Introduction: Horizontal Travel Robot Arm
This is the first product I built with an open design. It's a slight modification of a robotic arm and I built this with the intention of enabling practical and useful product movements.
The objective is to help you very quickly build an arm that enables you to add intelligence to it. I will publish the control libraries and image detection logic once I finish this first push of documentation.
Learn more at: https://www.fdxlabs.com/products/horizontal-travel...
Summary Specs
0.88 lbs (0.4 kg) tested max payload
Vertical travel Z-axis: 6.8 inches (17.3 cm)
Reach Y-axis: 10.2 in (26 cm)Customizable
Horizontal travel X-axis (3.3 ft (1 m) as tested.
Step 1: Bill of Materials & Screw Guide
Attached is the entire list of materials you will need.
.STL files available here:
Step 2: Gather All the Materials
This is the entire build materials, and this image follows the logical position of each of the components. You can refer this continuously as a map of the build.
Step 3: Build the Grip
Make sure that you center your servo before finishing the assembly of the servo gear.
Materials Required
Grip 3d Printer parts
7 – M3 Screws 12 mm
7 – M3 Locking Nuts
2 – M2 Screws 6mm
2 – M2 Nuts
1 – MicroServo including Horn and Horn Screw/Washer
Step 4: Build the Base
Materials Required
Base 3d Printed Part
2 – 2020 T-Slot profile 100mm length
4 – M3 Screws 8 mm
4 – M3 washers
4 – M3 T-Nuts
1 – 3mm diameter Aluminum rod
Step 5: Build the Arms
Materials Required
3d Printed Arms
2 – M2 8mm Screws
1 – M2 6mm Screws
3 – M2 Nuts
2 – 3mm Aluminum Rod
2 – M3 20 mm Screw
2 – M3 16 mm Screw
1 – 12mm Screw
5 – M3 Locking Nylon Nuts
11 – MR63ZZ Bearings
Step 6: Attach Grip
Materials Required
Grip AssemblyArm Assembly
1 – M3 20 mm Screw
1 – M3 16 mm Screw
2 – M3 Locking Nylon Nuts
3 – MR63ZZ Bearings
Step 7: Attach Servos
Make sure that you center the servos at a ~45 degree angle, as shown in the pictures with the arduino before coupling them to the arm.
The arms have to be at a ~45 degree angle as shown at the "center position" of each servo, this will be crucial to have optimal range of motion.
Materials Required:
3d printer Servo mounts
2 – Servos2 – M
3 Screws 6 mm (Horn screws can be an alternative)
4 – M4 Screws 14mm
4 – M4 Washers
4 – M4 Nuts
Step 8: Add Bearings
Materials Required
Bearing Plate 3d Print
8 – M4 10mm Screws
8 – M4 Washer
2 – SC8UU Linear Bearing Block
Step 9: Cable Management Snapshots
Step 10: Carriage Assembly
Step 11: Camera
Step 12: Wiring Diagram
The objective of the robot is for it to be surprising simple. I'm using a Raspberry Pi with a PiCamera, connected by USB interface to an Arduino.
The Arduino directly controls the servo motors, and uses an A4988 Stepper motor driver to control the X-Axis stepper motor.
For power, I used an ATX Power Supply to power the entire system, using an LM2596 voltage regulator to obtain the 6.8 volts required by the large servos. Everything else is consuming 5v or 12v directly from the power supply.
Step 13: Software
You can find the code repository I'm using here:
https://github.com/pacogarcia3/hta0-horizontal-rob...
The most challenging part is the Computer Vision with a single camera, and you can find more explanation on my blog post here:
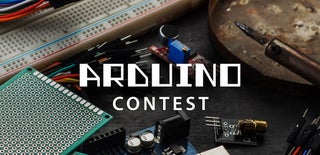
Participated in the
Arduino Contest 2019