure and protected. I also used hot glue to secure wire at its own place and make it insulated to minimize short-circuit.
For the main hub of power supply I used a connector where all the supply distributed to the switches, from there it goes in the component as per the circuit is made.
Step 16: ControllerStand and Led Mounting
After making controller l now the problem occurs that where and how to mount that on the machine. After designing and finding some old scrap I decided to make a stand in L shape above which a plate is mounted and on that plate, I screwed my controller from the bottom. Now the whole assembly mounted on its own separate stand.
For the Led screen, I made a u shape design having small piece of metal welded on its top. Then I made a whole inside it for screen mounting. Now I carefully drilled a whole in led screen stand and fasten it with the help of bolt.
Now the machine looks complete and makes me feel proud.
Step 17: Software Used & Software Settings
I used Artsoft Mach3 software.Mach 3 convert your PC into 6 axis CNC controller.i used only 3 axis (X,Y, & Z).but you can go beyond 3 axis level with your immagination & knowledge.the programming in Mach 3 or in CNC is comprised G code & M code with Mach 3 you can visualize & apply codes to your programs.Mach 3 interface can be highly customizable.but in this software little bit CAD/CAM knowledge is must.after installing software you can improve productivity by turning your PC into CNC controller. you can import file in JPG,BMP,DXF,HPGL files with lazy cam software.if you don't want to learn G codes & M codes.you can directly convert your DXF file to G code with the help of Lazycam.
you can download Mach 3 & Lazy cam software from this Link:-
I have also uploaded my Router settings in (MACH 3).Hope theses settings will also works for you.
Attachments
Step 18: Masking Painting & Sanding
This step is only for those people who really want to give their CNC a Custom look. For Painting, anything you just need to know some basic steps of painting. Following are the material used for painting purpose.
1. Spray Gun.
2. Paint brush
3. Primer
4. Sanding paper (100,200,400 Grit)
5. Thinner
6. Paint
7. Masking Tape
8. Wood filler
Before starting my paint work I sand of everything with sand paper than apply one coat of primer, then again do the sanding work with 200 frit sand paper and after that apply the first coat of paint. Before apply second coat I sand of the paint with 400grit paper and then apply the second coat. Make sure to sand your surface before every new coat of paint and then wipe down the dust with For my build, I painted even the linear bearings, pillow block, rod holders and ball nut housing. For painting technique, I use spray paint but at some place I prefer brush for painting. I also use wood filler for filling some minor crack to get smooth finish. For painting metal I apply first coat of primer, then sanding and then paint it.
I also used masking tape to protect that areas where I don’t want to paint, linear road bearing, pillow bearing, rod holder and ball nut housing from inside only so that it remain clean and don’t interrupt me during the installation process.
Step 19: Wire Management
Cable management is the one of the important point to make your CNC looks neat and clean. It makes your project pleasurable and you also get rid of cable tangling. There are many projects in the market to avoid cable tangling and makes good wire management. You can use zip ties to tie your cable close to your machine and improve its overall look. Following are the material which I used to improve my cable management: -
1) Zip ties
2) Shrinkable sleeves
3) Cable tray
Step 20: Finally................................!!!!!!!!
Here is the Test Run of my CNC Router.
Here you can see my CNC from All angles.I tried to show you every aspects of my CNC. If you have any quarry feel free to ask...
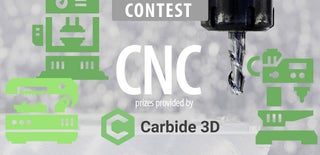
Participated in the
CNC Contest 2016
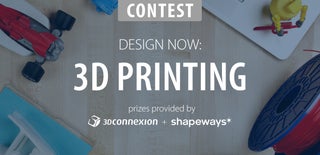
Participated in the
Design Now: 3D Design Contest 2016
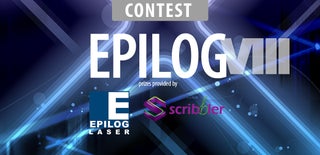
Participated in the
Epilog Contest 8