Introduction: Homemade Inverter Battery Trolley
So this Instructables is about an inverter trolley. The place where I lived there is a lot of power cuts during the rainy season because of heavy storms and to counter that problem people usually have an inverter for the power backup. Being a maker I need electricity to full fill my needs. It's not able to run all of my machines but if I have to run my CNC or a 3d printing work at that moment it's a huge timesaver and kept my equipment running during the power cuts. Power cuts mostly remain for 1-2 hrs and the inverter backup is plenty enough to keep everything alive. So for this build, I decided to reuse some of the old rusty stuff to get rid of them. I don't want to throw that because of rust so for the framework the material is all repurposed from old things which are no longer usable. Being a heavy item and usually needed to be replaced after a certain interval I made this to be movable because the place where it needs to be placed in a congested space so having mobility is surely gonna help in maintenance. Overall said this build is easy, there are surely no problematic areas where you get any problem. If you have any ideas or tips then surely let me know in the comments section down below.
Supplies
The material used: For this build, most of the material has been recovered from my old builds which are no longer usable and that's the reason why I am using materials randomly which fits into the desired area. Although I also need to use some fresh material too. The list of materials has been provided down below.
- 11/2" square Pipe
- 11/2" angle
- 1" angle
- 3/4" angle
- 1 mm MS sheet
- 1 mm stainless steel sheet
- 20 gauge mesh
- 4mm thick glass
- 4 mm rivets
- Casters
- Paint
Step 1: My Design Considerations Before Building
Before building this trolley I have made a rough sketch. I have thought about the requirements and specifications. I made a simple box shape design. The whole trolly can be easily moveable for cleaning and easily placing. So I fitted 4 no of PU castor wheels. The battery frame I have also provided wheels because batteries used for inverter are not dry batteries they are lead-acid batteries are used and over a period of time the acid gets dry and required top up with demineralized water. That will increase battery life as well. It is also required that the battery will remain cool inside the trolley so I cover the back and side with a perforated sheet. The top section where the inverter is placed in made back with the perforated sheet so that all the hot fumes from the inverter will easily escape. And inside components of the inverter will remain cool. I cover the front of the top section with 4 mm glass so that all the status will be easily shown. And it gives a good aesthetic look as well. Door front I made from rusted scrap sheet. and handles I made with ⅜" square rod that was bent with my forge.
Attachments
Step 2: Battery Rack
For most of my builds I usually cut down all the materials at once but this build is different because I have to reuse the old material. So whatever I found useful I included that material to my build and then focus on one section and complete that and move forward. The battery rack is made out of 1 1⁄2" angle piece. The joint is a but weld joint in which in any of the opposite two sides the ends are cut equals to the dimensions of the angle. Since the battery is a bit higher in the design in that case I have to weld additional arms so that I can provide some support so that during the dragging time the battery will not tip over. Usually, with the 1⁄4" thick material the current settings, I used generally lie between 85-90 amps. To keep the frame in the square I used a magnetic holder to keep the at 90° and tack weld all the sides one by one. If the material is a bit thicker than I always made 2-3mm chamfer so that a good weld joint can be formed.
Step 3: Constructing the Top Inverter Frame.
To construct the top inverter frame the construction is a bit more same as the battery rack but with a slight difference on the top frame there are going to be two frames joined together with some spacer pieces. The height is kept according to the thickness of the inverter. If you have a different inverter than that thickness might vary. So then onto the top inverter frame, two different angle frames have been connected. Since all of the material is scrap material and I have to attach the sheet to the top so I decided to use 3⁄4" angle pieces. The frame onto which the sheet has to be mounted, on that frame, I welded a stip instead of angle so that it's easy to place the inverter into the chamber.
Step 4: Welding the Legs.
For the legs, I used 11⁄2" square pipes. They are a bit rusty but it wasn't a big problem to remove that. I never got any problem with welding a rusty material, although it's mandatory to clean the surface and then made a weld. With the help of a magnet, I placed them temporarily with tack welds and once I satisfied with the position and squareness I made a complete weld. To provide strength to the lower base of the legs I welded 1 " square welding pipes as a stretcher piece. The advantage of these pieces is to keep the entire frame square and provide much more structural stability to the trolley when wheels get attached to the frame.
Since the battery has to be inserted inside that's why onto one of the sides the stretcher piece is not welded. Onto the end portion, I have to install the wheels that's why I made some end caps so that this work becomes much easier to carry out.
Step 5: Covering the Top Frame.
Once the mainframe has been completed I start the work onto the covering areas. The sheet for the bottom base has been recovered from the old door. Since this is not wide enough that's why I need to cut them to the required section and then welded them together to form a large sheet which sits inside those angle frame. Since over the plate, the inverter has to be placed and all of the work is painted that's why this joint does not go to create any problem. For the top visible area, I am going to use a stainless steel sheet. I cut it to the required dimensions and then weld it to its place.
Since the inverter is going to be placed inside this chamber that's why I decided to use a mesh and attached it from the inner side with the help of a rivet. At first, I attached the mesh to all the sides but then it seems a lot cheaper in the looks that's why I discarded that idea and kept the mesh area only at the backside of the top frame. Onto either side of the frame, I ended up with a mirror finish stainless steel sheet.
Step 6: Covering the Bottom Area
Since the bottom area has a different construction that's why I approached differently. There is no place to attach the mesh around it and I don't want to install the mesh around the legs. That's why for the looks I decided to make some angled frame and install them into the bottom legs. The frame is made with 1" angle with the simple but joint and then welded between the legs by making sure that the surface is completely flush with the legs surface. Instead of the full welds, I decided to go with some tacks onto a few places because it's really not necessary in this case. From thereafter I made marks onto the angled frame equally apart and then drill them with 4mm drill bit because that's the size of the rivet I am using in this entire build. After drilling the holes I cut down the sheet with the help of sheet metal cutter and then placed inside the frame. Some of the holes are not aligned with the holes onto the frame which I drilled earlier but that wasn't a huge deal in this case because it's easy to drill the holes onto the sheet. Then with the rivet, I attached the sheet all around to the inner side of the angled frame. I installed the mesh so that air circulation can take place in the battery compartment because it gets heat up when it's under load.
Step 7: Constructing the Front Doors.
Once the basic structure has been completed its. Time to start the work onto the doors. The door frame is again made with 1" angle piece. The welding joint is the same as I did for the rest of the build for both the bottom and top areas. For the front, I am using a scrap sheet received from the old cooler unit. I placed my frame over the sheet and then took the reference and then cut it with the help of an angle grinder. To attach the sheet to the frame I again use the rivet method.
I am using rivets because welding thin sheets are not ideal with a stick welder and the rivets make the whole build neat and clean. I first drill the holes with equal spacing onto the frame then transfer them onto the sheet and then insert the rivets into those holes I didn't secure the rivet at the first so that they provide a slight wiggle room to install the remaining rivets into there respective area. Once all the rivets are placed in the right location made them secure. The door for the top section has been attached with a glass sheet inside it so that it would be easier to see the status of the inverter.
Step 8: Constructing the Door Handles and Installation
For the door handles, I again used some old bars. The size of the handles is kept different according to the door size. There is a total of 3 handles are constructed one for the trolley and two for the doors. The construction is pretty simple. I first made a mark onto both the ends at equal distance and then heat those areas in the coal forge. From thereafter I hold them into my bench vise and made a bend to the marked area. Once the handles are made just with eyeballing I welded them to there place.
Step 9: Installation of the Door Hinges.
For the hinges, I am using regular wooden door hinges and attach them with the help of rivets. I first divide the frame into an equal section and then place the hinge over one of the sides and then made a layout of the holes. After that drill down those holes and attached the hinges to the door frame. With the same method, I transfer the hole location of the hinges onto the mainframe and then drill them and attach them to the mainframe.
Step 10: Installation of Wheels
To install the wheels I fist center punch all the areas where I have to install the wheel and then drill a 6.35mm hole and tap it with M5 thread tap. From thereafter with the help of Allen bolt, I attached the wheels to both the mainframe and the battery carriage.
Step 11: Painting and Finishing.
To start the paint job I fist start with filler material. I fill out all the voids and gaps where I just used tacks instead of long continuous welds. Then I sanded the surface with 120 grit. After that, I apply two coats of brown primer to make a good base layer. After that with the help of a brush apply one layer of orange and black paint. The brush applies a thick layer of paint compared to the paint gun that's why I preferred brush here and this has to face some moisture so I prefer that. The rivets have been colored with blue colour. For the front glass, I sanded the putter area a tiny bit so that epoxy can stick to the surface. Then I mixed two-part epoxy and mixed it thoroughly and apply to the sides and inserted them to the door frame with some clamps. Onto the bottom door, I mount my 3d printed logo which looks very beautiful to me.
Step 12: Final Looks
The final product is in front of you. If you have any suggestions to improve this then drop them in the suggestion box down below and I catch you in the next build. Till then keep making.
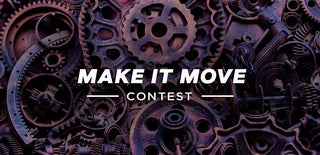
Participated in the
Make it Move Contest 2020